-
Dalingshan Industrial Guangdong
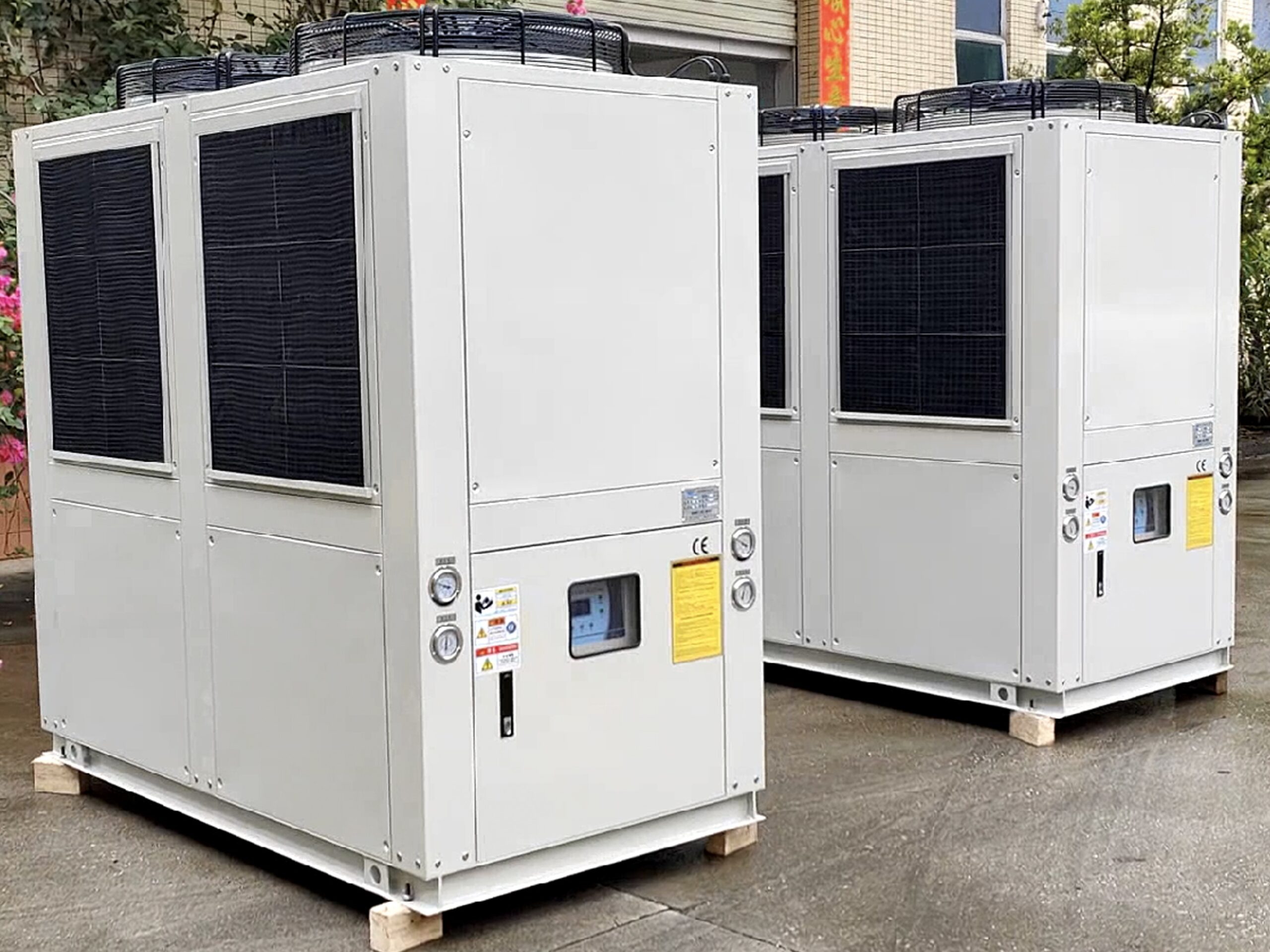
tips to use your industrial chiller more efficiently in 2023
Maximize Chiller Efficiency in 2023: Your Guide to Optimal Industrial Chiller Performance
This article dives deep into the critical aspects of optimizing commercial and industrial chiller efficiency. It provides actionable insights for various industries, including the Plastics and Rubber Industry, Machining Industry, Food and Beverage Industry, Chemical and Pharmaceutical Industry, Electronics Industry, Laser Industry, Printing Industry, Medical Industry, Laboratories and Research Institutions, and Data Centers. As an industrial chiller manufacturing plant, we understand the nuances of chiller performance and aim to share our expertise to help you achieve peak operational efficiency, reduce energy consumption, and save on energy costs. This guide is worth reading because it combines first-hand knowledge with practical tips and strategies, making it an invaluable resource for anyone looking to enhance their chiller system’s performance in 2023.
Inhoudsopgave
What Are the Main Types of Chillers Used in Commercial and Industrial Settings?
In commercial and industrial environments, chillers are essential for maintaining optimal operating temperatures. The two primary types of chillers are air-cooled and water-cooled. Air-cooled chillers use ambient air to remove heat from the refrigerant, while watergekoelde koelmachines utilize water from a cooling tower or another water source. Choosing the right chiller type depends on several factors, including the specific cooling needs, available space, and environmental considerations.
Each chiller type has its advantages. Air-cooled chillers are generally easier to install and maintain, making them suitable for smaller applications or where water resources are limited. On the other hand, water-cooled chillers are often more energy-efficient, especially in larger systems or areas with high ambient temperatures. For instance, a water-cooled screw central chiller can offer significant energy savings for large-scale industrial applications due to their superior heat transfer capabilities.
How Does Regular Maintenance Impact Chiller Efficiency?
Regular maintenance is essential for ensuring that your chiller operates efficiently and maintains its peak performance. Maintenance tasks such as cleaning condenser coils, checking refrigerant levels, and inspecting the compressor are crucial. Neglecting these tasks can lead to reduced efficiency, increased energy consumption, and higher energy bills. In fact, proper chiller maintenance can improve efficiency by up to 20% and potentially save on energy costs.
A well-maintained chiller ensures that all components are functioning correctly, which reduces the risk of breakdowns and extends the lifespan of the equipment. For example, a clean condenser coil ensures optimal heat transfer, allowing the chiller to cool more effectively. Additionally, regular checks of refrigerant levels prevent the compressor from working harder than necessary, thus conserving energy and reducing wear and tear. To enhance the operational efficiency of your chiller, it’s important to schedule regular inspections and maintenance by qualified technicians.
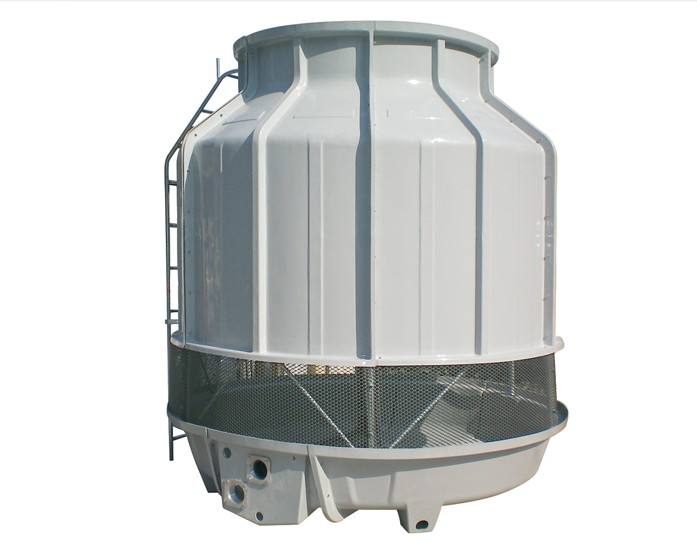
What Role Does Water Treatment Play in Optimizing Chiller Performance?
Proper water treatment is crucial for maintaining the efficiency of a chiller system, particularly in water-cooled chillers. Water quality directly impacts the heat transfer process, and poor water quality can lead to scaling, corrosion, and biological growth within the system. These issues can significantly reduce the chiller’s efficiency by obstructing water flow and reducing heat transfer efficiency.
Implementing a comprehensive water treatment program ensures that the water used in the chiller system is free of contaminants and minerals that can cause scaling and corrosion. Techniques such as filtration, chemical treatment, and regular monitoring of water quality are essential components of an effective water treatment program. For instance, using a shell and tube heat exchanger with a dedicated water treatment system can significantly enhance heat transfer efficiency and prolong the life of the equipment.
Can Upgrading Components Like Compressors and Using Variable Frequency Drives Improve Chiller Efficiency?
Upgrading key components, such as the compressor, and incorporating variable frequency drives (VFDs) can dramatically improve chiller efficiency. Modern compressors are designed for higher efficiency and can significantly reduce energy consumption compared to older models. Additionally, VFDs allow the chiller to adjust its output based on the actual cooling demand, rather than running at a constant speed.
Variable frequency drives are particularly effective in systems with fluctuating cooling loads. By adjusting the speed of the compressor motor, VFDs can optimize energy use and maintain a consistent chilled water supply temperature. This not only improves efficiency but also reduces wear and tear on the equipment, leading to lower maintenance costs and a longer lifespan. For example, an industrial chiller used in the food and beverage industry can benefit significantly from VFDs, as they can adjust to varying production levels and maintain optimal operating temperatures without wasting energy. A water-cooled scroll water chiller is an ideal choice for such applications due to its energy-efficient design and ability to handle variable loads.
How Important Is Monitoring and Adjusting Chilled Water Supply Temperature?
Monitoring and adjusting the chilled water supply temperature is vital for optimizing chiller efficiency. The chilled water supply temperature should be set to the highest possible level that still meets the cooling requirements of the application. This practice reduces the amount of energy required to chill the water, leading to lower energy consumption and operational costs.
Regularly monitoring the chilled water supply temperature and making necessary adjustments ensures that the chiller is not overcooling the water, which can waste energy. Modern chiller systems often come equipped with advanced control systems that allow for precise temperature management and monitoring. These systems can automatically adjust the chilled water supply temperature based on real-time cooling needs, further enhancing efficiency. For instance, a data center might use an air-cooled screw central chiller with advanced temperature controls to maintain optimal operating conditions while minimizing energy use.
What Are the Common Causes of Inefficiency in Commercial Chillers?
Several factors can contribute to inefficiency in commercial chillers. One common cause is improper maintenance, leading to issues like dirty condenser coils, low refrigerant levels, and malfunctioning compressors. Another significant factor is poor water quality, which can result in scaling and corrosion, reducing heat transfer efficiency and increasing energy consumption.
Additionally, operating a chiller at low loads or with an oversized or undersized chiller for the application can lead to reduced efficiency. An undersized chiller will struggle to meet cooling demands, while an oversized chiller will cycle on and off frequently, wasting energy. Using outdated or inefficient components can also contribute to inefficiency. For example, older compressors may not be as energy-efficient as newer models. Addressing these issues through regular maintenance, proper water treatment, and component upgrades can significantly improve chiller efficiency.
How Does a Cooling Tower Contribute to the Overall Efficiency of a Chiller System?
A cooling tower plays a crucial role in the overall efficiency of a water-cooled chiller system. Cooling towers remove heat from the water used in the condenser of the chiller, allowing the chiller to operate more efficiently. The efficiency of the cooling tower directly impacts the chiller’s ability to reject heat, which in turn affects its energy consumption.
Effective cooling tower maintenance, including regular cleaning and water treatment, ensures that the tower can efficiently remove heat from the water. This allows the chiller to operate at lower condensing temperatures, improving its efficiency and reducing energy consumption. Properly maintained cooling towers also help prevent issues like scaling and biological growth, which can impair heat transfer and reduce overall system efficiency.
What Are the Benefits of Optimizing Chiller Efficiency?
Optimizing chiller efficiency offers numerous benefits, including significant energy savings and reduced operating costs. Efficient chillers consume less energy, leading to lower energy bills and a smaller carbon footprint. Improved efficiency also reduces the risk of equipment breakdowns and extends the lifespan of the chiller, resulting in lower maintenance and replacement costs.
Enhanced efficiency can also improve the overall performance of the cooling system, ensuring consistent and reliable cooling for various applications. For example, in the plastics and rubber industry, maintaining a stable temperature is crucial for product quality. An efficient chiller system ensures that the required temperatures are consistently met, leading to higher product quality and reduced waste.
What Advanced Technologies Can Further Maximize Chiller Efficiency?
Advanced technologies, such as smart controls and energy management systems, can further maximize chiller efficiency. Smart controls use real-time data to optimize chiller operation, adjusting parameters like chilled water supply temperature and compressor speed to match the cooling load. These systems can also provide valuable insights into chiller performance, helping to identify areas for improvement.
Energy management systems integrate the chiller with other building systems, such as HVAC and lighting, to optimize overall energy use. These systems can automatically adjust settings based on occupancy, time of day, and other factors to minimize energy consumption. For instance, in a laboratory setting, an energy management system can coordinate the operation of the dairy milk chiller with other equipment to ensure optimal efficiency and consistent cooling performance.
How Can Businesses Ensure Their Chiller Operates at Peak Efficiency?
To ensure their chiller operates at peak efficiency, businesses should prioritize regular maintenance, implement proper water treatment, and consider component upgrades. Regular maintenance ensures that all parts of the chiller are functioning correctly, while a comprehensive water treatment program prevents scaling and corrosion, maintaining optimal heat transfer.
Upgrading to more efficient components, such as modern compressors and variable frequency drives, can significantly reduce energy consumption and improve overall efficiency. Additionally, incorporating advanced technologies like smart controls and energy management systems can further optimize chiller operation and provide valuable insights into performance. By taking these steps, businesses can ensure their chiller operates at peak efficiency, leading to significant energy savings and reduced operating costs. For example, using an anti-explosion chiller in a chemical plant can not only ensure safety but also provide efficient cooling with the right maintenance and upgrades.
FAQs
What is the best way to improve chiller efficiency?
The best way to improve chiller efficiency is through a combination of regular maintenance, proper water treatment, and strategic component upgrades. Regular maintenance ensures optimal operation, while water treatment prevents scaling and corrosion. Upgrading to energy-efficient compressors and using variable frequency drives can also significantly boost performance.
How often should a commercial chiller be serviced?
A commercial chiller should be serviced at least once a year, though twice a year is recommended for optimal performance. Regular servicing helps identify and address potential issues before they lead to reduced efficiency or breakdowns.
What are the signs of an inefficient chiller?
Signs of an inefficient chiller include increased energy bills, inconsistent cooling, unusual noises, and frequent cycling on and off. These symptoms often indicate underlying issues that need to be addressed through maintenance or component upgrades.
How does water quality affect chiller performance?
Water quality significantly affects chiller performance by influencing heat transfer efficiency. Poor water quality can lead to scaling, corrosion, and biological growth, which reduce efficiency and increase energy consumption. Implementing a proper water treatment program is essential for maintaining optimal performance.
Can using a VFD really save energy?
Yes, using a VFD can save energy by allowing the chiller to adjust its output based on the actual cooling demand. This means the chiller doesn’t have to run at full capacity all the time, reducing energy consumption and wear and tear on the equipment.
What type of compressor is most efficient for a commercial chiller?
Modern screw compressors are often considered the most efficient for commercial chillers. They offer high efficiency across a wide range of operating conditions and can significantly reduce energy consumption compared to older reciprocating or scroll compressors.
Belangrijkste opmerkingen
- Regular maintenance is essential for maintaining chiller efficiency and preventing breakdowns.
- Proper water treatment plays a crucial role in optimizing heat transfer and preventing scaling and corrosion.
- Upgrading components like compressors and using variable frequency drives can significantly improve efficiency.
- Monitoring and adjusting chilled water supply temperature helps reduce energy consumption.
- Advanced technologies like smart controls and energy management systems can further enhance chiller performance.
- Optimizing chiller efficiency leads to significant energy savings, reduced operating costs, and improved overall system performance.
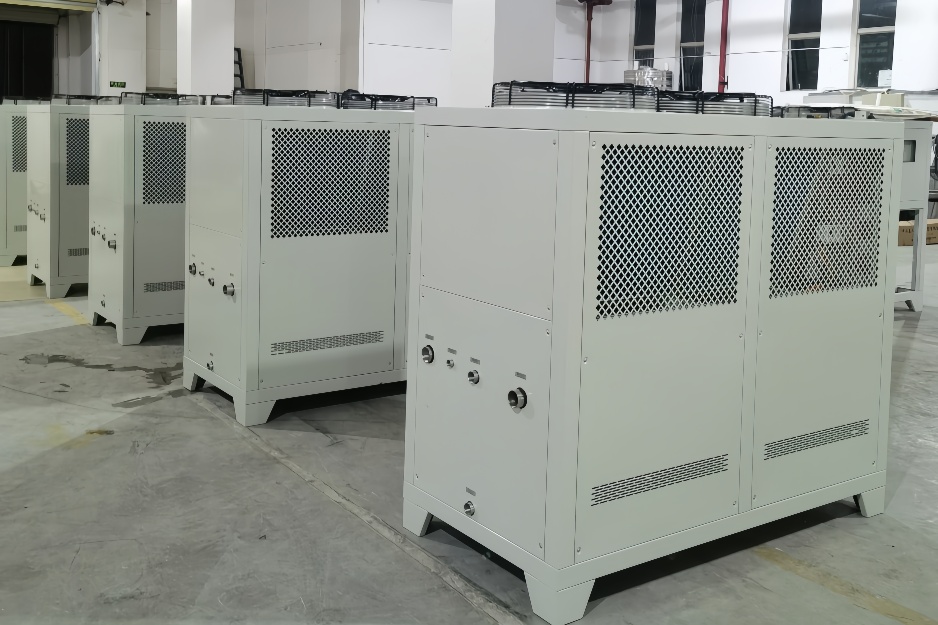