-
Dalingshan Industrial Guangdong
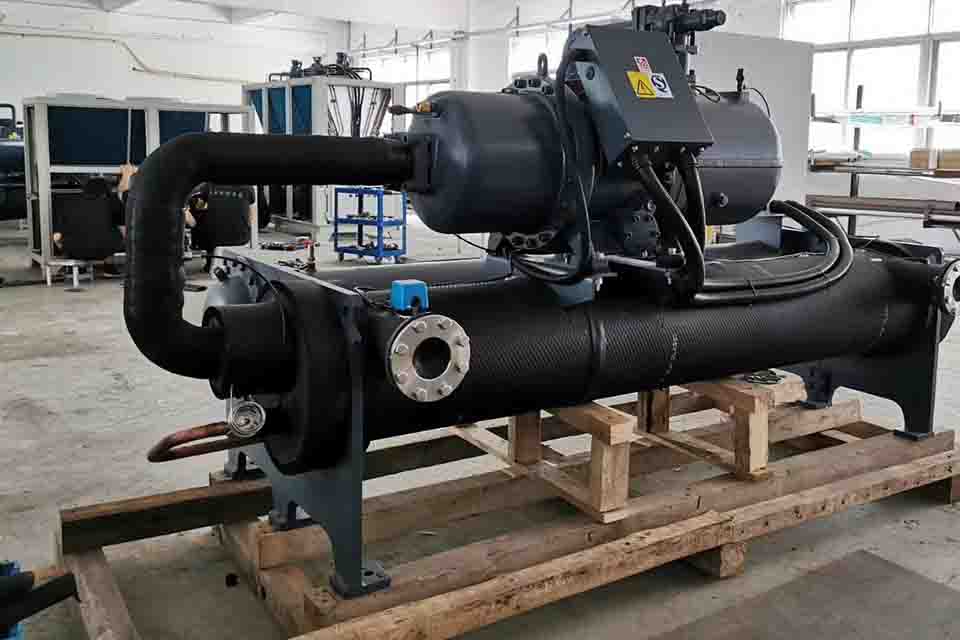
What are the 3 Types of Water-Cooled Condensers Used in Industrial Refrigeration?
Water-Cooled Condensers Used in Industrial Refrigeration
Water-cooled condenser types for industrial refrigeration: working, benefits, and uses.
Índice
What is a Water-Cooled Condenser and How Does It Work?
UM condensador refrigerado a água é um componente crítico em muitos refrigeração systems, particularly in industrial settings. Unlike condensadores refrigerados a ar that use ambient air to cool the refrigerant, water-cooled condensers use water como o resfriamento medium. This tipo de condensador é altamente eficiente because water has a higher capacity to absorb heat than air. In a water-cooled system, hot vapor refrigerante do compressor entra no condensador, where it comes into contact with tubes or plates cooled by water flowing through the system. The transferência de calor process causes the refrigerante para condensar de um vapor back into a liquid.
Condenser work involves removing calor do refrigerante, allowing it to change state. This is essential for the ciclo de refrigeração to continue. The water-cooled condenser unit is typically connected to a torre de resfriamento ou outra fonte de água de resfriamento that helps dissipate the heat from the condenser. This setup makes chillers resfriados a água particularly effective in environments where air cooling is insufficient or where precise temperature control is necessary. Our water-cooled condensers apresentam um highly efficient water-cooled design that ensures optimal performance. We understand that every facility has unique needs, and we’re committed to helping you find the perfect condensador refrigerado a água solução.
What are the Three Primary Types of Water-Cooled Condensers?
Há três tipos principais de condensadores usado em resfriado a água systems: casco e tubo, placa soldada, and coaxial tube-in-tube. Each tipo de condensador offers unique benefits and is suited to different applications. Shell and tube condensers are known for their robustness and ease of maintenance, making them a popular choice in large industrial setups. A brazed plate heat exchanger provides a compact and efficient solution, ideal for applications with space constraints. Coaxial tube-in-tube condensadores, while less common in large-scale operations, are appreciated for their simplicity and effectiveness in smaller systems.
Compreendendo o types of water-cooled systems available is crucial for selecting the right equipment. For example, the three types de water-cooled condensers each cater to specific needs within industrial and commercial applications. Whether you need to cool machinery in a plastics factory or maintain precise temperatures in a laboratory, the right tipo de condensador can significantly impact efficiency and performance. Water-cooled condensers use water from an external source to provide optimal resfriamento, making them a reliable choice for many industries.
How Does a Shell and Tube Condenser Work in Industrial Settings?
O shell and tube condenser is one of the most common types de water-cooled condensers usado em refrigeração industrial. It consists of a concha cilíndrica that houses a bundle of straight water tubes. Hot refrigerant vapor do compressor entra no shell and flows around the outside of the tubes. Cooling water circulates through the water tubes, absorvendo calor do refrigerante. Esse transferência de calor process causes the refrigerante para condensar into a liquid.
In this type of condensador, o water flows in the opposite direction to the refrigerante maximizar heat transfer rate. This counterflow arrangement ensures that the coldest water makes contact with the refrigerante that is about to exit the condensador, enhancing efficiency. Shell and tube condensers are favored in industrial settings due to their ability to handle high pressures and their ease of cleaning. Maintenance often involves removing the end covers to access the water tubes for inspection and cleaning, helping to prevent corrosão and maintain optimal performance. They are commonly used to cool large volumes of refrigerante in applications such as chemical processing and large-scale air conditioning systems.
What are the Advantages of Using a Brazed Plate Heat Exchanger as a Condenser?
UM brazed plate heat exchanger used as a condensador offers a compact and altamente eficiente solution for resfriamento em um sistema de refrigeração. Esse tipo de condensador consists of a series of thin, corrugated plates that are brazed together to create a series of channels. Hot refrigerant e água de resfriamento flow through alternating channels, facilitating rapid transferência de calor. The large surface area provided by the plates, combined with the turbulent flow of the fluids, results in a very efficient transferência de calor processo.
One of the primary advantages of brazed plate condensers is their compact size. They require significantly less space than condensadores de casco e tubo, making them ideal for applications where space is limited, such as in packaged chillers resfriados a água or in retrofitting existing systems. Additionally, brazed plate heat exchangers are known for their high efficiency and ability to operate with smaller temperature differences between the refrigerante e o água de resfriamento. This can lead to lower consumo de água and reduced operating costs. As a manufacturing plant specializing in industrial water chillers, we can incorporate brazed plate heat exchangers into systems designed for industries like plastics, food processing, and laboratories.
Why are Coaxial Tube-in-Tube Condensers Less Common in Large Industrial Applications?
Coaxial tube-in-tube condensadores, também conhecido como shell and coil condensers, are a simpler type of water-cooled condenser. They consist of one tube (the outer tube) with a smaller bobina or tube inside it (the inner tube). Typically, água de resfriamento flows through the inner bobina, enquanto hot refrigerant vapor flows in the space between the inner and outer tube. O transferência de calor occurs through the wall of the inner bobina, causando o refrigerante para condensar.
While coaxial condensadores are efficient and compact, they are less common in large industrial applications for several reasons. One key limitation is their difficulty in cleaning and maintenance. Unlike condensadores de casco e tubo, coaxial condensadores cannot be easily disassembled for cleaning, which can be a significant drawback in applications where water quality is poor or where the refrigerante is prone to causing fouling. Additionally, the transferência de calor capacity of coaxial condensadores is generally lower than that of casco e tubo ou placa soldada options, making them less suitable for high-capacity refrigeração industrial systems. However, they can still be a viable option for smaller, specialized applications where their simplicity and compact size are advantageous. We offer a range of condensador refrigerado a água solutions, including custom designs to fit specific industrial needs.
What Role Does Water Quality Play in the Efficiency of Water-Cooled Condensers?
Water quality is a critical factor in the performance and longevity of any condensador refrigerado a água. Impurities in the água de resfriamento, such as minerals, sediment, and biological growth, can lead to scaling, fouling, and corrosão dentro do condensador. These issues can significantly reduce the transferência de calor efficiency of the system and increase the risk of equipment failure. For example, hard water with high mineral content can cause scale buildup on the water tubes em um shell and tube condenser or the plates in a brazed plate heat exchanger.
To mitigate these problems, it’s essential to use treated or filtered water in resfriado a água systems. Regular monitoring of water quality and implementing appropriate water treatment measures, such as chemical treatments or filtration, can help maintain optimal performance. In some cases, using a torre de resfriamento with a water treatment system can provide a continuous supply of clean água de resfriamento. Proper maintenance, including regular cleaning and inspection of the water side do condensador, is also crucial. Ensuring good water quality not only enhances the efficiency of the processo de resfriamento but also extends the lifespan of the equipment, reducing downtime and maintenance costs.
How to Choose the Right Water-Cooled Condenser for Your Industrial Needs?
Selecionando o apropriado condensador refrigerado a água for your industrial application involves considering several factors. First, assess the heat load of your system to determine the required condensador capacity. This will help you decide between different types of condensers used, como casco e tubo, placa soldada, or coaxial designs. Consider the available space for installation; if space is limited, a compact brazed plate heat exchanger might be preferable.
Water quality is another crucial consideration. If your water source is prone to causing scaling or fouling, a shell and tube condenser, which is easier to clean, might be a better choice. Evaluate the operating temperatures and pressures of your system to ensure the selected condensador can handle these conditions. Additionally, consider the energy efficiency of different condenser types. Brazed plate condensers often offer higher efficiency, which can lead to lower operating costs. In choosing the best option for your needs, it is essential to consider factors such as cooling capacity, flow rate, and pressure requirements.
Here is an image of a Glycol Chiller:
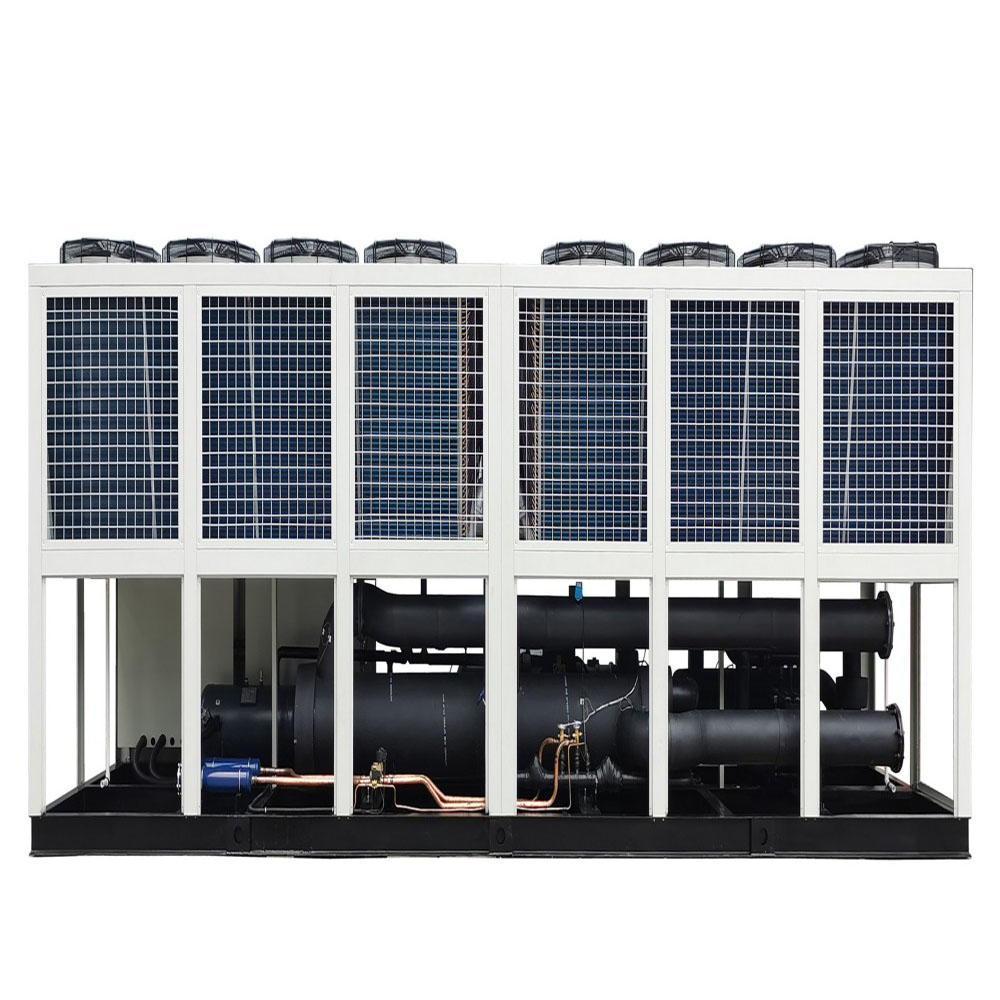
What Maintenance is Required for Water-Cooled Condensers to Ensure Longevity?
Regular maintenance is essential to keep water-cooled condensers operating efficiently and to extend their lifespan. The specific maintenance tasks depend on the tipo de condensador but generally include cleaning, inspecting for leaks, and monitoring water quality. For condensadores de casco e tubo, maintenance often involves removing the end covers to access the water tubes for cleaning. This helps remove any scale or fouling that can reduce transferência de calor eficiência.
Brazed plate heat exchangers typically require less maintenance but should still be inspected regularly for signs of clogging or leakage. Chemical cleaning or backflushing may be necessary to maintain their performance. Monitoring the water quality and implementing appropriate water treatment measures are crucial for all types of water-cooled systems. Regular inspections should also include checking for corrosão and ensuring that all connections are secure. By establishing a proactive maintenance schedule, you can prevent unexpected downtime, reduce repair costs, and ensure your condensador refrigerado a água continues to provide reliable resfriamento for your industrial processes.
Can Water-Cooled Condensers Be Used with a Cooling Tower?
Sim, water-cooled condensers are often used in conjunction with a torre de resfriamento in many industrial applications. A torre de resfriamento is a heat rejection device that removes waste heat from the condenser water and releases it into the atmosphere. In this setup, the water circulating através do condensador absorve calor do refrigerante and then flows to the torre de resfriamento. Dentro do torre de resfriamento, the warm water is sprayed over a fill material, and outdoor air is drawn through the tower, causing some of the water to evaporate.
This evaporative processo de resfriamento reduces the temperature of the remaining water, which is then returned to the condensador to continue the cooling cycle. Using a torre de resfriamento com um condensador refrigerado a água allows for continuous operation and helps maintain optimal resfriamento efficiency. It’s particularly beneficial in applications where large amounts of heat need to be dissipated, such as in chemical plants, power generation, and large air conditioning systems. This combination is highly effective in maintaining consistent temperatures and ensuring efficient operation of the sistema de refrigeração. Check HVAC Chiller Solutions page to learn more about HVAC applications.
What are the Environmental Impacts of Using Water-Cooled Condensers?
Enquanto water-cooled condensers offer high efficiency and are often preferred in industrial settings, they do have environmental implications that need to be considered. One primary concern is consumo de água. Refrigerado a água systems, especially those using once-through resfriamento, can use significant amounts of water. However, systems that incorporate torres de resfriamento can reduce water usage by recirculating and cooling the water.
Another environmental aspect is the potential for thermal pollution. If água de resfriamento is discharged directly into a natural water body at a higher temperature, it can affect aquatic ecosystems. Proper management and treatment of discharge water are essential to mitigate this impact. Additionally, the energy consumption of resfriado a água systems, including the compressor and pumps, contributes to their overall environmental footprint. However, the high efficiency of water-cooled condensers, particularmente placa soldada designs, can lead to lower energy use compared to some refrigerado a ar alternatives.
Perguntas frequentes
What are the main advantages of water-cooled condensers over air-cooled condensers?
Condensadores refrigerados a água offer higher efficiency, especially in high-temperature environments, because water is a more effective resfriamento medium than air. They provide more stable and precise temperature control, which is crucial for many industrial processes. Additionally, resfriado a água systems are generally quieter and can be installed indoors, offering more flexibility in system design.
How often should I clean my water-cooled condenser?
The frequency of cleaning depends on the tipo de condensador and the quality of your água de resfriamento. Shell and tube condensers may require cleaning every 6-12 months, while brazed plate heat exchangers might need less frequent cleaning. Regular monitoring of system performance and water quality can help determine the optimal cleaning schedule. Check Resfriadores anti-explosão page for specific needs.
Can I use any type of water in my water-cooled condenser?
It’s crucial to use treated or filtered water to prevent scaling, fouling, and corrosão. Hard water or water with high levels of impurities can significantly reduce the efficiency and lifespan of your condensador. Implementing a water treatment system, especially when using a torre de resfriamento, can help maintain optimal water quality.
What is the typical lifespan of a water-cooled condenser?
Com a manutenção adequada, um condensador refrigerado a água can last 15-20 years or even longer. The lifespan depends on factors such as the tipo de condensador, operating conditions, water quality, and the quality of maintenance. Regular inspections and timely repairs can help maximize the longevity of your equipment.
Are water-cooled condensers more energy-efficient than air-cooled condensers?
Geralmente sim. Condensadores refrigerados a água, especially those using brazed plate heat exchangers, are often more energy-efficient than refrigerado a ar options. Water’s higher heat capacity allows for more efficient transferência de calor, which can lead to lower energy consumption by the compressor and overall system.
What industries benefit most from using water-cooled condensers?
Many industries that require precise temperature control and high resfriamento capacity benefit from water-cooled condensers. These include plastics and rubber manufacturing, chemical and pharmaceutical processing, food and beverage production, data centers, and large commercial buildings with centralized air conditioning systems. The Resfriadores de leite page provides information on specific uses in the dairy industry.
Conclusão
- Condensadores refrigerados a água are crucial for efficient resfriamento in many industrial applications.
- Há three primary types of water-cooled condensers: casco e tubo, placa soldada, and coaxial tube-in-tube.
- Shell and tube condensers are robust and easy to maintain, suitable for large industrial setups.
- Brazed plate heat exchangers offer compact and altamente eficiente soluções.
- Water quality significantly impacts the performance and lifespan of water-cooled condensers.
- Regular maintenance, including cleaning and water treatment, is essential for optimal operation.
- Condensadores refrigerados a água can be effectively used with torres de resfriamento for continuous resfriamento.
- Enquanto resfriado a água systems have environmental considerations, their efficiency can lead to lower energy consumption compared to some alternatives.
- Escolhendo o caminho certo condensador refrigerado a água involves considering factors like heat load, space availability, water quality, and operating conditions.
- Industries such as plastics, chemicals, food processing, and data centers greatly benefit from using water-cooled condensers.
By understanding these key points, industries can make informed decisions about implementing and maintaining condensador refrigerado a água systems, ensuring efficient and reliable resfriamento for their operations. If you’re ready to optimize your resfriamento system with a condensador refrigerado a água, contact us today to discuss your specific needs and explore our range of solutions! If you are working in textile industry check our Resfriadores industriais para a indústria têxtil page. Here you can find more info about Resfriadores industriais para agricultura.
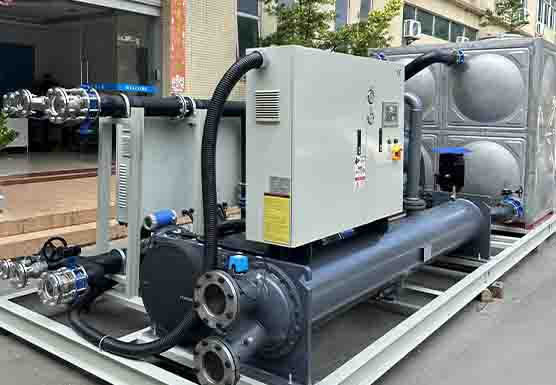