-
Dalingshan Industrial Guangdong
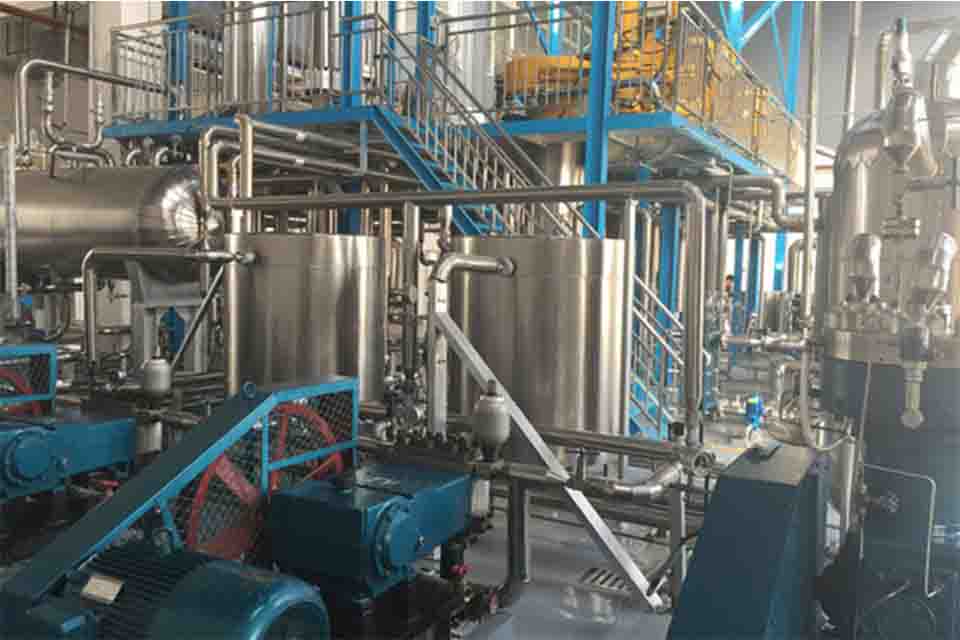
is a glycol chiller safe for food
Glycol Chiller Coolant: Everything You Need to Know About Glycol Chillers
This article dives into the world of glycol koelmachines, exploring their functionality, applications, and the crucial role they play in various industries. Whether you’re in the Plastics and Rubber Industry, Machining Industry, or the Food and Beverage Industry, understanding glycol chiller systems is essential for optimizing your operations. This is a must-read because it provides a comprehensive overview of glycol and its applications in industrial koelmachines, offering insights that can lead to improved efficiency, cost savings, and enhanced product quality.
Inhoudsopgave
1. What is a Glycol Chiller and How Does it Work?
A glycol chiller is a type of chiller system that uses a mixture of glycol and water as a coolant. Glycol is an organic compound known for its antifreeze properties, allowing it to lower the freezing point of water. This capability is crucial in industrial settings where temperatures need to be maintained below the normal freezing point of water.
Glycol chillers work by circulating the glycol-water coolant mixture through a heat exchanger or a series of pipes, absorbing heat from the process or equipment being cooled. The heated coolant then returns to the refrigeration unit to repeat the cooling process. This closed-loop system ensures consistent and efficient cooling, making glycol koelmachines ideal for various industrial applications. A glycol chiller is designed to provide cooling capabilities at low temperatures, typically below the freezing point of water. The glycol is mixed with water, known as a glycol mix, to create a heat transfer fluid that can operate at low-temperature ranges without freezing. This glycol chiller cooling process involves the coolant mixture from the refrigeration unit circulating through the thermal heat exchanger piping, absorbing heat, and then returning to the refrigeration unit to repeat the cooling cycle. It is very useful for the production of beer, wine and liquor, also for ice rinks.
2. What are the Different Types of Glycol Used in Chillers?
There are two primary types of glycol used in koelmachines: ethylene glycol en propylene glycol. Ethylene glycol is the more common type due to its excellent heat transfer properties and lower cost. However, it is toxic and should not be used in applications where it might come into contact with food or potable water.
Propylene glycol is less toxic than ethylene glycol and is considered food grade. It is often used in the food and beverage industry and other applications where safety is a primary concern. While propylene glycol is generally regarded as safe to use in food, it’s essential to use a formulation specifically designated as food safe or safe for incidental contact with food. I, as a representative of Industrial Water Chiller Manufacturing plants for products, can assure you that we use only food-grade glycol in our koelmachines to ensure the safety of your products.
3. What is the Role of Inhibitors in Glycol Solutions?
Inhibitors are additives used in glycol solutions to prevent corrosion and scale buildup in koelsystemen. Corrosion can significantly reduce the efficiency and lifespan of a chiller, leading to costly repairs and downtime. Inhibitor packages are designed to protect various metals commonly found in cooling systems, such as copper, brass, and aluminum. The type of glycol chosen, whether it be ethylene or propylene, significantly affects the chiller’s ability to operate efficiently at low temperatures. It’s crucial to understand the properties of ethylene and propylene glycol when deciding the type of glycol to use in your chilling system.
Using the correct type of inhibitor is crucial for maintaining the health of your glycol chiller system. As an expert in industrial koelmachines, I recommend consulting with a specialist to determine the best inhibitor for your specific application.
4. How Does a Glycol Chiller System Work in a Brewery?
In a brewery, glycol koelmachines are used to maintain precise temperatures during fermentation and to cool draft beer lines. The chilling system circulates chilled glycol through jackets surrounding the fermentation tanks, allowing brewers to control the fermentation process accurately. Maintaining the correct temperature is critical for producing high-quality beer. Glycol chiller systems that use a glycol solution ensure that the beer is chilled to the desired temperature without the risk of freezing.
Additionally, glycol is used to keep beer lines cold, ensuring that draft beer is served at the perfect temperature. As someone deeply involved in the manufacturing of industrial koelmachines, I understand the unique challenges faced by breweries and can provide tailored glycol chiller solutions to meet their specific needs. If you need more information, verify your email en check your inbox for recent posts and newsletters about our latest products and services.
5. How Does a Glycol Chiller Operate in Food Processing?
Glycol chillers play a vital role in the food and beverage industry, particularly in food processing. They are used to rapidly cool products after cooking, pasteurization, or other industrial process that requires precise temperature control. Rapid cooling helps to preserve the quality and safety of food products by inhibiting bacterial growth. The chiller is an essential component of many food processing systems, ensuring that temperatures are maintained within a safe range to slow the rate of freezing and extend the shelf life of products.
In food processing applications, propylene glycol is the preferred choice due to its non-toxic nature. As a manufacturer of industrial koelmachines, I ensure that our koelmachines designed for the food industry use only food-grade propylene glycol to comply with safety standards.
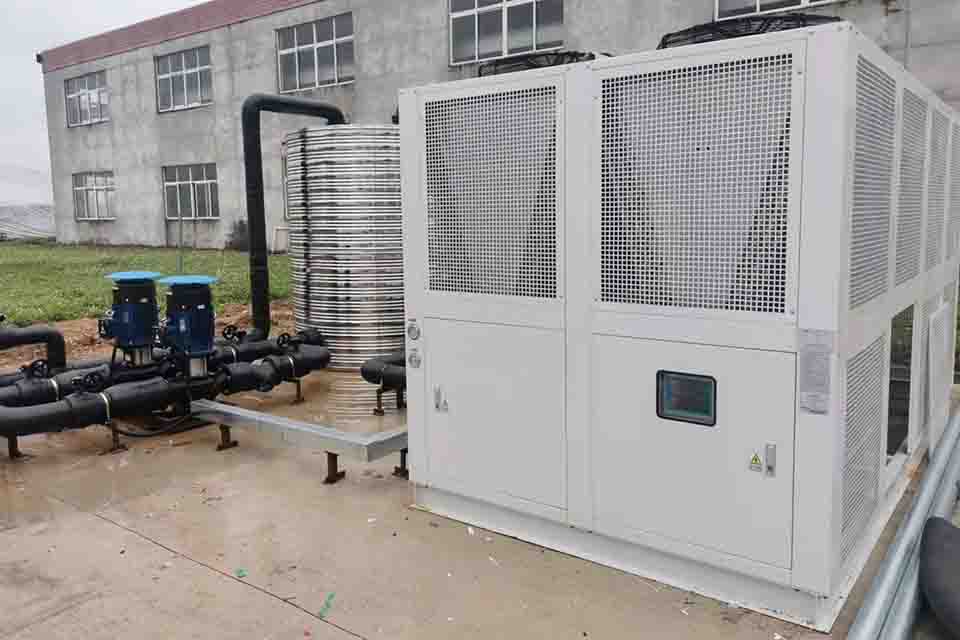
6. What is the Correct Ratio of Glycol to Water in a Chiller System?
The correct ratio of glycol to water in a chiller system depends on the specific application and the desired operating temperature. A higher concentration of glycol will lower the freezing point of the mixture but may also reduce its heat transfer efficiency. Generally, a glycol concentration of 30-50% is sufficient for most industrial applications. A refractometer is a tool that can be used to measure the concentration of glycol in a solution, ensuring that it is within the desired range for optimal performance of the glycol chiller.
Determining the right glycol concentration requires careful consideration of factors such as the temperature range, the type of equipment being cooled, and the potential for freezing. At Industrial Water Chiller Manufacturing plants, we can help you determine the optimal glycol mix for your chiller system to ensure maximum efficiency and performance. In worst case scenario if concentration is not sufficient, glycol will freeze, if concentration is too high, heat transfer will be reduced. The amount of glycol needed depends on the specific industrial process and the desired operating temperature range. To determine how much glycol is required, consider the freezing point you need to achieve and the total volume of the chilling system. Glycol comes in different types, such as ethylene en propylene, and the choice between them depends on whether the system is used in food and beverage processing. For food processing applications, it’s crucial to use food-grade propylene glycol, which is non-toxic en safe for incidental contact with food.
7. How to Determine if a Glycol Chiller is Right for Your Application?
Whether a glycol chiller is the right choice for your application depends on several factors. If your process requires cooling below the freezing point of water, a glycol chiller is likely necessary. Additionally, if you are working with food and beverage processing or other applications where food safety is a concern, a glycol chiller using food-grade propylene glycol is essential. Choosing the right glycol chiller involves considering factors such as the required temperature range, the type of equipment being cooled, and energy consumption. Consulting with an expert can help you make an informed decision.
Glycol chillers offer several advantages, including precise temperature control, the ability to operate at low temperatures, and the use of food-safe coolants. As a specialist in industrial koelmachines, I can help you assess your cooling needs and determine whether a glycol chiller is the right solution for your application.
8. What are the Maintenance Requirements for Glycol Chiller Systems?
Proper maintenance is crucial for ensuring the longevity and efficiency of glycol chiller systems. Regular checks of the glycol concentration and pH level are necessary to maintain the coolant’s effectiveness and prevent corrosion. It’s also important to inspect the system for leaks and to clean or replace filters as needed.
In addition to routine maintenance, it’s advisable to have your glycol chiller system serviced by a qualified technician at least once a year. As a manufacturer of industrial koelmachines, we offer comprehensive maintenance services to keep your chiller running smoothly.
9. What are the Safety Considerations When Using Glycol Chillers?
Safety is paramount when working with glycol koelmachines. Ethylene glycol is toxic and should be handled with care. It’s important to use appropriate safety equipment, such as gloves and eye protection, when handling glycol. In case of a spill, it’s crucial to follow proper cleanup procedures to prevent environmental contamination. Also is very important regular monitoring of the glycol-water coolant mixture helps prevent issues like freezing or insufficient cooling.
When using propylene glycol in food processing applications, it’s essential to ensure that the glycol is food grade en safe to use in food. As a responsible manufacturer, we adhere to strict safety standards in the design and production of our glycol koelmachines.
10. How to Optimize the Efficiency of Your Glycol Cooling System?
Optimizing the efficiency of your glycol cooling system involves several key strategies. Ensuring the correct glycol concentration is crucial, as an improper glycol mixture can reduce heat transfer efficiency. Regular maintenance, including checking for and repairing leaks, cleaning heat exchangers, and maintaining proper fluid levels, is essential.
Here is a table summarizing key factors affecting the efficiency of glycol cooling systems:
Factor | Impact on Efficiency | Optimization Strategy |
Glycol Concentration | Affects heat transfer and freezing point | Maintain optimal glycol-to-water ratio, typically between 30-50% glycol. |
System Maintenance | Influences overall system performance and longevity | Regularly check for leaks, clean heat exchangers, and maintain proper fluid levels. |
Temperature Control | Determines cooling effectiveness and energy consumption | Utilize advanced control systems for precise temperature regulation. |
Flow Rate | Affects heat transfer rate | Ensure proper flow rate as per system design specifications. |
Heat Exchanger Condition | Dirty or fouled heat exchangers reduce efficiency | Regularly clean and inspect heat exchangers to maintain optimal heat transfer. |
Insulation | Poor insulation leads to energy loss | Ensure proper insulation of pipes and components to minimize heat gain. |
System Design | Inefficient design can lead to higher operational costs | Optimize system design for specific application requirements, considering factors like load and usage. |
Coolant Quality | Degraded coolant reduces performance | Periodically test and replace coolant as needed to maintain quality. |
Ambient Temperature | High ambient temperatures can reduce system efficiency | Consider environmental factors during system design and operation. |
Energy-Efficient Components | Use of older, less efficient components increases costs | Upgrade to energy-efficient pumps, compressors, and other components. |
Additionally, using high-quality components and implementing advanced control systems can significantly improve efficiency. As a leading manufacturer of industrial koelmachines, we are committed to providing energy-efficient glycol chiller solutions that help our customers reduce operating costs and minimize their environmental impact.
FAQs
What is the main difference between ethylene and propylene glycol?
Ethylene glycol has better heat transfer properties and is less expensive, but it is toxic. Propylene glycol is less toxic and considered food grade, making it suitable for use in the food and beverage industry. While glycol is non-toxic in its food-grade form (propylene glycol), ethylene glycol has mildly toxic properties and should not be used in applications where it might come in contact with food.
Can I use RV antifreeze in my glycol chiller?
RV antifreeze is typically made from propylene glycol, but it may contain additives that are not suitable for industrial koelsystemen. It’s best to use a glycol solution specifically formulated for use in koelmachines.
How often should I change the glycol in my chiller system?
The frequency of glycol changes depends on the specific application and the operating conditions. Generally, it’s recommended to test the glycol concentration and pH level annually and change the glycol every 3-5 years.
What should I do if my glycol chiller system is not cooling properly?
If your glycol chiller system is not cooling properly, you should first check the glycol concentration and ensure that it is within the recommended range. Also check if there is enough glycol in the system and that the mixture is appropriate for your operating conditions. You should also inspect the system for leaks and check the operation of the pump and compressor. If the problem persists, it’s best to contact a qualified technician for assistance. Make sure there is enough glycol in the system and that the glycol mix is correct. If the glycol chiller is not cooling properly, check the amount of glycol and the condition of the heat exchanger. If you’re unsure how to check these components, consider reaching out to a professional for assistance.
Is glycol safe to use in food processing?
Propylene glycol is generally recognized as safe (GRAS) by regulatory agencies and is commonly used in food processing applications. It’s important to use food-grade propylene glycol and to follow proper handling and safety procedures.
How do I know if I have enough glycol in my system?
You can use a refractometer to measure the glycol concentration in your system. The refractometer will provide a reading that indicates the freezing point of the glycol solution, allowing you to determine if the concentration is within the desired range.
Conclusion
Here are the most important things to remember about glycol koelmachines:
- Glycol chillers are essential for applications requiring cooling below the freezing point of water.
- Ethylene glycol en propylene glycol are the two main types of glycol used in koelmachines, each with its own advantages and disadvantages.
- Inhibitors play a crucial role in preventing corrosion and maintaining the efficiency of glycol chiller systems.
- Glycol chillers are widely used in industries such as brewing and food processing to maintain precise temperatures and ensure product quality.
- The correct ratio of glycol to water is crucial for optimal performance and efficiency.
- Regular maintenance and adherence to safety guidelines are essential when working with glycol koelmachines.
Here are some of our products that might interest you: Water Cooled Screw Water Chiller, Air Cooled Screw Chiller, Glycol Chillers, Industrial Chillers For Agriculture, Industrial Chillers For Electroplating.
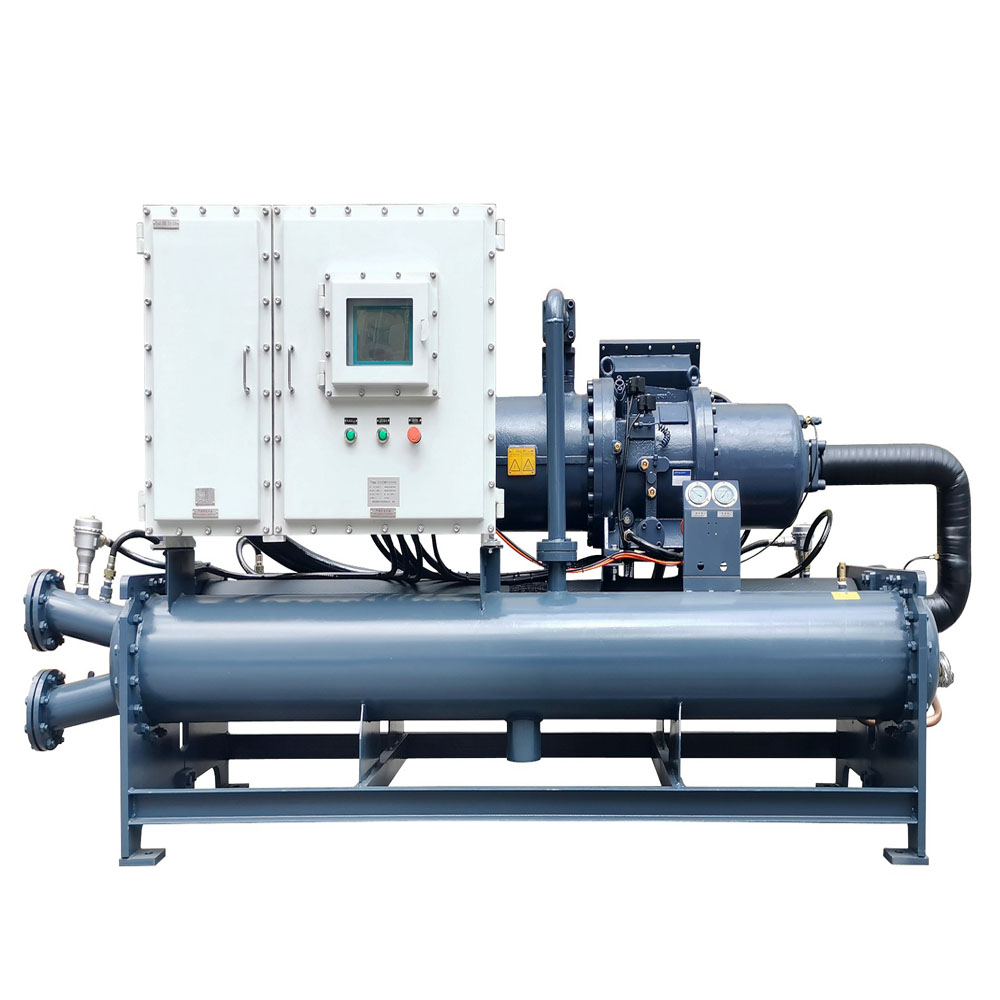