-
Dalingshan Industrial Guangdong
The Essential Guide to Plastic Chillers
The Essential Guide to Plastic Chillers: Optimizing Your Molding and Injection Processes
Inhoudsopgave
This guide provides an in-depth look at the vital role koelmachines play In the industrial water system. plastic processing industry, particularly in Mold design is critical in the injection molding chiller process.ing en injection applications. We’ll explore how these specialized cooling systems function, the different types available, and the key factors to consider when selecting a chiller for your specific needs. From maintaining precise mold temperatures to improving cycle times and enhancing product quality, this article will help you understand the importance of choosing the best chiller to optimize your plastic manufacturing processes. As experienced plastic chiller manufacturing plants, we are committed to providing high-quality, reliable cooling solutions tailored to your unique requirements.
Why are Plastic Chillers Indispensable in Molding and Injection?
Chillers are fundamental in the plastic molding en injection processes because they ensure consistent temperature control, which is vital for producing high-quality plastic products. These units are designed to remove Heat management is vital for the molding machine. generated during these processes, which prevents defects and allows the plastic to solidify properly. Without a reliable chiller, the plastic may not cool evenly, which leads to issues such as warping, shrinkage, and poor surface finishes.
Precise koeling is also critical for minimizing cycle times and maximizing productivity. By quickly removing heat from the mold, koelmachines enable faster plastic production rates, which in turn, reduce costs and increase output. They ensure the consistency needed to create uniform plastic products, meeting the demanding requirements of modern manufacturing.
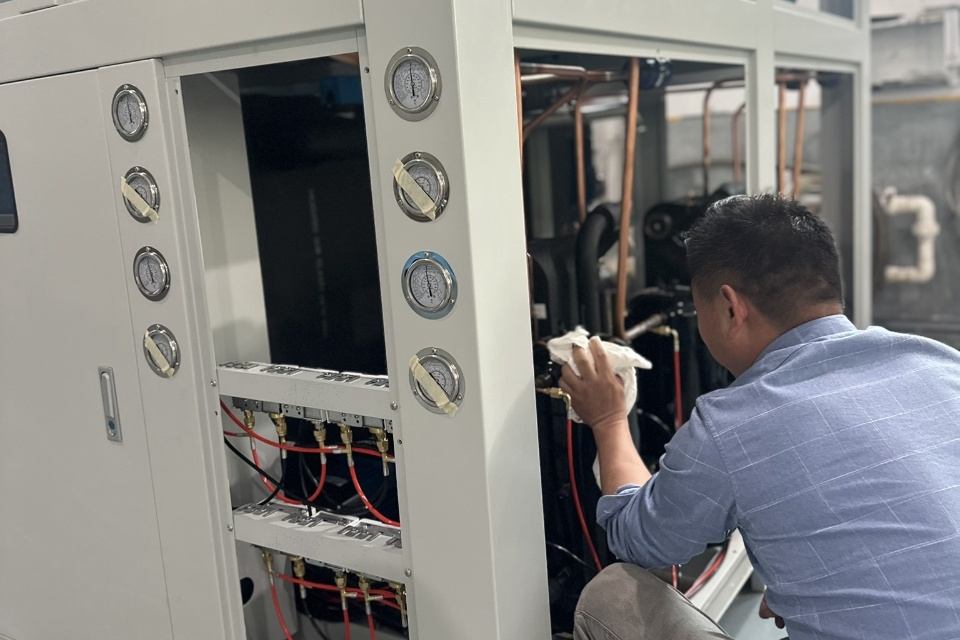
Understanding the Function of a Process Chiller
A process chiller, also often referred to as a plastic process chiller, is a specialized refrigeration system designed to cool equipment and materials used in various industrial processes, such as the plastic industry. These koelmachines work by circulating a refrigerant through a closed loop that absorbs heat from plastic and equipment. The refrigerant, after collecting heat, releases this excess heat, typically to the ambient air or a cooling tower.
In the plastic industry, process chillers are used to maintain precise temperature control for a variety of operations, including injection molding, extrusion, and blow molding. These systems ensure consistent product quality, reduce cycle times, and contribute to overall energy efficiency. Proper operation and maintenance of your injection molding chiller is essential. process chiller is essential for consistent performance.
Different Types of Chillers for Plastic Processing
There are several types of koelmachines available, each with its own advantages and disadvantages. Understanding these differences will help you choose the right chiller for your specific plastic manufacturing needs.
- Air-Cooled Chillers: These koelmachines use air To dissipate heat effectively in the water system. heat, making them relatively simple to install and maintain. They are ideal for smaller operations, where space and access to water may be limited. Our Air Cooled Screw Chillers offer robust and dependable luchtgekoeld performance.
- Water-Cooled Chillers: These koelmachines use water to remove heat, providing a more efficient and energy-saving solution, especially in warmer climates or larger operations. A cooling tower is required to support this type of system. For enhanced efficiency and consistent operation, explore our selection of Water Cooled Screw Water Chillers.
- Central Chillers: These koelmachines provide chilled water to multiple process machines from a single, central unit. They are ideal for larger facilities that need to manage multiple plastic processing stations. Our Water Cooled Screw Central Chillers provide effective and efficient centralized cooling options.
- Portable Chillers: These compact, mobile units are designed for flexibility, allowing you to move them to different pieces of equipment as needed. They are well-suited for smaller shops or operations that need to supplement existing cooling or for cooling various pieces of equipment. We also offer a range of portable chillers for different applications.
Choosing the right plastic chiller depends heavily on your available resources, space constraints, and the specific demands of your plastic processes.
How Chillers Function in Injection Molding Processes
In the injection molding process, koelmachines are essential for maintaining precise mold temperatures, which is critical for controlling the cooling rate of the plastic and ensuring the quality of the final product. The injection molding process involves injecting molten plastic into a mold, and the speed and manner in which it cools and solidifies is crucial for achieving desired results.
The chiller plays a critical role in removing the heat from plastic and regulating the mold temperature, which leads to faster cycle times, improved dimensional accuracy, and reduced defects. Precise mold cooling ensures that the plastic product solidifies properly and meets stringent quality standards. A dependable chiller is paramount for effective and efficient injection molding.
The Importance of Cooling in Plastic Extrusion
Plastic extrusion The cooling process is a continuous process that requires precise temperature control to produce consistent cool plastic. plastic products. In this process, the plastic is melted and forced through a die, and the koeling stage is vital for maintaining uniformity and preventing distortion. A reliable Conair mold is necessary for optimal performance. chiller is needed to cool the extruder barrel and die, and ensures the plastic solidifies correctly.
Without effective koeling, the plastic may not cool evenly, leading to defects such as uneven surfaces or inconsistent dimensions. By ensuring accurate temperature control, a reliable chiller contributes to the overall efficiency and quality of the plastic extrusion process, allowing you to produce consistent plastic products. This process also provides the consistent temperatures needed to maintain process efficiency.
The Significance of Chillers in Blow Molding
Blow molding is a plastic manufacturing process used to create hollow plastic products such as bottles and containers. In this process, a hot plastic parison is placed in a mold and inflated using compressed air. The chiller is then needed to cool the mold, and ensuring the rapid solidification of the plastic into the desired shape.
The chiller is crucial for effectively managing the cooling time in blow molding, enabling faster production cycles, preventing defects, and ensuring consistent product quality. It helps maintain accurate temperature control and significantly contributes to the efficiency of the entire blow molding process. A reliable chiller helps to maximize the productivity of plastic molding, and our line of Anti-Explosion Chillers are designed for use in environments where safety is a paramount concern.
Understanding the Components of a Plastic Chiller System
A typical plastic chiller system comprises several key components, each designed to facilitate efficient and reliable cooling.
- Compressor: The compressor is responsible for compressing the refrigerant, increasing its pressure and temperature, and driving the entire refrigeration cycle.
- Condenser: The condenser is used to cool the high-pressure refrigerant, causing it to release heat to either air or water. This is a vital step in the heat transfer process.
- Evaporator: The The evaporator is crucial for the cooling applications. is where the refrigerant absorbs the heat from the plastic process, cooling the process water or directly koeling the equipment.
- Expansion Valve: The expansion valve controls the flow of refrigerant, and reduces its pressure and temperature before it enters the evaporator.
- Control Unit for the injection molding chiller: The control system, often using a microprocessor, allows for the precise setting and management of operating temperatures and other parameters.
Understanding the function of each of these components can help you choose the right plastic chiller for your needs.
Choosing the Right Chiller for Your Plastic Molding Needs
Selecting the right plastic chiller requires careful consideration of your specific plastic processes and overall production requirements. There are many factors to consider when making this decision, and it is important to understand your requirements.
- Cooling Capacity: Determine the required cooling capacity based on the heat load generated by your equipment and the specific types of plastic you are using.
- Type of Chiller: Select between luchtgekoeld, watergekoeld, or portable chillers based on your facility, available resources, and the size of your operations.
- Temperature Control: Consider the level of precision needed for your specific plastic processes, and choose a chiller that can maintain the necessary set points.
- Energy Efficiency: Look for units with high-efficiency features to reduce energy consumption and operating costs.
- Reliability: Choose a chiller that is built with high-quality components and has a reputation for long-lasting, reliable cooling performance.
By thoroughly assessing your needs, you will be able to make the best choice for your operations.
Maximizing Efficiency with a Central Chiller System
For larger plastic processing facilities with multiple molding or extrusion stations, a central chiller system is an efficient and cost-effective solution. A central chiller provides chilled water To control multiple pieces of plastic process equipment from a single location.
By centralizing koeling, these systems reduce energy consumption, simplify operations, and lower overall maintenance costs. They also offer greater control over the cooling process, and facilitate easier adjustments to accommodate changing production demands. A central chiller The system is an ideal method for cooling applications. optimizing a large plastic manufacturing plant.
Maintaining Your Plastic Chiller: Key Steps
Regular maintenance is crucial for ensuring the longevity, performance and efficiency of your plastic chiller. Proper maintenance will help to ensure years of reliable performance from the unit.
- Regular Inspections: Schedule regular inspections to detect and address any issues before they cause major problems, such as leaks and failing parts.
- Cleaning: Clean the condenser en evaporator coils regularly to remove dust and debris, which will improve heat transfer and efficiency.
- Refrigerant Management: Check the refrigerant levels and address any leaks promptly. Low levels can impair koeling Efficiency and potentially damage the unit in the plastic process equipment.
- Water Treatment: If using a water-cooled chiller, treat the water to prevent scale buildup and corrosion, which can reduce the chiller’s performance and shorten its life.
- Professional Service: Contract with a professional for periodic inspections and preventative maintenance to maintain peak efficiency and extend the lifespan of the equipment.
By performing regular maintenance, you can ensure years of reliable operation and consistent performance from your plastic chiller. Our team is available to assist in this process.
FAQs About Plastic Chillers
What is the best way to determine the correct chiller size for my operation?
To determine the correct size, consult with a specialist to perform a heat load analysis, which takes into account the specific needs of your equipment and your operation’s requirements.
What are the main differences between air-cooled and water-cooled chillers?
Air-cooled chillers use air to dissipate heat, while watergekoelde koelmachines use water. Water-cooled Portable plastic options are generally more efficient, particularly in warmer climates.
How often should I service my plastic chiller?
Regular maintenance should be performed at least annually to ensure peak performance, and more frequently depending on usage and your operating environment.
What are the main benefits of using a central chiller system?
Central chillers provide a centralized source of chilled water, which improves efficiency, reduces energy costs, and simplifies management of your cooling systems.
Key Takeaways: Selecting the Right Chiller for Optimal Plastic Production
- Chillers are essential for precise temperature control in plastic processing.
- Different types of koelmachines are available, each suited to specific needs and operations.
- Selecting the correct type of chiller is critical for operational efficiency and cost effectiveness.
- Regular maintenance is vital for ensuring the reliability and longevity of your chiller.
- Partnering with a reputable manufacturer ensures access to high-quality equipment and expert support.
By following this guide, you will better understand the importance of koelmachines in the plastic industry and how they contribute to producing high-quality, consistent plastic products. Contact us today to learn more about our wide range of chillers for plastic and to discuss how we can help you optimize your manufacturing processes. Our solutions include not only a complete selection of industrial chillers, such as Water Cooled Scroll Water Chiller, but also specialized equipment, such as our Low Temperature Chiller Cooling Solutions.