-
Dalingshan Industrieel Guangdong
Industrial Chillers For Plastic Industry
Plastic chillers: Cooling Solution for the Plastic Industry
This comprehensive guide dives deep into the world of chillers for plastic processing, exploring the critical role they play in various plastic manufacturing applications. From injection molding to extrusion, understand how the right chiller can significantly improve your product quality, boost production efficiency, and enhance your bottom line. Whether you’re a seasoned plastics processor or just starting, this article provides valuable insights to help you choose the perfect chiller for your needs.
Inhoudsopgave
What is a Chiller and Why is it Essential for Plastic Processing?
A chiller is a refrigeration system that removes heat from a process and transfers it to another medium, typically water or air. In plastic processing, chillers are essential for maintaining precise temperature control during various manufacturing processes. This precise temperature control is crucial for achieving consistent product quality, reducing defects, and maximizing production efficiency.
Plastic manufacturing processes generate significant amounts of heat. Without adequate cooling from a cooling tower, this heat can lead to warped parts, inconsistent dimensions, and other defects. Chillers provide the reliable cooling necessary to prevent these issues, ensuring high-quality plastic products. Plastic chillers are used extensively for several process cooling applications. They deliver chilled water which is essential for cooling molds, machinery and other equipment used in the production of plastic items.
Types of Plastic Chillers: Air-Cooled vs. Water-Cooled
Two primary types of chillers dominate the plastics industry: air-cooled and water-cooled chillers. Air-cooled chillers use air to dissipate heat from the refrigeration system, making them relatively easy to install and maintain. They are often more portable, suitable for various applications like injection molding machine cooling or blow molding, particularly for smaller operations. These chillers for plastic provide precise temperature control, a critical factor in producing high-quality products. Water-cooled chillers use water to remove heat, offering higher energy efficiency, especially in larger industrial settings. However, they require a dedicated water system, which can add to the initial investment.
How Do Chillers Cool Plastic in Injection Molding?
In the injection molding process, molten plastic is injected into a mold. Rapid cooling is critical to solidify the plastic and maintain the desired shape. Chilled water from a plastic process chiller circulates through channels within the mold, effectively extracting heat from the hot plastic and accelerating the cooling time. This precise temperature control leads to faster cycle times, increased production output, and improved product quality.
The cooling system plays a vital role by ensuring the molded parts maintain their dimensional stability and structural integrity. A malfunctioning or inadequate cooling system can result in production delays and increased manufacturing costs. Selecting the right type of chiller – air-cooled or watergekoeld – depends on your facility’s infrastructure and specific cooling requirements.
Chiller Capacity: Sizing Your Chiller for Optimal Performance
Choosing the correct chiller capacity is crucial for efficient and effective cooling. The chiller capacity, typically measured in tons or kW, represents the amount of heat the portable chillers can remove per hour. Factors like the type of plastic, the size of the mold, and the desired cooling time influence the required chiller capacity. Undersized chillers struggle to maintain the required temperature, while oversized chillers consume excess energy, impacting operational costs.
A careful assessment of your plastic process equipment and cooling needs is essential to determine the optimal chiller capacity. Consulting with a chiller expert can help you calculate the appropriate size and select the right plastic chiller for your specific application. A properly sized chiller not only ensures efficient cooling but also contributes to energy efficiency and reduces operating expenses.
Choosing the Right Plastic Chiller for Your Application
Different plastic processes require different types of chillers. For instance, industrial chillers used in extrusion processes may differ from those used in blow molding. Consider factors like the type of plastic being processed, the required temperature range, the production volume, and the available space when selecting a chiller. Portable plastic chillers offer flexibility for smaller operations, while central chillers provide a centralized cooling solution for larger facilities.
Feature a compressor that enhances efficiency in maintaining optimal cooling temperatures. | Air-Cooled Chiller | Water-Cooled Chiller |
Installation | Easier, requires less infrastructure | More complex, needs dedicated water system |
Maintenance | Simpler | Can be more demanding due to water treatment needs |
Energie-efficiëntie | Lower, especially in hot climates | Higher, especially in larger capacities |
Portability | Generally more portable | Less portable |
Cost | Lower initial investment | Higher initial investment, potentially lower operating costs |
Understanding these differences helps you determine the type of chiller best suited to your specific needs. Whether you’re working with injection molding machines, blow molding equipment, or other plastic manufacturing machines, selecting the appropriate chiller is vital for achieving optimal performance and maximizing return on investment.
Blow Molding and the Importance of Process Cooling
Blow molding relies on precise temperature control to create hollow plastic products. The parison – a hollow tube of heated plastic – is inflated within a mold to take the desired shape. Chilled water circulating through the mold cools the plastic quickly, maintaining the shape and ensuring consistent wall thickness. Without proper cooling, the parison can sag or deform, resulting in defective products.
Maintaining precise temperature control throughout the blow molding process is essential for achieving high-quality results. The chiller plays a critical role in this process, providing the consistent cooling needed to prevent defects and ensure the final product meets the required specifications. Whether you are producing bottles, containers, or other hollow plastic products, a reliable chiller is crucial for maintaining product quality and efficient production.
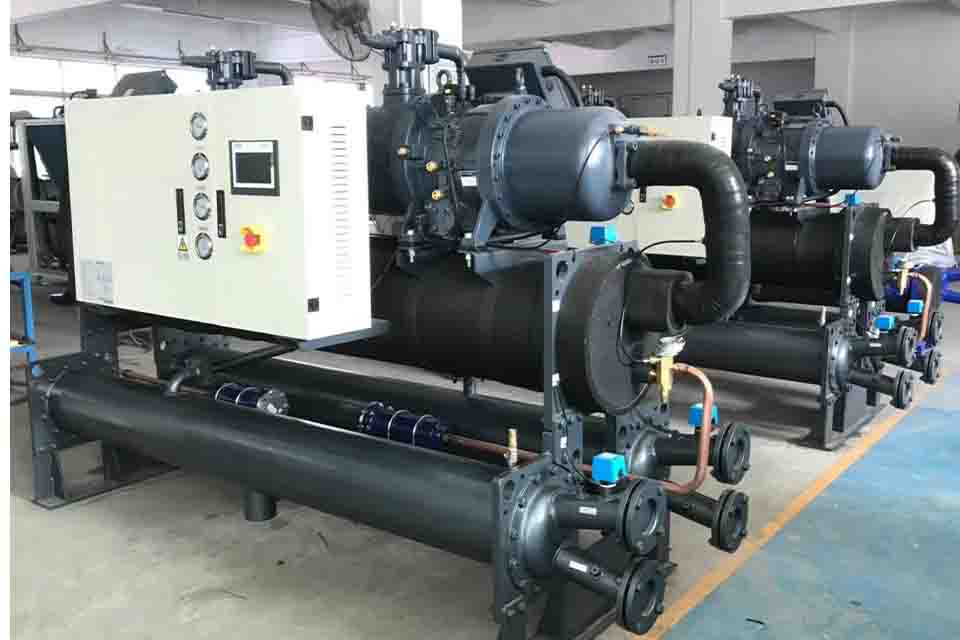
Optimizing Plastic Extrusion with Chillers for Extrusion
Extrusion involves melting plastic and forcing it through a die to create continuous shapes. Chilled water plays a vital role in cooling the extruded plastic, preventing deformation and maintaining the desired profile. Chillers for extrusion are designed to provide the consistent and precise temperature control necessary for this process. Maintaining the proper temperature during extrusion is crucial for producing uniform products with consistent dimensions.
The extruded plastic needs to cool rapidly and evenly to maintain its shape and prevent defects. The cooling solution needs to be highly efficient to meet the demands of the continuous extrusion process. An appropriately sized and configured chiller ensures that the extruded plastic cools at the correct rate, optimizing the production process and delivering high-quality products.
The Benefits of Using Industrial Chillers in Plastic Manufacturing
Industrial chillers provide numerous benefits in plastic manufacturing, including:
- Improved Product Quality: Precise temperature control leads to consistent product dimensions, reduces defects, and enhances overall product quality.
- Increased Production Efficiency: Faster cooling times in plastic injection processes mean shorter cycle times, increasing production output and reducing manufacturing lead times.
- Enhanced Energy Efficiency: Modern chillers are designed with energy efficiency in mind, minimizing energy consumption and reducing operating costs.
- Reliable Temperature Stability: Chillers provide a reliable source of cooling, ensuring consistent temperature control in plastic production regardless of ambient conditions.
These benefits contribute to a more efficient, cost-effective, and high-quality plastic manufacturing process. Whether you’re involved in injection molding, blow molding, extrusion, or other plastic processes, a reliable chiller is an essential investment for any plastic processing operation.
Maintaining Your Plastic Process Chiller for Long-Term Efficiency
Regular maintenance is essential to ensure the long-term efficiency and reliability of your plastic process chiller. This includes routine tasks like cleaning the condenser coils, checking refrigerant levels, and inspecting pumps and other components. A well-maintained chiller operates more efficiently, consumes less energy, and experiences fewer breakdowns.
Preventative maintenance also extends the lifespan of your chiller, maximizing your return on investment. By addressing potential issues early, you can avoid costly repairs and downtime. Establishing a regular maintenance schedule and adhering to manufacturer recommendations ensures optimal performance and extends the life of your chilling equipment.
Contact Us: Find the Perfect Chiller Solution for Your Business
Are you looking for a reliable and efficient chiller for your plastic manufacturing needs? Contact us today to discuss your requirements. Our team of experts can help you select the right plastic chiller manufacturing solution for your specific application, ensuring optimal performance and maximizing your return on investment. We offer a wide range of chiller solutions for various plastic processes, including injection molding, blow molding, extrusion, and more.
FAQs:
How do I choose the right chiller size for my plastic injection molding application?
Calculating the appropriate chiller size requires considering factors like the type of plastic, mold size, desired cooling time, and ambient temperature. Consulting with a chiller expert is recommended for accurate sizing.
What are the key maintenance tasks for a plastics chiller?
Regular maintenance includes cleaning condenser coils, checking refrigerant levels, inspecting pumps and other components, and ensuring adequate water treatment for water-cooled systems.
What are the signs that my chiller needs professional service?
Signs include reduced cooling capacity, unusual noises, leaks, excessive energy consumption, and frequent cycling on and off.
What type of coolant is best for my plastic chiller?
The most common coolant is water, but other fluids like glycol solutions can be used for specific applications requiring lower temperatures. Choosing the right coolant depends on your specific plastic production process requirements.
How can I improve the energy efficiency of my chiller system?
Optimizing chiller efficiency involves regular maintenance, proper sizing, using energy-efficient components, and implementing control strategies to match cooling capacity with demand.
What safety precautions should I take when operating a chiller?
Safety precautions include proper electrical grounding, adequate ventilation, following lockout/tagout procedures for maintenance, and handling refrigerants with care.
Key Takeaways:
- Chillers are essential for achieving precise temperature control in plastic injection molding processing.
- Air-cooled and water-cooled chillers offer distinct advantages and disadvantages.
- Proper chiller sizing is crucial for optimal performance and energy efficiency.
- Different plastic processes require different types of chillers.
- Regular maintenance extends the lifespan and efficiency of your chiller.
We offer a comprehensive range of high-quality industrial chillers designed specifically for the demanding requirements of plastic processing. Neem contact met ons op today to learn more about our industriële waterkoeler solutions and how we can help you optimize your plastic manufacturing operations, using air or water as your cooling medium. We are also experts in industrial chillers for various applications, such as those used in the HVAC industry and for creating ice rinks. Our chillers are even suitable for specialized applications like dairy milk cooling or usage in a concrete batch plant. If you require solutions for cooling systems, process cooling, or other chiller cooling needs, we encourage you to reach out to us. Our team can help you select the right plastic chiller for your injection molding machines or other plastic process equipment, ensuring reliable cooling for your manufacturing process and maximizing your overall efficiency.
Helpcentrum
Heb je een vraag? Bekijk deze vraag en antwoorden
Water Chiller zijn als volgt:
- Ontwerp een goed gecontroleerde beoordelingsroutine voor uw koelmachine om de prestaties na verloop van tijd nauwkeurig te controleren.
- Blijf de spoelen en pijpleidingen controleren op ophoping van stof, calcium- of magnesiumionen of puin om dit tijdig te verwijderen en te voorkomen dat er een verstopping ontstaat.
- Houd de koudemiddelvulling altijd op peil en laat deze niet zakken, omdat dit de prestaties met 5-10% verlaagt.
- Routinematig onderhoud om condenserspoelen te onderzoeken op verstopte en vrije luchtgedeelten.
- Houd eventuele schadelijke middelen in de gaten en als je schade vindt, laat deze dan zo snel mogelijk repareren, zodat er geen langdurige gevolgen zijn.
- Zorg voor een goede watervoorziening en gebruik bij voorkeur gekoeld water.