-
Dalingshan Industrial Guangdong
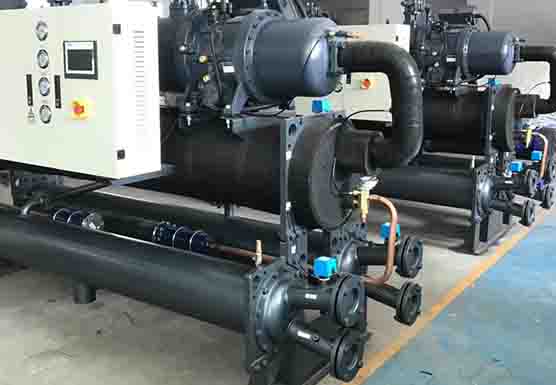
diferentes tipos de chillers para uso industrial e comercial
Comparando diferentes tipos de resfriadores para sistemas HVAC industriais e comerciais
Este artigo se aprofunda nos vários tipos de resfriadores usado em industrial e configurações comerciais. Exploraremos seus princípios operacionais, vantagens e desvantagens, fornecendo a você o conhecimento para tomar uma decisão informada ao selecionar o certo tipo de resfriador para suas necessidades específicas. Como profissional na área Industrial Refrigerador de água Setor de manufatura, vi em primeira mão o quão crucial é entender essas diferenças. Quer você esteja na indústria de plásticos e borracha, indústria de usinagem ou qualquer um dos vários setores que atendemos, este artigo esclarecerá por que uma compreensão completa de resfriador a tecnologia é essencial e como nossas soluções personalizadas podem atender às suas necessidades refrigeração industrial demandas, garantindo eficiência operacional e qualidade do produto. Essas informações o guiarão para fazer a melhor escolha para seu negócio, levando-o a aprender mais e, finalmente, encorajando-o a buscar uma consultoria personalizada.
Índice
1. Quais são os principais tipos de chillers?
Resfriadores são componentes essenciais em muitos industrial e ambientes comerciais, proporcionando legalpara processos e controle climático. Em termos gerais, resfriadores são classificados em duas categorias principais: resfriadores de compressão de vapor e resfriadores de absorção de vapor. Resfriadores de compressão de vapor use um mecanismo mecânico acionado eletricamente compressor para forçar o refrigerante em torno do sistema, enquanto resfriadores de absorção use uma fonte de calor para conduzir o resfriamento processo. Dentro do compressão de vapor categoria, existem quatro tipos principais: resfriadores de rolagem, resfriadores de parafuso, resfriadores centrífugos, e recíproco resfriadores. Como especialista nesta área, ajudei inúmeras empresas nos setores de alimentos e bebidas, produtos químicos e farmacêuticos, entre outros, a selecionar o tipo certo para suas necessidades específicas.
Cada resfriador tipo tem características únicas, tornando-o adequado para aplicações específicas. Por exemplo, resfriadores de rolagem são frequentemente preferidos em aplicações de pequeno a médio porte devido à sua eficiência energética e operação silenciosa. Em contraste, resfriadores centrífugos são ideais para grandes projetos Sistemas HVAC em edifícios comerciais e instalações industriais. Para nossos clientes na Indústria Médica e Laboratórios e Instituições de Pesquisa, escolher o certo resfriador é vital para manter condições ambientais precisas. Entender as diferenças entre esses tipos de resfriadores pode impactar significativamente sua eficiência operacional e seus resultados financeiros.
2. Como funciona um sistema de resfriamento a água?
Chillers resfriados a água usar água de um torre de resfriamento ou outro água fonte para remover calor do refrigerante. Esses resfriadores são altamente eficientes na transferência de calor, tornando-os ideais para processos industriais que requerem grandes quantidades de legaling. Na minha experiência de fabricação resfriadores de água, Eu vi como eles efetivamente mantêm temperaturas consistentes para clientes, particularmente aqueles na Indústria de Plásticos e Borracha e na Indústria Eletrônica. Um típico sistema de refrigeração a água consiste em um evaporador, compressor, condensador e válvula de expansão.
O processo começa com o refrigerante absorvendo calor no evaporador, transformando-o em um gás de baixa pressão. O compressor então aumenta a pressão e a temperatura do refrigerante gás, que então flui para o condensador. No condensador, água esfria o refrigerante, fazendo com que ele se condense novamente em um líquido, liberando o calor absorvido. O líquido de alta pressão refrigerante então passa pela válvula de expansão, que reduz sua pressão e temperatura, preparando-a para iniciar o ciclo novamente. Para obter informações mais detalhadas sobre a tecnologia de resfriamento a água, você pode explorar nosso Resfriador de água Scroll resfriado a água página. Chillers resfriados a água são geralmente mais eficientes em termos energéticos do que refrigerado a ar sistemas, especialmente em climas quentes, onde o ar ambiente a temperatura está alta.
3. O que é um chiller industrial resfriado a ar e quando ele é ideal?
Chillers resfriados a ar usar ar ambiente para remover o calor do refrigerante. Esses resfriadores são mais simples em design em comparação com chillers resfriados a água, pois não requerem uma torre de resfriamento ou um separado água fonte. A simplicidade os torna mais fáceis de instalar e manter, o que é uma vantagem significativa para muitos de nossos clientes na indústria de impressão e indústria de laser. Um refrigerador industrial refrigerado a ar consiste em um evaporador, um compressor, um condensador e uma válvula de expansão, semelhante a uma resfriado a água sistema. No entanto, em vez de usar água para legal o refrigerante no condensador, chillers resfriados a ar use ventiladores para soprar ar através das serpentinas do condensador.
Este tipo de resfriador é ideal para aplicações onde água a disponibilidade é limitada ou quando um torre de resfriamento não é viável. É importante notar que chillers resfriados a ar podem ser menos eficientes em climas muito quentes, pois seu desempenho é diretamente afetado pela ar ambiente temperatura. Chillers resfriados a ar pegar ar do seu entorno, legal e usá-lo para operar máquinas ou manter uma temperatura confortável. Ao usar este tipo de resfriador, é necessário forçar ar através dos tubos expostos para manter uma temperatura adequada. Um ótimo exemplo disso são nossos Chillers de parafuso resfriados a ar.
4. Quais são as vantagens dos resfriadores centrífugos em grandes sistemas HVAC?
Chillers centrífugos são comumente usados em grandes projetos comerciais e industrial aplicações devido à sua alta eficiência e capacidade de lidar com grandes cargas de resfriamento. Estes resfriadores usar um compressor centrífugo para comprimir o refrigerante, permitindo-lhes atingir altos níveis de legaling. Como alguém que trabalhou extensivamente nesta área, descobri que resfriadores centrífugos são particularmente adequados para grandes Sistemas HVAC em edifícios de escritórios, hospitais e outras grandes instalações. Os principais componentes de um resfriador centrífugo inclui um evaporador, um compressor centrífugo, um condensador e uma válvula de expansão.
Uma das principais vantagens de resfriadores centrífugos é a sua capacidade de operar eficientemente em condições de carga parcial, o que é crucial para aplicações com variações legalrequisitos de desempenho. Para nossos clientes do setor de Data Centers, essa eficiência é vital. Chillers centrífugos também tendem a ter uma vida útil mais longa em comparação com outros tipos de resfriadores, oferecendo um melhor retorno sobre o investimento ao longo do tempo. Além disso, resfriadores centrífugos usar refrigerantes que têm baixo potencial de aquecimento global, o que os torna uma opção mais ecológica.
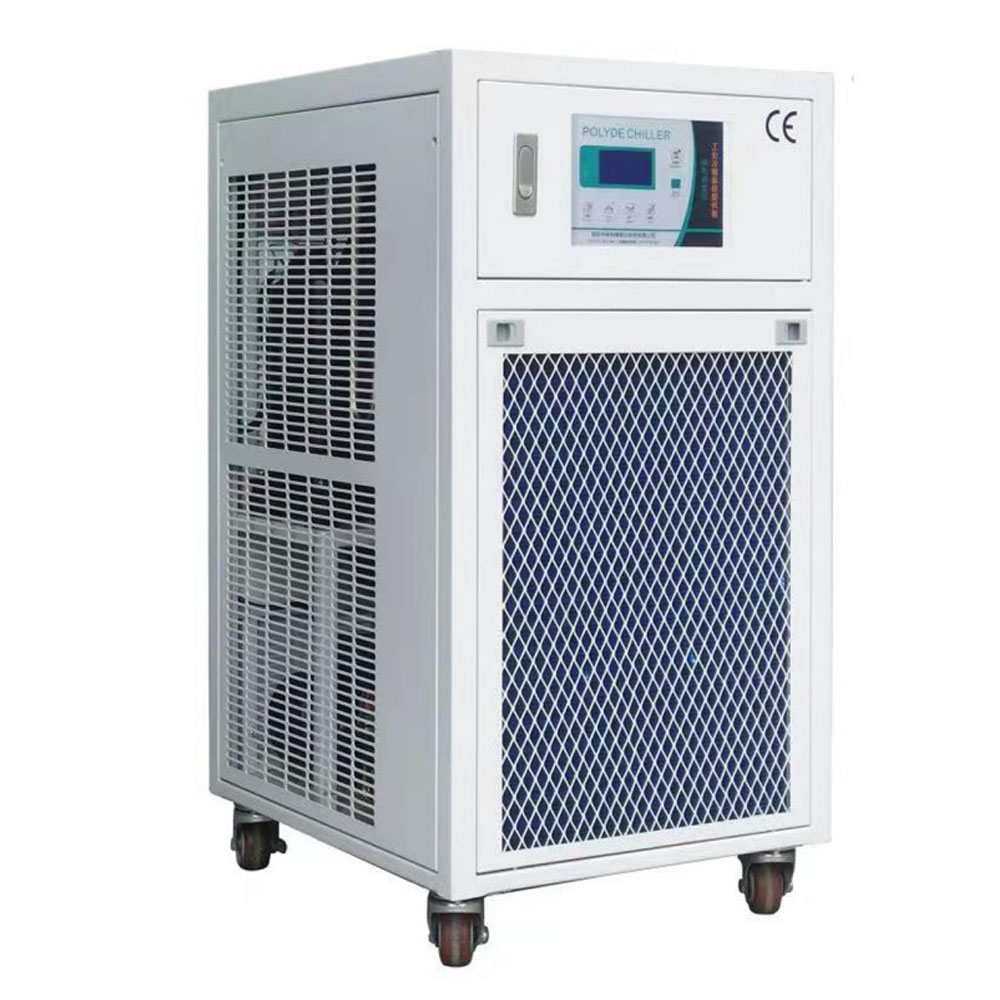
5. Por que escolher resfriadores de parafuso para aplicações industriais?
Resfriadores de parafuso são amplamente utilizados em uma variedade de industrial aplicações devido ao seu design robusto, eficiência e confiabilidade. Estes resfriadores usar um compressor de parafuso para comprimir o refrigerante, proporcionando controle preciso de temperatura e desempenho consistente. Da minha experiência na indústria Refrigerador de água Indústria de transformação, resfriadores de parafuso são uma excelente escolha para indústrias como a de Usinagem e a Química e Farmacêutica, onde as ferramentas de usinagem são estáveis e precisas. legalé crucial.
Os principais componentes de um resfriador de parafuso são semelhantes a outros resfriadores de compressão de vapor, incluindo um evaporador, um compressor de parafuso, um condensador e uma válvula de expansão. O compressor de parafuso é o coração do sistema, comprimindo o refrigerante gás a alta pressão e temperatura. Resfriadores de parafuso usar um compressor de parafuso para criar um legalefeito de ing. Resfriadores de parafuso são mais eficientes do que outros tipos de resfriadores, tornando-os ideais para industrial configurações.
Um dos principais benefícios de resfriadores de parafuso é sua capacidade de lidar com cargas variáveis de forma eficiente. Eles podem operar em uma ampla gama de capacidades, tornando-os adequados para aplicações com flutuação legalnecessidades. Além disso, resfriadores de parafuso geralmente requerem menos manutenção do que outros resfriador tipos, resultando em menores custos operacionais. Para ver como nosso resfriadores de parafuso pode beneficiar suas operações, confira nosso Resfriador de água de parafuso resfriado a água página.
6. Como os chillers scroll beneficiam ambientes comerciais e industriais?
Resfriadores de rolagem são conhecidos por sua eficiência energética, operação silenciosa e design compacto. Estes resfriadores usar um compressor de rolagem, que tem menos peças móveis do que outros tipos de compressores, levando a um desgaste reduzido e maior confiabilidade. Isso os torna uma escolha popular para uso comercial e industrial configurações.
Resfriadores de rolagem consistem tipicamente em um evaporador, um compressor de rolagem, um condensador e uma válvula de expansão. O compressor de rolagem comprime o refrigerante usando dois scrolls interligados, um estacionário e um orbital. Este design resulta em compressão suave e contínua, minimizando ruído e vibração.
Resfriadores de rolagem são particularmente adequados para aplicações que exigem controle preciso de temperatura e operação silenciosa, como hospitais, laboratórios e prédios de escritórios. Para a indústria médica, a confiabilidade de resfriadores de rolagem é primordial. Eles também são uma boa escolha para empresas de pequeno e médio porte industrial processos que necessitam de confiabilidade legalindo. Resfriadores de rolagem usar compressores scroll, que são conhecidos por sua operação silenciosa.
7. Qual é o mecanismo dos chillers de absorção de vapor?
Resfriadores de absorção de vapor use uma fonte de calor, como vapor ou água quente água, para conduzir o legalprocesso de fabricação, em vez de um processo mecânico acionado eletricamente compressor. Isso os torna uma opção atraente para aplicações onde o calor residual está disponível ou onde os custos de eletricidade são altos. Como fabricante, tenho visto um interesse crescente em resfriadores de absorção de indústrias que buscam melhorar sua eficiência energética e reduzir sua pegada de carbono.
Os componentes básicos de um resfriador de absorção de vapor incluem um evaporador, um absorvedor, um gerador e um condensador. O processo começa com o refrigerante, tipicamente água, evaporando no evaporador a baixa pressão, absorvendo calor e fornecendo legaling. O refrigerante o vapor é então absorvido por uma solução, geralmente brometo de lítio, no absorvedor. Esta solução é bombeada para o gerador, onde a fonte de calor é aplicada, separando o refrigerante da solução absorvente. O refrigerante o vapor então flui para o condensador, onde é legalcondensado de volta em um líquido, liberando o calor absorvido. Finalmente, o líquido refrigerante retorna ao evaporador para iniciar o ciclo novamente.
Resfriadores de absorção de vapor são geralmente menos eficientes do que resfriadores de compressão de vapor em termos de seu coeficiente de desempenho (COP). No entanto, eles podem ser mais econômicos quando o calor residual é utilizado. Este tipo de resfriador é frequentemente usado em sistemas de cogeração, onde o calor residual da geração de eletricidade é usado para alimentar o resfriador. Nossa página em Resfriadores anti-explosão pode fornecer mais informações sobre assuntos especializados resfriador aplicações.
8. Escolhendo o Chiller Certo: Principais Considerações
Selecionando o refrigerador certo para sua aplicação específica requer consideração cuidadosa de vários fatores. O primeiro passo é determinar o legalcarga de aquecimento, que é a quantidade de calor que precisa ser removida. Isso dependerá do tamanho do espaço ou da natureza do industrial processo. O legala carga influenciará a capacidade do resfriador obrigatório.
Outra consideração importante é o ambiente operacional. Por exemplo, se o resfriador será instalado em um clima quente, um refrigerador refrigerado a água pode ser mais eficiente do que um refrigerado a ar um. Por outro lado, se água a disponibilidade é uma preocupação, uma refrigerador refrigerado a ar pode ser a melhor escolha.
A eficiência energética também é um fator crucial. Resfriadores pode consumir uma quantidade significativa de energia, por isso é importante escolher um resfriador que é energeticamente eficiente e tem um COP alto. Para muitos dos nossos clientes, particularmente na Indústria de Alimentos e Bebidas, os custos de energia são uma grande preocupação. Em geral, chillers resfriados a água são mais eficientes do que chillers resfriados a ar, mas a eficiência específica dependerá da resfriador tipo e condições de operação.
Os requisitos de manutenção também devem ser levados em consideração. Alguns resfriadores, como resfriadores de rolagem, têm menos peças móveis e exigem menos manutenção do que outros. Isso pode resultar em menores custos operacionais ao longo da vida útil do resfriador.
9. Como os chillers garantem o desempenho ideal em operações industriais?
Resfriadores desempenham um papel fundamental na manutenção do desempenho ideal em muitos industrial operações. Elas garantem que os processos operem dentro da faixa de temperatura necessária, evitando o superaquecimento e garantindo a qualidade do produto. Por exemplo, na Indústria de Plásticos e Borracha, resfriadores estão acostumados a legal moldes e produtos extrudados, garantindo que eles solidifiquem corretamente e mantenham sua forma.
Na indústria de usinagem, resfriadores estão acostumados a legal ferramentas de corte e peças de trabalho, prevenindo danos térmicos e prolongando a vida útil da ferramenta. Para a Indústria Química e Farmacêutica, resfriadores manter temperaturas precisas durante reações químicas e armazenamento, garantindo a segurança e eficácia do produto. Resfriadores transferir calor de um processo para outro meio, como água ou ar. Resfriadores ajudar a evitar o superaquecimento das máquinas.
Resfriadores também são utilizados na indústria de alimentos e bebidas para legal produtos durante o processamento e armazenamento, preservando seu frescor e estendendo sua vida útil. Por exemplo, resfriadores são usados em cervejarias para legal mosto durante a fermentação e em laticínios para legal leite após pasteurização. Você pode encontrar mais informações em nosso Resfriadores de leite página.
10. Quais são os requisitos de manutenção para diferentes tipos de resfriadores?
A manutenção regular é essencial para garantir a operação confiável e a longevidade de qualquer resfriador sistema. Os requisitos específicos de manutenção variam dependendo do tipo de refrigerador e as condições de operação. No entanto, existem algumas tarefas gerais de manutenção que se aplicam a todos resfriadores.
Uma das tarefas de manutenção mais importantes é manter o refrigerador bobinas limpas. Bobinas sujas podem reduzir a refrigerador eficiência e aumentar o consumo de energia. Para chillers resfriados a ar, isso significa limpar regularmente as serpentinas do condensador para remover poeira e detritos. Para chillers resfriados a água, significa limpar os tubos do condensador para evitar incrustações e sujeira.
Refrigerante Os níveis também devem ser verificados regularmente. Baixo refrigerante os níveis podem reduzir o refrigerador legalcapacidade de carga e aumentar o consumo de energia. Se um vazamento for detectado, ele deve ser reparado imediatamente para evitar mais refrigerante perdas e danos potenciais ao compressor. Resfriadores requerem manutenção regular para continuar funcionando sem problemas.
O compressor é o coração do resfriador sistema, e deve ser inspecionado regularmente para sinais de desgaste ou danos. Para parafuso e resfriadores centrífugos, o compressor o óleo deve ser verificado e trocado periodicamente. Resfriadores de rolagem usar compressores scroll que requerem menos manutenção em comparação com outros tipos de resfriadores.
Para chillers resfriados a água, o torre de resfriamento ou água fonte também deve ser mantida. Isso inclui tratar o água para evitar a corrosão e o crescimento biológico, que podem afetar o refrigerador desempenho.
Perguntas frequentes
Qual é a diferença entre um chiller resfriado a ar e um resfriado a água?
Chillers resfriados a ar usar ar ambiente para remover o calor do refrigerante, enquanto chillers resfriados a água usar água de um torre de resfriamento ou outro água fonte. Chillers resfriados a água são geralmente mais eficientes, especialmente em climas quentes, mas requerem um água fonte e instalação mais complexa.
Que tipo de resfriador é melhor para grandes aplicações industriais?
Chillers centrífugos e resfriadores de parafuso são frequentemente as melhores escolhas para grandes industrial aplicações devido à sua alta capacidade, eficiência e capacidade de lidar com cargas variadas.
Com que frequência um refrigerador deve passar por manutenção?
UM resfriador deve ser reparado pelo menos uma vez por ano para garantir desempenho e longevidade ideais. No entanto, o intervalo de manutenção específico pode variar dependendo do tipo de refrigerador, as condições de operação e as recomendações do fabricante.
Os chillers de absorção podem ser usados em aplicações industriais?
Sim, resfriadores de absorção pode ser usado em industrial aplicações, particularmente onde há calor residual disponível. Eles são uma boa opção para melhorar a eficiência energética e reduzir custos operacionais em tais cenários.
Quais são as vantagens de usar um chiller scroll?
Resfriadores de rolagem oferecem várias vantagens, incluindo alta eficiência energética, operação silenciosa, design compacto e manutenção reduzida devido a menos peças móveis. Eles são adequados para uso comercial e industrial aplicações que exigem controle preciso da temperatura.
Como determino o tamanho certo do refrigerador para minhas necessidades?
Determinando o certo tamanho resfriador envolve o cálculo do legalcarga de aquecimento, que é a quantidade de calor que precisa ser removida. Fatores como o tamanho do espaço, o tipo de equipamento e a industrial processo influenciará o legalcarga. Consultando com um resfriador Um especialista pode ajudar a garantir que você selecione o tamanho apropriado para sua aplicação específica.
Resumo
- Resfriadores são essenciais para legalem vários industrial e aplicações comerciais.
- Existem dois tipos principais de resfriadores: compressão de vapor e absorção de vapor.
- Resfriadores de compressão de vapor incluir rolar, parafuso, centrífuga, e tipos recíprocos.
- Chillers resfriados a água usar água para remover calor e são geralmente mais eficientes do que refrigerado a ar modelos.
- Chillers resfriados a ar usar ar ambiente e são mais simples de instalar e manter.
- Chillers centrífugos são ideais para grandes Climatização sistemas devido à sua alta capacidade e eficiência.
- Resfriadores de parafuso são robustos e confiáveis, adequados para diversas industrial aplicações.
- Resfriadores de rolagem são energeticamente eficientes e operam silenciosamente, o que os torna ideais para aplicações que exigem controle preciso da temperatura.
- Chillers de absorção usam uma fonte de calor em vez de eletricidade, o que os torna mais econômicos quando há calor residual disponível.
- Escolhendo o refrigerador certo depende de fatores como legalcarga, ambiente operacional, eficiência energética e requisitos de manutenção.
- Manutenção regular, incluindo limpeza de bobinas, verificação refrigerante níveis e inspecionando o compressor, é crucial para resfriador longevidade e desempenho.
- Resfriadores desempenham um papel vital para garantir o desempenho ideal em industrial operações mantendo as temperaturas necessárias e evitando o superaquecimento.
- Compreendendo os diferentes tipos de resfriadores e suas aplicações podem ajudar você a tomar uma decisão informada e melhorar sua eficiência operacional. Nossa gama diversificada de resfriadores garante que podemos atender às necessidades exclusivas de indústrias que vão de plásticos e borracha a data centers.
- Se você precisa de um novo resfriador sistema, ou precisa substituir um antigo, por favor Contate-nos hoje para mais informações!
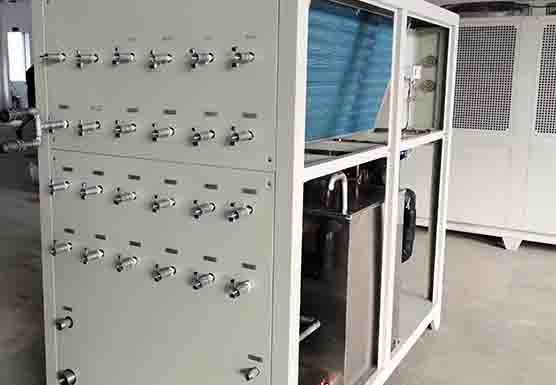