-
Далиншань Индустриальный Гуандун
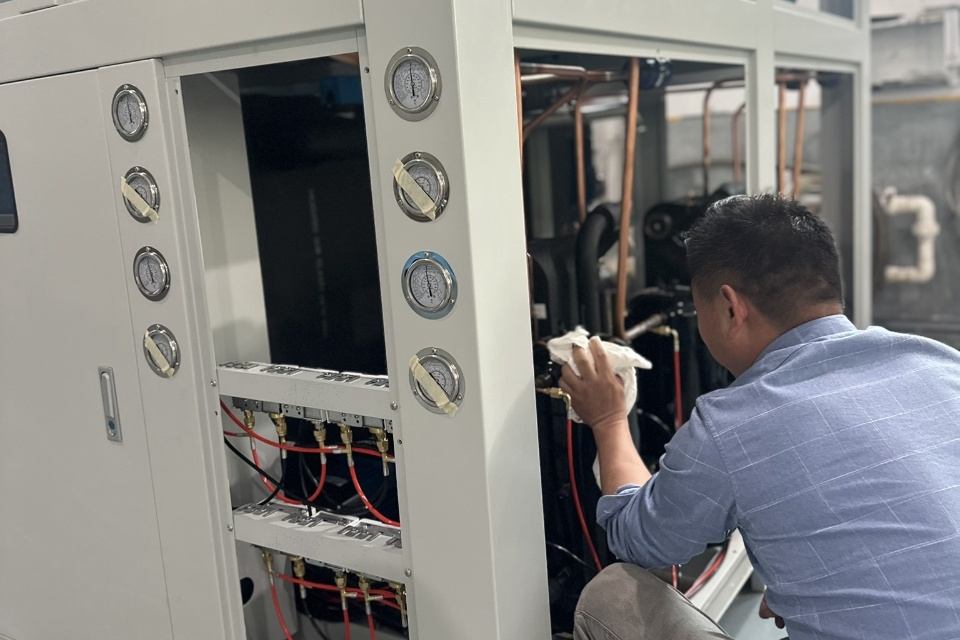
Пластиковые охладители: полное руководство по эффективному охлаждению технологических процессов
В этом руководстве представлен всесторонний обзор Пластиковые охладители необходимы для контроля температуры в различных промышленных процессах. и их решающая роль в пластмассовая промышленностьЧиллеры играют важную роль в управлении теплом от пластика во время производства. Мы рассмотрим, как эти чиллеры используются в процессе экструзии пластика. чиллеры работа, различные доступные типы и ключевые факторы, которые следует учитывать при выборе лучший охладитель для вашего конкретного пластический процесс. Если вы вовлечены в литье под давлением, экструзия или другие пластик Методы обработки, эта статья даст вам знания, которые помогут оптимизировать ваши процесс охлаждения и повысить качество продукции.
Оглавление
Что такое охладитель для переработки пластика?
А Охладитель пластика — это холодильный агрегат, предназначенный для охлаждения пластика в процессе его производства., также известный как технологический охладитель, это охлаждение система, специально разработанная для прохладный оборудование и материалы, используемые в пластические процессы нравиться литье под давлением и экструзия. Эти чиллеры Чиллеры обеспечивают точную и постоянную температуру для формовочных машин в пластмассовой промышленности. контроль, необходимый для производства высококачественной пластиковые изделия.
В пластмассовая промышленностьподдержание точной температуры имеет решающее значение. Пластиковые охладители обеспечить постоянное охлаждение формы, оборудования и материалов, предотвращение дефектов, улучшение качества продукции и повышение общей эффективности процесс производства пластика. Без охладитель, пластик может прохладный неравномерно, что приводит к короблению, усадке и другим проблемам с качеством.
Как работает охладитель при переработке пластмасс?
Пластиковые технологические охладители работают по принципу теплопередачи, используя хладагент для поглощения тепла из пластический процесс и рассеять его в другом месте. Давайте разберем, как эти охладители для пластмасс функция:
- Циркуляция хладагента: Специальный хладагент жидкость циркулирует в замкнутом контуре внутри охладитель.
- Поглощение тепла: The хладагент поглощает тепло из пластический процесс (как горячий формы в литье под давлением) через теплообменник. Это охлаждает пластик или используемое оборудование.
- Рассеивание тепла: Нагретый хладагент затем проходит через конденсатор, где поглощенное тепло высвобождается, как правило, в градирня или окружающий воздух (в системах с воздушным охлаждением).
- Охлаждение и повторение: The хладагент, теперь охлажденный, готов поглощать больше тепла, и цикл продолжается. Думайте об этом как о непрерывном цикле охлаждение.
Понимание этого процесса помогает операторам оценить важную роль каждого компонента, например компрессор, конденсатор, и испаритель, в поддержании надежное охлаждение и оптимальный контроль температуры.
Типы пластиковых охладителей: какой из них подойдет для ваших нужд?
Различные типы пластиковые охладители удовлетворять различные потребности и приложения в пластмассовая промышленность. Выбор правильного тип охладителя имеет решающее значение для оптимизации вашего процесса.
- Чиллеры с воздушным охлаждением: Эти чиллеры использовать воздух для прохладный the хладагент в конденсатор. Они относительно просты в установке и обслуживании, но менее эффективны в условиях высокой температуры. Винтовые чиллеры с воздушным охлаждением прочны и надежны для средних и крупных потребностей в охлаждении.
- Чиллеры с водяным охлаждением: Эти чиллеры используйте воду, чтобы прохладный the хладагент, предлагая более высокий энергоэффективность, особенно в теплом климате. Однако они требуют специального система водоснабжения, включая градирня или другой источник воды. Для оптимальной эффективности и экономии воды, рассмотрите Винтовые водоохладители с водяным охлаждением.
- Переносные охладители: Эти компактные устройства обеспечивают гибкость и могут легко перемещаться между различными машинами или процессами. Они идеально подходят для небольших операций или для дополнения существующих охлаждающая способность. Переносные охладители являются практичным выбором для различных систем охлаждения.
Выбор между воздушным охлаждением и с водяным охлаждением модели в значительной степени зависят от имеющихся у вас ресурсов, местного климата и долгосрочных эксплуатационных расходов. В то время как воздушные охлаждающие устройства могут показаться более простыми на первый взгляд, системы с водяным охлаждением часто предлагают значительные долгосрочные экономия средств через большее энергоэффективность, особенно в более теплых регионах. Это делает с водяным охлаждением чиллеры более экономичный выбор в долгосрочной перспективе. Для специальных требований к низким температурам, изучите Решения по охлаждению с помощью низкотемпературных охладителей.
Выбор правильного пластикового охладителя: ключевые факторы, которые следует учитывать
Выбор правый пластиковый охладитель включает в себя несколько факторов, которые могут существенно повлиять на ваш производство пластика процесс:
- Мощность охлаждения: The охладитель должно быть достаточно охлаждающая способность для удовлетворения потребностей вашего конкретного применения. Рассчитайте тепловую нагрузку, генерируемую вашими процессами, чтобы обеспечить адекватную мощность охлаждения.
- Контроль температуры: Точный контроль температуры имеет решающее значение в переработка пластика. Искать чиллеры с продвинутым регуляторы температуры и жесткие температурные допуски.
- Энергоэффективность: Энергоэффективность является ключевым фактором для снижения эксплуатационных расходов. Ищите чиллеры с высоким EER (коэффициентом энергоэффективности) и рассмотрите такие функции, как компрессоры с переменной скоростью для оптимизации потребление энергии.
- Требования к техническому обслуживанию: Выбирайте чиллер с легким доступом к компонентам для обслуживания, что сводит к минимуму время простоя.
Применение пластиковых охладителей в различных процессах
Пластиковые охладители имеют решающее значение для ряда процессов в промышленность по переработке пластмасс.
- Литье под давлением: Чиллеры играют важную роль в процесс литья под давлением путем охлаждения формы, что позволяет сократить время цикла и улучшить качество деталей. Это точный контроль температуры имеет важное значение для производства неизменно высококачественной продукции пластиковые детали.
- Экструзия: При экструзии, чиллеры поддерживать температуру цилиндра и матрицы экструдера, обеспечивая равномерный поток материала и предотвращая дефекты.
- Выдувное формование: Чиллеры охладить формы при выдувном формовании имеет решающее значение для получения желаемой формы деталей и предотвращения коробления.
- Термоформование: Чиллеры быстро прохладный сформированный пластик листы термоформуются, обеспечивая стабильность размеров и предотвращая деформацию.
Понимание этих конкретных приложений поможет вам выбрать лучшее решение для охладителя, отвечающее вашим конкретным потребностям. охладитель для охлаждения Ваше конкретное оборудование или применение потребует от вас оценки тепловой нагрузки, генерируемой во время процесс литья под давлением, или другой формование пластмасс методы. Учет этих тепловых нагрузок гарантирует, что вы приобретете охладитель с достаточным количеством охлаждающая способность для поддержания необходимого температура и давление необходимые для эффективного и производительного производства.
Поддержание оптимальной производительности вашего пластикового охладителя
Регулярное техническое обслуживание имеет решающее значение для увеличения срока службы и общая эффективность вашего пластиковый охладитель.
- Уборка: Регулярно очищайте змеевики конденсатора и испарителя от пыли и мусора, которые могут препятствовать теплопередаче и снижать эффективность.
- Проверки хладагента: Монитор хладагент своевременно контролируйте уровень и устраняйте утечки, чтобы обеспечить оптимальную эффективность охлаждения.
- Техническое обслуживание насоса: Регулярно проверяйте и обслуживайте насос для обеспечения надлежащего поток воды или поток хладагента через систему.
- Проверки системы управления: Периодически проверяйте правильность работы блока управления и убедитесь, что точный контроль температуры.
- Очистка воды: Чиллеры используются для поддержания оптимальной температуры воды в различных областях применения. Если вы используете чиллер с водяным охлаждением, реализуя вода Программа обработки имеет решающее значение для предотвращения образования накипи и коррозии в система водоснабжения. Правильно поддерживаемый вода система обеспечивает эффективное охлаждение и продлевает срок службы вашего охладитель. Обычный вода Проверка качества и обработка могут предотвратить образование минеральных отложений и накипи, которые могут препятствовать поток воды и уменьшить охладитель's охлаждение эффективность.
Соблюдая эти правила технического обслуживания, вы можете быть уверены, что ваш чиллер продолжит обеспечивать надежное охлаждение, увеличивая срок его службы и способствуя постоянному качеству продукции. Правильное обслуживание также способствует энергоэффективность и снижение ваши эксплуатационные расходы. Рассмотрите возможность изучения таких вариантов, как Центральные чиллеры с винтовым охлаждением и водяным охлаждением для крупномасштабных нужд охлаждения.
Часто задаваемые вопросы о пластиковых охладителях
Как лучше всего определить необходимую охлаждающую способность для моего процесса?
Требуемая мощность охлаждения зависит от таких факторов, как размер и тип вашего оборудования для обработки, тип обрабатываемого пластика и желаемое время цикла. Проконсультируйтесь с экспертом по чиллерам, чтобы точно рассчитать ваши конкретные потребности в охлаждении.
Какие типы систем охлаждения доступны для пластиковых чиллеров?
Основные типы — с воздушным и водяным охлаждением. Воздушные чиллеры используют воздух для рассеивания тепла, а водяные — воду. Выбор зависит от таких факторов, как температура окружающей среды, доступность воды и соображения стоимости.
Как работает регулятор температуры в пластиковом охладителе?
Регулятор температуры действует как мозг охладителя, контролируя охлажденная вода (или процесс вода) температуры и регулировка работы охладителя для поддержания заданного значения. Это обеспечивает точную и последовательную температура воды для оптимального охлаждения процесса.
Каковы преимущества использования переносного пластикового охладителя?
Переносные охладители обеспечивают гибкость, позволяя вам легко перемещать их между различными машинами или процессами. Они идеально подходят для небольших операций или для дополнения существующих систем охлаждения.
Основные выводы: оптимизация переработки пластика с помощью правильного охладителя
- Пластиковые охладители необходимы для последовательного и эффективного охлаждение в пластмассовая промышленность.
- Выбор правильного типа чиллера (с воздушным или водяным охлаждением) и его размера (холодопроизводительности) имеет решающее значение для оптимальной производительности.
- Регулярное техническое обслуживание имеет решающее значение для максимального увеличения срока службы и эффективности чиллера.
- Различные процессы переработки пластмасс (литье под давлением, экструзия, выдувное формование, термоформование) предъявляют особые требования к охлаждению.
- Сотрудничество с авторитетным производителем чиллеров может обеспечить экспертное руководство и поддержку.
Следуя рекомендациям и рекомендациям, представленным в этом руководстве, вы сможете эффективно управлять процессами охлаждения, что приведет к повышению качества пластиковых изделий, повышению эффективности работы и увеличению прибыльности. Свяжитесь с нами сегодня чтобы обсудить ваши конкретные охлаждающие приложения и изучите наш широкий ассортимент Решения для чиллеров. Мы также предлагаем Гликолевые охладители для специализированных нужд охлаждения.