-
Далиншань Индустриальный Гуандун
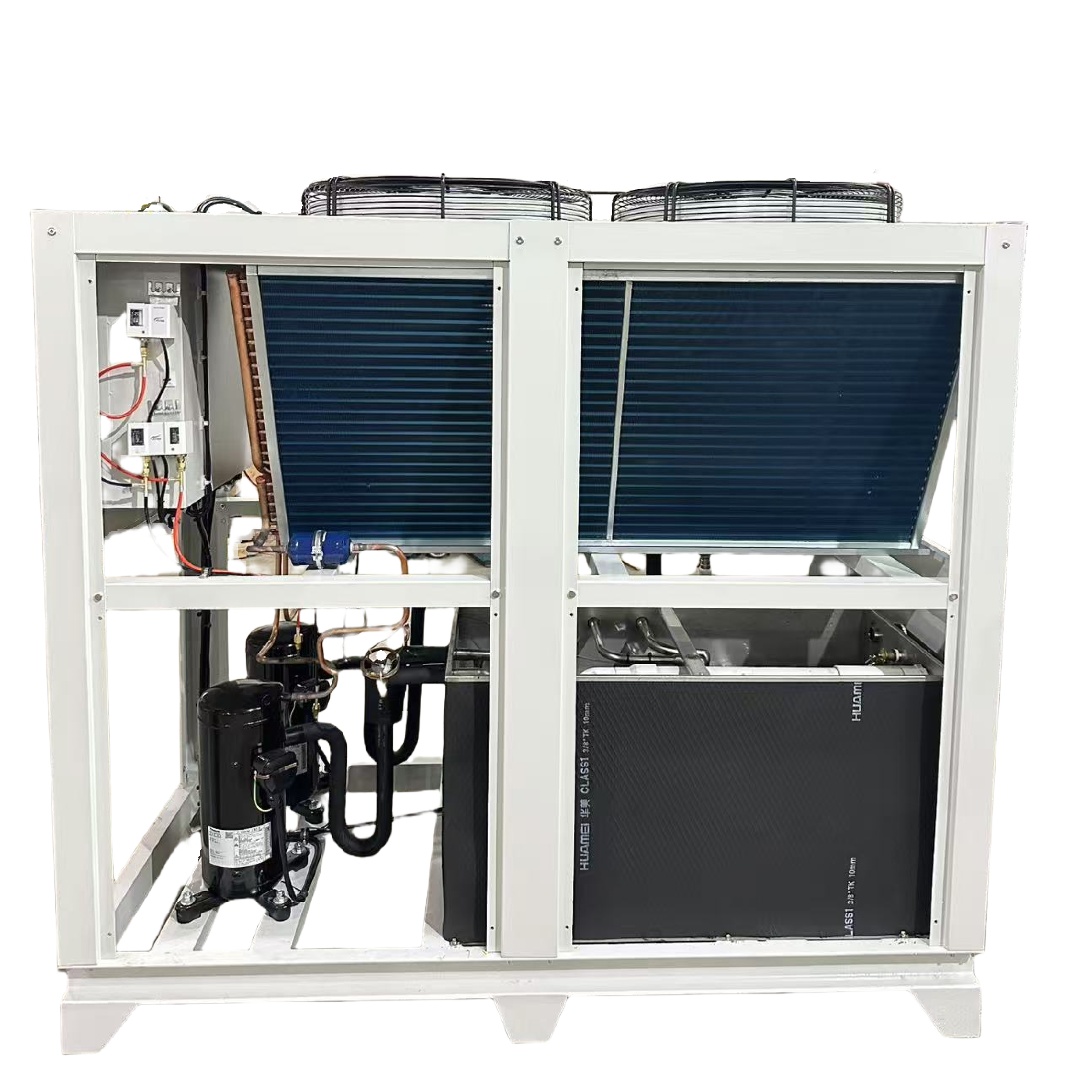
как работают вместе водоохладители и вентиляционные установки
Как чиллеры и воздухообрабатывающие агрегаты работают вместе в вашей системе HVAC
В этой статье исследуются сложные взаимоотношения между чиллеры и Вентиляционные установки (AHU) в пределах Системы ОВиК, сосредоточившись на том, как эти компоненты взаимодействуют для обеспечения эффективного охлаждение решения. Как ведущий производитель промышленных охладители воды, мы понимаем важность надежного и эффективного система охлаждения для различных отраслей промышленности. Независимо от того, работаете ли вы в пластмассовой и резиновой промышленности, машиностроении или управляете центром обработки данных, понимание того, как ваш система отопления, вентиляции и кондиционирования воздуха работает имеет решающее значение. Это руководство демистифицирует процесс, объяснит, почему правильный очистка воды является существенным, и продемонстрировать, почему эти знания ценны для тех, кто полагается на эти системы. Эту статью стоит прочитать, потому что она дает всестороннее понимание охладитель и АХУ операции, необходимые для оптимизации производительности и обеспечения долговечности ваших промышленных процессов.
Оглавление
1. Что такое чиллер и как он работает?
А охладитель является важнейшим компонентом многих Системы ОВиК, отвечающий за отвод тепла из жидкости через парокомпрессионный или абсорбционный холодильный цикл. Проще говоря, охладитель охлаждает воду, которая затем используется для прохладный здание или процесс. Я видел своими глазами на нашем производственном предприятии, насколько важно хорошо функционирующее охладитель есть. Наш чиллеры производятся в соответствии с высокими стандартами эффективности и надежности.
Чиллеры использовать хладагент к прохладный вода. Процесс включает в себя хладагент изменение состояния от газа низкого давления до жидкости высокого давления и обратно. испаритель вот где начинается волшебство —охлажденная вода распространяется через него, и хладагент поглощает тепло из воды, вызывая хладагент испаряться. Затем это тепло отводится через конденсатор, часто с помощью градирня. Этот охлажденная вода затем перекачивается по всему зданию, обеспечивая необходимое охлаждение. Это непрерывный цикл, который обеспечивает бесперебойную работу ваших операций. Например, в пищевой промышленности и производстве напитков наши чиллеры обеспечить хранение продукции при оптимальных температурах, сохраняя ее качество и безопасность.
Компонент | Функция |
Испаритель | Поглощает тепло из воды, охлаждая ее. |
Конденсатор | Отводит поглощенное тепло, часто с помощью градирня. |
Компрессор | Распространяет хладагент и увеличивает его давление и температуру. |
Расширительный клапан | Снижает давление и температуру хладагент. |
2. Что такое установка обработки воздуха (AHU)?
Ан Установка обработки воздуха (AHU) по сути это легкие вашего система отопления, вентиляции и кондиционирования воздуха. Он кондиционирует и обеспечивает циркуляцию воздуха по всему зданию. АХУ обычно включает в себя вентилятор, нагреватель или охлаждение элементы, стойки фильтров, шумоглушители и демпферы. обработчик воздуха отвечает за поддержание качества воздуха в помещении и обеспечение теплового комфорта. По нашему опыту, хорошо поддерживаемый АХУ может значительно повысить общую эффективность система отопления, вентиляции и кондиционирования воздуха.
AHU-установки могут быть сконфигурированы различными способами в зависимости от конкретных потребностей здания. Они могут быть простыми, только с вентилятором и фильтром, или более сложными, включающими охлаждающие змеевики, увлажнители и системы рекуперации тепла. AHU-установки работа по рисованию наружный воздух, кондиционирование его и подача в здание. обратный воздух из комнат смешивается с наружный воздух, фильтруется, а затем нагревается или охлаждается по мере необходимости. Это обеспечивает постоянный поток свежей, кондиционированный воздух по всему зданию. В медицинской промышленности, например, наши AHU-установки помогают поддерживать стерильную среду, что имеет решающее значение для ухода за пациентами и проведения хирургических процедур. Центральные чиллеры с воздушным охлаждением и винтовыми компрессорами идеально подходит для такого рода применения.
3. Как работают вместе чиллеры и установки кондиционирования воздуха?
Сотрудничество между чиллеры и AHU-установки это плавный танец передачи энергии. Чиллеры и AHU-установки работают вместе, чтобы обеспечить комфортную и контролируемую среду в помещении. охладитель генерирует охлажденная вода, который затем перекачивается в АХУ. АХУ дома а охлаждающий змеевик через который охлажденная вода Потоки. Как АХУ продувает воздух через охлаждающий змеевик, охлажденная вода поглощает тепло из воздуха, таким образом охлаждение перед тем, как он распространится по всему зданию. На нашем заводе мы оптимизировали этот процесс, чтобы обеспечить максимальную энергоэффективность и минимальные эксплуатационные расходы.
Вот как работает этот процесс: охлажденная вода предоставлено охладитель входит в охлаждающий змеевик в АХУ. теплый воздух из здания втягивается в АХУ и проходит над охлаждающий змеевик. охлажденная вода поглощает тепло в воздухе, и сейчас прохладный воздух распространяется через работа воздуховода в различные части здания. Это охлажденная вода, поглотив тепло, возвращается обратно в чиллер снова охлаждаться, завершая цикл. Эта синергия жизненно важна в таких отраслях, как химическая и фармацевтическая промышленность, где точный контроль температуры имеет важное значение для химических реакций и стабильности продукта.
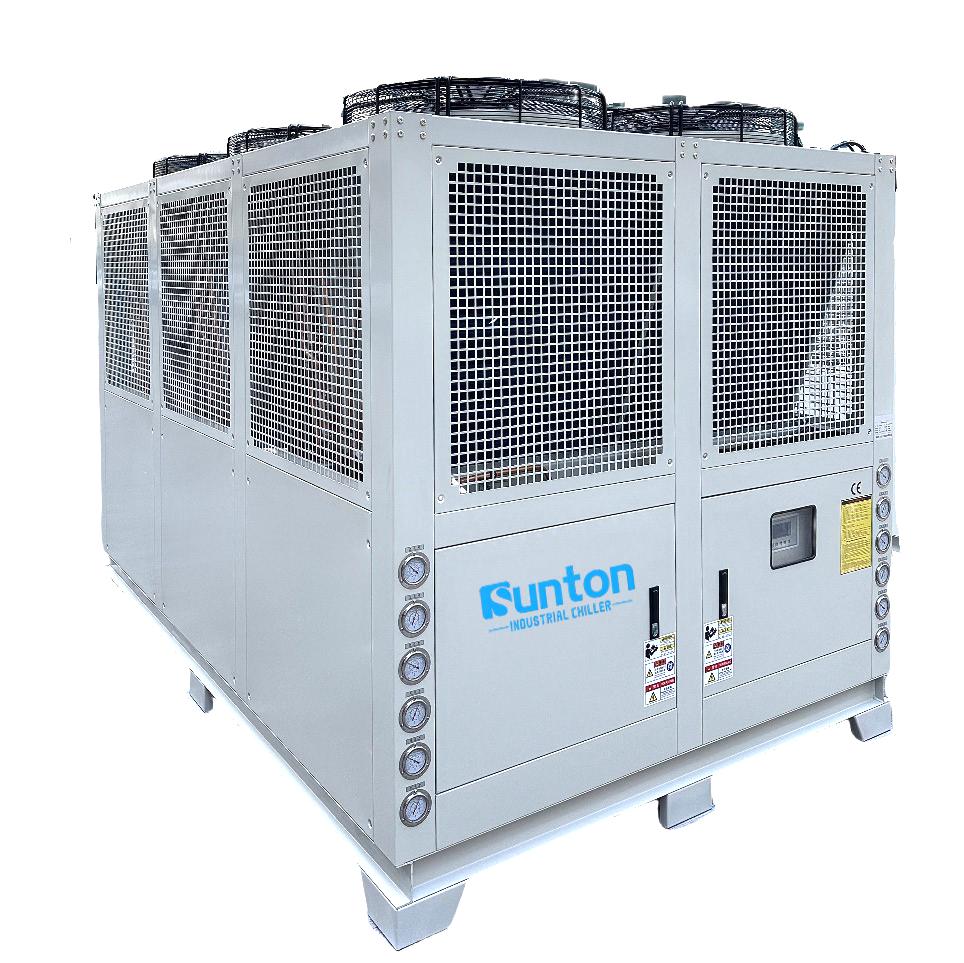
4. Какую роль играет градирня в этой системе?
А градирня часто используется вместе с чиллер с водяным охлаждением для отвода тепла из системы. Градирни работать, подвергая воду воздействию окружающий воздух, позволяя некоторой ее части испариться, что в свою очередь охлаждает оставшуюся воду. Это прохладный Затем вода используется для поглощения тепла из конденсатор принадлежащий охладитель. В наших промышленных установках мы часто интегрируем градирни для повышения эффективности нашей чиллеры с водяным охлаждением, особенно в теплом климате или в периоды пиковой нагрузки.
Процесс начинается, когда теплая вода из конденсатор чиллера закачивается в верхнюю часть градирня. Вода распыляется в воздушный поток, и большой вентилятор дует воздух через падающую воду. Это способствует испарению, которое отводит тепло от воды. Охлажденная вода собирается на дне башни и перекачивается обратно в охладительЭтот непрерывный процесс гарантирует, что охладитель может работать эффективно, поддерживая постоянный запас прохладный вода в конденсатор. Градирни особенно важны в таких отраслях, как производство пластмасс и резины, где управление теплом, выделяемым оборудованием, имеет решающее значение. Узнайте больше о конкретных Градирня.
5. Какие существуют типы чиллеров?
Чиллеры обычно делятся на два основных типа: чиллеры с воздушным охлаждением и чиллеры с водяным охлаждением. Чиллеры с воздушным охлаждением использовать окружающий воздух для отвода тепла от хладагент, пока чиллеры с водяным охлаждением используют воду, часто в сочетании с градирня. Каждый тип охладитель имеет свои преимущества и подходит для различных применений. В наших производственных процессах мы часто используем оба типа, в зависимости от конкретных требований проекта.
- Чиллеры с воздушным охлаждением:
- Используйте вентиляторы для продувать воздух через конденсатор к прохладный the хладагент.
- Как правило, их проще устанавливать и обслуживать.
- Подходит для небольших объектов или мест, где ощущается нехватка воды.
- Чиллеры с водяным охлаждением:
- Используйте воду для прохладный the хладагент в конденсатор.
- Более энергоэффективно, особенно в крупных приложениях.
- Часто используется с градирня для рассеивания тепла.
Выбор правильного типа охладитель зависит от таких факторов, как размер приложения, доступность воды и общие цели энергоэффективности. Например, электронная промышленность часто предпочитает чиллеры с водяным охлаждением из-за их более высокой эффективности и способности выдерживать большие тепловые нагрузки. Узнать больше о Винтовой чиллер с водяным охлаждением.
6. Почему водоподготовка важна в системах охлаждения?
Очистка воды является критическим аспектом поддержания системы охлаждения, особенно для чиллеры с водяным охлаждением. Неочищенная вода может привести к образованию накипи, коррозии и биологическому обрастанию, что может значительно снизить эффективность и срок службы охладительНа нашем заводе мы внедряем строгие очистка воды протоколы, гарантирующие долговечность и производительность нашего оборудования.
Правильный очистка воды включает использование химических ингибиторов для предотвращения образования накипи и коррозии, а также биоцидов для контроля биологического роста. Регулярный мониторинг и корректировка химии воды также важны. Поддерживая оптимальное качество воды, вы можете предотвратить образование отложений на поверхностях теплообмена, обеспечить эффективную теплопередачу и избежать дорогостоящего ремонта или замены. Это особенно важно в таких отраслях, как лаборатории и научно-исследовательские институты, где постоянная производительность и надежность имеют первостепенное значение.
7. Как можно оптимизировать систему охлаждения и кондиционирования воздуха?
Оптимизация вашего охладитель и Система кондиционирования воздуха включает несколько ключевых стратегий. Регулярное обслуживание имеет первостепенное значение. Это включает в себя очистку катушек, замену фильтров, проверку хладагент уровни и обеспечение надлежащего потока воды. По моему опыту, проактивный график технического обслуживания может предотвратить многие распространенные проблемы и продлить срок службы вашего оборудования.
Другим важным аспектом является мониторинг производительности системы. Отслеживая потребление энергии, охлажденная вода температуры и скорости воздушного потока, вы можете определить неэффективность и внести необходимые коррективы. Внедрение системы автоматизации зданий (BAS) может помочь автоматизировать этот процесс и предоставить данные о производительности системы в режиме реального времени. Кроме того, оптимизация стратегий управления для вашего чиллеры и AHU-установки может привести к значительной экономии энергии. Например, использование приводов с переменной скоростью на насосах и вентиляторах может регулировать производительность системы в зависимости от спроса, снижая потребление энергии в непиковые периоды. Для полиграфической промышленности оптимизация этих систем может привести к улучшению качества печати и снижению эксплуатационных расходов. Вам может быть интересно узнать больше о Гликолевые охладители.
8. Каковы наиболее распространенные проблемы с чиллерами и блоками обработки воздуха?
Несколько распространенных проблем могут повлиять на производительность чиллеры и AHU-установки. Хладагент утечки, например, могут уменьшить охлаждение вместимость охладитель и привести к повышенному потреблению энергии. охлаждающие змеевики в АХУ может ограничить поток воздуха и снизить эффективность теплопередачи. На нашем производственном предприятии мы регулярно проводим проверки на предмет этих проблем и оперативно их решаем для поддержания оптимальной производительности.
Другие распространенные проблемы включают отказы компрессора, водяной насос проблемы и электрические неисправности. Регулярное обслуживание и проверки могут помочь выявить и устранить эти проблемы до того, как они приведут к серьезным поломкам. Кроме того, обучение персонала распознаванию признаков потенциальных проблем может помочь предотвратить простои и обеспечить непрерывную работу. Для лазерной промышленности быстрое решение этих проблем имеет решающее значение для предотвращения сбоев в работе точных лазеров.
9. Как работает холодильный цикл в чиллере?
The хладагент цикл - это суть того, как охладитель работает. Это непрерывный цикл, где хладагент меняет состояние, чтобы поглощать и отдавать тепло. Цикл начинается в испаритель, где охлажденная вода охлаждается. хладагентв состоянии низкого давления и низкой температуры поглощает тепло из воды, заставляя ее испаряться, превращаясь в газ.
Далее компрессор увеличивает давление и температуру хладагент газ. Этот горячий газ высокого давления затем перемещается в конденсатор. В чиллер с водяным охлаждением, конденсаторная вода поглощает тепло из хладагент, заставляя его снова конденсироваться в жидкость. В охладитель с воздушным охлаждением, фанаты продувать воздух через конденсатор для достижения того же эффекта. Теперь жидкий хладагент проходит через расширительный клапан, который снижает его давление и температуру, и цикл начинается снова. Этот непрерывный цикл обеспечивает эффективный охлаждение и имеет жизненно важное значение для таких отраслей, как машиностроение, где необходимо эффективно управлять теплом, выделяемым оборудованием.
10. Почему стоит выбрать наши промышленные водоохладители?
Являясь ведущим производителем промышленного охладители водыМы гордимся тем, что предоставляем высококачественную, надежную и эффективную продукцию. охлаждение решения. Наши чиллеры разработаны для удовлетворения конкретных потребностей различных отраслей промышленности, от пластмассовой и резиновой промышленности до центров обработки данных. Мы используем передовые технологии и строгие процессы контроля качества, чтобы гарантировать, что наша продукция соответствует самым высоким стандартам. Например, наши чиллеры используемые в химической и фармацевтической промышленности, предназначены для обеспечения точного контроля температуры, что имеет решающее значение для химических реакций и стабильности продукта.
Наша приверженность удовлетворению потребностей клиентов отличает нас. Мы тесно сотрудничаем с нашими клиентами, чтобы понять их уникальные требования и предоставить индивидуальные решения, которые соответствуют их потребностям. Наша команда опытных инженеров и техников всегда готова оказать поддержку и помощь, гарантируя, что ваши система охлаждения работает с максимальной эффективностью. Выбирая наше промышленное охладители воды, вы инвестируете в надежный и эффективный охлаждение решение, которое будет служить вашим потребностям в течение многих лет. Если вам нужно чиллер с водяным охлаждением для вашего центра обработки данных или охладитель с воздушным охлаждением Для вашего производственного процесса у нас есть знания и опыт, чтобы предоставить вам правильное решение.
Часто задаваемые вопросы
В чем основное различие между чиллерами с воздушным и водяным охлаждением?
Чиллеры с воздушным охлаждением использовать окружающий воздух для отвода тепла от хладагент, пока чиллеры с водяным охлаждением используют воду, часто в сочетании с градирня. Чиллеры с водяным охлаждением как правило, более энергоэффективны, особенно в крупных приложениях, в то время как чиллеры с воздушным охлаждением их проще устанавливать и обслуживать.
Как часто следует проводить техническое обслуживание холодильной машины и системы кондиционирования воздуха?
Регулярное обслуживание имеет решающее значение для оптимальной производительности. Мы рекомендуем проактивный график обслуживания, который включает очистку катушек, замену фильтров, проверку хладагент уровни и обеспечение надлежащего расхода воды не реже одного раза в год. Однако в зависимости от вашего конкретного применения и использования может потребоваться более частое обслуживание.
Каковы признаки утечки хладагента в моем чиллере?
Признаки хладагент утечка включает уменьшенную охлаждение емкость, повышенное потребление энергии и шипящие звуки из охладитель. Если вы подозреваете утечку, важно обратиться к квалифицированному специалисту для скорейшего осмотра и устранения проблемы.
Почему водоподготовка важна для чиллеров с водяным охлаждением?
Очистка воды имеет важное значение для предотвращения образования накипи, коррозии и биологического обрастания чиллеры с водяным охлаждением. Неочищенная вода может привести к снижению эффективности, увеличению потребления энергии и дорогостоящему ремонту или замене.
Как повысить энергоэффективность моей системы охлаждения?
Повышение энергоэффективности включает несколько стратегий, включая регулярное обслуживание, мониторинг производительности системы и оптимизацию стратегий управления. Внедрение системы автоматизации зданий (BAS) и использование приводов с переменной скоростью на насосах и вентиляторах также может привести к значительной экономии энергии.
Какие отрасли промышленности получают наибольшую выгоду от использования промышленных водоохладителей?
Многие отрасли промышленности извлекают выгоду из использования промышленных охладители воды, включая промышленность пластмасс и резины, машиностроение, пищевую промышленность и производство напитков, химическую и фармацевтическую промышленность, электронную промышленность, лазерную промышленность, полиграфию, медицинскую промышленность, лаборатории и научно-исследовательские институты, а также центры обработки данных. Каждая из этих отраслей имеет уникальные охлаждение требования, которые наши чиллеры предназначены для удовлетворения.
Краткое содержание
- Чиллеры и Вентиляционные установки (AHU) работать вместе в Системы ОВиК обеспечить эффективное охлаждение.
- Чиллеры охлаждают вода, которая затем используется AHU-установки к прохладный воздух распространяется по всему зданию.
- Градирни часто используются с чиллеры с водяным охлаждением для отвода тепла из системы.
- С воздушным охлаждением и чиллеры с водяным охлаждением Каждый из них имеет свои преимущества и подходит для различных областей применения.
- Очистка воды имеет решающее значение для поддержания эффективности и срока службы чиллеры с водяным охлаждением.
- Оптимизация вашего охладитель и Система кондиционирования воздуха включает в себя регулярное техническое обслуживание, мониторинг производительности и реализацию стратегий энергоэффективного управления.
- Распространенные проблемы с чиллеры и AHU-установки включать хладагент утечки, загрязненные катушки, отказы компрессора и водяной насос проблемы.
- The хладагент цикл включает в себя хладагент изменение состояний для поглощения и отвода тепла, обеспечивая эффективное охлаждение.
- Наши промышленные охладители воды разработаны для удовлетворения конкретных потребностей различных отраслей промышленности, обеспечивая надежную и эффективную работу охлаждение решения.
- Выбирая наш чиллеры означает инвестирование в качество, надежность и удовлетворенность клиентов. Наш опыт Взрывобезопасные охладители обеспечивает безопасность вашего оборудования.
Понимая сложную взаимосвязь между чиллеры, AHU-установки, и градирни, вы можете быть уверены, что ваш система отопления, вентиляции и кондиционирования воздуха работает с максимальной эффективностью, обеспечивая комфортную и контролируемую среду для ваших операций. Независимо от того, работаете ли вы в индустрии пластмасс и резины, управляете центром обработки данных или работаете в любой другой отрасли, которая зависит от точного контроля температуры, наши промышленные охладители воды являются идеальным решением для вашего охлаждение потребности. Свяжитесь с нами сегодня, чтобы узнать больше о том, как мы можем помочь вам оптимизировать ваш система охлаждения и достичь ваших операционных целей. Не стесняйтесь также ознакомиться с нашими Промышленные охладители для гальванических покрытий и Промышленные охладители для катка.
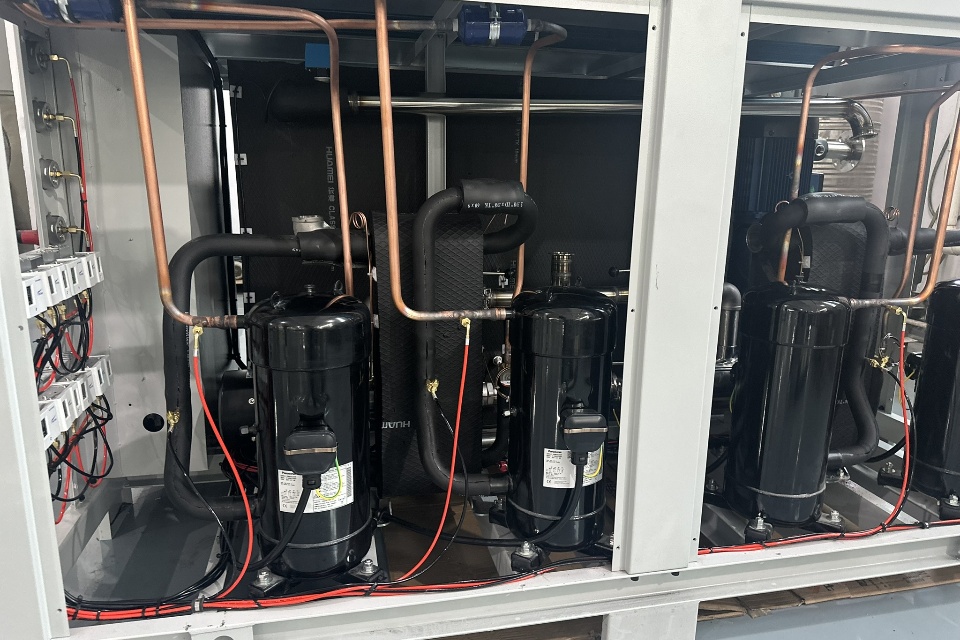