-
Далиншань Индустриальный Гуандун
Оптимизация эффективности литьевых форм с помощью современных систем охлаждения для процессов литья пластмасс
Оптимизируйте производство пластика: важная роль систем охлаждения процесса
Оглавление
Это всеобъемлющее руководство погружает вас в мир технологическое охлаждение для пластмассовая промышленность, объясняя, насколько это важно для достижения превосходного качества продукции, эффективности и экономии затрат Технологии охлаждения имеют важное значение. Независимо от того, участвуете ли вы в пластиковая инъекция, экструзия, или другой пластический процесс приложений, понимание того, как эффективно прохладный Ваше оборудование и материалы имеют первостепенное значение. Мы рассмотрим различные системы охлаждения, сосредоточив внимание на важности Температура пресс-формы имеет решающее значение для эффективного охлаждения процесса переработки пластмасс контроль и как скорость охлаждения процесс влияет на ваш конечный продукт. Это обязательно к прочтению для тех, кто хочет оптимизировать свой пластик производство. Мы рассмотрим, как охлаждение работает, какие решения доступны и преимущества выбора правильного система охлаждения.
Почему правильное охлаждение имеет решающее значение для пластмассовой промышленности?
Правильное охлаждение является краеугольным камнем пластмассовая промышленность, напрямую влияющие на качество продукции, время цикла и общую эффективность работы. В таких процессах, как пластиковая инъекция формование, поддержание точной температуры для охлаждения технологической воды форма температура имеет решающее значение для обеспечения пластик затвердевает правильно. Неадекватный или непоследовательный охлаждение приводит к дефектам, неточностям размеров и увеличению сроков производства.
The процесс охлаждения играет важную роль в укреплении пластиковая смола. Когда горячий пластик вводится в форма, его необходимо охлаждать, чтобы сохранить форму и размеры конечного продукта. Без постоянного и эффективного охлаждения пластик может деформироваться, сжиматься или иметь дефекты. Поэтому эффективный система технологического охлаждения имеет важное значение для достижения оптимальных результатов в пластмассах производственный процесс.
Понимание важности системы охлаждения
Надежный система охлаждения это больше, чем просто удобство; это важный компонент любого эффективного пластмассы Производственный процесс. система охлаждения речь идет не только о снижении температуры, но и о контроле скорость охлаждения процесс для обеспечения равномерного затвердевания и предотвращения дефектов формованных изделий.
Хорошо продуманный система охлаждения помогает поддерживать постоянную рабочую температуру на всех обрабатывающих машинах, что приводит к повышению качества продукции, уменьшению брака и повышению общей производительности. Кроме того, такая система может значительно сократить цикл раз, что приводит к большей производительности. Надежная система способствует однородности продукта и снижает эксплуатационные расходы за счет увеличения объемов производства и снижения потребления энергии.
Различные типы систем охлаждения для пластмассовой промышленности
The пластмассовая промышленность использует различные системы охлаждения для удовлетворения различных потребностей в охлаждении, каждое из которых имеет уникальные характеристики и преимущества. Понимание различных типов поможет вам выбрать лучшее решение для ваших конкретных требований.
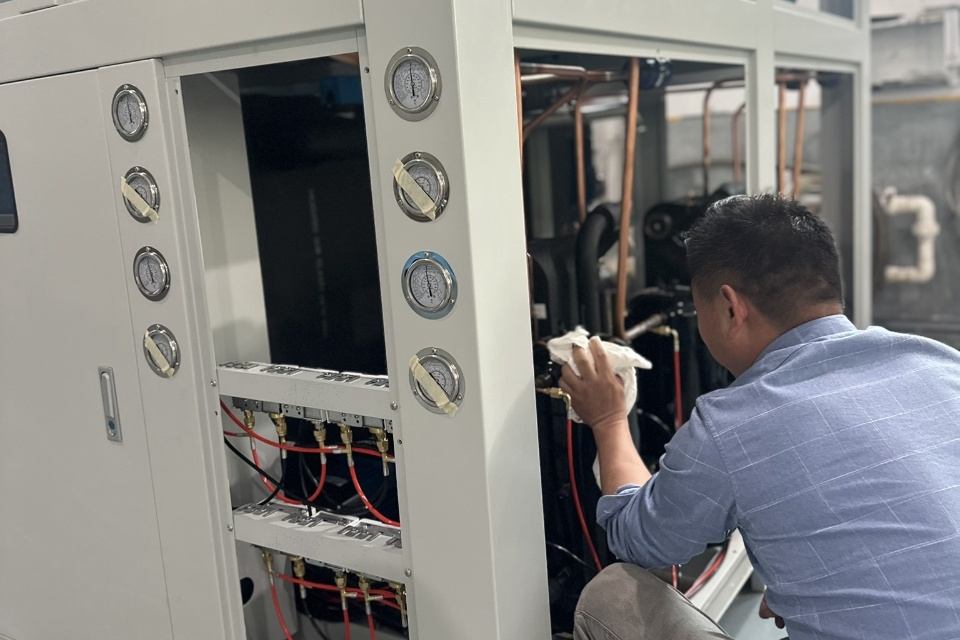
- Охладители воды: Эти системы используют охлажденная вода поглощать нагревать от технологического оборудования. Охладители воды очень эффективный и обеспечить превосходный Контроль температуры пресс-формы имеет важное значение для эффективного выдувного формования. Они особенно эффективны в условиях непрерывного воздействия высоких температур, особенно в производстве пластмасс.
- Градирни: Эти системы используют испарительное охлаждение рассеивать нагревать в атмосферу. Градирни являются жизненно важными компонентами в системах охлаждения. принцип испарения для высвобождения тепловая энергия, позволяя им прохладная вода для использования в промышленных процессах. Этот тип системы работает эффективно, обеспечивая прохладная вода, но есть количество потеря воды из-за испарения.
- Чиллеры с воздушным охлаждением: Эти системы рассеиваются нагревать в окружающий воздух использование компрессора для улучшенного охлаждения ребристый теплообменник и часто их проще установить, чем с водяным охлаждением системы, но они могут быть не столь эффективны в жарком климате. Чиллеры с воздушным охлаждением эффективны в условиях ограниченного пространства или ограниченного использования воды.
- Центральные охладители: Эти чиллеры предоставлять охлаждение для нескольких систем охлаждения обрабатывающие машины из одного блок охлажденияи обеспечивают масштабируемость и эффективное управление ресурсами для крупных объектов. Центральные чиллеры с винтовым охлаждением и водяным охлаждением вот примеры этого.
- Переносные охладители: Эти мобильные чиллеры может быть легко перемещен и подключен к разному оборудованию по мере необходимости, предлагая гибкость и удобство для небольших операций. Мы также предлагаем переносные охладители которые идеально подходят для различных нужд охлаждения.
Выбор оптимального система охлаждения зависит от нескольких факторов, включая масштаб вашей деятельности, специфику пластические процессы вовлеченных и местных условий окружающей среды. Каждый тип имеет свои плюсы и минусы, и идеальная система будет соответствовать вашим конкретным требованиям.
Роль охладителей в литье пластмасс под давлением
В пластиковая инъекция формовка, чиллеры имеют важное значение для поддержания температура формы имеет решающее значение для затвердевания пластика. Они удаляют нагревать из горячий пластик и помочь затвердевать это гарантирует, что конечный продукт соответствует требуемым спецификациям и размерам. форма Контроль температуры имеет первостепенное значение для обеспечения постоянного качества продукции, оптимального время охлаждения и минимизация дефектов.
Эффективный охлаждение пресс-формы приводит к более короткому цикл литья под давлением раз, более высокие темпы производства и снижение процента брака. Недостаточное охлаждение, с другой стороны, может привести к деформации деталей, плохой обработке поверхности и увеличению производственных затрат. Поэтому надежный и эффективный охладитель является важнейшей инвестицией для любого пластиковая инъекция операция.
Значение градирен в промышленных процессах
Градирни являются ключевым компонентом во многих промышленных системы охлаждения, особенно когда необходимо отвести большое количество тепла, они работают, выделяя нагревать через испарение вода, что является естественным и весьма эффективный Метод отвода тепла. Разные типы градирен доступны в зависимости от требований вашего конкретного применения.
Градирни часто сочетаются с чиллеры с водяным охлаждением уменьшить потребление воды и связанные с ними эксплуатационные расходы. градирня принимает подогретый технологическая вода из охладитель, охлаждает его через испарительное охлаждение, и рециркулирует более прохладная вода вернуться к охладитель. Пока градирни может помочь сократить цикл, они также могут быть источником потеря воды, поэтому необходим тщательный анализ потребностей вашего объекта в охлаждении, чтобы убедиться, что это наилучший вариант охлаждающее решение.
Важность устройств контроля температуры
Блоки контроля температуры (TCU) имеют решающее значение для поддержания точного температура пресс-формы в инъекция формовка процесс. TCU работают в тандеме с чиллеры к контролировать температуру принадлежащий форма именно путем распространения либо вода или масло через охлаждающие каналы в процессах выдувного формования.
Поддерживая точные температура пресс-формы, TCU обеспечивают согласованность в пластиковая инъекция процесса, что приводит к более высокому качеству продукции и меньшему количеству дефектов. Они гарантируют, что пластиковый материал затвердевает равномерно и предсказуемо, предотвращая коробление, усадку и другие несоответствия, и они обеспечивают единообразие контроль температуры, что способствует повышению эффективности производства и снижению процента брака.
Понимание процесса водяного охлаждения
Водяное охлаждение широко используемый метод в промышленности системы охлаждения, используя превосходство передача тепла возможности вода. В водяное охлаждение система, Технологическая вода перекачивается из оборудования, через теплообменник, где он поглощает тепло, а затем охлаждается перед рециркуляцией через замкнутый контур система.
The вода эффективно поглощает тепло в технологиях охлаждения the технологическое тепло и затем отправляется в градирня или чиллер с водяным охлаждением, где нагревать выбрасывается в атмосферу или в хладагент контур, что делает использование воды эффективным способом охлаждения процессов. Это надежный процесс что позволяет использовать эффективную технологию производства пластмасс охлаждение и последовательный температура воды контроль.
Различные методы теплопередачи в системах охлаждения
Передача тепла является жизненно важным механизмом в промышленности. системы охлаждения. Понимание того, как работает этот процесс, помогает оптимизировать производительность системы. Существует три основных метода передача тепла используется в промышленности охлаждение:
- Проводимость: Нагревать передается через прямой контакт между предметами или жидкостями.
- Конвекция: ключевой принцип охлаждения в процессе переработки пластмасс Нагревать передается посредством движения текучих сред (жидкостей или газов).
- Радиация: Нагревать передается посредством электромагнитных волн.
Понимание того, как эти методы передача тепла работа является ключом к выбору правильных типов оборудования для ваших конкретных нужд. Например, градирни используют принцип испарительное охлаждение для передача тепла, пока чиллеры используют комбинацию теплопроводности и конвекции.
Оптимизация охлаждения для производства пластмасс
Для достижения наилучших результатов в производство пластмасс, оптимизируя ваш процесс охлаждения имеет важное значение. Это включает в себя выбор правильного охлаждающее оборудование, обеспечивая надлежащее установка и обслуживаниеи мониторинг вашей системы, чтобы убедиться, что все работает эффективно.
Чтобы гарантировать ваш система охлаждения работает оптимально, вы должны учитывать конкретные потребности вашей производственной линии. Это включает в себя конкретный тип пластик вы используете, объем производства, условия окружающей среды и конкретное используемое оборудование. Эффективное планирование и выбор энергоэффективный оборудование имеет решающее значение для создания идеальная система транспортировки для технологий охлаждения вашего объекта.
Часто задаваемые вопросы об охлаждении при производстве пластмасс
Как выбрать охладитель подходящего размера для моей литьевой машины?
Чтобы выбрать правильный размер охладитель, рассчитайте количество тепла, вырабатываемого вашей машиной, исходя из ее тоннажа и времени цикла. Проконсультируйтесь с охлаждающее оборудование специалист определит правильную холодопроизводительность для вашего предприятия.
позвоните нам или напишите нам по электронной почте.
Каковы преимущества использования градирни вместо чиллера?
Градирни часто более энергоэффективный чем чиллеры, особенно в крупных операциях. Они также уменьшают потребление воды по сравнению с системами, которые используют чиллеры с водяным охлаждением без градирни.
Какое техническое обслуживание требуется для системы технологического охлаждения?
Техническое обслуживание обычно включает в себя регулярную чистку градирня, мониторинг качество воды, проверка хладагент уровни и проверка системы на предмет утечек или повреждений. Правильное обслуживание продлит срок службы система охлаждения и предотвращения эксплуатационных проблем.
Что такое естественное охлаждение и как оно работает?
Свободное охлаждение использует температура окружающей среды обеспечить технологическое охлаждение в прохладное время года, уменьшая или исключая необходимость в механическом охлаждение, тем самым уменьшая потребление энергии.
Ключевые выводы: основные моменты, касающиеся охлаждения в процессе переработки пластмасс
- Правильное охлаждение имеет решающее значение для достижения высокого качества пластиковые изделия.
- Другой системы охлаждения доступны, в том числе чиллеры, градирни, а также их комбинации.
- Точный контроль температуры имеет решающее значение в литье под давлением и экструзия.
- Регулярное техническое обслуживание имеет важное значение для система охлаждения эффективность и надежность.
- Оптимизация вашего система охлаждения приводит к большей эффективности, меньшему эксплуатационные расходыи улучшение качества продукции.
Мы предлагаем полный ассортимент из системы технологического охлаждения, разработанный для удовлетворения Разнообразие приложений в пластмассовая промышленностьНаши решения созданы с целью обеспечения превосходной производительности, долговечности и экономия энергии. Мы приветствуем возможность обсудить потребности вашего объекта и предложить индивидуальное решение, оптимизированное для максимальная производительность. Пожалуйста, свяжитесь с нами, чтобы обсудить ваши конкретные потребности.