-
Dalingshan Industrial Guangdong
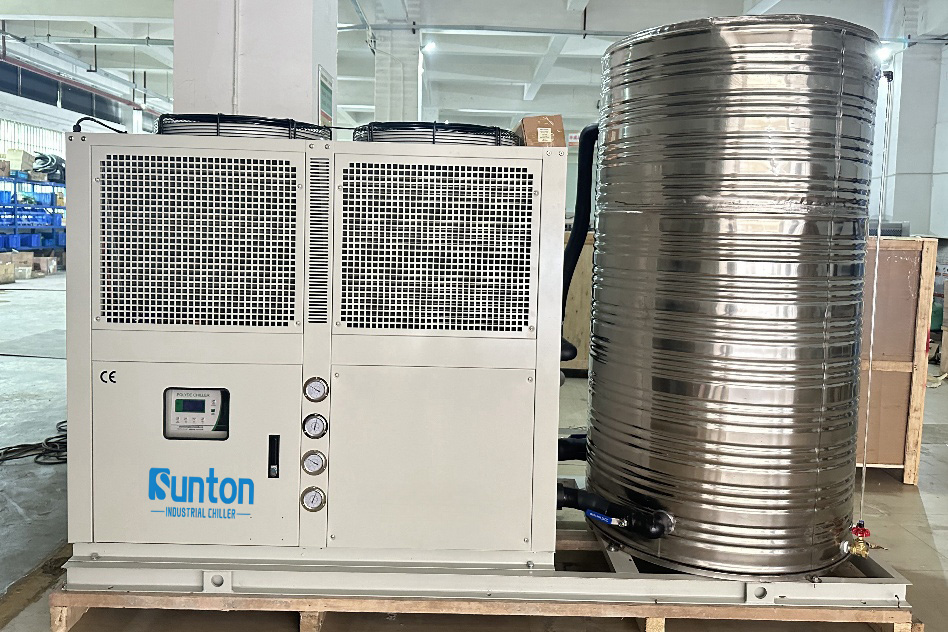
diferenças entre chiller resfriado a ar e chiller resfriado a água
Chillers resfriados a ar ou a água: qual é o ideal para suas necessidades industriais?
Este artigo se aprofunda no mundo dos chillers industriais, comparando refrigerado a ar e resfriado a água sistemas para ajudar você a tomar uma decisão informada para sua aplicação específica. Quer você esteja no setor de plásticos, alimentos, produtos químicos ou qualquer outra indústria que exija controle preciso de temperatura, entender as nuances entre esses dois tipos de resfriadores é crucial. Como um especialista experiente em resfriador de água industrial fabricação, vi em primeira mão como escolher o certo resfriador pode impactar significativamente a eficiência, os custos e o sucesso operacional geral. Vale a pena ler este artigo porque ele oferece meus insights pessoais com base em anos de experiência, ajudando você a evitar armadilhas comuns e a tomar uma decisão que se alinhe com seus objetivos de longo prazo.
Índice
O que é um resfriador e por que ele é essencial para o seu setor?
UM resfriador é uma máquina que remove calor de um líquido por meio de um ciclo de refrigeração por compressão de vapor ou absorção. Este líquido resfriado pode então ser circulado por um trocador de calor para legal equipamento, ou outro fluxo de processo (como ar ou água de processo). Como um fabricante experiente de produtos industriais resfriadores de água, posso dizer que eles são a espinha dorsal de muitos processos industriais. Indústrias como plásticos e borracha, usinagem, alimentos e bebidas, química e farmacêutica, eletrônica, laser, impressão, médica, laboratórios e instituições de pesquisa e data centers dependem fortemente do controle preciso de temperatura que resfriadores fornecer.
Por exemplo, na indústria de plásticos, resfriadores estão acostumados a legal o plástico quente que é injetado em um molde. Rápido resfriamento garante a consistência do produto e reduz os tempos de ciclo, impactando diretamente a produtividade. Da mesma forma, na indústria de alimentos e bebidas, resfriadores são vitais para manter a qualidade e a segurança dos produtos, como em nossos Resfriadores de leite. Sem confiável resfriamento, os processos podem ser interrompidos, levando a perdas financeiras significativas e potenciais riscos à segurança.
Como funcionam os chillers? Compreendendo os princípios básicos
Os refrigeradores funcionam usando um sistema de refrigeração para transferir calor. O princípio básico envolve um refrigerante que passa por diferentes estados (líquido e gás) para absorver e liberar calor. Existem dois tipos principais de resfriadores: refrigerado a ar e resfriado a água. O diferença entre chillers resfriados a água e resfriados a ar reside na forma como dissipam o calor absorvido pelo refrigerante.
Em termos simples, um resfriador opera em um loop contínuo. O refrigerante absorve calor da água do processo (ou água gelada), o que reduz a temperatura da água. O calor carregado refrigerante então viaja para o condensador, onde o calor é liberado para o ambiente ar ambiente (refrigerador refrigerado a ar) ou para um separado água fonte como uma torre de resfriamento (refrigerador refrigerado a água). Este processo se repete, garantindo um fornecimento consistente de água gelada para aplicações industriais. Nossos chillers, como o Chillers centrais de parafuso resfriados a água, exemplificam a transferência eficiente de calor em ação.
Quais são os principais componentes de um sistema de resfriamento?
Um típico sistema de resfriamento compreende várias chaves componentes do refrigerador: o compressor, condensador, válvula de expansão e evaporador. O compressor é o coração do sistema, bombeando o refrigerante ao longo do resfriador. O condensador é onde o calor é rejeitado, e pode ser refrigerado a ar ou resfriado a água. A válvula de expansão regula o fluxo de refrigerante, enquanto o evaporador é onde o refrigerante absorve calor da água do processo, portanto resfriamento isto.
Além desses componentes primários, resfriador os sistemas podem incluir bombas, controles e outros acessórios. Por exemplo, resfriado a água sistemas muitas vezes requerem torres de resfriamento e bombas de água do condensador para circular o resfriamento água. Compreendendo estes componentes do refrigerador é essencial compreender as diferenças entre chillers resfriados a ar e chillers resfriados a água. Cada parte desempenha um papel vital na eficiência e desempenho geral do resfriador.
Mergulho profundo em resfriadores resfriados a água: características, vantagens e considerações
Chillers resfriados a água são conhecidos por sua alta eficiência, especialmente em aplicações que exigem maiores capacidades de resfriamento. Eles usam um fonte de água, como um torre de resfriamento ou um dedicado água loop, para dissipar o calor do refrigerante. O água absorve o calor e depois é resfriado no torre de resfriamento antes de ser devolvido ao resfriador. Pela minha experiência, Os resfriadores refrigerados a água são normalmente mais eficiente em termos energéticos do que refrigerado a ar homólogos, especialmente em climas mais quentes.
Vantagens dos Chillers Resfriados a Água:
- Maior eficiência: Chillers resfriados a água geralmente têm um coeficiente de desempenho (COP) mais alto em comparação com refrigerado a ar unidades.
- Operação estável: Eles são menos afetados pelas flutuações de ar ambiente temperatura.
- Operação mais silenciosa: A ausência de grandes ventiladores os torna mais silenciosos do que chillers resfriados a ar.
- Maior vida útil: Com a manutenção adequada, chillers resfriados a água pode ter uma vida operacional mais longa.
Considerações sobre resfriadores resfriados a água:
- Disponibilidade de água: Eles exigem um confiável fonte de água e pode não ser adequado onde a água é escassa.
- Tratamento de água: Regular tratamento de água é necessário para evitar incrustações, corrosão e crescimento biológico.
- Custo inicial: O custo inicial pode ser maior devido à necessidade de um torre de resfriamento e tubulação associada.
- Custo de manutenção: Embora eficiente, o custo de manutenção pode ser maior devido a tratamento de água e torre de resfriamento manutenção.
- Maior capacidade de resfriamento.
Nosso Resfriador de água Scroll resfriado a água destaca as capacidades de resfriamento eficientes desta tecnologia.
Explorando resfriadores refrigerados a ar: como eles se comparam?
Chillers resfriados a ar, por outro lado, use ar ambiente para legal o refrigerante. Eles empregam grandes ventiladores para soprar ar sobre tubos contendo o refrigerante, dissipando assim o calor. Chillers resfriados a ar são mais simples de instalar e não requerem um torre de resfriamento ou um separado água loop. Eles são uma escolha popular em áreas onde água é limitado ou onde o custo inicial é uma grande preocupação.
Vantagens dos Chillers Refrigerados a Ar:
- Menor custo inicial: Geralmente, o custo inicial é menor em comparação com resfriado a água sistemas.
- Instalação mais fácil: Não há necessidade de um torre de resfriamento ou tubulação extensa.
- Menor manutenção: Menos componentes significam menor custo de manutenção comparado com resfriado a água.
- Conservação de água: Ideal para regiões com limitações água recursos ou onde conservação de água é uma prioridade.
Considerações sobre resfriadores resfriados a ar:
- Menor eficiência: Eles são normalmente menos eficientes do que chillers resfriados a água, especialmente em climas quentes.
- Níveis de ruído mais altos: Os ventiladores podem gerar ruído significativo.
- Vida útil mais curta: Eles podem ter uma vida útil mais curta em comparação com resfriado a água unidades, especialmente em ambientes hostis.
- Desempenho afetado pela temperatura ambiente: Seu desempenho pode degradar-se significativamente em condições de alta ar ambiente temperaturas.
Em regiões com calor extremo, a eficiência de um sistema refrigerado a ar pode cair, como visto em nosso Chillers centrais de parafuso resfriados a ar.
Chillers resfriados a ar versus resfriadores resfriados a água: uma comparação abrangente
O diferença entre chiller resfriado a ar e chiller resfriado a água pode ser resumido considerando vários fatores-chave: eficiência, custo, manutenção e impacto ambiental.
Recurso | Chiller resfriado a ar | Chiller resfriado a água |
Eficiência | Mais baixo, especialmente em climas quentes | Mais alto, menos afetado pela temperatura ambiente |
Custo inicial | Mais baixo | Mais alto |
Custo de manutenção | Mais baixo | Mais alto |
Uso da água | Nenhum | Requer um fornecimento contínuo de água |
Nível de ruído | Mais alto | Mais baixo |
Vida útil | Potencialmente mais curto, especialmente em ambientes hostis | Potencialmente mais longo com manutenção adequada |
Instalação | Mais simples | Mais complexo, requer torre de resfriamento e tubulação |
Impacto Ambiental | Menor impacto na água, maior uso de energia em climas quentes | Maior consumo de água, menor consumo de energia na maioria das condições |
Chillers resfriados a ar são frequentemente favorecidos por sua menor custo inicial e instalação mais simples. Eles são adequados para aplicações menores ou onde água a disponibilidade é uma preocupação. Em contraste, chillers resfriados a água são preferidos para instalações maiores onde maior eficiência e desempenho estável são críticos. A refrigerador refrigerado a água pode ser a melhor escolha se sua instalação tiver acesso a um serviço confiável fonte de água e pode gerenciar o mais alto custo de manutenção. Você pode pensar em nosso Resfriadores de glicol como um exemplo de resfriamento eficiente para necessidades industriais específicas.
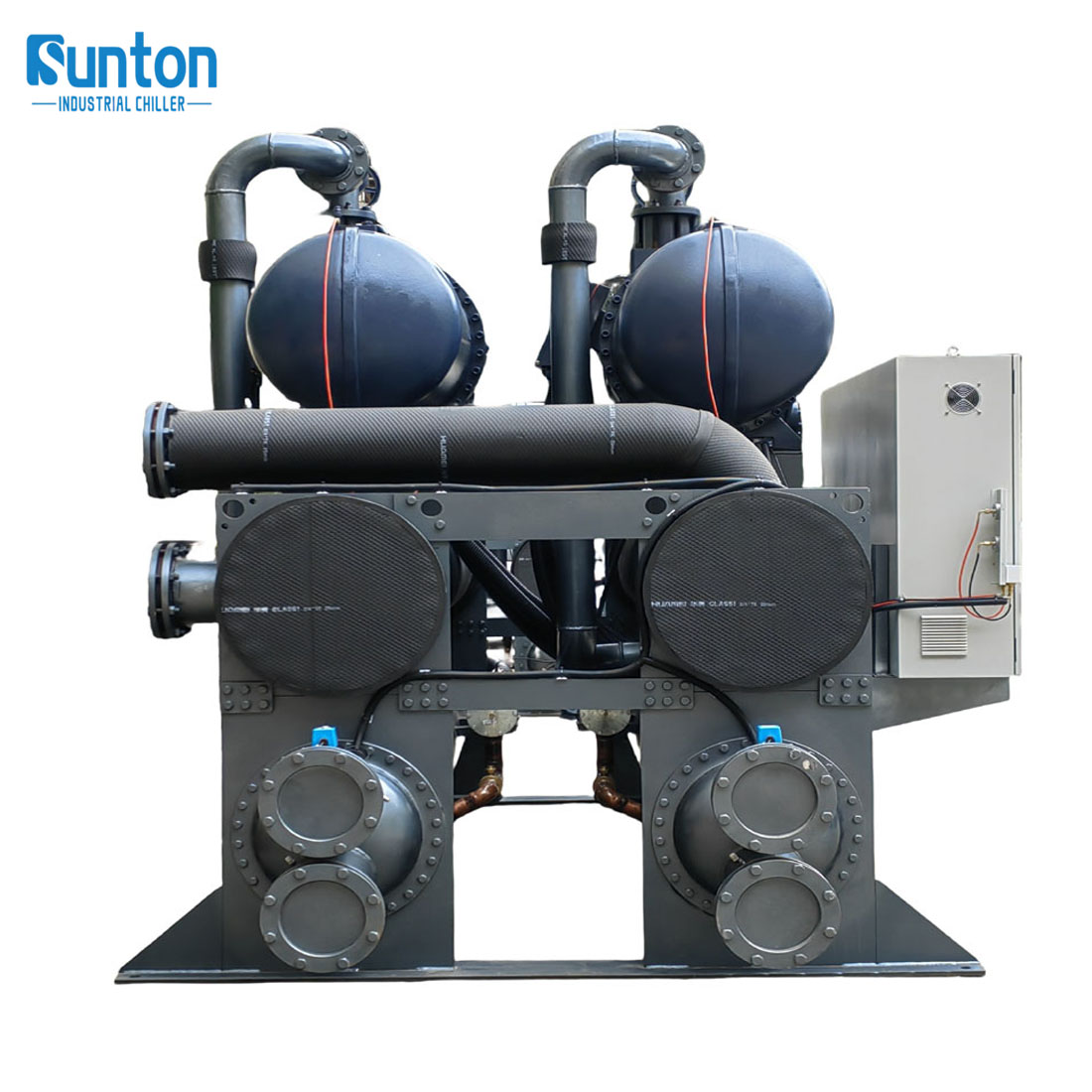
Quais fatores influenciam a eficiência e o desempenho do chiller?
Vários fatores influenciam eficiência do resfriador e desempenho, independentemente do tipo de refrigerador. Isso inclui o resfriador projeto, condições operacionais, práticas de manutenção e qualidade dos componentes utilizados. Eficiência do resfriador é frequentemente medido por seu coeficiente de desempenho (COP) ou razão de eficiência energética (EER). Um COP ou EER mais alto indica melhor eficiência.
Ar ambiente a temperatura desempenha um papel crucial no desempenho de chillers resfriados a ar. Como o temperatura do ar sobe, o resfriadorA capacidade de rejeitar calor diminui, resultando em menor eficiência. Chillers resfriados a água são menos suscetíveis a esse problema, mas dependem da eficiência do torre de resfriamento e a qualidade do água do condensador. Manutenção regular, como limpeza do condensador bobinas em chillers resfriados a ar e garantir o adequado tratamento de água em resfriado a água sistemas, é essencial para manter o desempenho ideal.
Como escolher o tipo certo de resfriador para suas necessidades específicas?
Escolhendo entre um refrigerador refrigerado a ar e um refrigerador refrigerado a água depende de vários fatores específicos para sua aplicação. Aqui estão algumas considerações importantes:
- Capacidade de resfriamento: Determinar o necessário Capacidade de resfriamento para o seu processo. Chillers resfriados a água são geralmente mais adequados para cargas mais altas.
- Clima: Considere o clima local. Chillers resfriados a ar pode ter dificuldades em ambientes extremamente quentes, enquanto chillers resfriados a água executar consistentemente.
- Disponibilidade de água: Avaliar a disponibilidade e o custo de água. Se a água é escassa ou caro, um refrigerado a ar o sistema pode ser mais prático.
- Restrições de espaço: Avalie o espaço disponível. A planta de refrigeração refrigerada a água ocupa mais espaço devido ao torre de resfriamento.
- Orçamento: Compare o custo inicial e custos operacionais de longo prazo, incluindo energia e manutenção.
- Restrições de ruído: Se o ruído for uma preocupação, chillers resfriados a água são geralmente mais silenciosos.
- Regulamentos ambientais: Considere os regulamentos locais relativos uso da água e eficiência energética.
- Componentes do resfriador
Ao avaliar cuidadosamente esses fatores, você pode tomar uma decisão informada que se alinhe com suas necessidades operacionais e orçamento. Como alguém profundamente envolvido na indústria, sempre aconselho os clientes a pensarem a longo prazo. Enquanto o custo inicial é importante, é igualmente crucial considerar o custo total de propriedade sobre o resfriadora vida útil do '.
Quais são os requisitos de manutenção para chillers resfriados a ar e a água?
A manutenção adequada é crucial para garantir a longevidade e a eficiência de qualquer resfriador. Chillers resfriados a ar normalmente requerem menos manutenção do que resfriado a água unidades. As tarefas regulares incluem a limpeza do condensador bobinas, verificação refrigerante níveis e inspecionar os ventiladores. Essas tarefas ajudam a evitar a degradação do desempenho e estendem a vida útil resfriadora vida útil do '.
Chillers resfriados a água requerem uma manutenção mais complexa devido à água sistema. Regular tratamento de água é essencial para evitar incrustações, corrosão e crescimento biológico, que podem impactar significativamente a eficiência. torre de resfriamento também precisa de limpeza e inspeção periódicas. Enquanto o custo de manutenção para chillers resfriados a água é maior, a manutenção adequada garante um desempenho confiável e pode evitar quebras dispendiosas.
O futuro da tecnologia de resfriamento: o que está por vir?
O resfriador a indústria está em constante evolução, impulsionada pelos avanços da tecnologia e um foco crescente na eficiência energética e na sustentabilidade ambiental. Estamos vendo inovações em refrigerante tecnologia, com uma mudança para refrigerantes de menor potencial de aquecimento global (GWP). Melhorias no design do compressor e sistemas de controle também estão contribuindo para maiores níveis de eficiência.
Outra tendência é o uso crescente de tecnologias inteligentes em resfriador sistemas. Essas tecnologias permitem monitoramento em tempo real, manutenção preditiva e diagnóstico remoto, o que pode reduzir significativamente o tempo de inatividade e otimizar o desempenho. Como fabricante, estamos constantemente explorando novas maneiras de aprimorar nossos produtos e fornecer aos nossos clientes os produtos mais avançados e eficientes resfriamento soluções disponíveis.
Perguntas frequentes
1. Qual é a principal diferença entre chillers resfriados a ar e resfriados a água?
O primário diferença entre chiller resfriado a ar e chiller resfriado a água é o método usado para dissipar calor. Chillers resfriados a ar usar ar ambiente, enquanto chillers resfriados a água usar um fonte de água, como um torre de resfriamento, para remover o calor do refrigerante.
2. Os chillers resfriados a água são mais eficientes do que os resfriados a ar?
Geralmente sim. Chillers resfriados a água são tipicamente mais eficientes, especialmente em climas mais quentes. Eles têm um coeficiente de desempenho (COP) mais alto e são menos afetados por flutuações em ar ambiente temperatura. Nosso Resfriadores anti-explosão são uma prova dos ganhos de eficiência possíveis com tecnologias avançadas de resfriamento.
3. Os chillers refrigerados a ar requerem fornecimento de água?
Não, Os resfriadores refrigerados a ar não requerem um fornecimento de águaEles usam o ar ambiente para resfriamento, tornando-os adequados para locais onde água é limitado ou onde conservação de água é uma prioridade.
4. Quais são os requisitos de manutenção para chillers resfriados a água?
Os resfriadores refrigerados a água requerem regular tratamento de água para evitar incrustações, corrosão e crescimento biológico. torre de resfriamento também precisa de limpeza e inspeção periódicas. Embora a manutenção seja mais complexa do que para refrigerado a ar unidades, garante ótimo desempenho e longevidade.
5. Qual tipo de resfriador é mais ecológico?
Depende das circunstâncias específicas. Chillers resfriados a água usam menos energia na maioria das condições, mas requerem quantidades significativas de água. Chillers resfriados a ar conservar água mas pode ser menos eficiente em termos de energia, especialmente em climas quentes. A escolha deve considerar tanto a energia quanto água objetivos de conservação.
6. Chillers refrigerados a ar podem ser usados em climas quentes?
Sim, mas com ressalvas. Chillers resfriados a ar podem operar em climas quentes, mas sua eficiência diminui à medida que ar ambiente a temperatura aumenta. O dimensionamento adequado e a consideração das condições climáticas específicas são essenciais para um desempenho ideal.
Principais conclusões
- Resfriadores são essenciais para o controle de temperatura em vários setores, incluindo plásticos, alimentos, produtos químicos e centros de dados.
- Chillers resfriados a ar usar ar ambiente para legal o refrigerante, enquanto chillers resfriados a água usar um água fonte como uma torre de resfriamento.
- Chillers resfriados a água são geralmente mais eficientes, mas requerem uma solução confiável água fornecimento e mais manutenção.
- Chillers resfriados a ar tem um menor custo inicial e são mais fáceis de instalar, mas podem ser menos eficientes em climas quentes.
- Escolhendo o caminho certo resfriador depende de fatores como resfriamento capacidade, clima, água disponibilidade, orçamento e considerações ambientais.
- A manutenção adequada é crucial para garantir a longevidade e a eficiência de ambos refrigerado a ar e chillers resfriados a água.
- O futuro de resfriador a tecnologia inclui avanços em refrigerante tecnologia, design de compressores e sistemas de controle inteligentes.
Escolhendo entre um refrigerador refrigerado a ar e um refrigerador refrigerado a água é uma decisão crítica que pode impactar significativamente suas operações. Ao entender as diferenças, vantagens e considerações para cada tipo, você pode fazer uma escolha informada que se alinhe com suas necessidades específicas e objetivos de longo prazo. Como um fabricante líder de resfriadores de água, estamos comprometidos em fornecer aos nossos clientes o que há de mais avançado e eficiente resfriamento soluções disponíveis. Se você está pronto para otimizar seu resfriamento processos e explorar o melhor resfriador opções para sua indústria, entre em contato conosco hoje mesmo. Vamos trabalhar juntos para atingir suas metas operacionais de forma eficiente e sustentável.
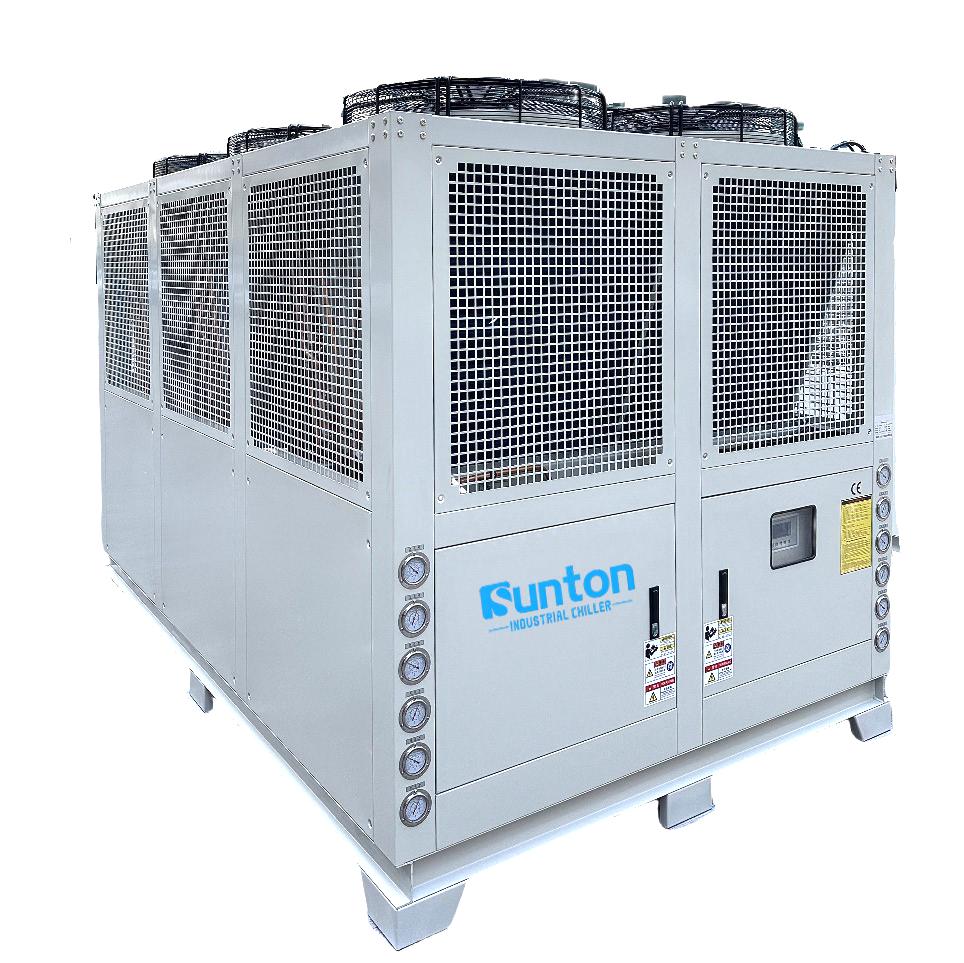