-
Dalingshan Industrial Guangdong
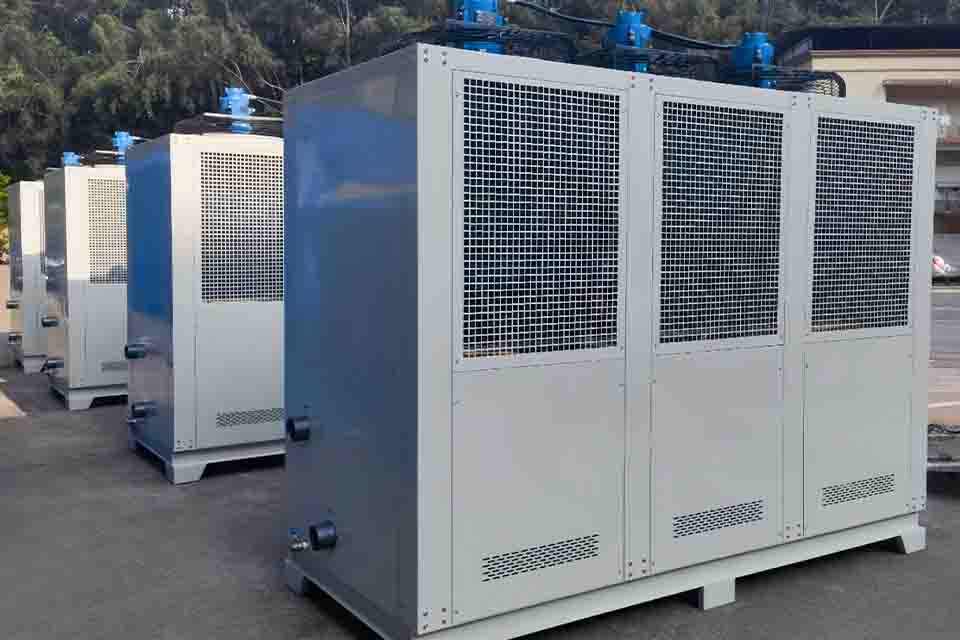
how do i choose my chiller
Choosing the Right Chiller: A Step-by-Step Guide for Your Application
This article provides a comprehensive guide on how to select a chiller that perfectly fits your needs, focusing on industrial applications. It covers the critical factors you must consider to ensure optimal performance, efficiency, and longevity of your chiller system. Whether you’re in the Plastics and Rubber Industry, Machining Industry, or any other sector requiring precise temperature control, this guide is designed to help you make an informed decision, ultimately leading to cost savings and improved operational efficiency. This article is a worthwhile read because it breaks down complex technical details into simple, understandable language, ensuring that even those new to koelmachines can grasp the essential concepts and make the best chiller choice for their specific requirements.
Inhoudsopgave
Wat is een industriële koelmachine en hoe werkt hij?
An industrial chiller is a refrigeration system that removes heat from a liquid via a vapor-compression or absorption refrigeration cycle. This cooled liquid then circulates through a heat exchanger to cool equipment or another process stream (such as air or process water). As a necessary component, refrigeration creates a continuous cycle of cooling and heat transfer.
In essence, a chiller functions by circulating a coolant, typically water or a water/glycol mixture, through a closed-loop system. The coolant absorbs heat from the process or equipment, which then flows to the chiller where the refrigerant within the chiller absorbs the heat. The compressor then increases the pressure and temperature of the refrigerant, which then flows to the condenser. Here, the heat is released, either to the ambient air in air-cooled chillers or to a separate water source in water-cooled systems. My experience has shown me that understanding this basic principle is crucial for anyone operating in an industrial setting.
Why is Selecting the Correctly Sized Chiller Crucial?
Selecting a correctly sized chiller is vital for maintaining optimal performance and efficiency in your operations. An undersized chiller will always struggle to meet the cooling demands, leading to inadequate koeling and potential damage to your process equipment and the process itself. My personal experience emphasizes that this can result in costly downtime and reduced productivity. This leads to issues where the chiller will never be able to properly cool the process equipment, leading to overheating and potential damage. Conversely, an oversized chiller will never operate at its peak efficiency, leading to higher energy consumption and unnecessary operational costs. Plus, the temperature will not be stable. The chiller might cool the process too quickly, leading to short cycling, where the chiller turns on and off frequently. This not only wastes energy but also puts extra wear and tear on the chiller’s components, reducing its lifespan. The oversized chiller will never be able to run at its rated capacity. Also, the initial investment for an oversized unit is higher, and it may require more space around the chiller for proper ventilation and maintenance, adding to the overall cost and complexity.
In simple terms, one size does not fit all. Getting the correct chiller size ensures that the system can handle the cooling load efficiently, maintaining the desired process water temperature and extending the lifespan of your equipment. An undersized chiller is like trying to cool a large room with a tiny fan – it simply won’t work efficiently. On the other hand, an oversized chiller is like using a massive air conditioner to cool a small closet – it’s overkill and wasteful. The correct size ensures that the chiller operates within its optimal range, providing efficient koeling without unnecessary strain.
What are the Main Types of Chillers?
Broadly speaking, koelmachines are categorized into two main types based on their heat rejection method: luchtgekoeld and water-cooled. Air-cooled chillers use ambient air to dissipate heat, while watergekoelde koelmachines use water from a cooling tower or other water source.
Air-cooled chillers are easy to install and require less maintenance than water-cooled systems. They are typically preferred in applications where water is scarce or where a simple, self-contained system is desired. Air-cooled chillers are typically used when the heat from the chiller can be exhausted directly outside. However, they can be less efficient in high ambient temperatures. My firsthand experience confirms that these chillers are ideal for smaller setups. These koelmachines use fans to blow ambient air across a condenser, which cools the refrigerant.
Feature | Luchtgekoelde chillers | Watergekoelde koelers |
Installation | Simpler, no need for a cooling tower | More complex, requires a cooling tower or water source |
Maintenance | Lower, fewer components to maintain | Higher, requires regular cleaning of cooling tower |
Efficiency | Generally lower, especially in high ambient temperatures | Generally higher, more consistent performance |
Space | Can be larger, requires clearance for airflow | Can be smaller, but requires space for cooling tower |
Noise | Louder due to fans | Quieter operation |
Water Usage | No water consumption | Requires a continuous water supply |
Toepassing | Suitable for smaller to medium cooling loads | Ideal for large cooling loads and high-heat environments |
Cost | Lower initial cost | Higher initial cost |
Energy Use | More in warm temperatures | Less, efficient cooling |
Indoor/Outdoor | Outdoor | Indoor |
Water-cooled chillers are more efficient than air-cooled units, especially in high ambient temperatures, because water is a more effective heat transfer medium than air. They require a separate koeling water source, which can be a cooling tower, a well, or a municipal water supply. Water-cooled chillers are generally more efficient because water has a higher heat capacity than air, meaning it can absorb more heat. These koelmachines circulate water through a condenser, which absorbs the heat from the refrigerant. The heated water is then pumped to a cooling tower where the heat is dissipated. Water-cooled chillers are ideal for large industrial applications where efficient koeling is critical and a reliable water source is available. While they require more maintenance, their energy efficiency often leads to lower operating costs in the long run. Additionally, they can be installed indoors, which protects them from weather elements and allows for easy inspection and maintenance. They are well-suited for large industrial applications where a reliable koeling source is available. From what I’ve seen, they are the go-to choice for large-scale operations. Also, watergekoelde koelmachines are typically placed indoors, while air-cooled chillers are usually placed outdoors.
How to Determine the Cooling Load for Your Application?
Determining the cooling load is a critical step in selecting the correct chiller size. The cooling load is the amount of heat that needs to be removed from the process or equipment to maintain the desired temperature. It’s usually measured in tons of refrigeration or BTUs per hour.
There are several methods to calculate the cooling load, including using the flow rate and temperature difference (inlet and outlet water) or by assessing the heat generated by the equipment itself. For instance, the formula to calculate the required chiller capacity based on water flow rate and temperature change is:
Cooling Load (BTU/hr) = Water Flow Rate (gallons/min) * 500 * (Inlet Water Temperature (°F) – Outlet Water Temperature (°F))
If the inlet water temperature is 65°F and the outlet water temperature is 55°F, and the rate of flow is 10 gallons per minute, then:
Cooling Load (BTU/hr) = 10 * 500 * (65 – 55) = 50,000 BTU/hr.
It’s crucial to consider all sources of heat generation within the process. In my experience, overlooking even minor heat sources can lead to an undersized system. When calculating koeling capacity, it is important to include a safety factor, typically around 20%, to account for variations in operating conditions and potential future expansion. This ensures that your chiller can handle unexpected increases in koeling demand without compromising performance. The goal is to help you make the best decision possible.
What Role Does Ambient Temperature Play in Chiller Selection?
Ambient air temperature significantly impacts chiller performance, particularly for luchtgekoeld units. In regions with high ambient temperatures, the chiller‘s ability to dissipate heat is reduced, requiring a larger chiller to achieve the same koeling capacity.
For instance, a chiller operating in a location with an average ambient air temperature of 95°F will need to work harder than one operating at 75°F. This is because the heat transfer efficiency decreases as the temperature difference between the refrigerant and the ambient air decreases. Therefore, it’s crucial to consider the maximum expected ambient temperature when selecting a chiller.
Ambient Temperature (°F) | Chiller Capacity Reduction (%) |
75 | 0 |
85 | 5 |
95 | 10 |
105 | 15 |
115 | 20 |
In my experience, customers in hotter climates often require a larger chiller to compensate for the reduced efficiency. It’s essential to consult with chiller manufacturers or experienced engineers to accurately account for ambient temperature variations. Remember, there may be other circumstances that affect your choice.
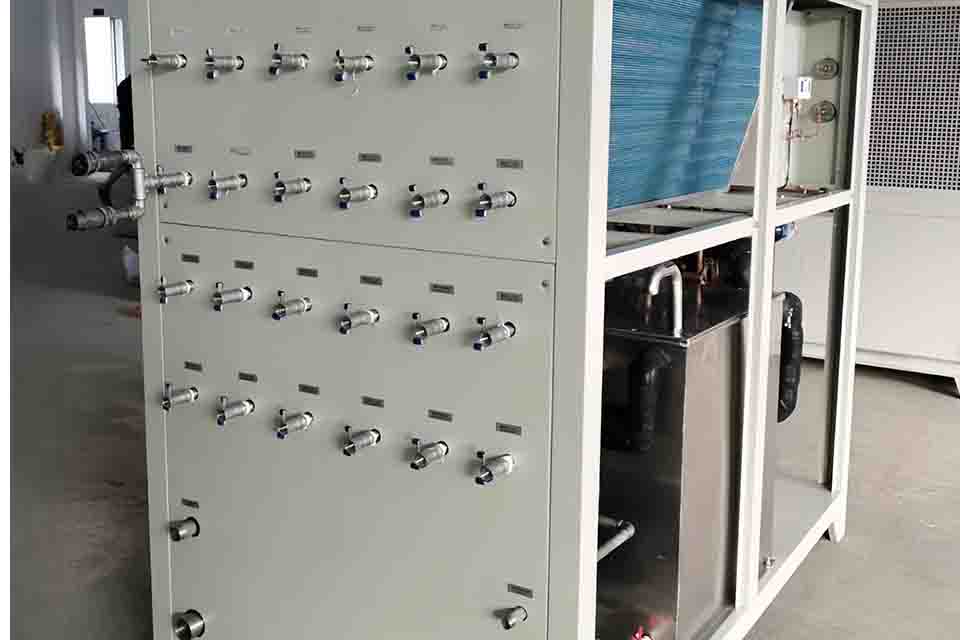
What is the Importance of Flow Rate and Pressure in a Chiller System?
The flow rate, or the volume of water circulated through the chiller per unit of time, is another critical factor. It directly impacts the chiller‘s ability to remove heat from the process. The correct flow rate ensures that the water spends enough time in the chiller to be cooled to the desired temperature.
The pressure the pump can deliver is also important, especially in systems with long hose runs or complex piping. Insufficient pressure can lead to reduced flow rates and inadequate koeling. It’s essential to select a chiller with a pump that can deliver the required flow rate across the system at the necessary pressure. In my experience, neglecting flow rate and pressure considerations can lead to significant performance issues.
Air-Cooled vs. Water-Cooled Chillers: Which is Right for You?
The choice between luchtgekoeld en watergekoelde koelmachines depends on various factors, including the application, the availability of water, the ambient temperature, and the desired efficiency.
Air-cooled chillers are generally simpler and have lower maintenance requirements, making them suitable for smaller applications or locations with limited water access. However, they are less efficient in high ambient temperatures. Water-cooled koelmachines offer higher efficiency and are preferred for larger industrial applications where koeling water is readily available. They are typically installed indoors and offer better performance in hot environments. I’ve often recommended watergekoelde koelmachines to clients with high koeling loads and access to a reliable water source.
Here are some additional factors to consider when choosing between luchtgekoeld en watergekoelde koelmachines:
- Noise: Air-cooled koelmachines are typically noisier than watergekoelde koelmachines because they use fans to dissipate heat. This can be a concern in noise-sensitive environments.
- Space: Air-cooled chillers require more space for ventilation than watergekoelde koelmachines.
- Corrosion: Water can be corrosive, which can shorten the lifespan of watergekoelde koelmachines if not properly maintained. Therefore, it is essential to monitor the water quality and use appropriate corrosion inhibitors.
How to Maintain and Troubleshoot Your Chiller?
Regular maintenance is crucial for ensuring the longevity and optimal performance of your chiller. This includes cleaning the condenser coils, checking refrigerant levels, inspecting the pump and piping for leaks, and monitoring the water quality. A used chiller requires even more attention.
Troubleshooting common issues, such as insufficient koeling, unusual noises, or leaks, often involves checking the flow rate, water temperature, and refrigerant levels. In many cases, these issues can be resolved by adjusting settings, cleaning components, or adding refrigerant. However, it’s always recommended to consult with a qualified technician for complex problems. My experience has taught me that proactive maintenance can prevent most issues and significantly extend the chiller‘s lifespan.
What are the Key Factors to Consider When Choosing a Chiller Manufacturer?
Selecting the correct manufacturer is as important as choosing the right chiller. Look for manufacturers with a proven track record, extensive experience in your industry, and a reputation for producing high-quality, reliable equipment.
Consider factors such as the manufacturer’s warranty, after-sales support, and the availability of spare parts. It’s also beneficial to choose a manufacturer that offers customization options to tailor the chiller to your specific needs. In my experience, working with a reputable manufacturer like us can make a significant difference in the overall performance and reliability of your chiller system.
Ready to Optimize Your Cooling System? Contact Us for Expert Guidance
Choosing the right chiller is a critical decision that impacts your operational efficiency, productivity, and bottom line. At Industrial Water Chiller Manufacturing Plants for products, we understand the complexities involved in selecting and sizing industrial chillers. With years of experience serving diverse industries, including Plastics and Rubber, Machining, Food and Beverage Industry, Chemical and Pharmaceutical, Electronics, Laser, Printing, Medical, Laboratories and Research Institutions, and Data Centers, we have the expertise to guide you through every step of the process.
Our team of experienced engineers can help you determine the optimal chiller size and type for your specific application, taking into account factors such as cooling load, ambient temperature, flow rate, and pressure requirements. We offer a wide range of koelmachines, including luchtgekoeld and water-cooled units, with various cooling capacities available to meet your unique needs.
We pride ourselves on providing personalized service and support, from initial consultation to installation and beyond. Our commitment to quality, reliability, and customer satisfaction sets us apart. We don’t just sell koelmachines; we provide comprehensive koeling solutions tailored to your specific needs.
Whether you need a standard unit or a customized system, we have the expertise and resources to deliver the perfect chiller for your application. Our website offers detailed information on a wide array of products including Air Cooled Screw Chillers, Industrial Chillers For Agriculture, Water Cooled Screw Central Chillers, Glycol chillers, HVAC Chillers, Water Cooled Screw Water Chiller, each designed to meet specific industrial needs. We’re here to help you make the best choice for your business. Let’s work together to optimize your cooling system and enhance your operational efficiency.
Neem contact met ons op today to discuss your koeling needs and discover how our expertise can benefit your operations.
FAQs
What is the difference between air-cooled and water-cooled chillers?
Air-cooled chillers use ambient air to remove heat, while water-cooled koelmachines use water. Water-cooled units are generally more efficient, especially in hot environments, but require a water source.
How do I determine the right size chiller for my application?
The correct size depends on the cooling load, which can be calculated based on the flow rate and temperature difference or the heat generated by your equipment.
What is the importance of flow rate in a chiller system?
Flow rate determines how quickly the water is cooled. The correct flow rate ensures the water spends enough time in the chiller to reach the desired temperature.
How does ambient temperature affect chiller performance?
High ambient temperatures reduce the efficiency of air-cooled chillers, requiring a larger unit to achieve the same koeling capacity.
What maintenance is required for chillers?
Regular maintenance includes cleaning condenser coils, checking refrigerant levels, inspecting pumps and piping, and monitoring water quality.
Why should I choose Industrial Water Chiller Manufacturing plants for products as my chiller supplier?
We have extensive experience, offer customized solutions, and are committed to quality and customer satisfaction. We provide comprehensive support from selection to installation and beyond.
Belangrijkste opmerkingen
- Selecting the correct chiller size is crucial for optimal performance and efficiency.
- Cooling load, ambient temperature, flow rate, and pressure are critical factors to consider.
- Air-cooled en watergekoelde koelmachines have distinct advantages and disadvantages.
- Regular maintenance is essential for extending chiller lifespan and preventing issues.
- Choosing a reputable manufacturer like us ensures quality, reliability, and expert support.
- There may be other circumstances to think about before making a decision.
By understanding these key concepts and partnering with experienced professionals, you can confidently select the right chiller for your application, ensuring efficient, reliable, and cost-effective koeling for years to come.
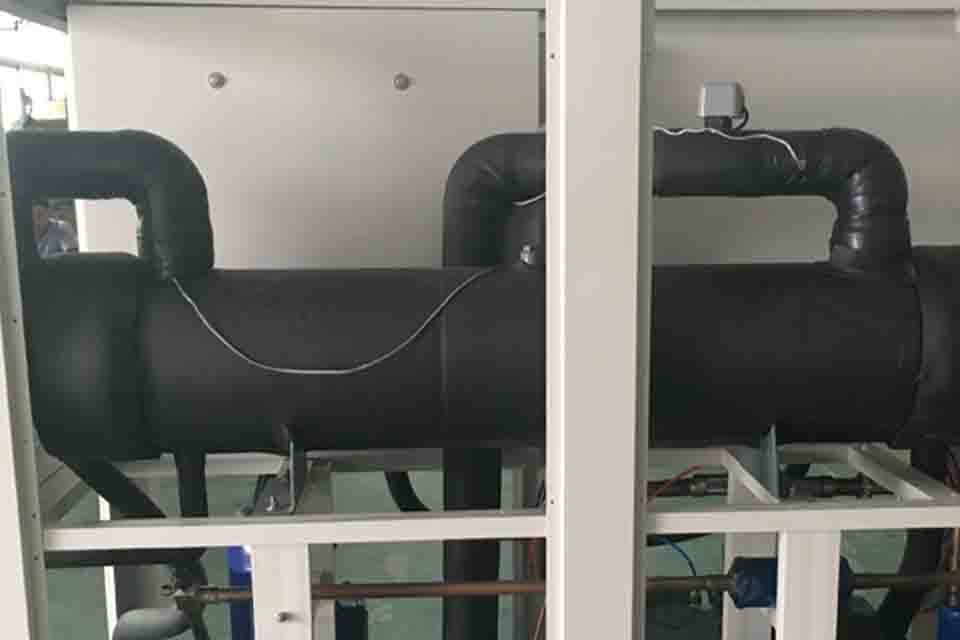