-
Khu công nghiệp Dalingshan Quảng Đông
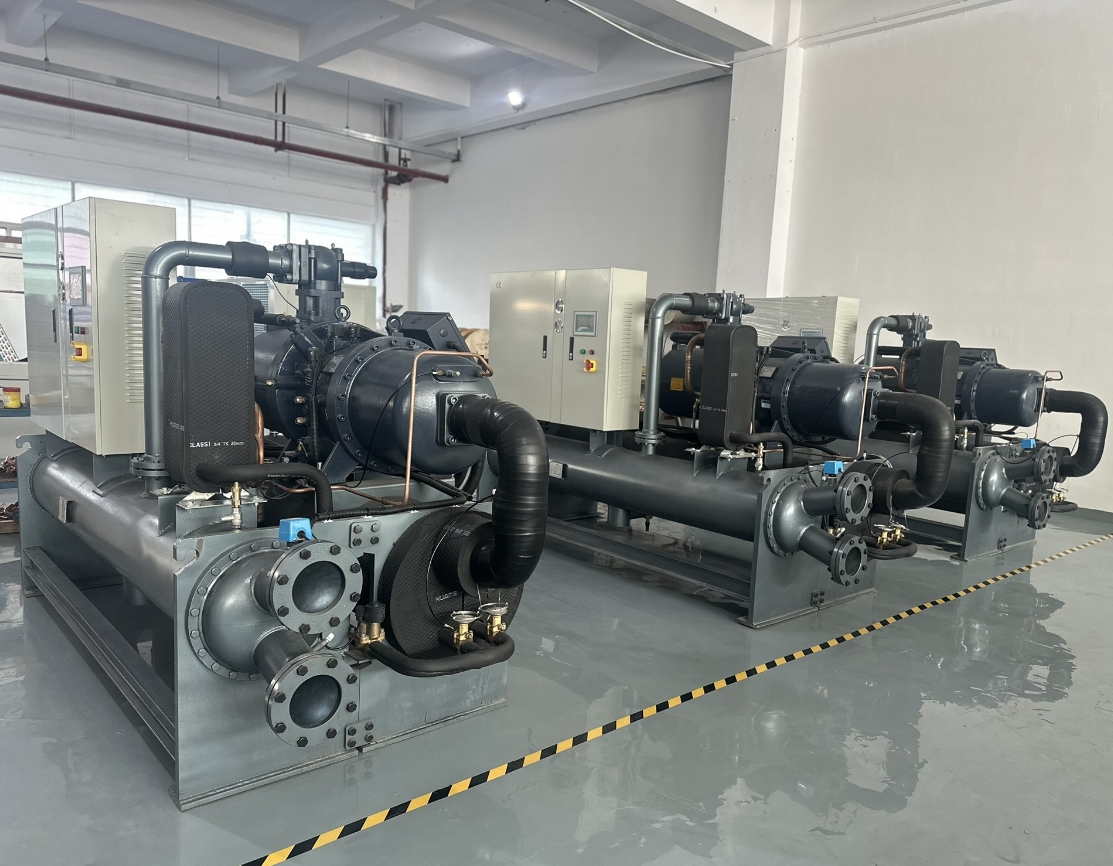
hệ thống làm mát đúc khuôn trong quá trình đúc khuôn
Làm mát chính xác: Nền tảng của quy trình đúc khuôn hiệu quả
Đúc khuôn là một quy trình sản xuất được sử dụng rộng rãi, được biết đến với khả năng sản xuất các bộ phận kim loại phức tạp, chất lượng cao với độ chính xác về kích thước và độ hoàn thiện bề mặt tuyệt vời. Tuy nhiên, để đạt được kết quả tối ưu trong quá trình đúc khuôn phụ thuộc đáng kể vào việc kiểm soát nhiệt độ chính xác trong giai đoạn làm mát. Bài viết này đi sâu vào vai trò quan trọng của các hệ thống làm mát trong quá trình đúc khuôn, khám phá cách chúng tác động đến hiệu quả sản xuất, chất lượng sản phẩm và lợi nhuận chung. Đây là bài viết phải đọc đối với bất kỳ ai tham gia vào ngành đúc khuôn, vì bài viết cung cấp những hiểu biết có giá trị về việc tối ưu hóa quy trình làm mát để nâng cao hiệu suất và mang lại kết quả vượt trội. Trong bài viết này, với tư cách là nhà sản xuất máy làm lạnh nước công nghiệp, tôi sẽ chia sẻ kinh nghiệm và chuyên môn của mình để tiết lộ bí quyết thành công của các hoạt động đúc khuôn.
Mục lục
1. Đúc khuôn là gì và tại sao làm mát lại quan trọng đến vậy?
Đúc khuôn là một quy trình sản xuất trong đó kim loại nóng chảy được phun dưới áp suất cao vào khuôn thép, còn được gọi là khuôn đúc. Khi kim loại nóng chảy lấp đầy khoang khuôn, nó được để nguội và đông cứng, tạo thành hình dạng mong muốn. Quy trình này được sử dụng rộng rãi trong nhiều ngành công nghiệp để sản xuất các bộ phận kim loại phức tạp và chất lượng cao.
Làm mát là một bước quan trọng trong quy trình đúc khuôn vì nó ảnh hưởng trực tiếp đến chất lượng, độ chính xác về kích thước và thời gian chu kỳ sản xuất của sản phẩm đúc. Kiểm soát đúng tốc độ làm mát đảm bảo kim loại nóng chảy đông đặc đồng đều, ngăn ngừa các khuyết tật như độ xốp, co ngót và đóng nguội. Do đó, kiểm soát nhiệt độ là một khía cạnh cơ bản của quá trình đúc khuôn. Là một người tham gia sâu vào quá trình sản xuất máy làm lạnh nước công nghiệp, tôi đã tận mắt chứng kiến các giải pháp làm mát hiệu quả có thể biến đổi quy trình đúc khuôn như thế nào. Làm mát hiệu quả không chỉ cải thiện chất lượng sản phẩm mà còn tăng đáng kể năng suất bằng cách giảm thời gian chu kỳ.
<img src="”https://thewaterchiller.com/wp-content/uploads/2024/12/industrial-chiller-water-cooled-water-chiller-with-scroll-compressor-5hp.jpg”" alt=""Nước" cooled scroll water chiller” />
2. Hệ thống làm mát trong đúc khuôn hoạt động như thế nào?
Trong đúc khuôn, hệ thống làm mát thường bao gồm một mạng lưới các kênh hoặc mạch bên trong khuôn mà qua đó chất làm mát, chẳng hạn như nước hoặc dầu, được lưu thông. Các mạch làm mát này được bố trí một cách chiến lược để loại bỏ nhiệt khỏi khuôn và kim loại nóng chảy nhanh nhất và đồng đều nhất có thể. Hiệu quả của hệ thống làm mát phụ thuộc vào các yếu tố như thiết kế mạch làm mát, lưu lượng chất làm mát và độ dẫn nhiệt của vật liệu khuôn.
Có nhiều phương pháp làm mát khác nhau được sử dụng trong đúc khuôn, bao gồm làm mát bằng nước, làm mát bằng dầu và làm mát bằng không khí. Mỗi phương pháp đều có những ưu điểm riêng và được lựa chọn dựa trên các yêu cầu ứng dụng cụ thể. Làm mát bằng nước là phương pháp phổ biến nhất do khả năng truyền nhiệt cao. Theo kinh nghiệm của tôi, một Máy làm lạnh nước dạng cuộn làm mát bằng nước có thể tăng cường đáng kể hiệu quả của quy trình đúc khuôn. Khách hàng của chúng tôi trong Ngành nhựa và cao su, Ngành gia công và Ngành thực phẩm và đồ uống đã báo cáo những cải tiến đáng kể về sản lượng sản xuất của họ sau khi triển khai các giải pháp làm mát theo yêu cầu của chúng tôi.
3. Những yếu tố nào ảnh hưởng đến tốc độ làm mát trong đúc khuôn?
Một số yếu tố ảnh hưởng đến tốc độ làm mát trong đúc khuôn, tác động đến hiệu quả chung của quy trình sản xuất. Những yếu tố chính trong số đó là:
- Thiết kế khuôn mẫu: Thiết kế và bố trí các kênh làm mát trong khuôn đóng vai trò quan trọng. Vị trí kênh thích hợp đảm bảo tản nhiệt đều.
- Tốc độ dòng chảy chất làm mát: Lưu lượng cao hơn thường dẫn đến làm mát nhanh hơn, nhưng phải cân bằng để tránh giảm áp suất quá mức.
- Vật liệu khuôn: Vật liệu có độ dẫn nhiệt cao hơn, như thép, giúp truyền nhiệt nhanh hơn.
- Nhiệt độ chất làm mát: Nhiệt độ chất làm mát thấp hơn có thể đẩy nhanh quá trình làm mát nhưng có thể làm tăng nguy cơ sốc nhiệt cho khuôn.
- Vật liệu đúc: Các kim loại khác nhau có đặc tính làm mát khác nhau; ví dụ, nhôm nguội nhanh hơn thép.
- Phần Hình học: Các phần dày hơn của vật đúc nguội chậm hơn các phần mỏng hơn, đòi hỏi phải cân nhắc cẩn thận khi thiết kế khuôn.
Hiểu được những yếu tố này là điều cần thiết để tối ưu hóa quy trình làm mát. Dựa trên nghiên cứu sâu rộng và phản hồi của khách hàng, chúng tôi nhận thấy rằng việc điều chỉnh hệ thống làm mát theo hợp kim và thiết kế bộ phận cụ thể có thể cải thiện đáng kể thời gian chu kỳ và giảm thiểu khuyết tật.
4. Những thách thức thường gặp trong quá trình làm mát đúc khuôn là gì?
Có một số thách thức có thể phát sinh trong quá trình làm mát đúc khuôn, thường dẫn đến tình trạng sản xuất kém hiệu quả và các bộ phận bị lỗi:
- Làm mát không đều: Nhiệt độ không đồng đều trong toàn bộ khuôn có thể dẫn đến quá trình đông đặc không đều, gây ra các khuyết tật như cong vênh và ứng suất dư.
- Mệt mỏi vì nhiệt: Các chu trình gia nhiệt và làm mát lặp đi lặp lại có thể gây ra hiện tượng mỏi nhiệt trong khuôn, làm giảm tuổi thọ của khuôn.
- Điểm nóng: Các khu vực có nhiệt độ quá cao cục bộ, được gọi là điểm nóng, có thể gây ra khuyết tật và làm hỏng khuôn.
- Làm mát không đủ: Công suất làm mát không đủ có thể kéo dài thời gian chu kỳ và hạn chế sản lượng.
- Cặn và ăn mòn: Các tạp chất trong nước làm mát có thể gây ra sự tích tụ cặn và ăn mòn trong các kênh làm mát, làm giảm hiệu quả.
Để giải quyết những thách thức này đòi hỏi một cách tiếp cận toàn diện, xem xét cả thiết kế của hệ thống làm mát và chất lượng của chất làm mát. Kinh nghiệm của chúng tôi trong Ngành công nghiệp hóa chất và dược phẩm, và Ngành công nghiệp điện tử, đã chỉ ra rằng việc bảo dưỡng thường xuyên và sử dụng chất làm mát chất lượng cao là điều cần thiết để ngăn ngừa nhiều vấn đề này.
5. Có những giải pháp làm mát tiên tiến nào dành cho đúc khuôn?
Để khắc phục những thách thức liên quan đến phương pháp làm mát truyền thống, một số giải pháp làm mát tiên tiến đã được phát triển:
- Làm mát theo hình dạng: Kỹ thuật này bao gồm việc tạo ra các kênh làm mát phù hợp với hình dạng của bộ phận, giúp làm mát đồng đều hơn.
- Chèn dẫn điện cao: Sử dụng vật liệu có độ dẫn nhiệt cao ở những khu vực quan trọng của khuôn có thể đẩy nhanh quá trình truyền nhiệt.
- Làm mát xung: Điều này bao gồm việc tuần hoàn dòng chất làm mát để cải thiện hiệu quả làm mát và giảm sốc nhiệt.
- Kênh làm mát vi mô: Các kênh nhỏ hơn cung cấp diện tích bề mặt lớn hơn để truyền nhiệt, nâng cao hiệu suất làm mát.
- Chất làm mát chuyên dụng: Chất làm mát được pha chế với tính chất nhiệt nâng cao và chất ức chế ăn mòn có thể cải thiện hiệu quả làm mát và bảo vệ khuôn.
Là nhà sản xuất máy làm lạnh công nghiệp, chúng tôi luôn đi đầu trong việc phát triển và triển khai các giải pháp làm mát tiên tiến này. Ví dụ, Máy làm lạnh Glycol đã được chứng minh là có hiệu quả cao trong Ngành Y tế và các Phòng thí nghiệm và Viện nghiên cứu, nơi kiểm soát nhiệt độ chính xác là tối quan trọng.
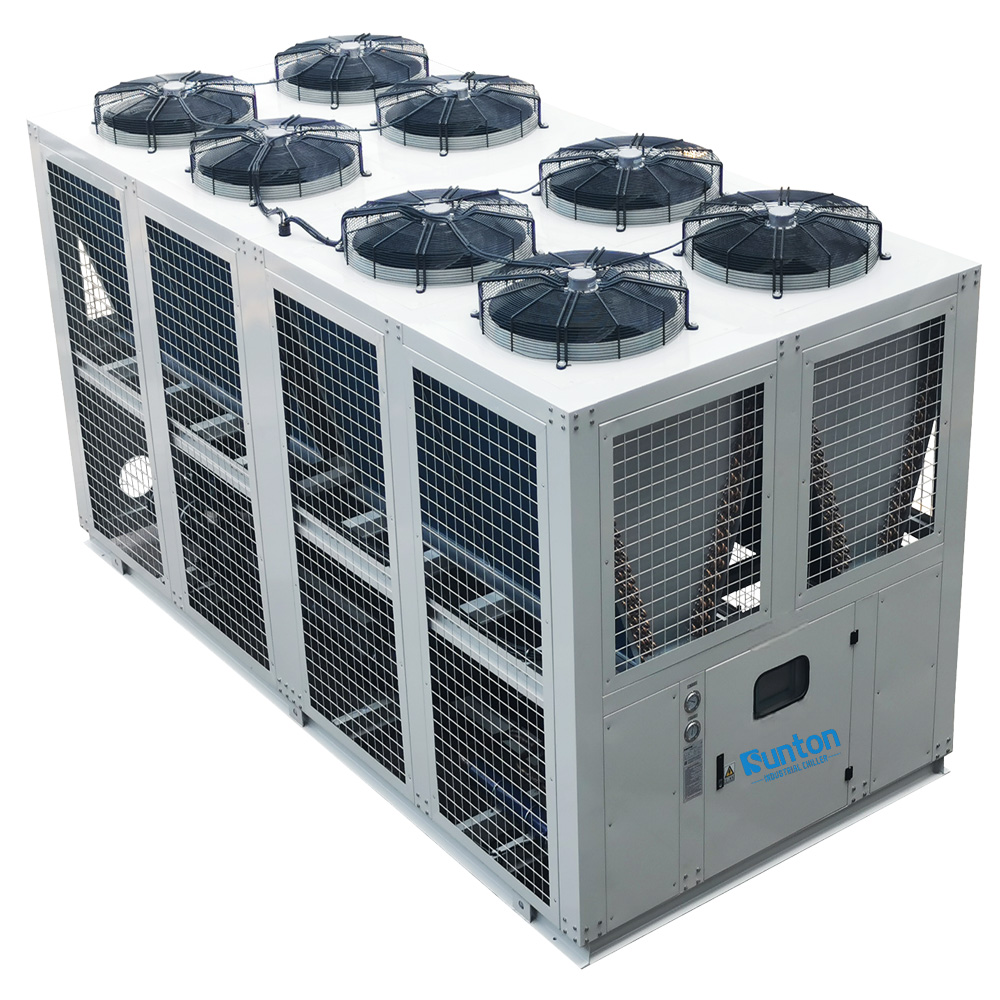
6. Làm thế nào để tối ưu hóa quá trình làm mát để đạt hiệu quả tối đa?
Việc tối ưu hóa quá trình làm mát trong đúc khuôn đòi hỏi một phương pháp tiếp cận đa chiều, xem xét nhiều yếu tố khác nhau:
- Thiết kế khuôn mẫu: Việc sử dụng các kỹ thuật tiên tiến như làm mát theo hình dạng và đặt các kênh làm mát một cách chiến lược có thể cải thiện đáng kể tính đồng nhất của quá trình làm mát.
- Lựa chọn chất làm mát: Việc lựa chọn chất làm mát phù hợp, có thể là nước, dầu hoặc chất lỏng chuyên dụng, và đảm bảo chất lượng của nó có thể tăng cường khả năng truyền nhiệt và ngăn ngừa các vấn đề như cặn và ăn mòn.
- Kiểm soát lưu lượng và áp suất: Tối ưu hóa lưu lượng và áp suất của chất làm mát đảm bảo tản nhiệt hiệu quả mà không gây áp lực quá mức lên khuôn.
- Theo dõi và kiểm soát nhiệt độ: Việc triển khai các cảm biến và hệ thống điều khiển để theo dõi và điều chỉnh nhiệt độ chất làm mát theo thời gian thực có thể duy trì khả năng làm mát ổn định.
- Bảo trì thường xuyên: Việc kiểm tra và bảo trì hệ thống làm mát thường xuyên, bao gồm vệ sinh kênh và kiểm tra rò rỉ, có thể ngăn ngừa tình trạng ngừng hoạt động bất ngờ.
7. Tác động của việc làm mát đến tuổi thọ của khuôn là gì?
Làm mát đóng vai trò quan trọng trong việc xác định tuổi thọ của khuôn đúc khuôn. Làm mát đúng cách có thể kéo dài tuổi thọ của khuôn bằng cách giảm mỏi nhiệt và ngăn ngừa hư hỏng do nhiệt độ quá cao. Khi khuôn phải chịu những thay đổi nhiệt độ nhanh và không đều, khuôn có thể bị nứt và các dạng hư hỏng khác làm giảm tuổi thọ hữu ích của khuôn.
Bằng cách đảm bảo làm mát đồng đều và có kiểm soát, ứng suất nhiệt trên khuôn được giảm thiểu, do đó kéo dài tuổi thọ của khuôn. Điều này không chỉ làm giảm tần suất thay thế khuôn tốn kém mà còn đảm bảo chất lượng bộ phận đồng nhất theo thời gian. Ví dụ, triển khai Máy làm lạnh trục vít làm mát bằng không khí có thể giúp duy trì nhiệt độ ổn định trong toàn bộ khuôn, giảm thiểu ứng suất nhiệt và kéo dài tuổi thọ khuôn. Chúng tôi đã thấy những cải thiện đáng kể về tuổi thọ khuôn trong số các khách hàng của chúng tôi trong Trung tâm dữ liệu và Ngành in ấn đã áp dụng các giải pháp làm mát tiên tiến của chúng tôi.
8. Tự động hóa đóng vai trò gì trong việc làm mát đúc khuôn?
Tự động hóa ngày càng trở nên quan trọng trong đúc khuôn, đặc biệt là trong việc kiểm soát quá trình làm mát. Các hệ thống làm mát tự động có thể theo dõi và điều chỉnh các thông số quy trình theo thời gian thực, đảm bảo làm mát hiệu quả và nhất quán. Các hệ thống này cũng có thể tích hợp với các khía cạnh khác của quy trình đúc khuôn, chẳng hạn như phun và đẩy, để tạo ra một dây chuyền sản xuất hoàn toàn tự động.
Tự động hóa không chỉ cải thiện khả năng lặp lại và độ chính xác của quá trình làm mát mà còn giảm nhu cầu kiểm soát và can thiệp thủ công. Điều này dẫn đến năng suất cao hơn, chi phí lao động thấp hơn và môi trường làm việc an toàn hơn. Ví dụ, Máy làm lạnh chống nổ được thiết kế với các tính năng tự động hóa tiên tiến, lý tưởng để sử dụng trong môi trường nguy hiểm.
9. Làm thế nào tôi có thể giảm thời gian chu kỳ bằng cách làm mát hiệu quả?
Giảm thời gian chu kỳ là mục tiêu chính trong đúc khuôn, vì nó tác động trực tiếp đến sản lượng và lợi nhuận. Làm mát hiệu quả đóng vai trò quan trọng trong việc đạt được thời gian chu kỳ ngắn hơn bằng cách nhanh chóng đông đặc kim loại nóng chảy và cho phép đẩy chi tiết ra nhanh hơn. Để giảm thời gian chu kỳ thông qua làm mát hiệu quả, hãy cân nhắc các chiến lược sau:
- Tối ưu hóa thiết kế kênh làm mát: Việc triển khai làm mát theo phương pháp phù hợp hoặc các thiết kế kênh tiên tiến khác có thể tăng cường truyền nhiệt và giảm thời gian làm mát.
- Tăng lưu lượng chất làm mát: Lưu lượng cao hơn có thể đẩy nhanh quá trình làm mát, nhưng phải cân bằng với nhu cầu tránh giảm áp suất quá mức.
- Sử dụng nhiệt độ chất làm mát thấp hơn: Việc hạ nhiệt độ chất làm mát có thể làm mát nhanh hơn, nhưng phải cẩn thận để tránh sốc nhiệt.
- Sử dụng công nghệ làm mát tiên tiến: Sử dụng các công nghệ như làm mát xung hoặc kênh làm mát vi mô có thể cải thiện hiệu quả làm mát.
- Tích hợp làm mát với tự động hóa quy trình: Tự động hóa quy trình làm mát và tích hợp nó với các khía cạnh khác của dây chuyền sản xuất có thể hợp lý hóa hoạt động và giảm tổng thời gian chu kỳ.
Bằng cách triển khai các chiến lược này, các nhà sản xuất có thể giảm đáng kể thời gian chu kỳ và tăng năng suất sản xuất. Khách hàng của chúng tôi trong Ngành công nghiệp Laser và Ngành công nghiệp Thực phẩm và Đồ uống đã báo cáo rằng thời gian chu kỳ giảm đáng kể sau khi triển khai các giải pháp làm mát được tối ưu hóa của chúng tôi, chẳng hạn như Tháp giải nhiệt.
10. Quá trình làm mát ảnh hưởng thế nào đến chất lượng của các bộ phận đúc khuôn?
Quá trình làm mát có tác động sâu sắc đến chất lượng của các bộ phận đúc khuôn. Làm mát đúng cách đảm bảo sự đông đặc đồng đều của kim loại nóng chảy, điều này rất cần thiết để đạt được các tính chất cơ học và độ chính xác về kích thước mong muốn. Làm mát không đủ hoặc không đều có thể dẫn đến nhiều khuyết tật khác nhau, bao gồm:
- Độ xốp: Không khí hoặc khí bị kẹt bên trong vật đúc có thể tạo ra các lỗ rỗng hoặc lỗ xốp, làm yếu bộ phận đó.
- Co ngót: Khi kim loại nguội đi và co lại, nó có thể co lại không đều, gây ra sự không chính xác về kích thước và ứng suất bên trong.
- Đóng cửa lạnh: Nếu kim loại nóng chảy nguội quá nhanh, chúng có thể không kết dính hoàn toàn với nhau, dẫn đến xuất hiện các đường hoặc vết nứt có thể nhìn thấy trên bề mặt.
- Biến dạng: Việc làm mát không đều có thể khiến bộ phận bị cong vênh hoặc biến dạng khi đông đặc.
- Ứng suất dư: Ứng suất bên trong do làm mát không đều có thể làm bộ phận yếu đi và dễ bị hỏng hơn khi chịu tải.
Bằng cách kiểm soát cẩn thận quá trình làm mát, các nhà sản xuất có thể giảm thiểu những khiếm khuyết này và sản xuất ra các bộ phận chất lượng cao với các đặc tính đồng nhất.
Chú ý (Mô hình bán hàng AIDA)
Đúc khuôn là một quy trình sản xuất chính xác, trong đó việc đạt được kết quả tối ưu phụ thuộc đáng kể vào việc kiểm soát nhiệt độ chính xác trong giai đoạn làm mát. Làm mát không đủ hoặc không đều thường dẫn đến tình trạng sản xuất kém hiệu quả và các bộ phận bị lỗi như xốp, co ngót và đóng nguội, ảnh hưởng đến chất lượng, độ chính xác về kích thước và thời gian chu kỳ sản xuất của sản phẩm đúc.
Quan tâm (Mô hình bán hàng AIDA)
Các giải pháp làm mát tiên tiến của chúng tôi, bao gồm Làm mát theo hình dạng, Chèn dẫn điện cao và Làm mát xung, được thiết kế để giải quyết những thách thức này. Bằng cách triển khai các công nghệ này, các nhà sản xuất có thể tăng đáng kể sản lượng sản xuất và cải thiện chất lượng sản phẩm. Ví dụ, Máy làm lạnh Glycol của chúng tôi đã chứng minh được hiệu quả cao trong các ngành công nghiệp đòi hỏi kiểm soát nhiệt độ chính xác, chẳng hạn như Ngành y tế và Phòng thí nghiệm.
Tính năng | Lợi ích |
Làm mát theo hình dạng | Làm mát đồng đều, giảm thiểu khuyết tật |
Chèn dẫn điện cao | Truyền nhiệt nhanh hơn, hiệu quả được cải thiện |
Làm mát xung | Nâng cao hiệu quả làm mát, giảm sốc nhiệt |
Chất làm mát chuyên dụng | Cải thiện tính chất nhiệt, chống ăn mòn |
Tự động hóa | Giám sát và kiểm soát thời gian thực, làm mát liên tục |
Sự mong muốn (Mô hình bán hàng AIDA)
Hãy tưởng tượng một quy trình đúc khuôn trong đó thời gian chu kỳ được giảm đáng kể, các khuyết tật được giảm thiểu và chất lượng sản phẩm luôn cao. Với các giải pháp làm mát được thiết kế riêng của chúng tôi, tầm nhìn này có thể trở thành hiện thực. Khách hàng của chúng tôi trong nhiều ngành công nghiệp khác nhau, bao gồm Ngành công nghiệp Laser và Ngành công nghiệp Thực phẩm và Đồ uống, đã báo cáo những cải tiến đáng kể trong quy trình sản xuất của họ sau khi triển khai hệ thống của chúng tôi. Bằng cách hợp tác với chúng tôi, bạn có thể đạt được:
- Giảm thời gian chu kỳ: Làm mát nhanh hơn có nghĩa là đẩy sản phẩm ra nhanh hơn và tăng năng suất sản xuất.
- Cải thiện chất lượng sản phẩm: Làm mát đồng đều đảm bảo các bộ phận có tính chất cơ học mong muốn và độ chính xác về kích thước.
- Tuổi thọ khuôn kéo dài: Làm mát đúng cách sẽ giảm thiểu ứng suất nhiệt, kéo dài tuổi thọ của khuôn.
- Hiệu quả nâng cao: Tự động hóa hợp lý hóa hoạt động, giảm chi phí lao động và cải thiện an toàn.
Hoạt động (Mô hình bán hàng AIDA)
Bạn đã sẵn sàng để chuyển đổi quy trình đúc khuôn của mình chưa? Liên hệ với chúng tôi ngay hôm nay để tìm hiểu thêm về các giải pháp làm mát tiên tiến của chúng tôi và cách chúng có thể mang lại lợi ích cho doanh nghiệp của bạn. Hãy để chúng tôi giúp bạn đạt được hiệu quả, chất lượng và lợi nhuận vô song trong hoạt động đúc khuôn của bạn. Đừng chần chừ nữa—hãy thực hiện bước đầu tiên để tối ưu hóa quy trình sản xuất của bạn ngay bây giờ!
Câu hỏi thường gặp
1. Nhiệt độ điển hình của nước làm mát dùng trong đúc khuôn là bao nhiêu?
Phạm vi nhiệt độ điển hình cho nước làm mát được sử dụng trong đúc khuôn là từ 20°C đến 40°C (68°F đến 104°F). Tuy nhiên, nhiệt độ tối ưu có thể thay đổi tùy thuộc vào các yếu tố như hợp kim cụ thể được đúc, hình dạng bộ phận và tốc độ làm mát mong muốn.
2. Tần suất vệ sinh kênh làm mát trong khuôn đúc khuôn là bao nhiêu?
Các kênh làm mát nên được vệ sinh thường xuyên để ngăn ngừa sự tích tụ của cặn, rỉ sét và các chất gây ô nhiễm khác có thể làm giảm hiệu quả làm mát. Tần suất vệ sinh phụ thuộc vào các yếu tố như chất lượng nước và loại chất làm mát được sử dụng, nhưng nguyên tắc chung là kiểm tra và vệ sinh các kênh từ 6 đến 12 tháng một lần.
3. Sử dụng nhiệt độ chất làm mát thấp hơn có thể làm hỏng khuôn không?
Trong khi sử dụng nhiệt độ chất làm mát thấp hơn có thể đẩy nhanh quá trình làm mát, nó cũng có thể làm tăng nguy cơ sốc nhiệt cho khuôn, có khả năng dẫn đến nứt hoặc hư hỏng khác. Điều quan trọng là phải cân bằng giữa việc làm mát nhanh và ngăn ngừa sốc nhiệt. Điều này có thể thực hiện bằng cách giảm dần nhiệt độ chất làm mát và theo dõi khuôn để tìm dấu hiệu ứng suất.
4. Ưu điểm của việc sử dụng dầu làm chất làm mát trong đúc khuôn là gì?
Dầu có thể được sử dụng làm chất làm mát trong đúc khuôn, đặc biệt là trong các ứng dụng yêu cầu nhiệt độ cao hơn. Một số lợi thế của việc sử dụng dầu bao gồm khả năng hoạt động ở nhiệt độ cao hơn mà không bị sôi, giảm nguy cơ ăn mòn so với nước và khả năng bôi trơn tốt hơn, có thể có lợi cho các bộ phận chuyển động bên trong khuôn.
5. Kích thước kênh làm mát ảnh hưởng đến hiệu quả làm mát như thế nào?
Kích thước của các kênh làm mát có tác động đáng kể đến hiệu quả làm mát. Các kênh nhỏ hơn cung cấp diện tích bề mặt lớn hơn để truyền nhiệt, có thể tăng cường hiệu suất làm mát. Tuy nhiên, các kênh nhỏ hơn cũng có thể dễ bị tắc nghẽn hơn và có thể yêu cầu áp suất chất làm mát cao hơn để duy trì lưu lượng thích hợp.
6. Vai trò của chốt lõi trong quá trình làm mát là gì?
Chốt lõi được sử dụng trong đúc khuôn để tạo ra các đặc điểm bên trong hoặc lỗ trong bộ phận đúc. Chúng cũng có thể đóng vai trò trong quá trình làm mát bằng cách cung cấp thêm bề mặt để truyền nhiệt. Trong một số trường hợp, chốt lõi có thể có các kênh làm mát bên trong riêng để giúp tản nhiệt từ vật đúc hiệu quả hơn.
Phần kết luận
- Làm mát là một khía cạnh quan trọng của quá trình đúc khuôn, ảnh hưởng đáng kể đến chất lượng sản phẩm, hiệu quả sản xuất và tuổi thọ của khuôn.
- Kiểm soát nhiệt độ thích hợp trong quá trình làm mát giúp ngăn ngừa các khuyết tật như xốp, co ngót và đóng lạnh.
- Các giải pháp làm mát tiên tiến như làm mát theo hình dạng, chèn dẫn điện cao và chất làm mát chuyên dụng có thể nâng cao hiệu suất làm mát.
- Việc tối ưu hóa quá trình làm mát liên quan đến việc cân nhắc cẩn thận về thiết kế khuôn, lựa chọn chất làm mát, lưu lượng và kiểm soát nhiệt độ.
- Tự động hóa đóng vai trò quan trọng trong việc đạt được khả năng làm mát hiệu quả và đồng đều, giảm thời gian chu kỳ và cải thiện năng suất chung.
- Việc bảo trì hệ thống làm mát thường xuyên là điều cần thiết để ngăn ngừa sự cố và đảm bảo hiệu suất lâu dài.
- Bằng cách áp dụng các chiến lược làm mát hiệu quả, các nhà sản xuất đúc khuôn có thể đạt được thời gian chu kỳ ngắn hơn, chất lượng sản phẩm cao hơn và lợi nhuận tăng lên.
Bằng cách hiểu và giải quyết các yếu tố khác nhau ảnh hưởng đến quá trình làm mát trong đúc khuôn, các nhà sản xuất có thể tối ưu hóa quy trình của mình, cải thiện chất lượng sản phẩm và giành được lợi thế cạnh tranh trên thị trường. Là nhà sản xuất máy làm lạnh nước công nghiệp, chúng tôi cam kết cung cấp các giải pháp làm mát sáng tạo đáp ứng nhu cầu ngày càng phát triển của ngành đúc khuôn.
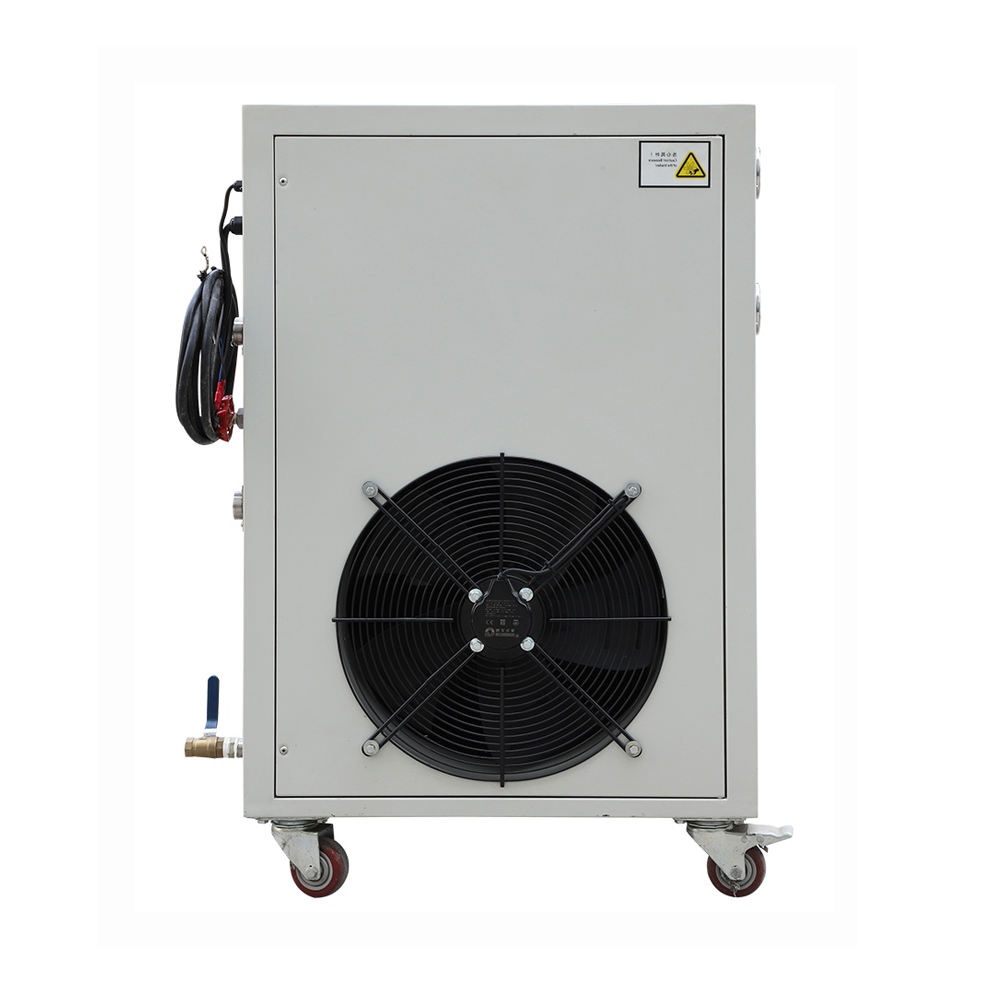