-
டாலிங்ஷான் தொழில்துறை குவாங்டாங்
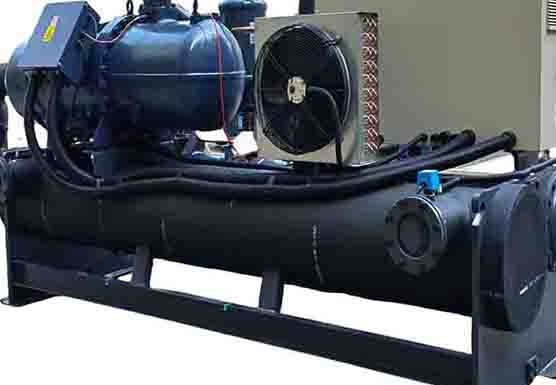
கிளைகோல் சில்லர் vs. வாட்டர் சில்லர் - ஏன் கிளைகோலைப் பயன்படுத்த வேண்டும்?
கிளைகால் சில்லர் vs வாட்டர் சில்லர்: முக்கிய வேறுபாடுகள் மற்றும் பயன்பாடுகளைப் புரிந்துகொள்வது
இந்தக் கட்டுரை தொழில்துறை குளிர்விப்பான் உலகில் மூழ்கி, குறிப்பாக கிளைகோல் குளிர்விப்பான்கள் மற்றும் நீர் குளிர்விப்பான்களை ஒப்பிடுகிறது. அவற்றின் வேறுபாடுகள், நன்மைகள் மற்றும் சிறந்த பயன்பாடுகளை நாங்கள் ஆராய்வோம். நீங்கள் பிளாஸ்டிக் துறையில் இருந்தாலும், உணவு பதப்படுத்துதலில் இருந்தாலும் அல்லது தரவு மையத்தை நிர்வகிப்பவராக இருந்தாலும் சரி, திறமையான மற்றும் செலவு குறைந்த செயல்பாட்டிற்கு இந்த அமைப்புகளைப் புரிந்துகொள்வது மிக முக்கியம். ஒரு முன்னணி தொழில்துறை நீர் குளிர்விப்பான் உற்பத்தி ஆலையாக, இரண்டின் நுணுக்கங்களையும் நாங்கள் நன்கு அறிந்திருக்கிறோம். நீர் குளிர்விப்பான்கள் மற்றும் கிளைகோல் குளிர்விப்பான்கள். மிகவும் பொருத்தமானதைத் தீர்மானிக்க உங்களுக்குத் தேவையான அத்தியாவசியத் தகவல்களை வழங்குவதற்காக இந்தக் கட்டுரை வடிவமைக்கப்பட்டுள்ளது. குளிர்விப்பான் வகை உங்கள் குறிப்பிட்ட தேவைகளுக்கு. சிக்கலான கருத்துக்களை தெளிவுபடுத்துவதற்கு நேரடி நுண்ணறிவுகளையும் நடைமுறை உதாரணங்களையும் நாங்கள் சேர்ப்போம், இது அவர்களின் குளிரூட்டும் அமைப்புகளை மேம்படுத்த விரும்பும் எவருக்கும் ஒரு மதிப்புமிக்க வாசிப்பாக அமைகிறது.
பொருளடக்கம்
கிளைகால் குளிர்விப்பான் என்றால் என்ன, அது எப்படி வேலை செய்கிறது?
அ கிளைகோல் குளிர்விப்பான் ஒரு வகை தொழில்துறை குளிர்விப்பான் அது ஒரு பயன்படுத்துகிறது கிளைக்கால் மற்றும் தண்ணீரின் கலவை என குளிர்விக்கும் ஊடகம்தி கிளைகோல், பொதுவாக எத்திலீன் கிளைக்கால் அல்லது புரோப்பிலீன் கிளைக்கால், அதன் உறைநிலையைக் குறைக்க தண்ணீரில் சேர்க்கப்படுகிறது. இது அனுமதிக்கிறது குளிர்விப்பான் உறைநிலைக்குக் கீழே உள்ள வெப்பநிலையில் செயல்பட தூய நீர் குளிர்விப்பான் உறைந்து, அமைப்பை சேதப்படுத்தும் ஆபத்து இல்லாமல். தொழில்துறை நீர் குளிர்விப்பான் உற்பத்தி ஆலைகள் பெரும்பாலும் பரிந்துரைக்கின்றன கிளைகோல் குளிர்விப்பான்கள் விண்ணப்பங்களுக்கு விரைவான குளிர்விப்பு தேவைப்படும் மற்றும் இயக்க நிலைமைகள் உறைபனிக்குக் கீழே வெப்பநிலையை அடையக்கூடிய இடங்களில்.
கிளைகோல் குளிர்விப்பான்கள் சுற்றுவதன் மூலம் வேலை செய்யுங்கள் கிளைகோல் ஒரு குளிர்பதன அலகு வழியாக கரைசல், அதை குளிர்விக்கிறது. குளிர்ந்த கிளைகோல் பின்னர் கரைசல் ஒரு வெப்பப் பரிமாற்றி வழியாக செலுத்தப்படுகிறது, அங்கு அது செயல்முறை அல்லது குளிர்விக்கப்படும் உபகரணங்களிலிருந்து வெப்பத்தை உறிஞ்சுகிறது. கிளைகோல் பின்னர் திரும்பப் பெறப்படுகிறது குளிர்விப்பான் மீண்டும் குளிர்விக்கப்பட வேண்டும். கிளைகோலின் பயன்பாடு என்பதை உறுதி செய்கிறது குளிர்விப்பான் அமைப்பு மிகக் குறைந்த வெப்பநிலையிலும் திறமையாகச் செயல்பட முடியும், இது உணவு மற்றும் பானங்கள், மருந்துகள் போன்ற தொழில்களுக்கும், குளிர்ந்த சூழல்களில் துல்லியமான வெப்பநிலைக் கட்டுப்பாடு தேவைப்படும் எந்தவொரு பயன்பாட்டிற்கும் ஏற்றதாக அமைகிறது. தொழில்துறை நீர் குளிர்விப்பான் உற்பத்தியாளர்களாக, நாம் அடிக்கடி பார்க்கிறோம் காய்ச்சி வடிகட்டிய பயன்பாடு அல்லது அயனியாக்கம் நீக்கப்பட்ட நீர் உடன் கலக்க பரிந்துரைக்கப்படுகிறது கிளைகோல் அமைப்பினுள் கனிம படிவுகள் மற்றும் அரிப்பைத் தவிர்க்க.
வாட்டர் சில்லர் என்றால் என்ன, அது எவ்வாறு இயங்குகிறது?
அ நீர் குளிர்விப்பான் மற்றொரு வகை தொழில்துறை குளிர்விப்பான் அது பயன்படுத்துகிறது தண்ணீர் என குளிர்விக்கும் ஊடகம்இவை குளிர்விப்பான்கள் குளிர்விக்க வடிவமைக்கப்பட்டுள்ளது. தண்ணீர் ஒரு குறிப்பிட்ட வெப்பநிலைக்கு வெப்பத்தை மாற்றி, பின்னர் தொழில்துறை செயல்முறைகள், இயந்திரங்கள் அல்லது ஏர் கண்டிஷனிங் அமைப்புகளிலிருந்து வெப்பத்தை உறிஞ்சுவதற்கு வெப்பப் பரிமாற்றி வழியாக அதைச் சுழற்றுகிறது. நீர் குளிர்விப்பான்கள் தேவையான வெப்பநிலை உறைநிலைக்கு மேல் இருக்கும்போது மிகவும் திறமையானவை தண்ணீர்.
நீர் குளிர்விப்பான்கள் சுழற்சி மூலம் இயக்கவும் குளிர்ந்த நீர் ஒரு வழியாக குளிர்விப்பதற்கான குளிர்பதன அலகு. குளிர்ந்த தண்ணீர் பின்னர் ஒரு வெப்பப் பரிமாற்றி வழியாக உந்தப்படுகிறது, அங்கு அது செயல்முறை அல்லது குளிர்விக்கப்படும் உபகரணங்களிலிருந்து வெப்பத்தை உறிஞ்சுகிறது. தண்ணீர் பின்னர் திரும்பப் பெறப்படுகிறது குளிர்விப்பான் மீண்டும் குளிர்விக்க வேண்டும். நீர் குளிர்விப்பான்கள் அதிக அளவு இருப்பதால் பல பயன்பாடுகளில் விரும்பப்படுகின்றன வெப்ப பரிமாற்றம் பண்புகள் தண்ணீர்இருப்பினும், வெப்பநிலை உறைநிலைக்குக் கீழே குறையும் இடங்களில் அவை பயன்பாடுகளுக்கு ஏற்றவை அல்ல. தண்ணீர், இது ஏற்படுத்தக்கூடும் என்பதால் தண்ணீர் உறைய வைத்து சேதப்படுத்தக்கூடிய வகையில் குளிர்விப்பான் கூறுகள். பயன்படுத்தி தண்ணீர் என குளிரூட்டி பயன்படுத்துவதை விட பெரும்பாலும் எளிமையானது மற்றும் செலவு குறைந்ததாகும். கிளைகோல், ஆனால் உறைநிலைப் புள்ளியால் விதிக்கப்பட்ட வரம்புகள் தண்ணீர் கவனமாக பரிசீலிக்கப்பட வேண்டும்.
கிளைகோல் குளிர்விப்பான்கள் மற்றும் நீர் குளிர்விப்பான்கள் இடையே உள்ள முக்கிய வேறுபாடுகள் என்ன?
முதன்மை கிளைகோலுக்கு இடையிலான வேறுபாடு குளிர்விப்பான்கள் மற்றும் நீர் குளிர்விப்பான்கள் உள்ளது குளிர்விக்கும் ஊடகம் பயன்படுத்தப்பட்டது. கிளைகோல் குளிர்விப்பான்கள் பயன்படுத்து எத்திலீன் கிளைக்கால் கலவை மற்றும் தண்ணீர், அதே நேரத்தில் நீர் குளிர்விப்பான்கள் பயன்படுத்த மட்டும் தண்ணீர்இந்த அடிப்படை வேறுபாடு அவற்றின் செயல்பாடு, செயல்திறன் மற்றும் பயன்பாடுகளில் பல வேறுபாடுகளுக்கு வழிவகுக்கிறது.
அம்சம் | கிளைகால் குளிர்விப்பான் | நீர் குளிர்விப்பான் |
கூலண்ட் | கலவை கிளைக்கால் மற்றும் தண்ணீர் | தூய நீர் அல்லது நகர நீர் |
உறைபனிப் புள்ளி | சேர்ப்பதன் மூலம் குறைக்கப்பட்டது கிளைகோல் | 0°C (32°F) |
இயக்க வெப்பநிலை | 0°C (32°F) க்கும் குறைவான வெப்பநிலையில் இயங்க முடியும். | பொதுவாக 0°C (32°F) க்கு மேல் இயங்கும் |
வெப்ப பரிமாற்றம் | சற்று குறைவாக வெப்ப பரிமாற்றம் ஒப்பிடும்போது செயல்திறன் தண்ணீர் | உயர்ந்தது வெப்ப பரிமாற்றம் செயல்திறன் |
பயன்பாடுகள் | குறைந்த வெப்பநிலை பயன்பாடுகள், வெளிப்புற நிறுவல்களுக்கு ஏற்றது, உறைதல் பாதுகாப்பு | மிதமான வெப்பநிலை பயன்பாடுகள், உட்புற அமைப்புகளுக்கு ஏற்றது |
செலவு | அதிக ஆரம்ப செலவு காரணமாக கிளைகோல், பராமரிப்பு செலவுகள் அதிகரிக்க வாய்ப்புள்ளது | குறைந்த ஆரம்ப செலவு, சாத்தியமான குறைந்த பராமரிப்பு செலவுகள் |
சேர்த்தல் கிளைகோல் க்கு குளிர்விப்பான் குளிரூட்டி உறைநிலையைக் குறைக்கிறது, இதனால் கிளைகோல் குளிர்விப்பான்கள் வெப்பநிலை உறைநிலைக்குக் கீழே குறையும் சூழல்களுக்கு ஏற்றது. தண்ணீர்தி நீர் குளிர்விப்பான் அடிக்கடி திரவ மாற்றங்கள் தேவைப்படுவதால், பராமரிப்பு அதிகமாக இருக்கும். நீர் குளிர்விப்பான்கள்மறுபுறம், பொதுவாக மிகவும் திறமையானவை வெப்ப பரிமாற்றம் உறைநிலைக்கு மேலே இயங்கும்போது, இதன் காரணமாக தண்ணீர் விட வெப்பத்தை சிறப்பாக உறிஞ்சும் திறன் கொண்டது கிளைகோல்இருப்பினும், பயன்படுத்தி தண்ணீர் உறைபனிக்குக் கீழே உள்ள சூழ்நிலைகளில் ஏற்படும் அபாயங்கள் உறைதல், இது குறிப்பிடத்தக்க சேதத்தை ஏற்படுத்தக்கூடும் குளிர்விப்பான் அமைப்பு. கிளைகோல் குளிர்விப்பான்கள் மேலும், குளிர்விப்பான் இருப்பிடம் அவை உள்ளார்ந்த தன்மையை வழங்குவதால், வெளியில் உள்ளது உறைதல் தடுப்பி பண்புகள்.
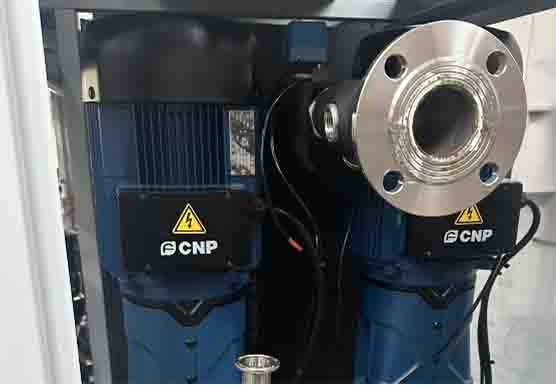
தொழில்துறை குளிர்விப்பான்களில் கிளைகோலை ஏன் பயன்படுத்த வேண்டும்?
முதன்மையான காரணம் கிளைகோலைப் பயன்படுத்துங்கள் உள்ளே தொழில்துறை குளிர்விப்பான்கள் தடுக்க வேண்டும் குளிர்வித்தல் திரவம் உறைதல் குறைந்த வெப்பநிலையில். கிளைகோல் ஒரு உறைதல் தடுப்பி, இன் உறைநிலைப் புள்ளியைக் குறைக்கிறது தண்ணீர் அமைப்பில். இது பயன்பாடுகளில் மிக முக்கியமானது, அங்கு குளிர்விப்பான் குளிர்ந்த சூழல்களில் அல்லது குளிர்விக்கப்படும் செயல்முறைக்கு உறைநிலைக்குக் கீழே வெப்பநிலை தேவைப்படும் இடங்களில் செயல்படுகிறது. தண்ணீர்.
கிளைகோல் அரிப்பு பாதுகாப்பு போன்ற பிற நன்மைகளையும் வழங்குகிறது. பல தொழில்துறை குளிர்விப்பான்கள் பயன்படுத்து தடுக்கப்பட்ட கிளைக்கால், இது அமைப்பினுள் அரிப்பு மற்றும் அளவிடுதலைத் தடுக்கும் சேர்க்கைகளைக் கொண்டுள்ளது. இது ஆயுளை நீட்டிக்க உதவுகிறது குளிர்விப்பான் மேலும் அதன் செயல்திறனைப் பராமரிக்கவும். கூடுதலாக, கிளைகோல் பாக்டீரியா மற்றும் பாசிகளின் வளர்ச்சியைக் குறைக்க உதவும் குளிர்வித்தல் அமைப்பு. தி கிளைகோலின் நன்மைகள் உணவு பதப்படுத்துதல் போன்ற தொழில்களில் இது குறிப்பாகத் தெளிவாகத் தெரிகிறது, அங்கு குறைந்த வெப்பநிலையை பராமரிப்பது தயாரிப்பு பாதுகாப்பு மற்றும் தரத்திற்கு அவசியம். கிளைகோல் அடிப்படையிலான குளிர்விப்பான்கள் மிகவும் பொருத்தமானவை. இந்த பயன்பாடுகளுக்கு நீர் குளிர்விப்பான்கள், இவை அதிக பாதிப்புக்குள்ளாகும் உறைதல் சிக்கல்கள். இங்கே சில உணவு மற்றும் பானத் தொழிலுக்கான தொழில்துறை குளிர்விப்பான்கள்.
குளிர்விப்பான்களில் என்ன வகையான கிளைக்கால் பயன்படுத்தப்படுகிறது?
முதன்மையாக இரண்டு உள்ளன கிளைகோல் வகைகள் பயன்படுத்தப்பட்டது குளிர்விப்பான்கள்: எத்திலீன் கிளைக்கால் மற்றும் புரோப்பிலீன் கிளைக்கால். எத்திலீன் கிளைக்கால் அதன் உயர்ந்த தன்மை காரணமாக இது மிகவும் பொதுவானது. வெப்ப பரிமாற்றம் பண்புகள் மற்றும் குறைந்த விலை. இருப்பினும், இது உட்கொண்டால் நச்சுத்தன்மை வாய்ந்தது, எனவே கவனமாக கையாளுதல் தேவைப்படுகிறது.
புரோப்பிலீன் கிளைகோல்மறுபுறம், இது நச்சுத்தன்மையற்றது மற்றும் உணவு மற்றும் பானத் தொழில் போன்ற தற்செயலான உட்கொள்ளல் ஆபத்து உள்ள பயன்பாடுகளில் பெரும்பாலும் பயன்படுத்தப்படுகிறது. புரோப்பிலீன் கிளைக்கால் பாதுகாப்பானது, இது சற்று குறைவாக உள்ளது வெப்ப பரிமாற்றம் ஒப்பிடும்போது செயல்திறன் எத்திலீன் கிளைக்கால். இடையேயான தேர்வு எத்திலீன் கிளைக்கால் அல்லது புரோப்பிலீன் கிளைக்கால் குறிப்பிட்ட பயன்பாடு மற்றும் பாதுகாப்பு பரிசீலனைகளைப் பொறுத்தது. இரண்டும் கிளைகோல் வகைகள் உறைநிலையைக் குறைப்பதில் பயனுள்ளதாக இருக்கும் தண்ணீர், ஆனால் இடையேயான தேர்வு புரோப்பிலீன் அல்லது எத்திலீன் கிளைக்கால் பெரும்பாலும் நச்சுத்தன்மை தொடர்பான கவலைகளுக்கு வருகிறது.
உறைபனிப் புள்ளி குளிர்விப்பான் செயல்திறனை எவ்வாறு பாதிக்கிறது?
உறைபனிப் புள்ளி குளிர்வித்தல் திரவம் ஒரு முக்கிய காரணியாகும் குளிர்விப்பான் செயல்திறன், குறிப்பாக குறைந்த வெப்பநிலை பயன்பாடுகளில். குளிர்வித்தல் திரவம் உறைகிறது, இது குறிப்பிடத்தக்க சேதத்தை ஏற்படுத்தும் குளிர்விப்பான் ஆவியாக்கி மற்றும் குழாய் போன்ற கூறுகள். இது விலையுயர்ந்த பழுதுபார்ப்பு மற்றும் செயலிழப்பு நேரத்திற்கு வழிவகுக்கும்.
ஒரு பயன்படுத்தி கிளைக்கால் கலவை அனுமதிக்கிறது குளிர்விப்பான் உறைநிலைக்குக் கீழே உள்ள வெப்பநிலையில் செயல்பட தண்ணீர் ஆபத்து இல்லாமல் உறைதல். இது குளிர்ந்த சூழல்களில் கூட தொடர்ச்சியான மற்றும் நம்பகமான செயல்பாட்டை உறுதி செய்கிறது. கிளைகோல் கரைசலின் உறைநிலையை செறிவு தீர்மானிக்கிறது. அதிக கிளைகோல் செறிவுகள் குறைந்த உறைநிலை புள்ளிகளுக்கு காரணமாகின்றன. இருப்பினும், அதிகரிப்பதைக் கவனத்தில் கொள்ள வேண்டியது அவசியம் கிளைகோல் செறிவு மேலும் குறைக்கிறது வெப்ப பரிமாற்றம் திரவத்தின் செயல்திறன். கிளைகோல் என்பதால் விடக் குறைவான குறிப்பிட்ட வெப்பத்தைக் கொண்டுள்ளது தண்ணீர், இது வெப்பத்தை அவ்வளவு திறம்பட உறிஞ்சாது. எனவே, உகந்ததைக் கண்டறிதல் கிளைகோல் சமநிலைப்படுத்துவதற்கு செறிவு மிக முக்கியமானது. உறைதல் பாதுகாப்பு மற்றும் குளிர்வித்தல் செயல்திறன். உதாரணமாக, தூய எத்திலீன் கிளைக்கால் சுமார் -12.9°C (8.8°F) வெப்பநிலையில் உறைந்து போகும், ஆனால் a கிளைக்கால் மற்றும் தண்ணீரின் கலவை மிகக் குறைந்த வெப்பநிலையிலும் திரவமாக இருக்க முடியும்.
கிளைகால் குளிரூட்டியைப் பயன்படுத்துவதன் நன்மைகள் என்ன?
கிளைகோல் குளிர்விப்பான்கள் பல நன்மைகளை வழங்குகின்றன நீர் குளிர்விப்பான்கள், குறிப்பாக குறைந்த வெப்பநிலை பயன்பாடுகளில்:
- உறைபனி பாதுகாப்பு: முதன்மை நன்மை என்னவென்றால், உறைநிலைக்குக் கீழே செயல்படும் திறன் ஆகும். தண்ணீர் ஆபத்து இல்லாமல் குளிர்வித்தல் திரவம் உறைதல். இது பயன்பாடுகளுக்கு அவசியமானது, அங்கு குளிர்விப்பான் குளிர்ந்த வெப்பநிலைக்கு ஆளாக்கப்படுகிறது அல்லது குளிர்விக்கப்படும் செயல்முறைக்கு உறைபனி வெப்பநிலை குறைவாக தேவைப்படுகிறது.
- அரிப்பு பாதுகாப்பு: தடுக்கப்பட்ட கிளைக்கால் கரைசல்களில் அரிப்பு மற்றும் அளவிடுதலைத் தடுக்கும் சேர்க்கைகள் உள்ளன. குளிர்விப்பான் இது உபகரணங்களின் ஆயுளை நீட்டிக்கவும் அதன் செயல்திறனைப் பராமரிக்கவும் உதவுகிறது.
- குறைக்கப்பட்ட பாக்டீரியா வளர்ச்சி: கிளைகோல் பாக்டீரியா மற்றும் பாசிகளின் வளர்ச்சியைத் தடுக்க உதவும் குளிர்வித்தல் சுகாதாரத்தை மேம்படுத்தவும் பராமரிப்பு தேவைகளைக் குறைக்கவும் கூடிய அமைப்பு.
- பல்துறை: கிளைகோல் குளிர்விப்பான்கள் வெளிப்புற நிறுவல்கள், உணவு மற்றும் பான பதப்படுத்துதல், மருந்துகள் மற்றும் இரசாயன பதப்படுத்துதல் உள்ளிட்ட பல்வேறு பயன்பாடுகளில் இதைப் பயன்படுத்தலாம்.
இந்த நன்மைகள் கிளைகோல் குளிர்விப்பான்கள் பல தொழில்களுக்கு ஒரு பிரபலமான தேர்வு. உறைதல் தடுப்பு பண்புகள் இன் கிளைகோல் குளிர் காலநிலை உள்ள பகுதிகளில் குறிப்பாக முக்கியமானது, அங்கு நீர் குளிர்விப்பான்கள் நடைமுறைக்கு மாறானதாக இருக்கும்.
கிளைக்கால் குளிரூட்டியை விட வாட்டர் குளிரூட்டியை எப்போது பயன்படுத்த வேண்டும்?
போது கிளைகோல் குளிர்விப்பான்கள் பல நன்மைகளை வழங்குகின்றன, சில சூழ்நிலைகள் உள்ளன, அதாவது நீர் குளிர்விப்பான்கள் சிறந்த தேர்வாக இருக்கும்:
- மிதமான வெப்பநிலை பயன்பாடுகள்: தேவைப்பட்டால் குளிர்வித்தல் வெப்பநிலை தொடர்ந்து உறைநிலைக்கு மேலே இருக்கும் தண்ணீர், அ நீர் குளிர்விப்பான் பெரும்பாலும் மிகவும் திறமையானது மற்றும் செலவு குறைந்ததாகும். தண்ணீர் விட அதிக குறிப்பிட்ட வெப்ப திறன் கொண்டது கிளைகோல்அதாவது, கொடுக்கப்பட்ட வெப்பநிலை மாற்றத்திற்கு அதிக வெப்பத்தை உறிஞ்சும்.
- உட்புற பயன்பாடுகள்: வெப்பநிலை கட்டுப்படுத்தப்பட்டு, எந்த ஆபத்தும் இல்லாத உட்புற சூழல்களில் உறைதல், நீர் குளிர்விப்பான்கள் பொதுவாக அவற்றின் உயர்ந்த தன்மை காரணமாக விரும்பப்படுகின்றன வெப்ப பரிமாற்றம் திறன்.
- செலவு பரிசீலனைகள்: நீர் குளிர்விப்பான்கள் பொதுவாக குறைந்த ஆரம்ப செலவைக் கொண்டிருக்கும் கிளைகோல் குளிர்விப்பான்கள்கூடுதலாக, தண்ணீர் இதை விட விலை குறைவு கிளைகோல், எனவே ஒரு இயக்க செலவுகள் நீர் குளிர்விப்பான் சில சந்தர்ப்பங்களில் குறைவாக இருக்கலாம்.
- சுற்றுச்சூழல் கவலைகள்: தண்ணீர் சுற்றுச்சூழலுக்கு உகந்தது, சில கிளைகோல் தீர்வுகள், குறிப்பாக எத்திலீன் கிளைக்கால், நச்சுத்தன்மையுடையதாக இருக்கலாம்.
உதாரணமாக, இல் HVAC அமைப்புகள் எங்கே குளிர்ந்த நீர் காற்றுச்சீரமைப்பிக்குப் பயன்படுத்தப்படுகிறது மற்றும் வெப்பநிலை உறைநிலைக்கு மேல் இருக்கும், a நீர் குளிர்விப்பான் பொதுவாக சிறந்த தேர்வாகும்.
சரியான கிளைகோல் மற்றும் நீர் விகிதத்தை எவ்வாறு தீர்மானிப்பது?
சரியானதைத் தீர்மானித்தல் கிளைகோலின் விகிதம் செய்ய தண்ணீர் உகந்ததற்கு முக்கியமானது குளிர்விப்பான் செயல்திறன். சிறந்த கிளைகோல் செறிவு எதிர்பார்க்கப்படும் குறைந்தபட்ச இயக்க வெப்பநிலை மற்றும் விரும்பிய அளவைப் பொறுத்தது உறைதல் பாதுகாப்பு.
- மிகக் குறைந்த வெப்பநிலையை மதிப்பிடுங்கள்: மிகக் குறைந்த வெப்பநிலையை தீர்மானிக்கவும் குளிர்விப்பான் சூழல் அல்லது குளிர்விக்கப்படும் செயல்முறை காரணமாக, வெளிப்படும்.
- கிளைகோல் செறிவு விளக்கப்படங்களைப் பாருங்கள்: உற்பத்தியாளர்கள் கிளைகோல் பல்வேறு வகையான உறைநிலைகளைக் காட்டும் விளக்கப்படங்களை வழங்கவும். கிளைகோல் செறிவுகள்.
- பாதுகாப்பு விளிம்பில் காரணி: பாதுகாப்பு விளிம்பைச் சேர்க்க பரிந்துரைக்கப்படுகிறது கிளைகோல் எதிர்பாராத வெப்பநிலை வீழ்ச்சிகள் அல்லது மாறுபாடுகளைக் கணக்கிடுவதற்கான செறிவு கிளைகோல் கலவை.
- வெப்ப பரிமாற்ற செயல்திறனைக் கவனியுங்கள்: உயர்ந்ததை நினைவில் கொள்ளுங்கள் கிளைகோல் செறிவுகள் குறைக்கின்றன வெப்ப பரிமாற்றம் செயல்திறன் குளிர்வித்தல் திரவம்.
உதாரணமாக, எதிர்பார்க்கப்படும் குறைந்தபட்ச வெப்பநிலை -10°C (14°F) என்றால், a கிளைகோல் சுமார் 30-40% செறிவு பொருத்தமானதாக இருக்கலாம். இருப்பினும், வெப்பநிலை -20°C (-4°F) ஆகக் குறையக்கூடும் என்றால், 40-50% இன் அதிக செறிவு தேவைப்படலாம். ஒரு நிபுணருடன் கலந்தாலோசிப்பது முக்கியம். குளிர்விப்பான் நிபுணர் அல்லது கிளைகோல் உகந்ததை தீர்மானிக்க உற்பத்தியாளர் கிளைகோல் உங்கள் குறிப்பிட்ட பயன்பாட்டிற்கான செறிவு. சரியானதைத் தேர்ந்தெடுப்பது கிளைகாலின் சதவீதம் இரண்டையும் தடுக்க அவசியம் உறைதல் மற்றும் தேவையற்ற குறைப்புக்கள் குளிர்வித்தல் திறன்.
கிளைக்கால் மற்றும் நீர் குளிரூட்டிகளுக்கான பராமரிப்புத் தேவைகள் என்ன?
இரண்டும் கிளைகோல் மற்றும் நீர் குளிர்விப்பான்கள் உகந்த செயல்திறன் மற்றும் நீண்ட ஆயுளை உறுதி செய்ய வழக்கமான பராமரிப்பு தேவைப்படுகிறது. இருப்பினும், அவற்றின் பராமரிப்பு தேவைகளில் சில வேறுபாடுகள் உள்ளன:
- திரவ சோதனை மற்றும் மாற்றீடு: கிளைகோல் தீர்வுகளை உறுதி செய்ய அவ்வப்போது சோதிக்கப்பட வேண்டும் கிளைகோல் செறிவு சரியாக உள்ளது மற்றும் திரவம் அசுத்தங்கள் இல்லாமல் உள்ளது. கிளைகோல் காலப்போக்கில் சிதைந்துவிடும், எனவே ஒவ்வொரு சில வருடங்களுக்கும் அதை மாற்ற வேண்டியிருக்கும். நீர் குளிர்விப்பான்கள் வழக்கமான தேவையும் உள்ளது தண்ணீர் சோதனை மற்றும் மாற்றீடு, ஆனால் பாக்டீரியா வளர்ச்சி மற்றும் கனிமக் குவிப்புக்கான சாத்தியக்கூறு காரணமாக அதிர்வெண் அதிகமாக இருக்கலாம்.
- அரிப்பு ஆய்வு: இரண்டு வகையான குளிர்விப்பான்கள் அரிப்புக்காக தொடர்ந்து பரிசோதிக்கப்பட வேண்டும். இருப்பினும், கிளைகோல் குளிர்விப்பான்கள் உடன் தடுக்கப்பட்ட கிளைக்கால் பொதுவாக அரிப்புக்கு குறைவாகவே பாதிக்கப்படுகின்றன நீர் குளிர்விப்பான்கள்.
- உறைபனி பாதுகாப்பு: க்கு கிளைகோல் குளிர்விப்பான்கள், சரிபார்க்க வேண்டியது அவசியம் கிளைகோல் குளிர் காலம் தொடங்குவதற்கு முன் போதுமான அளவு செறிவு உறுதி செய்யப்பட வேண்டும். உறைய வைக்கவும் பாதுகாப்பு.
- கணினி சுத்தம்: இரண்டும் கிளைகோல் மற்றும் நீர் குளிர்விப்பான்கள் அளவு, வண்டல் மற்றும் உயிரியல் வளர்ச்சியை அகற்ற அவ்வப்போது அமைப்பு சுத்தம் செய்ய வேண்டியிருக்கலாம்.
இரண்டு வகையான குளிர்விப்பான்கள் பழுதடைவதைத் தடுக்கவும், செயல்திறனைப் பராமரிக்கவும், உபகரணங்களின் ஆயுளை நீட்டிக்கவும். பராமரிப்பைப் புறக்கணிப்பது விலையுயர்ந்த பழுதுபார்ப்பு மற்றும் செயலிழப்பு நேரத்திற்கு வழிவகுக்கும்.
அடிக்கடி கேட்கப்படும் கேள்விகள்
கிளைகோல் குளிரூட்டியைப் பயன்படுத்துவதன் முக்கிய நன்மை என்ன?
பயன்படுத்துவதன் முக்கிய நன்மை கிளைகோல் குளிர்விப்பான் உறைநிலைக்குக் கீழே உள்ள வெப்பநிலையில் செயல்படும் அதன் திறன் தண்ணீர் ஆபத்து இல்லாமல் குளிர்வித்தல் திரவம் உறைதல்இது குறைந்த வெப்பநிலை பயன்பாடுகளுக்கும், குளிர்ந்த காலநிலையில் வெளிப்புற நிறுவல்களுக்கும் ஏற்றதாக அமைகிறது.
எனது குளிரூட்டியில் தூய கிளைகோலைப் பயன்படுத்தலாமா?
இது பரிந்துரைக்கப்படவில்லை தூய கிளைகோலைப் பயன்படுத்துங்கள் ஒரு குளிர்விப்பான். கிளைகோல் பொதுவாக தண்ணீரில் கலக்கப்பட்டது விரும்பிய உறைநிலையை அடைந்து மேம்படுத்த வெப்ப பரிமாற்றம் திறன். தூய கிளைக்கால் விட குறைவான குறிப்பிட்ட வெப்ப கொள்ளளவு கொண்டது தண்ணீர், அதாவது வெப்பத்தை உறிஞ்சுவதில் இது குறைவான செயல்திறன் கொண்டது.
எனது குளிரூட்டியில் உள்ள கிளைகோலை எத்தனை முறை மாற்ற வேண்டும்?
அதிர்வெண் கிளைகோல் மாற்றீடு என்பது பல காரணிகளைப் பொறுத்தது, அவற்றில் வகை உட்பட கிளைகோல் பயன்படுத்தப்பட்டது, இயக்க நிலைமைகள் மற்றும் உற்பத்தியாளரின் பரிந்துரைகள். பொதுவாக, கிளைகோல் தீர்வுகள் குறைந்தபட்சம் ஆண்டுதோறும் சோதிக்கப்பட வேண்டும் மற்றும் ஒவ்வொரு 3-5 வருடங்களுக்கும் மாற்றப்பட வேண்டும். நீங்கள் ஒரு பயன்படுத்தினால் கிளைகோல் குளிர்விப்பான்கள் நீங்கள் அவ்வப்போது கிளைகோலின் அளவை சரிபார்க்க வேண்டும்.
குளிர்விப்பான்களுக்கு எத்திலீன் கிளைக்கால் அல்லது புரோப்பிலீன் கிளைக்கால் சிறந்ததா?
இரண்டும் எத்திலீன் கிளைக்கால் மற்றும் புரோப்பிலீன் கிளைக்கால் அவற்றின் நன்மைகள் மற்றும் தீமைகள் உள்ளன. எத்திலீன் கிளைக்கால் சிறப்பாக வழங்குகிறது வெப்ப பரிமாற்றம் மேலும் விலை குறைவாக உள்ளது, ஆனால் அது நச்சுத்தன்மை வாய்ந்தது. புரோப்பிலீன் கிளைகோல் உட்கொள்ளும் ஆபத்து உள்ள பயன்பாடுகளுக்கு நச்சுத்தன்மையற்றது மற்றும் பாதுகாப்பானது, ஆனால் இது சற்று குறைவாக உள்ளது. வெப்ப பரிமாற்றம் செயல்திறன். சிறந்த தேர்வு குறிப்பிட்ட பயன்பாடு மற்றும் பாதுகாப்புக் கருத்தாய்வுகளைப் பொறுத்தது.
எனது குளிரூட்டியில் கிளைகோல் செறிவு மிகக் குறைவாக இருந்தால் என்ன நடக்கும்?
என்றால் கிளைகோல் செறிவு மிகவும் குறைவாக உள்ளது, தி குளிர்வித்தல் குறைந்த வெப்பநிலையில் திரவம் உறைந்து போகக்கூடும், இது குறிப்பிடத்தக்க சேதத்தை ஏற்படுத்தும். குளிர்விப்பான் ஆவியாக்கி மற்றும் குழாய் போன்ற கூறுகள். இது விலையுயர்ந்த பழுதுபார்ப்பு மற்றும் செயலிழப்பு நேரத்திற்கு வழிவகுக்கும்.
வாட்டர் சில்லரில் என்ன வகையான தண்ணீரைப் பயன்படுத்த வேண்டும்?
வெறுமனே, பயன்படுத்தப்படும் நீர் ஒரு நீர் குளிர்விப்பான் இருக்க வேண்டும் சுத்திகரிக்கப்பட்ட நீர், காய்ச்சி வடிகட்டியது போல அல்லது அயனியாக்கம் நீக்கப்பட்ட நீர், கனிம உருவாக்கம் மற்றும் அரிப்பைக் குறைக்க. பயன்படுத்துதல் நகர நீர் சாத்தியம் ஆனால் கனிமங்கள் மற்றும் அசுத்தங்கள் இருப்பதால் அடிக்கடி பராமரிப்பு தேவைப்படலாம்.
முடிவுரை
நினைவில் கொள்ள வேண்டிய முக்கிய குறிப்புகள் இங்கே:
- கிளைகோல் குளிர்விப்பான்கள் பயன்படுத்து கிளைக்கால் மற்றும் தண்ணீரின் கலவை உறைநிலையைக் குறைக்க குளிர்வித்தல் திரவம், அவை உறைநிலைக்குக் கீழே செயல்பட அனுமதிக்கிறது தண்ணீர்.
- நீர் குளிர்விப்பான்கள் பயன்படுத்த மட்டும் தண்ணீர் என குளிர்வித்தல் நடுத்தர மற்றும் பொதுவாக மிகவும் திறமையானவை வெப்ப பரிமாற்றம் உறைநிலைக்கு மேலே செயல்படும் போது.
- ஒரு இடையேயான தேர்வு கிளைகோல் குளிர்விப்பான் மற்றும் ஒரு நீர் குளிர்விப்பான் குறிப்பிட்ட பயன்பாடு, இயக்க வெப்பநிலை மற்றும் சுற்றுச்சூழல் நிலைமைகளைப் பொறுத்தது.
- எத்திலீன் கிளைக்கால் மற்றும் புரோப்பிலீன் கிளைக்கால் இரண்டு முக்கியமா? கிளைகோல் வகைகள் பயன்படுத்தப்பட்டது குளிர்விப்பான்கள், ஒவ்வொன்றும் அதன் சொந்த நன்மைகள் மற்றும் தீமைகள் உள்ளன.
- சரியானதைத் தீர்மானித்தல் கிளைகோல் செய்ய தண்ணீர் உகந்த தன்மைக்கு விகிதம் மிக முக்கியமானது குளிர்விப்பான் செயல்திறன், சமநிலைப்படுத்துதல் உறைதல் பாதுகாப்பு மற்றும் வெப்ப பரிமாற்றம் திறன்.
- இருவருக்கும் வழக்கமான பராமரிப்பு அவசியம் கிளைகோல் மற்றும் நீர் குளிர்விப்பான்கள் உகந்த செயல்திறனை உறுதி செய்வதற்கும், செயலிழப்புகளைத் தடுப்பதற்கும், உபகரணங்களின் ஆயுளை நீட்டிப்பதற்கும்.
- சரியான வகையைப் பயன்படுத்துதல் குளிர்விப்பான் மேலும் அதை முறையாகப் பராமரிப்பது உங்கள் தொழில்துறை செயல்முறைகளின் செயல்திறன் மற்றும் செலவு-செயல்திறனை கணிசமாக பாதிக்கும்.
- முக்கிய இரண்டு வகைகளுக்கும் இடையிலான வேறுபாடு இன் குளிர்விப்பான்கள் இதன் பயன்பாடு கிளைகோல், இது ஒரு உறைதல் தடுப்பி.
- சரியான கிளைகோலின் விகிதம் செய்ய தண்ணீர் குறிப்பிட்ட இயக்க நிலைமைகள் மற்றும் விரும்பிய அளவைப் பொறுத்தது உறைதல் பாதுகாப்பு.
நினைவில் கொள்ளுங்கள், இடையிலான வேறுபாடுகளைப் புரிந்துகொள்வது கிளைகோல் மற்றும் நீர் குளிர்விப்பான்கள் உங்கள் தொழில்துறை பற்றி தகவலறிந்த முடிவுகளை எடுப்பதற்கு இது மிகவும் முக்கியமானது. குளிர்வித்தல் தேவைகள். இந்தக் கட்டுரையில் விவாதிக்கப்பட்ட காரணிகளை கவனமாகக் கருத்தில் கொள்வதன் மூலம், நீங்கள் சரியானதைத் தேர்ந்தெடுக்கலாம் குளிர்விப்பான் உங்கள் பயன்பாட்டிற்காகவும், உகந்த செயல்திறன், செயல்திறன் மற்றும் நீண்ட ஆயுளை உறுதி செய்யவும். உங்களுக்கு மேலும் உதவி தேவைப்பட்டால் அல்லது உங்கள் குறிப்பிட்ட தேவைகளைப் பற்றி விவாதிக்க விரும்பினால், தயவுசெய்து உங்கள் நம்பகமான தொழில்துறை நீர் குளிர்விப்பான் உற்பத்தி கூட்டாளியான எங்களைத் தொடர்பு கொள்ள தயங்க வேண்டாம். உங்கள் இலக்கை அடைய உங்களுக்கு உதவ நாங்கள் இங்கே இருக்கிறோம். குளிர்வித்தல் இலக்குகள்!
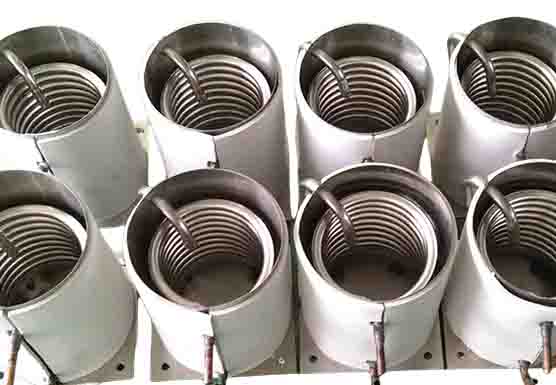