-
Даліншань Індастріал Гуандун
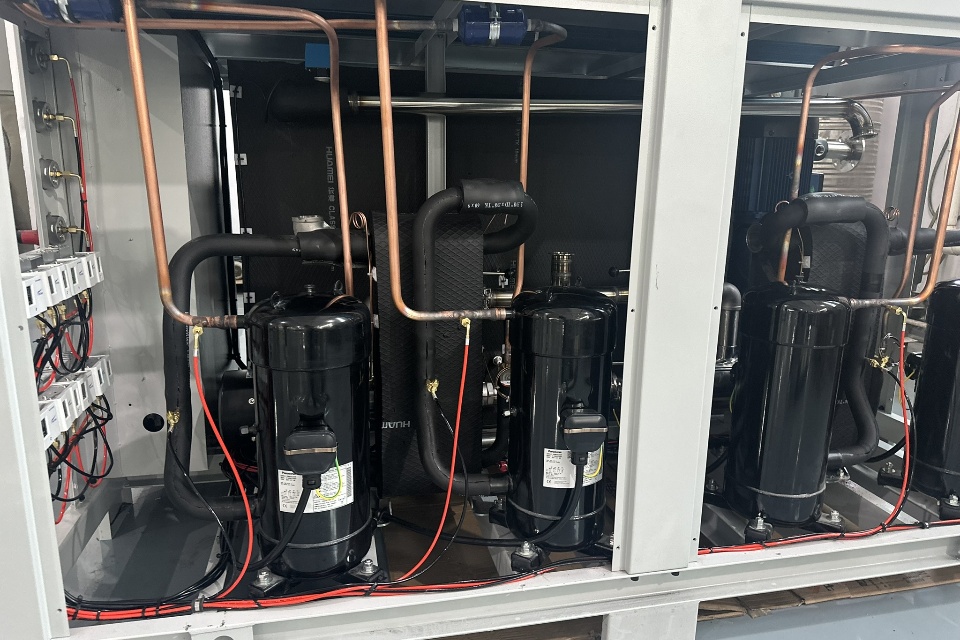
Чиллер для промислових процесів для напівпровідників
Висока точність: охолоджувачі рідини та системи обігріву, які використовуються для досліджень, мають вирішальне значення. Важлива роль чиллерів у напівпровідниковій промисловості
Зміст
Напівпровідникова промисловість є основою сучасних технологій, яка забезпечує живлення всього, від наших смартфонів до передового медичного обладнання. Але чи знаєте ви, що точний контроль температури є життєво важливим для підвищення врожайності під час швидких термічних процесів. є абсолютно критичним у виробництві напівпровідників? Тут на допомогу приходять промислові чиллери, які відіграють важливу роль за кадром. У цій статті ми дослідимо, чому чиллери є незамінними для напівпровідникової промисловості, різні доступні типи та як правильний чиллер може оптимізувати ваш виробничий процес. Ми також розглянемо, як вибір правильного чиллера може підвищити ефективність, зменшити витрати та, зрештою, призвести до вищої якості напівпровідників. Отже, якщо ви займаєтеся виробництвом напівпровідників, це обов’язково потрібно прочитати!
Опис статті:
- Що таке чиллер і чому він важливий для напівпровідникової промисловості?
- Як чиллери впливають на процес виробництва напівпровідників?
- Які конкретні вимоги до контролю температури під час виробництва напівпровідників?
- Типи холодильних установок, які використовуються у виробництві напівпровідників: глибоке занурення
- Вибір правильного охолоджувача для вашого напівпровідникового застосування: ключові міркування
- Оптимізація продуктивності чиллера для максимальної ефективності та надійності
- Аналіз витрат і вигод: інвестиції в правильну систему охолодження
- Майбутні тенденції в технології чиллерів для напівпровідникової промисловості
- Тематичні дослідження: реальні приклади застосування холодильних установок у напівпровідникових установках
- Технічне обслуговування та усунення несправностей напівпровідникових чиллерів
Що таке чиллер і чому він важливий для напівпровідникової промисловості?
Чиллер — це система охолодження, яка відбирає тепло від процесу або програми та передає його в інше місце. Уявіть собі холодильник, але в набагато більшому, промисловому масштабі. У напівпровідниковій промисловості охолоджувач для напівпровідників є абсолютно необхідним, оскільки виробничий процес неймовірно чутливий до коливань температури. Напівпровідник пристрої побудовані на пластинах, виготовлених із таких матеріалів, як кремній. Процес виробництва напівпровідників включає численні етапи, такі як травлення, осадження та літографія, усі з яких виділяють значну кількість тепла. Якщо цим теплом не керувати точно, це може призвести до дефектів, зниження врожайності та навіть повного виходу продукту з ладу. Чиллер забезпечує точний контроль температури, гарантуючи, що кожен етап процесу відбувається в оптимальних умовах. BV Thermal Systems спеціалізується на економічно ефективних напівпровідникових рішеннях, наприклад, надає такі ключові теплові системи.
Подумайте про випікання торта: якщо температура в духовці неправильна, торт не підніметься належним чином. Подібним чином у виробництві напівпровідників навіть незначні коливання температури можуть мати величезний вплив. Чиллери призначені для підтримки стабільної температури, забезпечуючи плавний та ефективний процес виробництва напівпровідників. Цей точний контроль температури життєво важливий для досягнення високих врожаїв під час швидкої термічної обробки. Напівпровідникова промисловість покладається на чиллери для видалення надлишкового тепла та підтримки необхідної стабільності температури.
Як чиллери впливають на процес виробництва напівпровідників?
Чиллери мають значний вплив на кожен етап процесу виробництва напівпровідників. Від вирощування кристалів кремнію до упаковки кінцевих чіпів точний контроль температури не підлягає обговоренню. Наприклад, під час швидкої термічної обробки кремнієвих пластин охолоджувачі допомагають підтримувати точні температури, необхідні для точного легування та відпалу. Без цієї точності електричні властивості напівпровідникового матеріалу були б скомпрометовані. Процес вимагає неймовірно стабільної температури середовища. Чиллер забезпечує це.
Крім того, охолоджувачі відіграють вирішальну роль у фотолітографії, ключовому етапі виготовлення напівпровідників, де схеми схем витравлюються на пластинах. Процес виготовлення напівпровідників надзвичайно чутливий до коливань температури. Чиллери використовуються для охолодження обладнання та хімікатів, що використовуються в цьому процесі, запобігаючи спотворенням і забезпечуючи точну передачу малюнка. Крім того, чиллери використовуються для охолодження обладнання, що використовується в автоматизованих системах оптичного контролю напівпровідників. Ці системи часто виділяють значну кількість тепла, а чиллери запобігають перегріву та забезпечують точні результати перевірки. Сучасне виробництво напівпровідників покладається на чиллери, які забезпечують точне регулювання температури, таким чином підвищуючи контроль якості та загальну продуктивність під час швидкої термічної обробки.
Які конкретні вимоги до контролю температури під час виробництва напівпровідників?
Напівпровідникова промисловість вимагає надзвичайно жорстких температурних допусків, часто в межах часток градуса Цельсія. Конкретні вимоги до температури змінюються залежно від конкретного етапу процесу виробництва напівпровідників. Наприклад, для кремнієвих пластин для напівпровідника може знадобитися інший контроль температури, ніж для хімічних ванн, які використовуються для травлення. Для деяких процесів можуть знадобитися температури до -80°C, а для інших – сотні градусів Цельсія. Чиллери для метрології напівпровідників повинні бути особливо точними. Напівпровідниковий процес є складним, і кожен етап потребує певного теплового середовища.
Потужність охолодження, необхідна для певного застосування, залежить від різних факторів, включаючи тепло, що виділяється обладнанням, температуру навколишнього середовища та бажану задану температуру. Напівпровідникові системи мають особливі потреби, і правильний чиллер може досягти необхідної стабільності температури. Ці системи часто працюють у режимі 24/7, тому чиллери мають бути надійними та здатними підтримувати постійну продуктивність протягом тривалого часу. Холодильники забезпечують необхідне керування температурою, щоб відповідати цим суворим вимогам. Сама система охолоджувача потребує моніторингу та обслуговування, щоб забезпечити її постійну точність.
Типи холодильних установок, які використовуються у виробництві напівпровідників: глибоке занурення
У напівпровідниковій промисловості використовується кілька типів чилерів, кожен з яких має свої переваги та недоліки. Рециркуляційні холодильні машини є звичайними, і вони працюють шляхом безперервної циркуляції теплоносія через систему для видалення тепла. Існує дві основні категорії: рециркуляційні холодильні машини з охолодженою рідиною та неохолоджені системи відведення тепла.
- Холодильні чиллери: Ці чиллери використовують холодоагент для охолодження теплоносія, забезпечуючи точне та потужне охолодження. Вони бувають різних конфігурацій, включаючи моделі з водяним і повітряним охолодженням. Гвинтовий охолоджувач води з водяним охолодженням часто використовуються для великих застосувань з високим тепловим навантаженням.
- Термоелектричні чиллери: Ці чиллери використовують ефект Пельтьє для створення різниці температур і відведення тепла. Термоелектричні чиллери розроблені для застосувань, де важливі компактні розміри та точне регулювання температури. Вибухозахищені охолоджувачі забезпечують додатковий рівень безпеки в середовищах з небезпечними матеріалами. Вони є різновидом термоелектричних чиллерів і стають все більш популярними в напівпровідниковій промисловості завдяки своїй ефективності та невеликій площі.
- Занурювальні чиллери: Ці чиллери безпосередньо охолоджують технологічну рідину шляхом занурення охолоджувальної котушки або зонда в рідину. Вони часто використовуються для додатків, які вимагають швидкого охолодження або де простір обмежений.
- Технологічні чиллери: ці холодильні машини розроблені для спеціальних промислових процесів, таких як виробництво напівпровідників. Гвинтова охолоджувальна машина з повітряним охолодженням є прикладом, що пропонує міцну продуктивність і надійність.
Вибір правильного охолоджувача для вашого напівпровідникового застосування: ключові міркування
Вибір правильного чиллера є критично важливим рішенням, яке може значно вплинути на ефективність, надійність і економічну ефективність виробництва напівпровідників. Слід враховувати кілька факторів:
- Потужність охолодження: Чиллер повинен мати достатню охолоджувальну потужність, щоб справлятися з тепловим навантаженням, яке створює процес. Зазвичай це вимірюється в кіловатах (кВт) або BTU/год. Потужності охолодження в 400 Вт може бути достатньо для деяких метрологічних застосувань, тоді як більшим об’єктам можуть знадобитися чиллери потужністю в десятки або сотні кіловат. Враховуйте поточні та майбутні потреби в охолодженні.
- Температурний діапазон і стабільність: Чиллер повинен бути здатний підтримувати необхідний температурний діапазон і стабільність для конкретного напівпровідникового застосування. Шукайте чиллери, які забезпечують точний контроль температури, як правило, в межах ±0,1°C або краще.
- Сумісність охолоджуючої рідини: Чиллер і його компоненти повинні бути сумісні з теплоносієм, який використовується в процесі виробництва напівпровідників. Для деяких процесів можуть знадобитися спеціальні охолоджуючі рідини для запобігання корозії або забрудненню.
- Надійність і технічне обслуговування: Вибирайте чиллер від авторитетного виробника з перевіреною репутацією надійності. Враховуйте зручність обслуговування та наявність запчастин. Час простою може бути надзвичайно дорогим у виробництві напівпровідників.
- Вартість володіння: Оцініть загальну вартість володіння напівпровідниковим обладнанням, включаючи початкову ціну придбання, витрати на встановлення, експлуатаційні витрати та витрати на обслуговування. Рециркуляційні чилери є кращим варіантом у довгостроковій перспективі, якщо вам потрібно заощадити гроші.
- Вимоги до площі та місця: Переконайтеся, що холодильна машина поміщається в межах наявного простору в приміщенні. Термоелектричні рециркуляційні чиллери займають меншу площу порівняно з більшими компресорними системами.
Оптимізація продуктивності чиллера для максимальної ефективності та надійності
Після вибору правильного чиллера дуже важливо оптимізувати його продуктивність для досягнення максимальної ефективності та надійності. Ось кілька ключових стратегій:
- Правильне встановлення та налаштування: Переконайтеся, що холодильну машину встановлено правильно та всі з’єднання належним чином загерметизовано. Дотримуйтеся вказівок виробника щодо встановлення та запуску.
- Регулярне технічне обслуговування: Впроваджуйте програму профілактичного обслуговування, включаючи регулярні перевірки, очищення та обслуговування чилера та його компонентів. Це може допомогти запобігти несподіваним поломкам і продовжити термін служби обладнання. Холодильники розраховані на тривалий термін служби, але вони пропрацюють лише за умови належного обслуговування. Старіші системи на основі компресорів. Старішим типам напівпровідників може знадобитися більше уваги, ніж новим, вдосконаленим.
- Керування охолоджуючою рідиною: Слідкуйте за системою рідинного охолодження навколишнього середовища для досягнення оптимальної продуктивності. регулярно перевіряйте рівень і якість охолоджуючої рідини. За потреби замініть охолоджуючу рідину, щоб зберегти її ефективність і запобігти корозії. Суміш рекомендується використовувати для запобігання біологічного росту в системі.
- Балансування навантаження: Якщо це можливо, рівномірно розподіліть охолоджувальне навантаження між кількома холодильними установками. Це може підвищити ефективність і зменшити знос окремих блоків. Теплове навантаження постійно змінюється, тому необхідні інтелектуальні засоби керування.
- Заходи з енергоефективності: Впроваджуйте енергозберігаючі методи, такі як оптимізація робочих параметрів і використання приводів із змінною швидкістю для насосів і вентиляторів. Сучасні чиллери часто мають розширені функції енергозбереження. Наприклад, твердотільна термоелектрична технологія зменшує споживання енергії, що призводить до зниження експлуатаційних витрат.
- Моніторинг та аналіз даних: Використовуйте системи моніторингу чиллера для відстеження даних про продуктивність, таких як температура, тиск і споживання енергії. Ці дані можна використовувати для виявлення потенційних проблем і оптимізації робочих параметрів. Сучасні системи охолодження включають вдосконалені датчики та діагностичні засоби.
Аналіз витрат і вигод: інвестиції в правильну систему охолодження
Інвестиції у високоякісну холодильну систему становлять значні початкові витрати, але вони можуть принести значні довгострокові вигоди. Добре спроектована та обслуговувана холодильна система може:
- Поліпшення якості продукції: Точний контроль температури веде до вищого виходу під час швидкої термічної обробки та меншої кількості дефектів, що призводить до вищої якості напівпровідникових пристроїв. Це означає підвищення задоволеності клієнтів і вищі ціни продажу.
- Підвищення ефективності виробництва: Надійні чиллери мінімізують час простою та забезпечують плавну та ефективну роботу процесу виробництва напівпровідників. Це призводить до підвищення продуктивності та зниження витрат виробництва.
- Зменшення споживання енергії: Енергоефективні холодильні машини можуть значно знизити експлуатаційні витрати, особливо в приміщеннях з високими вимогами до охолодження. Сучасні чиллери часто включають такі функції, як приводи зі змінною швидкістю та розширені алгоритми керування для оптимізації використання енергії. Деякі сучасні компресорні системи набагато ефективніші за старіші версії.
- Подовження терміну служби обладнання: Належний контроль температури може продовжити термін служби обладнання для виробництва напівпровідників, зменшивши потребу у дорогих замінах. Сам охолоджувач, якщо його доглядати, також матиме довший термін служби.
- Підвищення безпеки: Надійні чиллери можуть запобігти перегріву та іншим загрозам безпеці, захищаючи як персонал, так і обладнання. Схвалені UL для використання в промислових лабораторіях, деякі чиллери пропонують гарантовані функції безпеки.
Ретельний аналіз витрат і вигод повинен враховувати всі ці фактори, щоб визначити оптимальну інвестицію в систему охолодження. Хоча нижча початкова ціна може здаватися привабливою, якісніший і ефективніший холодильний агрегат часто може забезпечити кращу віддачу від інвестицій протягом усього терміну експлуатації.
Майбутні тенденції в технології чиллерів для напівпровідникової промисловості
Напівпровідникова промисловість постійно розвивається, і технологія чиллерів не відстає від неї. Кілька тенденцій формують майбутнє чиллерів для напівпровідникових систем:
- Підвищена енергоефективність: Оскільки витрати на електроенергію продовжують зростати, а проблеми з навколишнім середовищем зростають, наголошується на розробці більш енергоефективних чиллерів. Це включає використання передових холодоагентів, приводів із змінною швидкістю та складних алгоритмів керування. Термоелектрична технологія зменшує кількість рухомих частин, що призводить до меншого споживання енергії.
- Менший розмір: На підприємствах з виробництва напівпровідників часто мало місця, тому існує попит на чиллери з меншою площею. Термоелектричні чиллери пропонують значну перевагу в цьому відношенні.
- Покращений контроль температури та стабільність: У міру того, як напівпровідникові пристрої стають все складнішими та вимагають жорсткіших температурних допусків, чиллери розроблені для забезпечення ще більшої точності та стабільності. Сучасні холодильні машини використовують вдосконалені датчики та системи контролю зі зворотним зв’язком для підтримки точних заданих температур. Підвищена стабільність і тепловий захист для чутливого обладнання є ключовим напрямком.
- Розумні чиллери та інтеграція IoT: Чиллери стають все більш інтелектуальними, з вбудованими датчиками, мікропроцесорами та можливостями зв’язку. Це дозволяє здійснювати дистанційний моніторинг, діагностику та контроль, а також інтеграцію з іншими системами виробництва напівпровідників через Інтернет речей (IoT).
- Використання альтернативних холодоагентів: Через проблеми з навколишнім середовищем щодо традиційних холодоагентів зростає тенденція до використання альтернативних холодоагентів із нижчим потенціалом глобального потепління (GWP). До них належать природні холодоагенти, такі як CO2 і аміак, а також синтетичні холодоагенти з покращеними екологічними профілями. Деякі підприємства намагаються повністю відмовитися від використання шкідливих холодоагентів.
- Розширені системи управління температурою: Чиллери майбутнього будуть інтегровані в більш комплексні системи управління температурою, які оптимізують охолодження всього підприємства з виробництва напівпровідників. Це передбачатиме використання передових датчиків, аналітику даних і складні стратегії контролю. Зростаючі вимоги до управління температурою напівпровідникових установок стимулюють ці інновації. Це стосується систем, які можуть у режимі реального часу пристосовуватися до динамічних теплових навантажень у процесі виробництва напівпровідників.
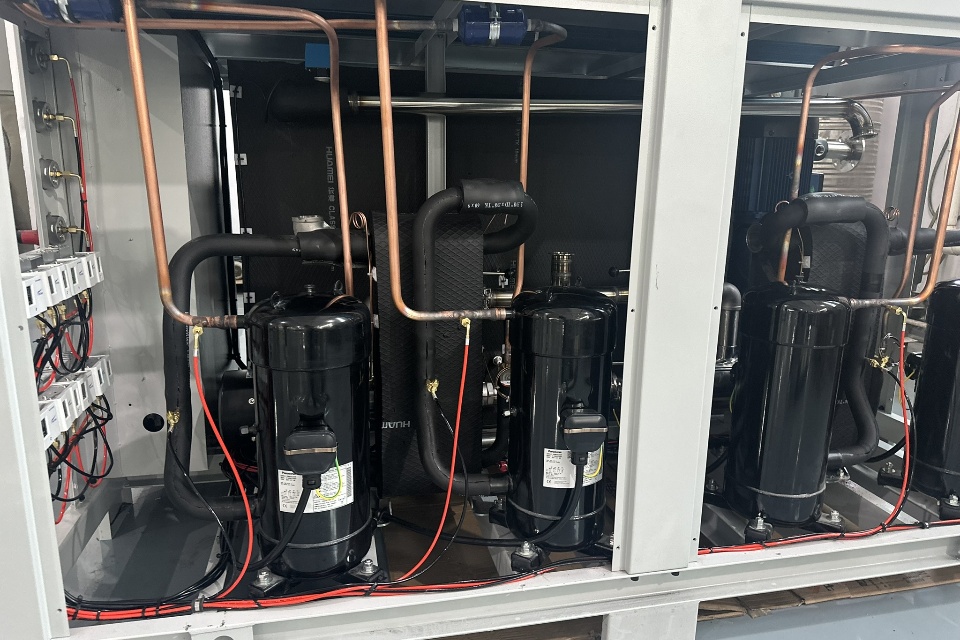
Тематичні дослідження: реальні приклади застосування холодильних установок у напівпровідникових установках
Давайте розглянемо деякі конкретні приклади того, як чиллери використовуються в реальних підприємствах з виробництва напівпровідників:
Приклад 1: Провідний напівпровідниковий холодильний пристрій може підвищити ефективність. виробник напівпровідників зіткнувся з проблемами продуктивності через температурні коливання під час швидкої термічної обробки кремнієвих пластин. Вони впровадили нову систему охолодження з покращеними можливостями контролю температури, що призвело до збільшення врожайності 5% і значного скорочення брухту. Нові чиллери забезпечували стабільну температуру в межах +/- 0,05°C.
Приклад 2: Підприємство з виробництва напівпровідників боролося з високими витратами на електроенергію, пов’язаними зі старішою системою охолодження. Вони замінили старі чиллери на сучасні, енергоефективні моделі, що призвело до зниження споживання енергії та значної економії коштів. Нові чиллери також мали меншу площу, що звільнило цінний простір у приміщенні. Спіральний охолоджувач води з повітряним охолодженням було обрано через їх меншу площу.
Приклад 3: Напівпровідникова компанія розробляла нову автоматизовану метрологічну систему з використанням лазерів. Ці системи вимагають високоточного контролю температури, щоб підтримувати точність лазерних вимірювань. Вони впровадили термоелектричний охолоджувач із високою продуктивністю та точною стабільністю температури, що дозволяє їм досягти необхідної точності вимірювань. Чиллер зміг забезпечити потужність охолодження 400 Вт, зберігаючи стабільність температури в межах ±0,01°C.
Приклад 4: У спробі підвищити врожайність під час швидкої термічної обробки, напівпровідникова компанія звернулася до більш просунутих термічних рішень. Вони модернізували своє підприємство холодильними установками, які забезпечують точний контроль температури, що має вирішальне значення для чутливого процесу термічної обробки кремнієвих пластин. Це призвело не тільки до підвищення врожайності, але й до зменшення теплового навантаження на обладнання, подовження терміну його експлуатації та сприяння більш стабільному виробничому процесу. Покращена температурна стабільність також позитивно вплинула на якість продукції, що дозволило їм відповідати строгим специфікаціям своїх клієнтів у таких галузях, як авіакосмічна промисловість і телекомунікації. Низькотемпературні охолоджувальні рішення для чиллерів | Передові технології охолодження дав їм необхідну точність.
Приклад 5: головний гравець у напівпровідниковій промисловості зіткнувся з проблемами, пов’язаними з вартістю володіння автоматизованим оптичним обладнанням для контролю напівпровідників. Точкове охолодження систем метрологічного контролю виявилося дорогим із наявною установкою, яка покладалася на вентилятори або навколишнє рідинне охолодження. Вони вирішили впровадити термоелектричні рециркуляційні чиллери, які були потрібні для точкового охолодження та були набагато більш енергоефективними. Ця зміна призвела до значного зниження експлуатаційних витрат і підвищила надійність процесу перевірки. Крім того, це рішення призвело до більшої стабільності в термоуправлінні автоматизованих систем оптичного контролю напівпровідників. Оскільки охолоджувачі на термоелектричній основі розроблені для точного контролю температури, системи перевірки тепер постійно працюють при оптимальних температурах, покращуючи якість перевірки та мінімізуючи потребу в повторному калібруванні, ще більше скорочуючи час простою та вартість володіння напівпровідниковими автоматизованими оптичними системами. Охолоджувач води з водяним охолодженням пропонують універсальне рішення для таких потреб.
Ці тематичні дослідження демонструють вирішальну роль, яку чиллери відіграють в оптимізації
64,3s arrow_upwardarrow_downwardeditmore_vert
продовжити arrow_upwardarrow_downwardeditmore_vert
процеси виробництва напівпровідників, покращення якості продукції, підвищення ефективності та зниження витрат.
Технічне обслуговування та усунення несправностей напівпровідникових чиллерів
Належне технічне обслуговування має важливе значення для забезпечення надійної та ефективної роботи напівпровідникових чилерів. Програма профілактичного обслуговування може запобігти неочікуваним поломкам, продовжити термін служби обладнання та мінімізувати час простою. Основні завдання технічного обслуговування включають:
- Регулярні перевірки: Регулярно перевіряйте систему охолодження на наявність витоків, корозії та інших ознак зносу. Перевірте рівень, тиск і температуру охолоджуючої рідини.
- Прибирання: Регулярно очищуйте змійовики конденсатора, змійовики випарника та фільтри, щоб забезпечити оптимальну теплопередачу. Брудні змійовики можуть значно знизити ефективність чиллера.
- Аналіз та обробка охолоджуючої рідини: Періодично аналізуйте охолоджуючу рідину, щоб переконатися, що вона відповідає специфікаціям. За потреби обробіть охолоджуючу рідину, щоб запобігти корозії та біологічному розвитку.
- Змащення: Змащуйте насоси, вентилятори та інші рухомі частини відповідно до рекомендацій виробника.
- Калібрування: Регулярно калібруйте датчики температури та системи керування, щоб забезпечити точний контроль температури. Контроль температури напівпровідникових процесів значною мірою залежить від точності цих датчиків.
- Моніторинг продуктивності: Відстежуйте дані продуктивності чиллера, такі як температура, тиск і споживання енергії, щоб завчасно виявити потенційні проблеми. Ці дані можна використовувати для оптимізації робочих параметрів і запобігання збоїв.
- Облік: Вести детальний облік усіх заходів з технічного обслуговування, включаючи перевірки, ремонти та зміни охолоджуючої рідини.
Незважаючи на регулярне технічне обслуговування, час від часу у чиллерах можуть виникати проблеми. Загальні дії щодо усунення несправностей включають:
- Перевірте наявність сигналів тривоги та кодів помилок: Більшість сучасних чиллерів мають вбудовані системи діагностики, які відображають сигнали тривоги та коди помилок. Зверніться до посібника з чиллера, щоб розтлумачити ці коди та визначити джерело проблеми.
- Перевірте електричні з’єднання: Перевірте, чи немає ослаблених чи корозійних електричних з’єднань, оскільки вони можуть спричинити несправності холодильної машини.
- Перевірте потік охолоджуючої рідини: Переконайтеся, що в системі є достатній потік теплоносія. Низький потік теплоносія може призвести до перегріву та зниження холодопродуктивності.
- Перевірте заправку холодоагенту: Якщо холодильна машина використовує холодоагент, переконайтеся, що холодоагент заправлений правильно. Низька кількість холодоагенту може свідчити про витік.
- Перевірте компресор: Компресор є важливим компонентом багатьох чилерів. Огляньте компресор на наявність ознак зносу або пошкодження.
Якщо кроки з усунення несправностей не принесли результатів, найкраще звернутися до кваліфікованого спеціаліста з обслуговування чиллера. Чиллери є кращим варіантом, якщо вони працюють за призначенням, але для вирішення складних проблем потрібні навчені спеціалісти.
поширені запитання:
Чому контроль температури такий важливий у напівпровідниковій промисловості?
Контроль температури має вирішальне значення, оскільки процес виробництва напівпровідників включає надзвичайно чутливі матеріали та процеси. Навіть незначні коливання температури можуть призвести до дефектів, зниження врожайності та псування продукції. Виробництво напівпровідникових приладів вимагає неймовірно стабільного теплового середовища.
Які переваги використання термоелектричних чиллерів у виробництві напівпровідників?
Термоелектричні чиллери пропонують ряд переваг, включаючи компактні розміри, точне регулювання температури, високу надійність і низький рівень шуму. Вони також є екологічно чистими, оскільки не використовують холодоагенти з високим потенціалом глобального потепління. Крім того, термоелектричні рециркуляційні чиллери особливо ефективні для точкового охолодження. Вони також ідеально підходять для охолодження напівпровідникового метрологічного обладнання.
Як я можу визначити відповідну потужність охолодження для мого напівпровідникового застосування?
Необхідна потужність охолодження залежить від кількох факторів, зокрема від тепла, що виділяється обладнанням, температури навколишнього середовища та бажаної заданої температури. Щоб визначити необхідну потужність охолодження, слід виконати розрахунок теплового навантаження. Не забудьте врахувати теплове навантаження всієї системи. Загалом рециркуляційні холодильні машини є кращим засобом для роботи з вимогливими промисловими додатками, а чиллери є кращим варіантом для точного керування температурою.
Які типові завдання з технічного обслуговування напівпровідникових чиллерів?
Загальні завдання технічного обслуговування включають регулярні перевірки, очищення, аналіз та обробку охолоджуючої рідини, змащування, калібрування, моніторинг продуктивності та ведення записів. Технологічні чиллери часто вимагають спеціального догляду та технічного обслуговування.
Як я можу покращити енергоефективність моєї напівпровідникової системи охолодження?
Енергоефективність можна підвищити за допомогою належного встановлення та налаштування, регулярного технічного обслуговування, управління охолоджувачем, балансування навантаження, енергозберігаючих практик, а також моніторингу й аналізу даних. Сучасні чиллери часто мають розширені функції енергозбереження. Розгляньте можливість оновлення до новіших сучасних компресорних систем для підвищення ефективності.
Які останні тенденції в технологіях чиллерів для напівпровідникової промисловості?
Останні тенденції включають підвищення енергоефективності, зменшення займаної площі, покращений контроль температури та стабільність, розумні чиллери та інтеграцію Інтернету речей, а також використання альтернативних холодоагентів. Ці досягнення спрямовані на задоволення зростаючих потреб напівпровідникової промисловості. Складний характер виготовлення напівпровідників вимагає постійних інновацій у рішеннях для охолодження.
- Точний контроль температури не підлягає обговоренню: Чиллери необхідні для підтримки надзвичайно жорстких температурних допусків, необхідних у виробництві напівпровідників. Навіть невеликі відхилення можуть призвести до значних проблем з якістю та втрат урожаю.
- Чиллери впливають на кожен етап виробництва: Чиллери відіграють важливу роль у забезпеченні стабільного та контрольованого теплового середовища від росту кристалів кремнію до остаточного упакування мікросхем.
- Вибір правильного охолоджувача має вирішальне значення: Необхідно ретельно враховувати такі фактори, як потужність охолодження, стабільність температури, сумісність з теплоносіями, надійність, вартість володіння та площа.
- Оптимізація та технічне обслуговування є ключовими: Регулярне технічне обслуговування, правильне встановлення та енергозберігаючі практики можуть максимізувати продуктивність чилера, зменшити витрати та продовжити термін служби обладнання.
- Технологія прогресує: Майбутнє чилерів для напівпровідникової промисловості передбачає підвищення енергоефективності, меншу площу, розумніші засоби керування та використання альтернативних холодоагентів.
- Інвестиції в правильний холодильний апарат окупаються: Хоча початкові інвестиції можуть бути значними, високоякісна холодильна система може призвести до покращення якості продукції, підвищення ефективності, зменшення споживання енергії та кращого прибутку. Вибір і технічне обслуговування правильного чиллера для напівпровідникових застосувань має важливе значення для успіху в цій складній галузі.
На закінчення:
Розуміючи вирішальну роль холодильних машин, різноманітні доступні типи та найкращі методи вибору, експлуатації та обслуговування, виробники напівпровідників можуть забезпечити безперебійну, ефективну та прибуткову роботу їхніх виробничих процесів. Для всіх ваших потреб у промислових чиллерах шукайте лише надійного досвідченого постачальника, який спеціалізується на теплових системах для виробництва напівпровідників. BV Thermal Systems, наприклад, має великий досвід у наданні теплових рішень для сектору напівпровідників і має Гвинтові центральні охолоджувачі з повітряним охолодженням. Якщо у вашому виробництві чи випробуваннях використовуються лазери як джерело тепла, високоточний холодильний агрегат є обов’язковим. Не забувайте досліджувати Гвинтові центральні охолоджувачі з водяним охолодженням опції також для досягнення точного керування температурою.