-
Dalingshan Industrial Guangdong
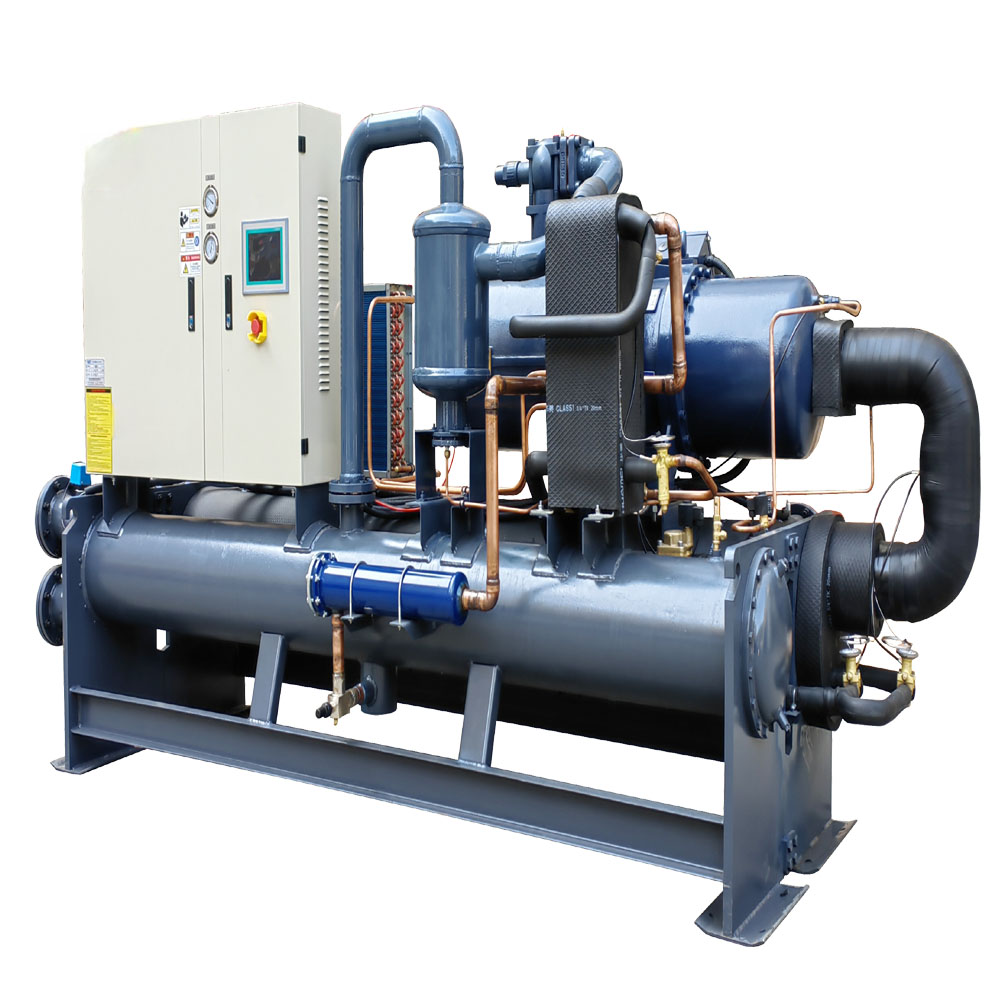
como os lasers são feitos?
Dominando o resfriamento a laser: o guia definitivo para precisão e eficiência
Este artigo aprofunda-se nos aspectos críticos de resfriamento a laser, explorando sua importância em vários setores e fornecendo uma visão geral abrangente de como ele garante o desempenho ideal de tecnologia laser. Do Indústria de Plásticos e Borracha para Centros de Dados, entendimento resfriamento a laser é essencial para manter laser eficiência, precisão e longevidade dos sistemas. Quer você esteja lidando com um laser de diodo no Indústria Eletrônica ou um laser pulsado no Indústria Médica, este guia oferece insights valiosos sobre o gerenciamento calor do laser e reunião específica necessidades de resfriamento.
Índice
O que é resfriamento a laser e por que ele é importante?
Resfriamento a laser é um processo crucial que mantém a eficiência operacional e a longevidade de laser sistemas. Lasersincluindo lasers de diodo e lasers pulsados, geram calor significativo durante a operação. Como especialista em resfriadores de água industriais, vi em primeira mão como o calor excessivo pode degradar o desempenho, reduzir a vida útil e até mesmo danificar componentes sensíveis. Eficaz resfriamento a laser garante que o laser opera dentro de sua faixa de temperatura ideal, preservando a integridade do raio laser e manter a precisão em aplicações como corte a laser.
Resfriamento a laser é vital porque impacta diretamente na estabilidade e confiabilidade do laser sistema. Por exemplo, em corte a laser, um estábulo raio laser é essencial para obter cortes limpos e precisos. Sem o resfriamento adequado, o laserA saída de energia pode flutuar, levando a resultados inconsistentes e danos potenciais ao material que está sendo processado. Indústrias como a Indústria de Plásticos e Borracha dependem fortemente da precisão de corte a laser para a fabricação de componentes complexos. Portanto, manter uma eficiência sistema de resfriamento não se trata apenas de proteger o laser equipamentos, mas também sobre garantir a qualidade do produto final. A importância de resfriamento a laser não pode ser exagerado, pois salvaguarda tanto a laser e o processo de fabricação. Estamos falando sobre manter a precisão e a eficiência, pessoal. É tão crítico!
Como funciona o corte a laser e quais são seus requisitos de resfriamento?
Corte a laser é um processo térmico que utiliza um concentrado raio laser para derreter, vaporizar ou queimar materiais. Esta tecnologia é amplamente utilizado em indústrias como Indústria de Usinagem e Indústria Eletrônica pela sua precisão e versatilidade. O raio laser é direcionado para a superfície do material, onde sua alta densidade de energia cria calor intenso. corte a laser parâmetros do processo, como potência do laser, frequência lasere energia de pulso de laser, são cuidadosamente controlados para atingir o efeito de corte desejado.
O necessidades de resfriamento para corte a laser são significativos devido às altas temperaturas envolvidas. Um robusto sistema de resfriamento é essencial para dissipar o calor gerado durante a corte a laser processo. O sistema de resfriamento normalmente inclui um resfriador a laser que circula o líquido de arrefecimento através do laser sistema, absorvendo e removendo calor. O resfriamento eficaz garante que o laser opera dentro de sua faixa de temperatura ideal, mantendo a estabilidade do raio laser e prevenir danos térmicos ao laser componentes. No Indústria de Plásticos e Borracha, por exemplo, precisão corte a laser depende de consistente potência do laser e qualidade do feixe, que são diretamente influenciados pela eficiência do sistema de resfriamento. Se você já se perguntou por que seu corte a laser os resultados variam, a resposta pode estar apenas no sistema de resfriamento. Sim, é tão importante!
Quais são os diferentes tipos de lasers e suas necessidades específicas de resfriamento?
Existem vários tipos de lasers utilizados em aplicações industriais, cada um com características únicas e necessidades de resfriamento. Lasers de CO2, também conhecido como lasers de dióxido de carbono, são amplamente utilizado para corte a laser, gravação e marcação devido à sua alta potência e eficiência. Lasers de fibra são conhecidos por sua excelente qualidade de feixe e são comumente usados em processamento de materiais e tratamento de superfície a laser. Lasers de diodo são compactos e energeticamente eficientes, o que os torna adequados para uma ampla gama de aplicações, incluindo procedimentos médicos e telecomunicações. Laser excimer é uma forma de laser ultravioleta comumente usada na produção de dispositivos microeletrônicos, circuitos integrados baseados em semicondutores ou “chips”, cirurgia ocular e microusinagem.
Cada tipo de laser tem específico necessidades de resfriamento com base em sua potência de saída, comprimento de onda e características operacionais. Lasers de CO2 normalmente requerem refrigeração a água resfriadores a laser para dissipar a grande quantidade de calor gerada durante a operação. Lasers de fibra geralmente usam sistemas refrigerados a ar ou a água, dependendo do seu nível de potência. Lasers de diodo, com sua menor potência de saída, às vezes podem ser resfriados efetivamente usando apenas resfriamento a ar. No entanto, alta potência lasers de diodo pode exigir resfriamento a água para manter o desempenho ideal. Entendendo o específico necessidades de resfriamento de diferente laser tipos é crucial para selecionar o apropriado sistema de resfriamento e garantir confiabilidade laser operação.
O que é um resfriador a laser e como ele funciona?
UM resfriador a laser é um componente crítico de um laser do sistema sistema de resfriamento. Ele é projetado para remover o calor do laser e manter uma temperatura operacional estável. Resfriadores a laser normalmente usam um sistema de refrigeração para resfriar um fluido circulante, como água ou uma mistura de água e glicol. O fluido resfriado é então bombeado através do laser sistema, absorvendo calor do laser componentes e transportá-los para longe do laser. O fluido aquecido retorna ao resfriador a laser, onde é resfriado novamente antes de ser recirculado. Este processo também é conhecido como ciclos de resfriamento.
Resfriadores a laser são essenciais para manter o desempenho e a longevidade laser sistemas. Eles evitam danos térmicos em componentes sensíveis, como o laser ressonador e óptica, e garantir estabilidade laser saída. A capacidade de um resfriador a laser é determinado por sua capacidade de remover calor, normalmente medida em watts ou BTUs por hora. Escolhendo o certo resfriador a laser para uma aplicação específica depende do laserpotência de saída e a carga de calor gerada durante a operação. A manutenção adequada do resfriador a laser, incluindo limpeza regular e verificações de fluidos, é crucial para garantir sua eficácia e prolongar a vida útil do laser sistema.
Para um resfriamento robusto, recomendamos verificar nosso Chillers centrais de parafuso resfriados a água, perfeito para ambientes de alta demanda. O Chillers centrais de parafuso resfriados a água também é ideal para manter temperaturas ideais.
Quais são as aplicações específicas do laser em vários setores?
Lasers são amplamente utilizado em uma infinidade de indústrias devido à sua precisão, versatilidade e eficiência. No Indústria de Plásticos e Borracha, lasers são usados para cortar, marcar e soldar componentes plásticos com alta precisão. Indústria de Usinagem utiliza lasers para cortar e gravar peças metálicas, enquanto o Indústria de alimentos e bebidas emprega laser tecnologia para marcação e codificação de produtos. No Indústria Química e Farmacêutica, lasers são usados para corte de precisão e marcação de materiais sensíveis, incluindo tratamento de superfície a laser.
O Indústria Eletrônica depende de lasers para micro-usinagem, soldagem e corte de placas de circuito. Indústria Laser ele próprio utiliza lasers no desenvolvimento e produção de laser sistemas e componentes. No Indústria de impressão, lasers são usados para gravar chapas de impressão e marcar vários substratos. Indústria Médica emprega lasers para procedimentos cirúrgicos, diagnósticos e tratamentos terapêuticos. Laboratórios e Instituições de Pesquisa usar lasers para pesquisa científica, espectroscopia e análise de materiais. Centros de Dados utilizar laser tecnologia em sistemas de transmissão e armazenamento de dados de alta velocidade. Cada uma dessas indústrias se beneficia das capacidades únicas de lasers, tornando-os uma ferramenta indispensável na fabricação e tecnologia modernas, incluindo irradiação a laser.
Como gerenciar o calor em processos a laser de forma eficaz?
Gerenciando o calor em laser processos é essencial para manter o desempenho, a confiabilidade e a segurança dos laser sistemas. O calor excessivo pode levar ao estresse térmico, degradação de componentes e até mesmo falha catastrófica. Existem várias estratégias para gerenciar o calor de forma eficaz em laser processos. Uma abordagem é usar um tamanho apropriado resfriador a laser que pode remover calor de forma eficiente laser sistema. O resfriador a laser deve ser selecionado com base no laserpotência de saída e a carga de calor gerada durante a operação.
Outra estratégia é otimizar a laser parâmetros para minimizar a geração de calor. Isso pode envolver o ajuste do potência do laser, frequência lasere energia de pulso de laser para atingir os resultados de processo desejados, reduzindo o calor desnecessário. Ventilação e fluxo de ar adequados ao redor do laser sistema também são essenciais para dissipar o calor. A manutenção regular do sistema de resfriamento, incluindo a limpeza de trocadores de calor e a verificação dos níveis de refrigerante, garante que o sistema opere com eficiência máxima. Monitorando a temperatura do laser sistema e o líquido de arrefecimento fornece um feedback valioso sobre a eficácia das estratégias de gerenciamento de calor. Essas dicas práticas podem ajudar a manter seu laser sistema funcionando suave e eficientemente. É tudo uma questão de ser proativo, não é?
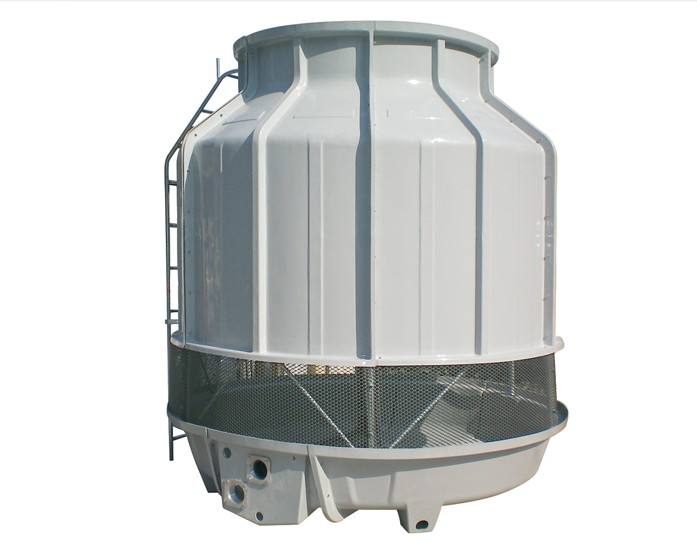
Qual o papel do tubo laser no resfriamento do laser?
O tubo laser é um componente crítico em muitos laser sistemas, particularmente em Lasers de CO2. É onde o laser ação ocorre e gera uma quantidade significativa de calor durante a operação. tubo laser consiste tipicamente em um tubo de vidro ou cerâmica selado preenchido com uma mistura de gases, como dióxido de carbono, nitrogênio e hélio. Quando uma corrente elétrica é aplicada, a mistura de gases é excitada, produzindo luz laser. O necessidades de resfriamento do tubo laser são significativas porque a eficiência do laser ação e a vida útil do tubo laser são diretamente afetados pela temperatura.
Resfriamento eficaz do tubo laser é obtido pela circulação de um refrigerante, normalmente água, ao redor da parte externa do tubo. O refrigerante absorve calor do tubo laser e o leva para um trocador de calor, onde é dissipado. A temperatura do refrigerante é cuidadosamente controlada para manter a temperatura operacional ideal do tubo laser. O resfriamento adequado garante que o tubo laser opera de forma eficiente, produz um ambiente estável raio laser, e tem uma longa vida útil. Manutenção regular do sistema de resfriamento, incluindo a limpeza do tubo laser e verificar a vazão do líquido de arrefecimento é essencial para garantir confiabilidade laser operação.
Compreendendo a fusão de leito de pó a laser e seus desafios de resfriamento
Fusão de leito de pó a laser (LPBF) é um processo de fabricação aditiva que utiliza um laser de alta potência para derreter e fundir seletivamente partículas de pó de metal, camada por camada, para criar objetos tridimensionais. Esta tecnologia é amplamente utilizado em indústrias como aeroespacial, automotiva e médica para produzir peças complexas e de alto desempenho. raio laser é focado em uma fina camada de pó de metal, derretendo as partículas e fundindo-as. À medida que o laser move-se através do leito de pó, ele cria uma camada sólida do objeto que está sendo construído. Este processo é repetido para cada camada sucessiva até que todo o objeto esteja completo.
O necessidades de resfriamento em LPBF são significativos devido às altas temperaturas envolvidas na fusão do pó metálico. O calor intenso gerado pelo laser pode causar estresse térmico, empenamento e até mesmo rachaduras na peça que está sendo construída se não for gerenciado adequadamente. O resfriamento eficaz é essencial para controlar os gradientes térmicos dentro da peça e garantir sua precisão dimensional e integridade mecânica. Várias estratégias de resfriamento são empregadas em LPBF, incluindo o uso de fluxo de gás inerte para remover o calor da câmara de construção, incorporando canais de resfriamento dentro da plataforma de construção e otimizando os parâmetros do processo para minimizar a entrada de calor. O controle cuidadoso do processo de resfriamento é crucial para obter peças de alta qualidade e sem defeitos em LPBF. Para processos de manufatura aditiva como LPBF, nosso Resfriador de parafuso resfriado a ar fornece resfriamento consistente e confiável.
Como otimizar os parâmetros do laser para um resfriamento eficiente?
Otimização laser parâmetros são cruciais para alcançar um resfriamento eficiente e maximizar o desempenho de laser sistemas. A chave laser Os parâmetros que afetam a geração de calor incluem potência do laser, frequência laser, energia de pulso de lasere laser velocidade de varredura. Ao ajustar cuidadosamente esses parâmetros, é possível atingir os resultados de processo desejados, minimizando a entrada de calor. Por exemplo, reduzindo a potência do laser ou aumentando o laser a velocidade de varredura pode diminuir a quantidade de calor depositado no material, reduzindo a carga de resfriamento no sistema.
Além de ajustar o laser parâmetros, otimizar os parâmetros do processo também pode melhorar a eficiência do resfriamento. Isso pode envolver o uso de técnicas como pré-aquecimento do material para reduzir a diferença de temperatura durante laser processamento ou uso de um pulso laser modo para permitir o resfriamento intermitente entre os pulsos. A seleção cuidadosa dos parâmetros do processo, combinada com o monitoramento em tempo real da temperatura e o controle de feedback, pode ajudar a otimizar o laser processo para resfriamento eficiente e resultados de alta qualidade. Se você está procurando melhorar seu laser desempenho do sistema, considere explorar nosso Resfriadores de glicol para controle preciso da temperatura.
Quais são os últimos avanços na tecnologia de resfriamento a laser?
Avanços recentes em resfriamento a laser tecnologia se concentrou em melhorar a eficiência, confiabilidade e precisão dos sistemas de resfriamento para laser aplicações. Uma área de avanço é o desenvolvimento de sistemas mais eficientes e compactos resfriadores a laser que podem fornecer controle preciso de temperatura enquanto consomem menos energia. Esses avançados resfriadores a laser frequentemente incorporam recursos como compressores de velocidade variável, válvulas de expansão eletrônicas e sistemas de controle inteligentes que podem se adaptar a mudanças nas cargas de calor e otimizar o desempenho do resfriamento.
Outra área de avanço é o desenvolvimento de novas técnicas de resfriamento, como Resfriamento Doppler, resfriamento de banda laterale Sísifo esfriando. Essas técnicas usam luz laser para manipular o movimento de átomos ou íons, reduzindo sua energia cinética e efetivamente resfriando-os a temperaturas extremamente baixas. Embora essas técnicas sejam usadas principalmente em pesquisas científicas e aplicações de computação quântica, elas têm o potencial de serem adaptadas para aplicações industriais laser resfriamento no futuro. Além disso, os avanços na ciência dos materiais levaram ao desenvolvimento de novos materiais e projetos de trocadores de calor que podem melhorar a eficiência da transferência de calor e reduzir o tamanho e o peso dos sistemas de resfriamento. Para melhorar ainda mais suas capacidades de resfriamento, o Resfriadores anti-explosão oferece recursos de segurança avançados sem comprometer o desempenho.
Perguntas frequentes
Qual é o principal objetivo do resfriamento a laser?
O principal objetivo de resfriamento a laser é manter a temperatura operacional ideal de laser sistemas, garantindo sua eficiência, estabilidade e longevidade. Previne danos térmicos e mantém a qualidade do raio laser.
Como funciona um resfriador a laser?
UM resfriador a laser funciona circulando um refrigerante através do laser sistema para absorver calor. O refrigerante aquecido é então resfriado no chiller usando um sistema de refrigeração e recirculado, fornecendo resfriamento contínuo.
Quais são os tipos comuns de lasers usados nas indústrias?
Comum tipos de lasers usado em indústrias incluem Lasers de CO2, lasers de fibra, lasers de diodoe laser excimer. Cada tipo tem características e requisitos de resfriamento exclusivos.
Por que o resfriamento é importante no corte a laser?
O resfriamento é importante em corte a laser porque evita danos térmicos ao material e à laser sistema, garante consistência potência do laser e qualidade do feixe, e mantém a precisão do processo de corte.
Quais são os principais fatores na escolha de um resfriador a laser?
Os principais fatores na escolha de um resfriador a laser incluir o laserpotência de saída, a carga de calor gerada durante a operação, a estabilidade de temperatura necessária e a eficiência do resfriador.
Como posso otimizar meus parâmetros de laser para melhor resfriamento?
Você pode otimizar seu laser parâmetros ajustando o potência do laser, frequência lasere energia de pulso de laser para minimizar a geração de calor enquanto se alcança os resultados desejados. Além disso, otimizar parâmetros de processo e usar monitoramento de temperatura em tempo real pode melhorar a eficiência do resfriamento.
Conclusão
- Resfriamento a laser é essencial para manter o desempenho e a longevidade do laser sistemas.
- Diferentes tipos de lasers, como Lasers de CO2, lasers de fibrae lasers de diodo, têm requisitos de resfriamento exclusivos.
- Resfriadores a laser desempenham um papel crucial na remoção de calor e na manutenção de temperaturas operacionais estáveis.
- Estratégias eficazes de gestão do calor incluem o uso de aquecedores de tamanho apropriado resfriadores a laser, otimizando laser parâmetros e garantindo ventilação adequada.
- O tubo laser requer resfriamento cuidadoso para manter sua eficiência e vida útil.
- Fusão de leito de pó a laser apresenta desafios de resfriamento únicos que exigem técnicas de resfriamento especializadas.
- Avanços em resfriamento a laser a tecnologia continua a melhorar a eficiência e a precisão dos sistemas de resfriamento.
- Indústrias que vão desde Plásticos e Borracha para Centros de Dados confiar em eficaz resfriamento a laser para desempenho ideal.
- Para explorar mais sobre como nossos produtos podem atender às suas necessidades específicas, visite nossa página em Resfriadores industriais para a indústria têxtil.
- Para quem atua no setor de alimentos e bebidas, nossa Resfriadores de glicol industriais para cervejarias são projetados para fornecer soluções de resfriamento ideais.
- Manutenção e monitoramento adequados de laser Os sistemas de refrigeração são cruciais para garantir a sua eficácia e a longevidade laser equipamento.
Espero que este guia abrangente tenha esclarecido os meandros de resfriamento a laser e seu papel fundamental em várias aplicações industriais. Caso tenha mais alguma dúvida ou precise de soluções personalizadas, não hesite em entrar em contato. Seu sucesso é nossa prioridade, e estamos aqui para apoiá-lo em cada etapa do caminho.
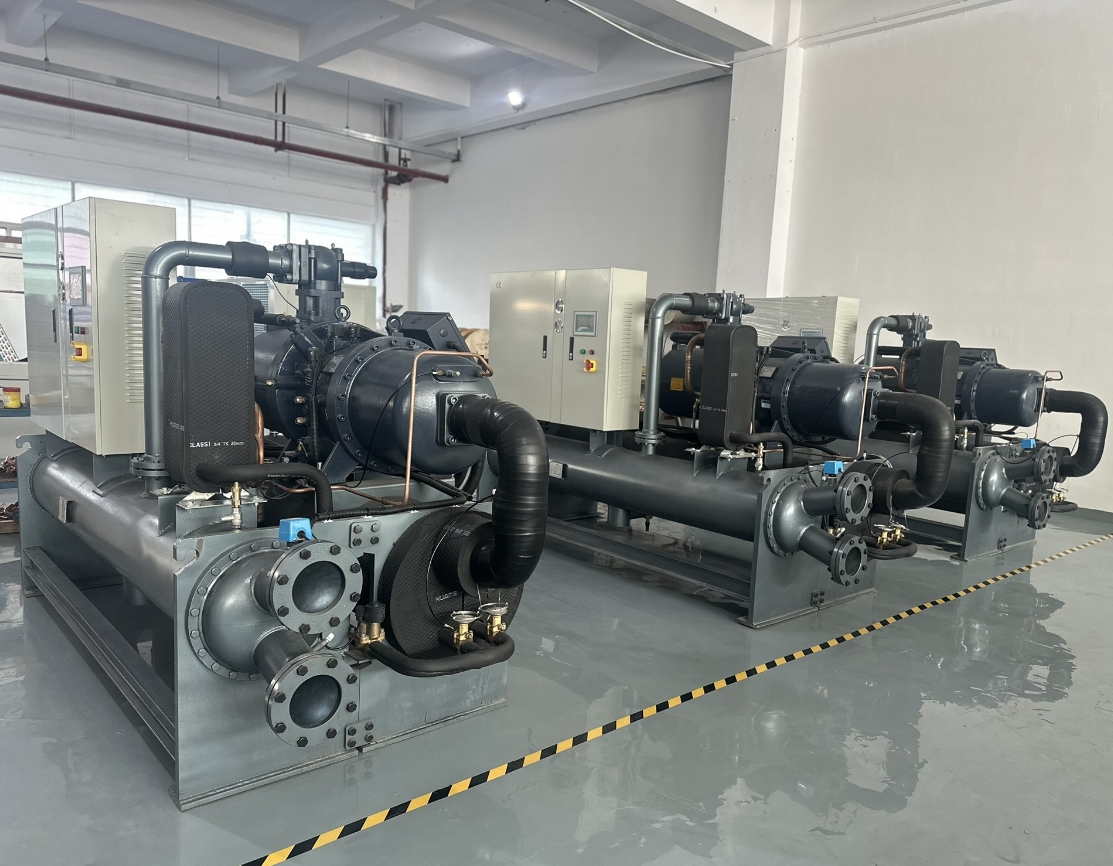