-
大嶺山工業 廣東

乳製品冷卻器 – 用於散裝罐的農場乙二醇牛奶冷卻系統
革新乳業:牛奶冷卻系統基本指南
本文探討了牛奶冷卻器在乳製品產業中的重要作用,重點介紹這些系統如何確保從農場到餐桌的牛奶品質和安全。本指南專為塑膠和橡膠、機械加工、食品和飲料、化學和製藥、電子、雷射、印刷、醫療行業以及實驗室、研究機構和資料中心的人士而設計,全面概述了牛奶冷卻技術。其目的在於強調為什麼投資高品質的冷卻器系統不僅有益,而且對於維持產品完整性和運作效率至關重要。無論您是酪農、加工廠的成員,還是參與冷卻技術的更廣泛的工業應用,了解牛奶冷卻器的細微差別將使您掌握做出明智決策的知識,從而提高您的營運和產品品質。
目錄
快速牛奶冷卻對乳牛場的重要性是什麼?
快速冷卻牛奶對於乳製品行業至關重要。擠乳後,流出乳牛的生牛奶溫度約為 95°F (35°C)。為了保持牛奶的品質和安全,盡快將牛奶冷卻至 40°F (4°C) 以下至關重要。這種快速冷卻過程顯著抑制了細菌的生長,確保牛奶保持新鮮並延長其保質期。眾所周知,如果牛奶在室溫下保存,細菌數量每 20 分鐘就會增加一倍。這不僅影響口感和質地,也對消費者的健康構成風險。
此外,快速冷卻牛奶有助於保存其天然酵素和營養成分,確保牛奶保留其營養價值和風味。酪農明白牛奶的品質直接影響他們的獲利能力。由於冷卻不當而不符合品質標準的牛奶可能會被加工商拒收,導致經濟損失。因此,投資高效的牛奶冷卻系統不僅是品質控制問題,也是乳牛場的重要的經濟考量。
牛奶冷卻器如何運作?
牛奶冷卻器採用冷凍原理運行,可有效冷卻牛奶。冷卻器系統的核心包括壓縮機、冷凝器、膨脹閥和蒸發器。當壓縮機對冷媒氣體加壓並升高其溫度時,該過程就開始了。然後,這種熱的加壓氣體移動到冷凝器,在那裡被冷卻並凝結成液體,並在此過程中釋放熱量。接下來,液體冷媒通過膨脹閥,在這裡迅速膨脹並冷卻。然後冷冷媒流過蒸發器盤管。在蒸發器中,冷媒吸收牛奶中的熱量,導致牛奶冷卻。吸收熱量後,冷媒返回壓縮機,重複循環。
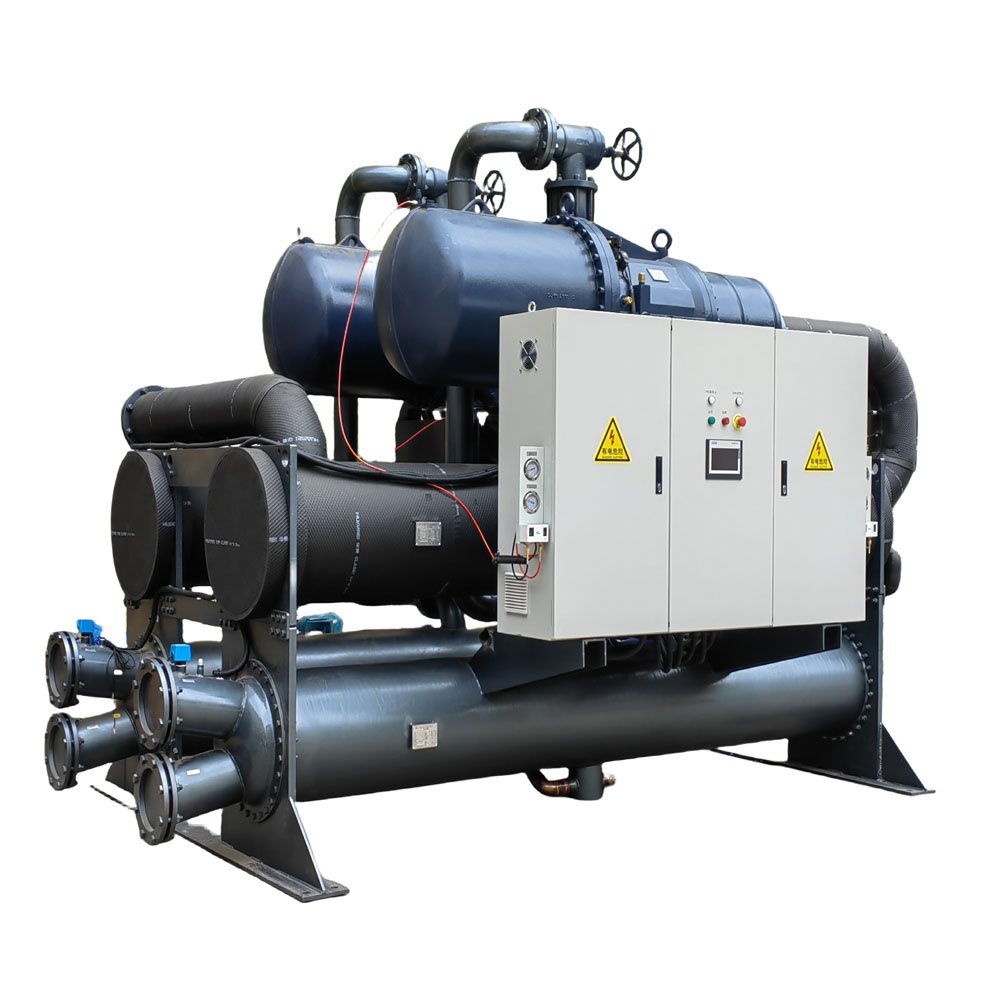
在直接膨脹系統中,蒸發器與牛奶罐直接接觸,提供高效率的冷卻。其他系統則使用板式冷卻器或熱交換器將牛奶中的熱量間接傳遞給冷媒。牛奶冷卻器的效率受其冷卻能力、所使用的冷媒類型以及系統設計的影響。先進的冷卻器還可以包含熱回收等功能,利用從牛奶中提取的熱量來加熱水,從而提高能源效率。您可以在這裡了解有關 水冷式螺桿式冷水機組.
有哪些不同類型的乳製品冷藏機?
乳製品冷卻機有多種類型,每種類型都適合不同規模的農場和營運需求。直接膨脹式冷水機組通常用於小型企業。它們能夠提供有效的冷卻,但是隨著牛奶量的增加,其效率會降低。對於中型到大型乳牛場來說,通常首選乙二醇冷卻器。這些系統使用由冷卻系統冷卻的水和乙二醇的混合物,透過板式冷卻器或熱交換器來冷卻牛奶。
另一種是即時冷卻系統,當牛奶通過一系列冷卻板時,它幾乎可以立即冷卻。這些對於大規模操作來說非常高效,可確保牛奶快速冷卻至所需溫度。此外,還有水冷式和風冷式冷水機組。水冷系統使用水來冷卻冷凝器,而風冷系統則依靠空氣。這些之間的選擇取決於水的可用性、環境溫度和能源成本等因素。
為什麼乙二醇是牛奶冷卻系統的首選?
乙二醇在牛奶冷卻系統中受到青睞,主要是因為其冰點比水低。乙二醇溶液可以冷卻到 32°F (0°C) 以下而不會結冰,從而可以更有效地將牛奶冷卻至低至 34°F (1°C) 的溫度。這種能力對於快速冷卻牛奶並維持其恆定的低溫至關重要。
- 效率:乙二醇系統效率很高,因為乙二醇可以快速冷卻牛奶,減少牛奶暴露在可能促進細菌生長的溫度下的時間。
- 溫度控制:精確的溫度控制是另一個優點。乙二醇系統可以保持一致的溫度,確保整批牛奶均勻冷卻。
- 靈活性:乙二醇冷卻器也是多功能的。它們可以用於多種配置,包括板式冷卻器和散裝罐,使其適用於不同的乳牛場設定。
- 熱回收:在許多乙二醇系統中,都採用了熱回收技術。乙二醇在冷卻過程中吸收的熱量可用於加熱水以供農場的其他用途,例如清潔和消毒設備。
乙二醇系統需要大量投資,但可以在牛奶品質、能源效率和操作靈活性方面帶來長期利益。
探索散裝牛奶冷藏裝置的優勢
散裝牛奶冷卻裝置為乳牛場提供了多種優勢,特別是對於牛奶產量高的乳牛場。這些裝置用於快速冷卻大量牛奶,並將其保持在恆定的低溫下,直到被收集起來進行加工為止。
優點包括:
- 可擴展性:它們可以處理大量的牛奶,使其成為發展乳製品業務的理想選擇。
- 一致性:這些裝置確保均勻冷卻,這對於維持整批牛奶的品質至關重要。
- 自動化:許多散裝冷卻裝置配備自動控制裝置,可實現精確的溫度管理並減少人工勞動。
- 能源效率:現代散裝冷卻器的設計充分考慮了能源效率,並採用了變速驅動器和熱回收系統等功能。
此外,散裝冷卻裝置可幫助農民滿足乳製品加工商和監管機構要求的嚴格品質標準。透過確保牛奶快速冷卻並儲存在正確的溫度下,這些裝置在保持牛奶的新鮮度和營養價值方面發揮關鍵作用。
如何為您的乳牛場選擇合適的牛奶冷卻機?
選擇合適的牛奶冷卻器取決於幾個因素。
考慮 | 描述 |
農場規模和牛奶產量 | 小型農場可能會選擇直接膨脹式冷卻器,而大型農場可能需要乙二醇冷卻器或即時冷卻系統來有效處理大量牛奶。 |
冷卻能力 | 冷卻器的容量應該與農場的牛奶產量相符。考慮潛在成長非常重要,因為低估產能可能導致效率低下。 |
能源效率 | 尋找能源效率等級高的冷卻器。隨著時間的推移,熱回收等功能可以顯著降低營運成本。 |
冷水機類型 | 根據環境條件和資源可用性考慮風冷或水冷系統是否更合適。 |
預算 | 平衡初始投資與長期營運成本。儘管更有效率的系統可能有更高的前期成本,但從長遠來看,它們可以節省成本。 |
也建議諮詢冷卻器製造商或乳製品設備專家,他們可以評估您的特定需求並推薦最合適的系統。此外,請考慮您所在地區維護和支援服務的可用性。
牛奶冷卻機的維護要求是什麼?
定期維護對於確保牛奶冷卻器的使用壽命和效率至關重要。其中包括:
- 打掃:定期清潔冷凝器、蒸發器和板式冷卻器等零件,可防止牛奶殘渣和污染物的積聚,影響性能。
- 冷媒水平:檢查並維持適當的冷媒水平對於最佳冷卻性能至關重要。
- 檢查組件:定期檢查壓縮機、幫浦和風扇等零件的磨損狀況。及時更換任何損壞或磨損的零件。
- 校準:確保溫度感測器和控制器經過準確校準,以保持精確的冷卻溫度。
- 專業服務:安排合格技術人員進行年度或每兩年一次的維修,進行徹底檢查並執行任何必要的維修或調整。
適當的維護不僅可以確保高效運行,而且還可以幫助防止代價高昂的故障並延長冷水機組的使用壽命。
牛奶冷卻的能源效率和永續性
能源效率越來越受到乳牛養殖業的關注。現代牛奶冷卻器的設計充分考慮了永續性,採用了減少能源消耗和最大限度減少環境影響的功能。
主要包括:
- 變速驅動器:這些允許冷卻器根據需求調整其冷卻輸出,從而在低需求期間減少能源使用。
- 熱回收:如前所述,熱回收系統利用從牛奶中提取的熱量來加熱水,從而減少了對水加熱的額外能源的需求。
- 高效冷媒:使用全球暖化潛勢值(GWP)較低的冷媒可以減少冷卻系統對環境的影響。
- 智慧控制:先進的控制系統可以優化冷水機組的運行,確保其以最佳效率運作。
透過投資節能牛奶冷卻機,酪農可以降低營運成本,減少碳足跡,並為更永續的乳製品產業做出貢獻。
牛奶冷卻器在確保牛奶品質和安全方面的作用
牛奶冷卻器在維持牛奶品質和安全方面發揮關鍵作用。透過將牛奶快速冷卻至適當的儲存溫度,這些系統可以防止細菌生長,保持牛奶的新鮮度並延長其保質期。這不僅確保牛奶可以安全食用,而且還有助於保留其營養價值和風味。牛奶冷卻是牛奶品質最重要的因素。
此外,許多現代冷卻器都配備了監控和警報系統,可以在任何溫度偏差時向農民發出警報,以便及時採取糾正措施。這在乳製品監管嚴格的地區尤其重要,因為這些地區必須保持適當的冷卻溫度。
牛奶冷卻技術的創新與未來趨勢
牛奶冷卻領域正在不斷發展,並不斷創新以提高效率、永續性和性能。
一些主要趨勢包括:
- 先進冷媒:對 GWP 較低的新型冷媒的研究正在進行中,預計將進一步減少對環境的影響。
- 智慧科技:與農場管理系統的整合可以即時監控和控制牛奶冷卻,優化性能和能源使用。
- 再生能源:一些乳牛場正在探索使用再生能源,例如太陽能或風能,來運行他們的牛奶冷卻器,從而進一步減少他們的碳足跡。
- 改進的熱交換器:熱交換器設計的進步使得熱傳遞更加高效,從而增強了冷卻過程。
這些創新有望進一步增強牛奶冷卻器的功能,使其在未來幾年更有效率和永續性。例如, 水耕工業冰水機 已經在農業領域引起轟動。
常見問題解答
乳牛場應將牛奶冷卻到多少溫度?
為確保品質和安全,擠乳後兩小時內應將牛奶冷卻至 40°F (4°C) 以下。
牛奶在散裝罐中可以儲存多久?
經過適當冷卻的牛奶可以在收集前存放在散裝罐中長達 48 小時。
乙二醇系統可以在乳牛場用於其他用途嗎?
是的,除了冷卻牛奶外,乙二醇系統還可用於其他冷卻需求和熱回收,例如加熱水用於清潔。
哪些跡象顯示牛奶冷卻器需要維護?
跡象包括冷卻不足、異常噪音、洩漏和能耗增加。
政府對投資節能牛奶冷卻器是否有任何激勵措施?
許多地區為投資節能設備(包括牛奶冷卻機)的酪農提供回扣、稅收抵免或補助。請諮詢當地農業或能源部門,以了解可用的計劃。
板式冷卻器在牛奶冷卻系統中如何運作?
板式冷卻器使用一系列冷卻板來快速冷卻流經它們的牛奶,從而實現從牛奶到冷卻劑的有效熱傳遞。
結論
- 快速冷卻牛奶對於維持牛奶品質、安全和延長保質期至關重要。
- 牛奶冷卻器,包括直接膨脹、乙二醇和即時冷卻系統,在乳製品行業中發揮至關重要的作用。
- 乙二醇因其較低的凝固點、效率和精確的溫度控製而受到青睞。
- 散裝牛奶冷卻裝置為大型乳製品企業提供了可擴展性、一致性和自動化優勢。
- 選擇合適的冷卻器需要考慮農場規模、冷卻能力、能源效率、冷卻器類型和預算。
- 定期維護至關重要,包括清潔、冷媒檢查、組件檢查和專業維修。
- 具有變速驅動器、熱回收和高效冷媒等功能的節能冷水機組有助於實現永續發展。
- 牛奶冷卻器對於防止細菌生長、維持牛奶品質和確保遵守安全法規至關重要。
- 先進的冷媒、智慧技術、再生能源整合和改進的熱交換器等創新正在塑造牛奶冷卻的未來。
- 投資高品質的冷卻系統不僅有益,而且對於維持乳製品行業的產品完整性、營運效率和盈利能力至關重要。
請記住,作為工業冷水機製造廠,我們了解包括乳製品行業在內的各個行業面臨的獨特挑戰。我們的專業知識和先進的冷卻器解決方案,例如 牛奶冷卻機, 防爆冷水機組, 和 風冷式螺桿式中央冷水機組,旨在迎接這些挑戰。我們提供客製化系統,確保精確的溫度控制、能源效率和可靠性,這對於維持最高的營運品質和安全標準至關重要。無論您從事塑膠和橡膠、機械加工、食品和飲料或其他任何行業,我們的冷水機組都能提供您所需的冷卻性能。我們邀請您聯絡我們,討論您的具體要求,並了解我們的客製化冷水機組解決方案如何使您的業務受益。讓我們利用最先進的冷卻器技術來幫助您優化營運並實現生產目標。透過與我們合作,您可以獲得尖端技術和致力於支援您成功的專家團隊。
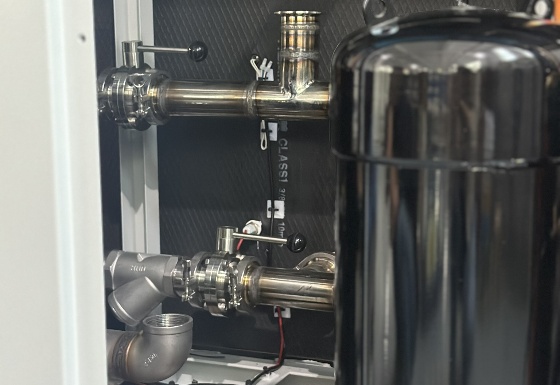