-
Даліншань Індастріал Гуандун
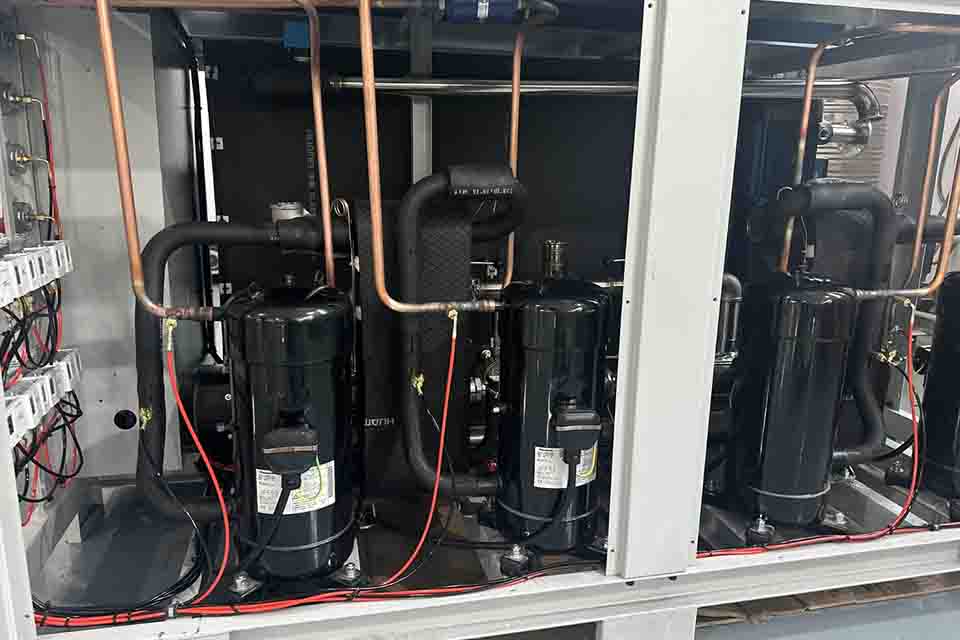
Промислові охолоджувачі для машин для видування пляшок: Повний посібник
Промислові охолоджувачі для машин для видування пляшок: Повний посібник
У цьому посібнику розглядається критична роль чиллерів, зокрема промислових водяних охолоджувачів, в оптимізації операцій видування пляшок. Від розуміння різних типів чиллерів до вибору правильного розміру чиллера та впровадження найкращих практик технічного обслуговування, ця стаття містить цінну інформацію для всіх, хто бере участь у видуванні пляшок або видувному формуванні. Ми розглянемо все, від базових принципів охолодження до передових технологій чиллерів, що дасть вам змогу приймати обґрунтовані рішення, які підвищать якість продукту, підвищать ефективність і підвищать прибутки.
Зміст
Що таке чиллер і чому він важливий для машин для видування пляшок?
Чиллер — це, по суті, система охолодження, призначена для охолодження технологічної води, яка потім використовується для регулювання температури машин і обладнання. У контексті машин для видування пляшок або машин для видувного формування чиллери відіграють абсолютно важливу роль. Вони забезпечують швидке та контрольоване охолодження форм, що є ключовим аспектом для виробництва високоякісних пластикових пляшок. Без належного функціонування охолоджувача процес формування може стати неефективним, що призведе до таких дефектів, як викривлення, неоднорідна товщина стінок і подовжені цикли формування.
Машини для видування пляшок, які використовуються для виготовлення різних пластикових пляшок, виділяють значну кількість тепла під час роботи, що вимагає використання холодильної машини з охолодженням. Цим теплом потрібно ефективно керувати, щоб зберегти цілісність пластику та ефективність виробничого процесу. Саме тут вступає в дію наш асортимент промислових холодильних установок, спеціально розроблених для вимогливих застосувань, таких як видування пляшок. Забезпечуючи постійну подачу охолодженої води, ці чиллери допомагають регулювати температуру форми, забезпечуючи постійне та високоякісне виробництво пляшок.
Типи охолоджувачів води для видувного формування: повітряне охолодження проти водяного охолодження
Існує два основних типи охолоджувачів, які використовуються з машинами для видування пляшок: чиллери з повітряним охолодженням і чиллери з водяним охолодженням. Чиллери з повітряним охолодженням використовують навколишнє повітря для розсіювання тепла, що полегшує їх установку та потребує менше інфраструктури, ніж їхні аналоги з водяним охолодженням. Вони часто є кращим вибором для невеликих операцій або там, де доступ до надійного джерела води обмежений. Чиллери з водяним охолодженням, з іншого боку, використовують окреме джерело води, часто градирню, щоб відвести тепло. Хоча вони пропонують вищу потужність охолодження та енергоефективність, вони потребують більш складного встановлення та поточного обслуговування.
Вибір між ан чиллер з повітряним охолодженням а чиллер із водяним охолодженням вимагає ретельного розгляду таких факторів, як доступний простір, температура навколишнього середовища, доступ до води та довгострокові експлуатаційні витрати. Кожен тип має власний набір переваг і недоліків, і ідеальний вибір значною мірою залежить від конкретних потреб і обставин операції видування пляшок. Такі фактори, як масштаб виробництва, навколишнє середовище та бюджетні міркування часто впливають на вибір між цими двома основними типами чиллерів.
Розуміння потужності холодильної камери та її розмірів для видування пляшок
Потужність охолоджувача, зазвичай вимірюється в тоннах або кінських силах (HP), визначає, скільки тепла охолоджувач може видалити за годину. Правильний вибір розміру холодильної машини має вирішальне значення для ефективного видування пляшок. Чиллер із заниженим розміром важко охолоджувати форми належним чином, що призводить до затримок виробництва та проблем із якістю. Холодильник великого розміру, хоча технічно здатний охолоджувати, споживатиме надлишок енергії, що зайво збільшуватиме експлуатаційні витрати.
Кілька факторів впливають на необхідний розмір охолоджувача для машини для видування пляшок. До них належать розмір і кількість форм, що охолоджуються, тип використовуваного пластику (PET, HDPE тощо), бажаний час циклу та температура навколишнього середовища виробництва. Точна оцінка цих факторів і розрахунок охолоджувального навантаження має важливе значення для вибору чиллера правильного розміру.
Вибір ідеального охолоджувача для вашої машини для видування пляшок
Крім основного вибору між повітряним і водяним охолодженням, кілька інших факторів відіграють вирішальну роль у виборі правильного охолоджувача для вашої машини для видування пляшок. Тип використовуваного пластику, бажаний вихід, розмір і кількість форм, а також доступний простір – усе це впливає на процес прийняття рішення. Деякі операції з видування пляшок можуть отримати переваги від спеціальних функцій, таких як можливості низькотемпературного охолодження або інтегровані системи керування процесом у їхній холодильній машині з повітряним охолодженням.
Наприклад, видування ПЕТ-пляшок часто вимагає точного контролю температури води для досягнення бажаних властивостей матеріалу. А низькотемпературний чиллер Для цього холодильного агрегату з повітряним охолодженням необхідне належне обслуговування. Крім того, деякі виробники пропонують інтегровані системи, які поєднують охолодження з іншими функціями, такими як нагрівання та контроль температури форми. Ці системи можуть упорядкувати операції та додатково оптимізувати процес видування пляшок.
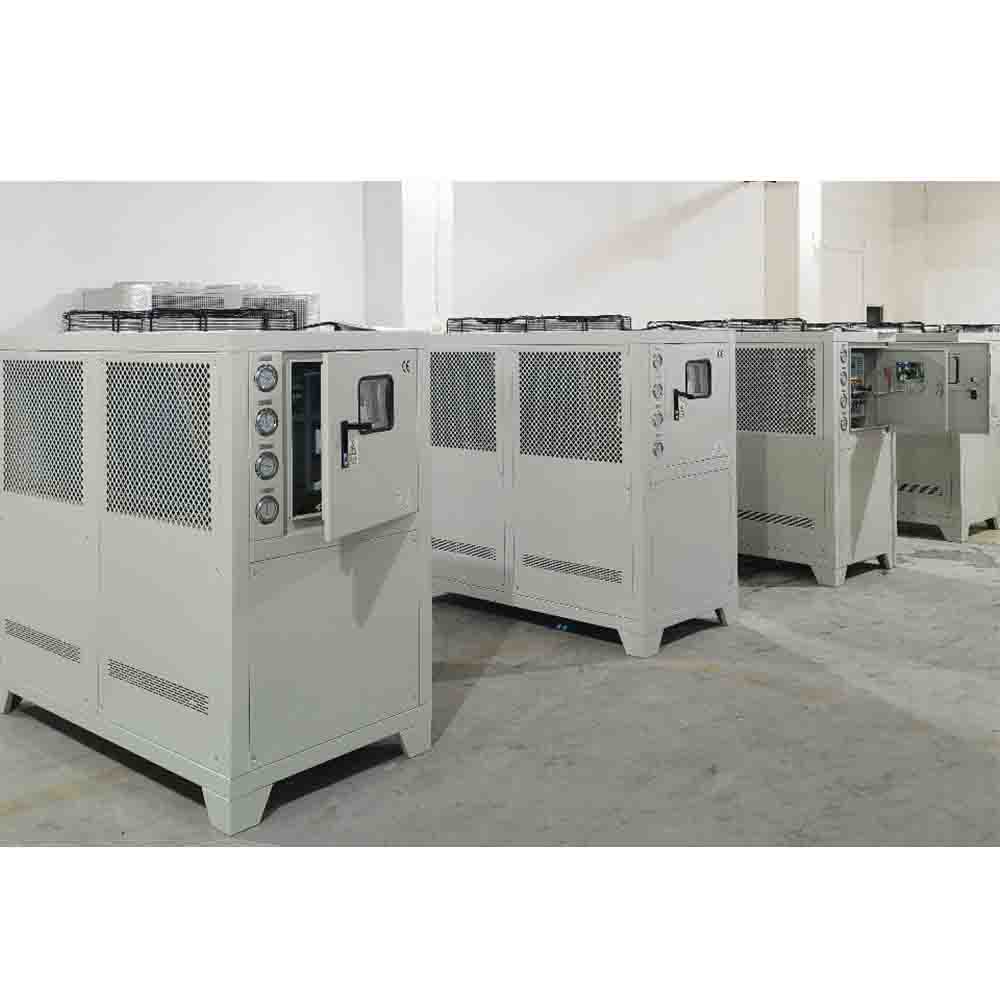
Процес видування пляшок: як чиллери сприяють ефективності
Процес видування пляшки складається з кількох етапів: від нагрівання преформи до охолодження форми. Охолоджувачі забезпечують підтримку правильної температури у формах, дозволяючи розплавленому пластику швидко охолонути та тверднути. Це скорочує тривалість циклу, збільшує продуктивність і покращує загальну ефективність машини для видування пляшок. Правильно охолоджені форми також сприяють якості готових пляшок, мінімізуючи дефекти та забезпечуючи постійну товщину стінок.
Сам процес видування передбачає надування нагрітої преформи всередині форми за допомогою стисненого повітря. Точно контрольовані ступені низького тиску є вирішальними для досягнення бажаної форми пляшки. Чиллер, як важлива складова система охолодження, відіграє безпосередню роль у контролі цих етапів і гарантує, що процес охолодження узгоджується з точними потребами кожного етапу формування пляшки.
Обслуговування системи охолодження для оптимальної роботи
Регулярне технічне обслуговування є ключовим фактором забезпечення довгострокової ефективності та надійності вашої холодильної системи. Такі прості завдання, як очищення котушок конденсатора, перевірка рівня холодоагенту та перевірка насосів та інших компонентів, можуть запобігти серйозним проблемам і дорогим простоям. Графік профілактичного обслуговування холодильної машини повинен включати регулярні перевірки, очищення та заміну компонентів за потреби.
Ефективна робота чилера значною мірою залежить від належного обслуговування. Це включає підтримку якості води для системи водяного охолодження, забезпечуючи належну заправку холодоагенту та утримуючи конденсатор від сміття. Регулярне технічне обслуговування не тільки подовжує термін служби чилера, але й забезпечує оптимальну ефективність охолодження, зменшуючи споживання енергії та покращуючи загальну ефективність системи.
Усунення поширених проблем холодильної камери в системах видувного формування
Незважаючи на регулярне технічне обслуговування, час від часу можуть виникати проблеми з чиллером. Розуміння поширених проблем та їх потенційних причин може допомогти вам швидко діагностувати та вирішити проблеми у вашій холодильній машині. Такі проблеми, як недостатнє охолодження, витоки, незвичайні шуми або надмірне споживання енергії, часто можна віднести до певних компонентів, таких як компресор, конденсатор або система холодоагенту.
Маючи базові знання про роботу холодильної машини та загальні кроки з усунення несправностей, можна мінімізувати час простою та запобігти дорогому ремонту. Наприклад, зниження потужності охолодження може вказувати на проблему з холодоагентом, тоді як незвичні шуми можуть вказувати на несправність компресора. Знання того, на що звертати увагу, може допомогти вам визначити проблему та визначити, чи це просте вирішення, чи вимагає професійного обслуговування.
Супутні продукти та інтегровані системи для покращеного охолодження
На додаток до автономних холодильних установок, цілий ряд супутніх продуктів і інтегрованих систем може ще більше підвищити ефективність охолодження в системах видування пляшок. Це може включати градирні для охолоджувачів з водяним охолодженням, блоків контролю температури для точного регулювання температури форми та насосних систем для оптимальної циркуляції води. Інтеграція цих компонентів у єдину систему може оптимізувати весь процес видування пляшок.
Для великих операцій з видування пляшок централізована система охолодження може бути більш ефективною, ніж окремі холодильні машини для кожної машини. Ці системи часто включають кілька охолоджувачів, насосів і розподільну мережу для подачі охолодженої води в різні точки виробничого процесу. Такий підхід дозволяє краще контролювати параметри охолодження, оптимізує споживання енергії та спрощує технічне обслуговування.
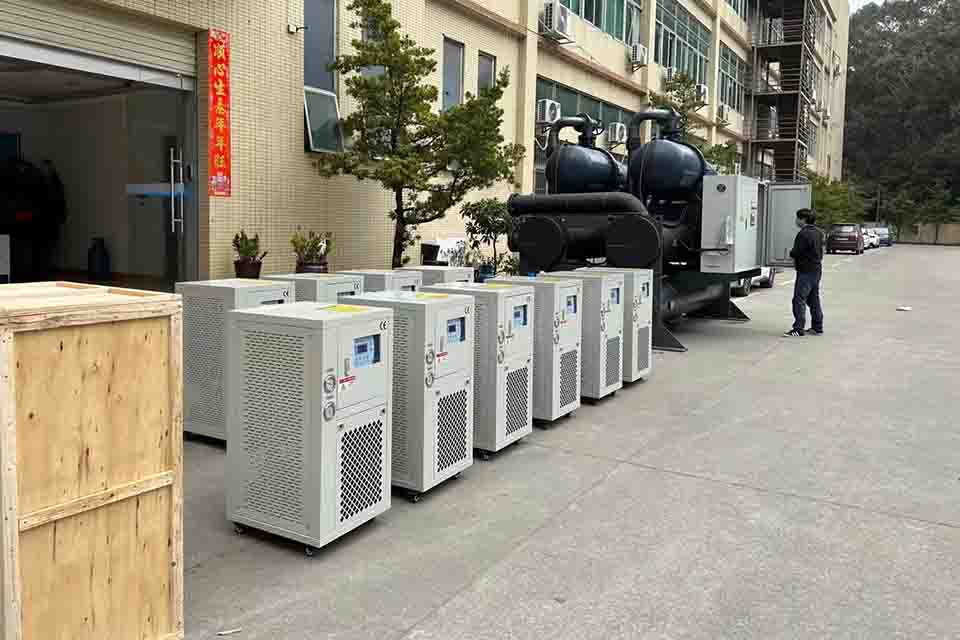
Вивчення передових технологій охолодження для видування пляшок
Сфера технологій охолоджувачів постійно розвивається з новими інноваціями, спрямованими на підвищення ефективності, зменшення впливу на навколишнє середовище та підвищення продуктивності. Вдосконалені чиллери можуть включати компресори зі змінною швидкістю, складні системи керування та екологічно чисті холодоагенти. Ці технології пропонують значні переваги з точки зору економії енергії, точного контролю температури та зниження експлуатаційних витрат.
Наприклад, компресори зі змінною швидкістю регулюють свою потужність залежно від потреби в охолодженні, оптимізуючи споживання енергії та зменшуючи знос компресора. Удосконалені системи керування забезпечують моніторинг у режимі реального часу та точні налаштування для підтримки оптимальних параметрів охолодження в холодильній машині з водяним охолодженням. Ці технології розширюють межі продуктивності чиллерів і пропонують значні переваги для операцій з видування пляшок.
Зв’яжіться з нами, щоб отримати експертну консультацію та індивідуальні рішення для охолодження
Бажаєте оптимізувати процес видування пляшок за допомогою високопродуктивного холодильного пристрою? Зв'яжіться з нами сьогодні! Ми пропонуємо широкий вибір холодильних установок, адаптованих до конкретних потреб машин для видування пляшок. Наша команда експертів може допомогти вам вибрати правильного виробника чиллера для ваших потреб у переробці пластику. розмір чиллера, тип і конфігурацію для вашої програми, незалежно від того, чи є ви малим підприємством, яке використовує одну машину для видування пляшок, чи великим виробником із кількома виробничими лініями.
поширені запитання:
Яка різниця між чиллером з водяним охолодженням і чиллером з повітряним охолодженням для видування пляшок?
Чиллери з водяним охолодженням використовують окремий водяний контур і градирню для розсіювання тепла, забезпечуючи вищу ефективність, але вимагаючи більш складної установки. Чиллери з повітряним охолодженням використовують навколишнє повітря для охолодження, що спрощує установку, але потенційно має нижчу ефективність у жаркому кліматі.
Як визначити правильну потужність охолоджувача для моєї машини для видування пляшок?
Розмір холодильника залежить від таких факторів, як кількість і розмір форм, тип пластику, бажаний час циклу та температура навколишнього середовища. Щоб отримати точні розміри, радимо проконсультуватися з фахівцем із чиллерів.
Які ключові етапи технічного обслуговування холодильної машини, що використовується з машиною для видування пляшок?
Основні завдання з технічного обслуговування включають регулярне очищення котушок конденсатора, перевірку рівнів холодоагенту, перевірку насосів та інших компонентів, а також забезпечення належної очистки води для систем водяного охолодження.
Які поширені проблеми з охолоджувачами, що використовуються для видування пляшок, і як я можу їх усунути?
Поширені проблеми включають недостатнє охолодження, витоки, незвичайні шуми та високе споживання енергії. Усунення несправностей часто передбачає перевірку рівнів холодоагенту в холодильній машині з повітряним охолодженням, перевірку компресора та конденсатора та перевірку належного потоку води.
Які переваги використання гліколевої холодильної машини з машиною для видування пляшок?
Гліколеві охолоджувачі дозволяють знизити температуру охолодження, що може бути корисним для певних типів пластику або спеціалізованих програм для видування пляшок.
Як я можу покращити енергоефективність моєї системи охолодження під час операції видування пляшок?
Підвищення енергоефективності включає регулярне технічне обслуговування, правильний вибір розміру холодильної машини, використання енергоефективних компонентів і впровадження систем керування, які відповідають потужності охолодження відповідно до вимог водяного холодильного агрегату для видування пляшок.
Основні висновки
- Чиллери мають вирішальне значення для підтримки ефективних і високоякісних операцій видування пляшок.
- Вибір правильного типу та розміру холодильної машини є важливим для оптимальної продуктивності.
- Регулярне технічне обслуговування чиллера з водяним охолодженням запобігає дорогим поломкам і продовжує термін служби обладнання.
- Розуміння поширених проблем охолоджувача дозволяє швидко усунути несправності охолоджувача води для видування пляшок.
- Удосконалені технології чиллерів можуть додатково підвищити ефективність і знизити експлуатаційні витрати.