-
ഡാലിംഗ്ഷൻ ഇൻഡസ്ട്രിയൽ ഗ്വാങ്ഡോംഗ്
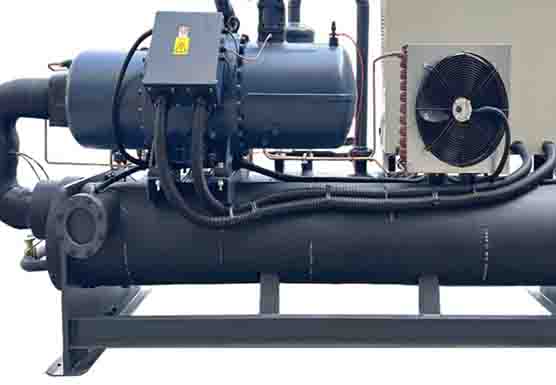
സാധാരണ ചില്ലർ പ്രശ്നങ്ങളും പരിഹാരങ്ങളും - ഒരു ട്രബിൾഷൂട്ടിംഗ് ഗൈഡ്
ചില്ലർ ട്രബിൾഷൂട്ടിംഗ് ഗൈഡ്: പൊതുവായ പ്രശ്നങ്ങളും പരിഹാരങ്ങളും കൈകാര്യം ചെയ്യൽ
വ്യാവസായിക വാട്ടർ ചില്ലറുകളിൽ നേരിടുന്ന സാധാരണ പ്രശ്നങ്ങൾ കണ്ടെത്തുന്നതിനും പരിഹരിക്കുന്നതിനുമുള്ള സമഗ്രമായ ഒരു ഗൈഡ് ഈ ലേഖനം വാഗ്ദാനം ചെയ്യുന്നു. നിങ്ങൾ പ്ലാസ്റ്റിക്, ഭക്ഷണം, പാനീയങ്ങൾ അല്ലെങ്കിൽ ഈ നിർണായക കൂളിംഗ് സിസ്റ്റങ്ങളെ ആശ്രയിക്കുന്ന മറ്റേതെങ്കിലും വ്യവസായത്തിൽ പ്രവർത്തിക്കുന്നവരായാലും, കാര്യക്ഷമത നിലനിർത്തുന്നതിനും, പ്രവർത്തനരഹിതമായ സമയം തടയുന്നതിനും, ചെലവേറിയ അറ്റകുറ്റപ്പണികൾ ഒഴിവാക്കുന്നതിനും സാധാരണ പ്രശ്നങ്ങൾ എങ്ങനെ പരിഹരിക്കാമെന്ന് മനസ്സിലാക്കേണ്ടത് അത്യാവശ്യമാണ്. ഇടയ്ക്കിടെയുള്ള ചില്ലർ തകരാറുകളും അവയുടെ പരിഹാരങ്ങളും പര്യവേക്ഷണം ചെയ്യുന്നതിലൂടെ, നിങ്ങളുടെ ചില്ലർ സിസ്റ്റം സുഗമമായും കാര്യക്ഷമമായും പ്രവർത്തിപ്പിക്കുന്നതിനുള്ള അറിവ് നിങ്ങൾക്ക് നൽകാൻ ഈ ഗൈഡ് ലക്ഷ്യമിടുന്നു. ചില്ലർ പ്രവർത്തനത്തെയും അറ്റകുറ്റപ്പണികളെയും കുറിച്ചുള്ള നിങ്ങളുടെ ഗ്രാഹ്യം വർദ്ധിപ്പിക്കുന്ന പ്രായോഗിക നുറുങ്ങുകളും ഉൾക്കാഴ്ചകളും കണ്ടെത്താൻ വായിക്കുക, വ്യാവസായിക തണുപ്പിക്കൽ പ്രക്രിയകളിൽ ഏർപ്പെട്ടിരിക്കുന്ന ആർക്കും ഈ ലേഖനം ഒരു വിലമതിക്കാനാവാത്ത ഉറവിടമാക്കി മാറ്റുന്നു.
ഉള്ളടക്ക പട്ടിക
വ്യാവസായിക വാട്ടർ ചില്ലർ സിസ്റ്റങ്ങളുടെ ആമുഖം
പ്ലാസ്റ്റിക്, റബ്ബർ വ്യവസായം, മെഷീനിംഗ്, ഭക്ഷ്യ പാനീയ സംസ്കരണം, കെമിക്കൽ, ഫാർമസ്യൂട്ടിക്കൽ നിർമ്മാണം, ഇലക്ട്രോണിക്സ്, ലേസർ സാങ്കേതികവിദ്യ, പ്രിന്റിംഗ്, മെഡിക്കൽ ആപ്ലിക്കേഷനുകൾ, ലബോറട്ടറികൾ, ഡാറ്റാ സെന്ററുകൾ എന്നിവയുൾപ്പെടെ വിവിധ മേഖലകളിലെ കൂളിംഗ് സിസ്റ്റങ്ങളുടെ നട്ടെല്ലാണ് വ്യാവസായിക വാട്ടർ ചില്ലറുകൾ. ഒരു ചില്ലർ നിർമ്മാതാവ് എന്ന നിലയിൽ, ഒപ്റ്റിമൽ പ്രോസസ് താപനില നിലനിർത്തുന്നതിലും ഉൽപ്പന്ന ഗുണനിലവാരം ഉറപ്പാക്കുന്നതിലും പ്രവർത്തന കാര്യക്ഷമത വർദ്ധിപ്പിക്കുന്നതിലും ഈ സംവിധാനങ്ങൾ എങ്ങനെ നിർണായക പങ്ക് വഹിക്കുന്നുവെന്ന് ഞാൻ നേരിട്ട് കണ്ടിട്ടുണ്ട്. ഒരു പ്രക്രിയയിൽ നിന്നോ ഉപകരണത്തിൽ നിന്നോ ചൂട് നീക്കം ചെയ്യുന്നതിനായി ഒരു കൂളന്റ് ദ്രാവകം, സാധാരണയായി വെള്ളം അല്ലെങ്കിൽ ഗ്ലൈക്കോൾ ലായനി, പ്രചരിപ്പിച്ചുകൊണ്ട് ഒരു ചില്ലർ സിസ്റ്റം പ്രവർത്തിക്കുന്നു. ചില്ലറിനുള്ളിലെ റഫ്രിജറന്റ് ഒരു റഫ്രിജറേഷൻ സൈക്കിളിന് വിധേയമാകുന്നു, കൂളന്റിൽ നിന്ന് ചൂട് ആഗിരണം ചെയ്ത് എയർ-കൂൾഡ് അല്ലെങ്കിൽ വാട്ടർ-കൂൾഡ് കണ്ടൻസർ വഴി പരിസ്ഥിതിയിലേക്ക് മാറ്റുന്നു.
ചില്ലർ സിസ്റ്റത്തിന്റെ മൂല്യം കേവലം താപനില നിയന്ത്രണത്തിനപ്പുറം വ്യാപിക്കുന്നു. ഇത് യന്ത്രങ്ങളെ അമിതമായി ചൂടാകുന്നതിൽ നിന്ന് സംരക്ഷിക്കുകയും ഉൽപ്പന്ന വൈകല്യങ്ങൾ തടയുകയും തണുപ്പിക്കൽ പ്രക്രിയ ഒപ്റ്റിമൈസ് ചെയ്യുന്നതിലൂടെ ഊർജ്ജ കാര്യക്ഷമത വർദ്ധിപ്പിക്കുകയും ചെയ്യുന്നു. ചില്ലർ പ്രവർത്തനത്തിന്റെ അടിസ്ഥാനകാര്യങ്ങൾ മനസ്സിലാക്കുന്നത് ഫലപ്രദമായ ട്രബിൾഷൂട്ടിംഗിന് അടിസ്ഥാനപരമാണ്. കംപ്രസ്സർ, കണ്ടൻസർ, ബാഷ്പീകരണം, എക്സ്പാൻഷൻ വാൽവ് തുടങ്ങിയ ഘടകങ്ങളുടെ പതിവ് പരിശോധനകൾ പല സാധാരണ ചില്ലർ പ്രശ്നങ്ങളും തടയാൻ കഴിയും. ഏതെങ്കിലും തകരാറുകൾക്കോ പിശക് കോഡുകൾക്കോ വേണ്ടി ചില്ലറിന്റെ ഡിസ്പ്ലേ യൂണിറ്റിൽ ശ്രദ്ധ പുലർത്തുന്നതും നിർണായകമാണ്.
എന്തുകൊണ്ടാണ് പതിവ് ചില്ലർ അറ്റകുറ്റപ്പണി പ്രധാനമായിരിക്കുന്നത്?
വിശ്വസനീയമായ ചില്ലർ പ്രവർത്തനത്തിന്റെ മൂലക്കല്ലാണ് ശരിയായ അറ്റകുറ്റപ്പണി. എന്റെ അനുഭവത്തിൽ, ചില്ലർ ട്രബിൾഷൂട്ടിംഗിലേക്ക് നയിക്കുന്ന നിരവധി പ്രശ്നങ്ങൾ അറ്റകുറ്റപ്പണികൾക്ക് മുൻകരുതൽ സമീപനത്തിലൂടെ ഒഴിവാക്കാനാകും. പതിവ് ചില്ലർ അറ്റകുറ്റപ്പണി എല്ലാ ഘടകങ്ങളും ശരിയായി പ്രവർത്തിക്കുന്നുണ്ടെന്ന് ഉറപ്പാക്കുന്നു, ഇത് ഉത്പാദനം നിർത്താനും ചെലവേറിയ അറ്റകുറ്റപ്പണികൾക്ക് കാരണമാകുന്ന അപ്രതീക്ഷിത പരാജയങ്ങളുടെ സാധ്യത കുറയ്ക്കുന്നു.
റഫ്രിജറന്റ് അളവ് പരിശോധിക്കൽ, ചോർച്ചയുണ്ടോയെന്ന് പരിശോധിക്കൽ, കണ്ടൻസർ കോയിലുകൾ വൃത്തിയാക്കൽ, പമ്പുകളുടെയും ഫാനുകളുടെയും ശരിയായ പ്രവർത്തനം പരിശോധിക്കൽ എന്നിവ പ്രതിരോധ അറ്റകുറ്റപ്പണികളിൽ ഉൾപ്പെടണം. ഈ ഘട്ടങ്ങൾ ചില്ലറിന്റെ ആയുസ്സ് വർദ്ധിപ്പിക്കുക മാത്രമല്ല, അതിന്റെ ഊർജ്ജ കാര്യക്ഷമത നിലനിർത്തുകയും ഊർജ്ജ ചെലവ് നിയന്ത്രിക്കുകയും ചെയ്യുന്നു. സ്ഥിരമായ തണുപ്പിക്കൽ പ്രകടനം ഉറപ്പാക്കാൻ ചില്ലർ ഔട്ട്ലെറ്റിലെ ഫ്ലോ റേറ്റും താപനിലയും നിരീക്ഷിക്കേണ്ടതും പ്രധാനമാണ്. നന്നായി ഘടനാപരമായ ഒരു അറ്റകുറ്റപ്പണി ഷെഡ്യൂൾ പാലിക്കുന്നതിലൂടെ, ബിസിനസുകൾക്ക് പ്രവർത്തനരഹിതമായ സമയം ഗണ്യമായി കുറയ്ക്കാനും അവരുടെ പ്രവർത്തനങ്ങളുടെ മൊത്തത്തിലുള്ള ഉൽപ്പാദനക്ഷമത വർദ്ധിപ്പിക്കാനും കഴിയും. ഞങ്ങളുടെ ലിങ്ക് പരിശോധിക്കുക. ഷെൽ ആൻഡ് ട്യൂബ് ഹീറ്റ് എക്സ്ചേഞ്ചർ നിങ്ങളുടെ കൂളിംഗ് സിസ്റ്റങ്ങൾ എങ്ങനെ ഒപ്റ്റിമൈസ് ചെയ്യാം എന്നതിനെക്കുറിച്ചുള്ള കൂടുതൽ വിവരങ്ങൾക്ക് പേജ്.
ചില്ലർ പ്രശ്നങ്ങളുടെ പൊതുവായ കാരണങ്ങൾ എന്തൊക്കെയാണ്?
വിവിധ വ്യവസായങ്ങളിൽ ഒപ്റ്റിമൽ താപനില നിലനിർത്തുന്നതിന് അത്യാവശ്യമായ ചില്ലറുകൾക്ക് അവയുടെ പ്രകടനത്തെ ബാധിക്കുന്ന നിരവധി പ്രശ്നങ്ങൾ നേരിടേണ്ടി വന്നേക്കാം. സമയബന്ധിതമായ ഇടപെടലിനും പരിഹാരത്തിനും ചില്ലർ പ്രശ്നങ്ങളുടെ ഈ സാധാരണ കാരണങ്ങൾ തിരിച്ചറിയുന്നത് നിർണായകമാണ്. മൂന്ന് പ്രാഥമിക വിഭാഗങ്ങളിൽ മിക്ക ചില്ലർ തകരാറുകളും ഉൾപ്പെടുന്നു: വൈദ്യുത പ്രശ്നങ്ങൾ, റഫ്രിജറന്റുമായി ബന്ധപ്പെട്ട പ്രശ്നങ്ങൾ, മെക്കാനിക്കൽ പരാജയങ്ങൾ.
ചില്ലർ സ്റ്റാർട്ട് ആകാത്ത സാഹചര്യത്തിലാണ് പലപ്പോഴും വൈദ്യുത പ്രശ്നങ്ങൾ പ്രത്യക്ഷപ്പെടുന്നത്. പൊട്ടിയ ഫ്യൂസ്, അയഞ്ഞ വയർ, അല്ലെങ്കിൽ ട്രിപ്പ് ചെയ്ത സർക്യൂട്ട് ബ്രേക്കർ എന്നിവ വൈദ്യുതി വിതരണത്തെ തടസ്സപ്പെടുത്തുകയും ചില്ലർ ഷട്ട്ഡൗൺ ആകാൻ കാരണമാവുകയും ചെയ്യും. വൈദ്യുത ഘടകങ്ങളുടെ പതിവ് പരിശോധനകളും കണക്ഷനുകളുടെ സമഗ്രത ഉറപ്പാക്കലും അത്തരം സംഭവങ്ങൾ തടയും.
റഫ്രിജറന്റുമായി ബന്ധപ്പെട്ട പ്രശ്നങ്ങളിൽ കുറഞ്ഞ റഫ്രിജറന്റ് അളവ്, റഫ്രിജറന്റ് ചോർച്ച, അല്ലെങ്കിൽ സിസ്റ്റത്തിലെ അമിതമായ റഫ്രിജറന്റ് എന്നിവ ഉൾപ്പെടുന്നു. ഈ അവസ്ഥകൾ ചില്ലറിന്റെ തണുപ്പിക്കൽ ശേഷിയും കാര്യക്ഷമതയും ഗണ്യമായി കുറയ്ക്കും. ഒപ്റ്റിമൽ ചില്ലർ പ്രകടനം നിലനിർത്തുന്നതിന് റഫ്രിജറന്റ് അളവ് പതിവായി നിരീക്ഷിക്കുകയും ഏതെങ്കിലും ചോർച്ചകൾ ഉടനടി പരിഹരിക്കുകയും ചെയ്യേണ്ടത് അത്യന്താപേക്ഷിതമാണ്.
കംപ്രസ്സർ, കണ്ടൻസർ, ബാഷ്പീകരണം അല്ലെങ്കിൽ വാൽവുകൾ പോലുള്ള ഘടകങ്ങൾ മെക്കാനിക്കൽ തകരാറുകൾക്ക് കാരണമാകാം. ഉദാഹരണത്തിന്, ഭാഗികമായി അടച്ച വാൽവ് അല്ലെങ്കിൽ അടഞ്ഞുപോയ ഫിൽട്ടർ ഡ്രയർ കൂളന്റിന്റെയോ റഫ്രിജറന്റിന്റെയോ ഒഴുക്കിനെ നിയന്ത്രിക്കും, ഇത് കാര്യക്ഷമമല്ലാത്ത പ്രവർത്തനത്തിലേക്കോ സിസ്റ്റം പരാജയത്തിലേക്കോ നയിക്കുന്നു. ഈ പൊതുവായ കാരണങ്ങൾ മനസ്സിലാക്കുന്നത് മികച്ച പ്രതിരോധ അറ്റകുറ്റപ്പണികൾക്കും വേഗത്തിലുള്ള ട്രബിൾഷൂട്ടിംഗിനും അനുവദിക്കുന്നു.
നിങ്ങളുടെ ചില്ലർ സ്റ്റാർട്ട് ആകാത്തപ്പോൾ എങ്ങനെ ട്രബിൾഷൂട്ട് ചെയ്യാം
ഒരു ചില്ലർ സ്റ്റാർട്ട് ആകാതെ വരുമ്പോൾ, അത് നിരാശാജനകമായ ഒരു അനുഭവമായിരിക്കും, പ്രത്യേകിച്ച് അത് നിർണായക പ്രവർത്തനങ്ങളെ തടസ്സപ്പെടുത്തുമ്പോൾ. ട്രബിൾഷൂട്ടിംഗിലെ ആദ്യപടി വൈദ്യുതി വിതരണം പരിശോധിക്കുക എന്നതാണ്. ചില്ലർ ശരിയായി ബന്ധിപ്പിച്ചിട്ടുണ്ടെന്നും സർക്യൂട്ട് ബ്രേക്കർ ട്രിപ്പ് ചെയ്തിട്ടില്ലെന്നും ഉറപ്പാക്കുക. പൊട്ടിയ ഫ്യൂസോ അയഞ്ഞ വയർ പോലുമോ ചില്ലർ സ്റ്റാർട്ട് ആകുന്നത് തടയാൻ കഴിയും.
വൈദ്യുതി വിതരണം കേടുകൂടാതെയിരിക്കുകയാണെങ്കിൽ, അടുത്ത ഘട്ടം കൺട്രോൾ പാനൽ പരിശോധിച്ച് എന്തെങ്കിലും പിശക് കോഡുകൾ ഉണ്ടോ എന്ന് പരിശോധിക്കുക എന്നതാണ്. ഈ കോഡുകൾക്ക് പ്രശ്നത്തിന്റെ സ്വഭാവത്തെക്കുറിച്ച് വിലപ്പെട്ട സൂചനകൾ നൽകാൻ കഴിയും. ഉദാഹരണത്തിന്, കുറഞ്ഞ റഫ്രിജറന്റുമായി ബന്ധപ്പെട്ട ഒരു പിശക് കോഡ് ഒരു ചോർച്ചയെ സൂചിപ്പിക്കാം, അതേസമയം ഉയർന്ന മർദ്ദം സൂചിപ്പിക്കുന്ന ഒരു കോഡ് ഒരു അടഞ്ഞ കണ്ടൻസറിനെ സൂചിപ്പിക്കാം.
ചില സന്ദർഭങ്ങളിൽ, സജീവമാക്കിയ ഒരു സുരക്ഷാ സ്വിച്ച് പോലെ ലളിതമായ ഒരു പ്രശ്നമുണ്ടാകാം. ചില്ലർ പുനഃസജ്ജമാക്കുന്നതിലൂടെയോ ജലപ്രവാഹ നിരക്ക് പരിശോധിക്കുന്നതിലൂടെയോ ചിലപ്പോൾ പ്രശ്നം പരിഹരിക്കാൻ കഴിയും. ഈ പരിശോധനകൾക്ക് ശേഷവും ചില്ലർ ആരംഭിക്കുന്നില്ലെങ്കിൽ, ഒരു പ്രൊഫഷണൽ ടെക്നീഷ്യനെ സമീപിക്കുന്നത് നല്ലതാണ്. സങ്കീർണ്ണമായ പ്രശ്നങ്ങൾ കണ്ടെത്തുന്നതിലും ചില്ലറിന് കൂടുതൽ കേടുപാടുകൾ സംഭവിക്കുന്നത് തടയുന്നതിലും അവരുടെ വൈദഗ്ദ്ധ്യം വിലമതിക്കാനാവാത്തതാണ്.
ചില്ലർ കൂളിംഗ് ശേഷിയിലെ പ്രശ്നങ്ങൾ പരിഹരിക്കൽ
ചില്ലറിന്റെ ഏറ്റവും സാധാരണമായ പ്രശ്നങ്ങളിലൊന്ന് കൂളിംഗ് ശേഷിയിലെ പ്രകടമായ കുറവാണ്. ഇത് പ്രോസസ്സ് താപനിലയിലെ ക്രമാനുഗതമായ വർദ്ധനവായോ അല്ലെങ്കിൽ ആവശ്യമുള്ള താപനില നിലനിർത്താൻ ചില്ലർ പാടുപെടുന്നതായോ പ്രകടമാകാം. കുറഞ്ഞ റഫ്രിജറന്റ് അളവ്, വൃത്തികെട്ടതോ അടഞ്ഞതോ ആയ കണ്ടൻസർ, അല്ലെങ്കിൽ തകരാറിലായ കംപ്രസ്സർ എന്നിവയുൾപ്പെടെ നിരവധി ഘടകങ്ങൾ ഈ പ്രശ്നത്തിന് കാരണമാകും.
കുറഞ്ഞ തണുപ്പിക്കൽ ശേഷി പരിഹരിക്കുന്നതിന്, റഫ്രിജറന്റ് ലെവൽ പരിശോധിച്ചുകൊണ്ട് ആരംഭിക്കുക. കുറഞ്ഞ റഫ്രിജറന്റ് ചില്ലറിന്റെ ഫലപ്രദമായി തണുപ്പിക്കാനുള്ള കഴിവിനെ സാരമായി ബാധിക്കും. ലെവൽ കുറവാണെങ്കിൽ, സിസ്റ്റം റീചാർജ് ചെയ്യുന്നതിന് മുമ്പ് ഏതെങ്കിലും റഫ്രിജറന്റ് ചോർച്ചകൾ തിരിച്ചറിഞ്ഞ് നന്നാക്കേണ്ടത് അത്യാവശ്യമാണ്.
തണുപ്പിക്കൽ ശേഷി കുറയാനുള്ള മറ്റൊരു സാധാരണ കാരണം വൃത്തികെട്ട കണ്ടൻസർ ആണ്. കണ്ടൻസർ കോയിലുകളിൽ പൊടിയും അവശിഷ്ടങ്ങളും അടിഞ്ഞുകൂടുകയും ചൂട് ഇല്ലാതാക്കാനുള്ള അവയുടെ കഴിവ് കുറയ്ക്കുകയും ചെയ്യും. കണ്ടൻസർ പതിവായി വൃത്തിയാക്കുന്നത് ഈ പ്രശ്നം തടയാനും മികച്ച കൂളിംഗ് പ്രകടനം ഉറപ്പാക്കാനും സഹായിക്കും.
റഫ്രിജറന്റുമായി ബന്ധപ്പെട്ട പ്രശ്നങ്ങൾ മനസ്സിലാക്കുകയും പരിഹരിക്കുകയും ചെയ്യുക
ഏതൊരു ചില്ലർ സിസ്റ്റത്തിന്റെയും ജീവരക്തമാണ് റഫ്രിജറന്റ്, അതുമായി ബന്ധപ്പെട്ട പ്രശ്നങ്ങൾ പ്രകടനത്തെ സാരമായി ബാധിക്കും. ഒരു സാധാരണ പ്രശ്നം കുറഞ്ഞ റഫ്രിജറന്റ് ലെവലാണ്, ഇത് റഫ്രിജറന്റ് ചോർച്ച മൂലമാകാം. ചോർച്ചയുടെ ലക്ഷണങ്ങളിൽ ഹിസ്സിംഗ് ശബ്ദങ്ങൾ, ഫിറ്റിംഗുകൾക്ക് ചുറ്റുമുള്ള എണ്ണമയമുള്ള അവശിഷ്ടങ്ങൾ അല്ലെങ്കിൽ തണുപ്പിക്കൽ ശേഷിയിൽ പ്രകടമായ കുറവ് എന്നിവ ഉൾപ്പെടുന്നു.
റഫ്രിജറന്റുമായി ബന്ധപ്പെട്ട പ്രശ്നങ്ങൾ പരിഹരിക്കുന്നതിന്, ആദ്യപടി ഏതെങ്കിലും ചോർച്ചകൾ കണ്ടെത്തി നന്നാക്കുക എന്നതാണ്. ഇതിൽ പലപ്പോഴും ഒരു ലീക്ക് ഡിറ്റക്ടർ ഉപയോഗിച്ച് ചോർച്ചയുടെ ഉറവിടം കൃത്യമായി കണ്ടെത്തുകയും തുടർന്ന് ബാധിച്ച ഘടകങ്ങൾ നന്നാക്കുകയോ മാറ്റിസ്ഥാപിക്കുകയോ ചെയ്യുന്നത് ഉൾപ്പെടുന്നു. ചോർച്ച പരിഹരിച്ചുകഴിഞ്ഞാൽ, ശരിയായ അളവിലുള്ള റഫ്രിജറന്റ് ഉപയോഗിച്ച് സിസ്റ്റം റീചാർജ് ചെയ്യാൻ കഴിയും.
സിസ്റ്റത്തിൽ വളരെയധികം റഫ്രിജറന്റ് ഉണ്ടാകാനും സാധ്യതയുണ്ട്, ഇത് ഉയർന്ന പ്രവർത്തന സമ്മർദ്ദം, കാര്യക്ഷമത കുറയൽ തുടങ്ങിയ പ്രശ്നങ്ങൾക്ക് കാരണമാകും. അത്തരം സന്ദർഭങ്ങളിൽ, യോഗ്യതയുള്ള ഒരു ടെക്നീഷ്യൻ അധിക റഫ്രിജറന്റ് നീക്കം ചെയ്യേണ്ടതുണ്ട്. റഫ്രിജറന്റ് ലെവലുകളും മർദ്ദവും പതിവായി നിരീക്ഷിക്കുന്നത് ഈ പ്രശ്നങ്ങൾ തടയാനും ഒപ്റ്റിമൽ ചില്ലർ പ്രവർത്തനം ഉറപ്പാക്കാനും സഹായിക്കും.
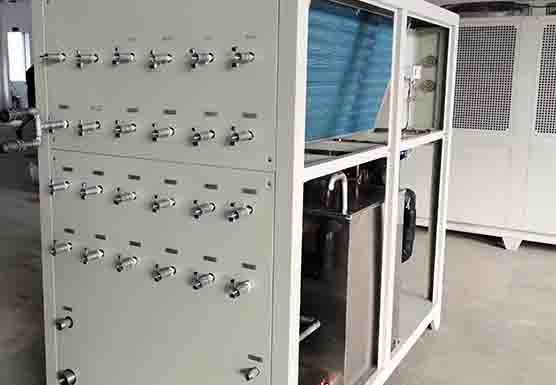
കംപ്രസ്സർ പ്രശ്നങ്ങൾ: രോഗനിർണയവും പരിഹാരങ്ങളും
കംപ്രസ്സർ ചില്ലറിന്റെ ഹൃദയഭാഗമാണ്, സിസ്റ്റത്തിലുടനീളം റഫ്രിജറന്റ് പ്രചരിക്കുന്നതിന് ഇത് ഉത്തരവാദിയാണ്. കംപ്രസ്സറിലെ പ്രശ്നങ്ങൾ തണുപ്പിക്കൽ ശേഷി കുറയുന്നത് മുതൽ സിസ്റ്റം പൂർണ്ണമായി പരാജയപ്പെടുന്നത് വരെ നിരവധി പ്രശ്നങ്ങൾക്ക് കാരണമാകും. വൈദ്യുത തകരാറുകൾ, മെക്കാനിക്കൽ തേയ്മാനം, എണ്ണ പ്രശ്നങ്ങൾ എന്നിവയാണ് സാധാരണ കംപ്രസ്സർ പ്രശ്നങ്ങളിൽ ഉൾപ്പെടുന്നത്.
കംപ്രസ്സർ പ്രശ്നങ്ങൾ നിർണ്ണയിക്കാൻ, ആദ്യം വൈദ്യുത കണക്ഷനുകൾ പരിശോധിച്ച് കംപ്രസ്സറിന് വൈദ്യുതി ലഭിക്കുന്നുണ്ടെന്ന് ഉറപ്പാക്കുക. ഒരു ട്രിപ്പ് ബ്രേക്കറോ അയഞ്ഞ വയർ കംപ്രസ്സർ സ്റ്റാർട്ട് ചെയ്യുന്നത് തടയും. ഇലക്ട്രിക്കൽ സിസ്റ്റം കേടുകൂടാതെയിരിക്കുകയാണെങ്കിൽ, പൊടിക്കുകയോ മുട്ടുകയോ ചെയ്യുന്ന ശബ്ദങ്ങൾ പോലുള്ള അസാധാരണമായ ശബ്ദങ്ങൾ കംപ്രസ്സറിൽ നിന്ന് കേൾക്കുക. ഇവ മെക്കാനിക്കൽ തേയ്മാനമോ ആന്തരിക നാശമോ സൂചിപ്പിക്കാം.
എണ്ണയുടെ അളവ് കുറയുകയോ മലിനമായ എണ്ണ പോലുള്ള എണ്ണ പ്രശ്നങ്ങളും കംപ്രസ്സറിന്റെ പ്രകടനത്തെ ബാധിച്ചേക്കാം. പതിവായി എണ്ണ പരിശോധിച്ച് മാറ്റുന്നത് ഈ പ്രശ്നങ്ങൾ തടയും. കംപ്രസ്സർ തകരാറിലാണെന്ന് കണ്ടെത്തിയാൽ, അത് നന്നാക്കുകയോ യോഗ്യതയുള്ള ഒരു ടെക്നീഷ്യനെക്കൊണ്ട് മാറ്റി സ്ഥാപിക്കുകയോ ചെയ്യേണ്ടി വന്നേക്കാം.
കണ്ടൻസർ പ്രശ്നങ്ങൾ: തണുപ്പ് നിലനിർത്തൽ
റഫ്രിജറന്റിൽ നിന്ന് പരിസ്ഥിതിയിലേക്ക് താപം പുറന്തള്ളുന്നതിലൂടെ റഫ്രിജറേഷൻ ചക്രത്തിൽ കണ്ടൻസർ നിർണായക പങ്ക് വഹിക്കുന്നു. കണ്ടൻസറിലെ പ്രശ്നങ്ങൾ തണുപ്പിക്കൽ ശേഷി കുറയുന്നതിനും, ഊർജ്ജ ഉപഭോഗം വർദ്ധിക്കുന്നതിനും, സിസ്റ്റം പരാജയപ്പെടുന്നതിനും കാരണമാകും. ഒരു സാധാരണ പ്രശ്നം വൃത്തികെട്ടതോ അടഞ്ഞതോ ആയ കണ്ടൻസർ ആണ്, ഇത് വായുപ്രവാഹത്തെ നിയന്ത്രിക്കുകയും താപ കൈമാറ്റം കുറയ്ക്കുകയും ചെയ്യുന്നു.
കണ്ടൻസർ തണുപ്പായി നിലനിർത്താൻ, പതിവായി വൃത്തിയാക്കൽ അത്യാവശ്യമാണ്. പൊടി, അവശിഷ്ടങ്ങൾ, മറ്റ് മാലിന്യങ്ങൾ എന്നിവ കണ്ടൻസർ കോയിലുകളിൽ അടിഞ്ഞുകൂടുകയും ചൂട് ഇല്ലാതാക്കാനുള്ള അവയുടെ കഴിവ് കുറയ്ക്കുകയും ചെയ്യും. ബ്രഷ് അല്ലെങ്കിൽ കംപ്രസ് ചെയ്ത വായു ഉപയോഗിച്ച് കോയിലുകൾ വൃത്തിയാക്കുന്നത് വായുപ്രവാഹം മെച്ചപ്പെടുത്തുകയും തണുപ്പിക്കൽ പ്രകടനം മെച്ചപ്പെടുത്തുകയും ചെയ്യും.
ശ്രദ്ധിക്കേണ്ട മറ്റൊരു പ്രശ്നം ഉയർന്ന അന്തരീക്ഷ താപനിലയാണ്. ചില്ലറിന് ചുറ്റുമുള്ള പരിസ്ഥിതി വളരെ ചൂടുള്ളതാണെങ്കിൽ, കണ്ടൻസർ ഫലപ്രദമായി ചൂട് പുറന്തള്ളാൻ പാടുപെടും. മതിയായ വായുസഞ്ചാരം ഉറപ്പാക്കുകയും ചില്ലറിന് ചുറ്റുമുള്ള പ്രദേശം തണുപ്പായി നിലനിർത്തുകയും ചെയ്യുന്നത് ഈ പ്രശ്നം തടയാൻ സഹായിക്കും.
ബാഷ്പീകരണ പ്രശ്നങ്ങൾ: ഒപ്റ്റിമൽ താപ വിനിമയം ഉറപ്പാക്കൽ
പ്രോസസ്സ് ഫ്ലൂയിഡിൽ നിന്ന് താപം ആഗിരണം ചെയ്ത് റഫ്രിജറന്റ് ആവശ്യമുള്ള താപനിലയിലേക്ക് തണുപ്പിക്കുന്ന സ്ഥലമാണ് ഇവാപ്പറേറ്റർ. ഇവാപ്പറേറ്ററിലെ പ്രശ്നങ്ങൾ തണുപ്പിക്കൽ ശേഷി കുറയുന്നതിനും കാര്യക്ഷമമല്ലാത്ത പ്രവർത്തനത്തിനും കാരണമാകും. ഇവാപ്പറേറ്റർ കോയിലുകളിൽ ഐസ് അടിഞ്ഞുകൂടുന്നത് ഒരു സാധാരണ പ്രശ്നമാണ്, ഇത് വായുപ്രവാഹത്തെ നിയന്ത്രിക്കുകയും താപ കൈമാറ്റം കുറയ്ക്കുകയും ചെയ്യും.
ഐസ് അടിഞ്ഞുകൂടുന്നത് തടയാൻ, ചില്ലർ അതിന്റെ നിർദ്ദിഷ്ട താപനില പരിധിക്കുള്ളിൽ പ്രവർത്തിക്കുന്നുണ്ടെന്നും പ്രോസസ്സ് ദ്രാവകത്തിന്റെ ഒഴുക്ക് നിരക്ക് ശരിയാണെന്നും ഉറപ്പാക്കുക. ഐസ് രൂപപ്പെടുകയാണെങ്കിൽ, ഭാവിയിൽ ഐസ് രൂപപ്പെടുന്നത് തടയാൻ ബാഷ്പീകരണി സ്വമേധയാ ഡീഫ്രോസ്റ്റ് ചെയ്യുകയോ ചില്ലറിന്റെ ക്രമീകരണങ്ങൾ ക്രമീകരിക്കുകയോ ചെയ്യേണ്ടി വന്നേക്കാം.
മറ്റൊരു ശ്രദ്ധിക്കേണ്ട പ്രശ്നം അടഞ്ഞുപോയതോ വൃത്തികെട്ടതോ ആയ ബാഷ്പീകരണ യന്ത്രമാണ്. ബാഷ്പീകരണ യന്ത്ര കോയിലുകളിൽ അഴുക്കും അവശിഷ്ടങ്ങളും അടിഞ്ഞുകൂടുകയും ചൂട് ആഗിരണം ചെയ്യാനുള്ള അവയുടെ കഴിവ് കുറയ്ക്കുകയും ചെയ്യും. ബാഷ്പീകരണ യന്ത്രം പതിവായി വൃത്തിയാക്കുന്നത് ഈ പ്രശ്നം തടയാനും ഒപ്റ്റിമൽ താപ കൈമാറ്റം ഉറപ്പാക്കാനും സഹായിക്കും.
ചില്ലർ കാര്യക്ഷമതയിൽ വാൽവുകളുടെ പങ്ക്
ചില്ലർ സിസ്റ്റത്തിനുള്ളിലെ റഫ്രിജറന്റിന്റെയും പ്രോസസ്സ് ദ്രാവകത്തിന്റെയും ഒഴുക്ക് നിയന്ത്രിക്കുന്നതിൽ വാൽവുകൾ നിർണായക പങ്ക് വഹിക്കുന്നു. തകരാറുള്ള ഒരു വാൽവ് തണുപ്പിക്കൽ ശേഷി കുറയുന്നത് മുതൽ സിസ്റ്റം പരാജയം വരെ നിരവധി പ്രശ്നങ്ങൾക്ക് കാരണമാകും. ഒരു സാധാരണ പ്രശ്നം ഭാഗികമായി അടഞ്ഞ വാൽവാണ്, ഇത് ഒഴുക്ക് നിയന്ത്രിക്കുകയും കാര്യക്ഷമത കുറയ്ക്കുകയും ചെയ്യുന്നു.
ചില്ലറിന്റെ കാര്യക്ഷമത ഉറപ്പാക്കാൻ, വാൽവുകൾ പതിവായി പരിശോധിക്കുകയും പരിപാലിക്കുകയും ചെയ്യേണ്ടത് അത്യാവശ്യമാണ്. ചോർച്ചയുടെയോ കേടുപാടുകളുടെയോ ലക്ഷണങ്ങൾ ഉണ്ടോയെന്ന് പരിശോധിക്കുക, ആവശ്യാനുസരണം വാൽവുകൾ പൂർണ്ണമായും തുറന്നിട്ടുണ്ടോ അല്ലെങ്കിൽ അടച്ചിട്ടുണ്ടോ എന്ന് ഉറപ്പാക്കുക. ഒരു വാൽവ് തകരാറിലാണെന്ന് കണ്ടെത്തിയാൽ, അത് നന്നാക്കുകയോ മാറ്റിസ്ഥാപിക്കുകയോ ചെയ്യേണ്ടി വന്നേക്കാം.
മറ്റൊരു ശ്രദ്ധിക്കേണ്ട പ്രശ്നം വാൽവ് സ്റ്റക്ക് ആണ്, ഇത് റഫ്രിജറന്റിന്റെയോ പ്രോസസ്സ് ദ്രാവകത്തിന്റെയോ ഒഴുക്ക് പൂർണ്ണമായും തടയും. ഇത് സിസ്റ്റം പൂർണ്ണമായും ഷട്ട്ഡൗൺ ചെയ്യാൻ ഇടയാക്കും, പരിഹരിക്കാൻ പ്രൊഫഷണൽ ഇടപെടൽ ആവശ്യമായി വന്നേക്കാം.
വിപുലമായ ട്രബിൾഷൂട്ടിംഗ്: എപ്പോൾ പ്രൊഫഷണൽ സഹായം തേടണം
ചില്ലറിന്റെ പല സാധാരണ പ്രശ്നങ്ങളും അടിസ്ഥാന ട്രബിൾഷൂട്ടിംഗ് വഴി പരിഹരിക്കാമെങ്കിലും, ചില സമയങ്ങളിൽ പ്രൊഫഷണൽ സഹായം തേടുന്നതാണ് നല്ലത്. കംപ്രസർ പരാജയം, പ്രധാന റഫ്രിജറന്റ് ചോർച്ച, അല്ലെങ്കിൽ നിയന്ത്രണ സംവിധാനത്തിലെ പ്രശ്നങ്ങൾ തുടങ്ങിയ സങ്കീർണ്ണമായ പ്രശ്നങ്ങൾക്ക് പലപ്പോഴും യോഗ്യതയുള്ള ഒരു ടെക്നീഷ്യന്റെ വൈദഗ്ദ്ധ്യം ആവശ്യമാണ്.
എല്ലാ അടിസ്ഥാന ട്രബിൾഷൂട്ടിംഗ് ഘട്ടങ്ങളും നിങ്ങൾ പൂർത്തിയാക്കിയിട്ടും ചില്ലർ ഇപ്പോഴും ശരിയായി പ്രവർത്തിക്കുന്നില്ലെങ്കിൽ, ഒരു പ്രൊഫഷണലിനെ വിളിക്കേണ്ട സമയമാണിത്. ശരിയായ പരിശീലനവും ഉപകരണങ്ങളും ഇല്ലാതെ സങ്കീർണ്ണമായ പ്രശ്നങ്ങൾ പരിഹരിക്കാൻ ശ്രമിക്കുന്നത് കൂടുതൽ കേടുപാടുകൾക്കും അറ്റകുറ്റപ്പണി ചെലവ് വർദ്ധിപ്പിക്കുന്നതിനും ഇടയാക്കും.
ഒരു യോഗ്യതയുള്ള ടെക്നീഷ്യന് പ്രശ്നം കൃത്യമായി നിർണ്ണയിക്കാനും ഏറ്റവും മികച്ച നടപടി ശുപാർശ ചെയ്യാനും കഴിയും. അവർക്ക് ആവശ്യമായ അറ്റകുറ്റപ്പണികൾ നടത്താനും ചില്ലർ സുരക്ഷിതമായും കാര്യക്ഷമമായും പ്രവർത്തിക്കുന്നുണ്ടെന്ന് ഉറപ്പാക്കാനും കഴിയും.
പതിവായി ചോദിക്കുന്ന ചോദ്യങ്ങൾ (പതിവ് ചോദ്യങ്ങൾ)
എന്റെ ചില്ലർ ശരിയായി തണുക്കുന്നില്ലെങ്കിൽ ഞാൻ എന്തുചെയ്യണം?
നിങ്ങളുടെ ചില്ലർ ശരിയായി തണുപ്പിക്കുന്നില്ലെങ്കിൽ, റഫ്രിജറന്റ് ലെവലുകൾ പരിശോധിച്ചുകൊണ്ട് ആരംഭിക്കുക. കുറഞ്ഞ റഫ്രിജറന്റ് കൂളിംഗ് പ്രകടനത്തെ സാരമായി ബാധിക്കും. കൂടാതെ, കണ്ടൻസറും ബാഷ്പീകരണിയും അഴുക്കോ തടസ്സങ്ങളോ ഉണ്ടോയെന്ന് പരിശോധിക്കുക. വൃത്തിയുള്ള ഒരു കണ്ടൻസറും ബാഷ്പീകരണിയും കാര്യക്ഷമമായ താപ കൈമാറ്റം ഉറപ്പാക്കുന്നു. ഈ ഘട്ടങ്ങൾ പ്രശ്നം പരിഹരിക്കുന്നില്ലെങ്കിൽ, കംപ്രസ്സറിലോ വാൽവുകളിലോ പ്രശ്നങ്ങൾ ഉണ്ടാകാം, ഒരു പ്രൊഫഷണലിനെ സമീപിക്കുന്നത് നല്ലതാണ്.
എന്റെ ചില്ലറിൽ എത്ര തവണ ഞാൻ അറ്റകുറ്റപ്പണി നടത്തണം?
നിങ്ങളുടെ ചില്ലർ സുഗമമായി പ്രവർത്തിക്കുന്നതിന് പതിവ് അറ്റകുറ്റപ്പണി നിർണായകമാണ്. ചോർച്ചയുണ്ടോയെന്ന് പരിശോധിക്കുക, കണ്ടൻസർ വൃത്തിയാക്കുക തുടങ്ങിയ അടിസ്ഥാന പരിശോധനകൾ കുറഞ്ഞത് മൂന്ന് മാസത്തിലൊരിക്കലെങ്കിലും നടത്തണം. റഫ്രിജറന്റ് ലെവലുകൾ പരിശോധിക്കുക, ഇലക്ട്രിക്കൽ ഘടകങ്ങൾ പരിശോധിക്കുക എന്നിവയുൾപ്പെടെ കൂടുതൽ സമഗ്രമായ പരിശോധന ഒരു യോഗ്യതയുള്ള ടെക്നീഷ്യൻ വർഷം തോറും നടത്തണം. ശരിയായ അറ്റകുറ്റപ്പണി ഏറ്റവും സാധാരണമായ ചില്ലർ പ്രശ്നങ്ങൾ തടയാനും നിങ്ങളുടെ യൂണിറ്റിന്റെ ആയുസ്സ് വർദ്ധിപ്പിക്കാനും കഴിയും.
റഫ്രിജറന്റ് ചോർച്ചയുടെ ലക്ഷണങ്ങൾ എന്തൊക്കെയാണ്?
റഫ്രിജറന്റ് ചോർച്ചയുടെ ലക്ഷണങ്ങളിൽ ചില്ലറിന് സമീപമുള്ള ഹിസ്സിംഗ് ശബ്ദങ്ങൾ, ഫിറ്റിംഗുകൾക്ക് ചുറ്റുമുള്ള എണ്ണമയമുള്ള അവശിഷ്ടങ്ങൾ, അല്ലെങ്കിൽ കൂളിംഗ് ശേഷിയിൽ പ്രകടമായ കുറവ് എന്നിവ ഉൾപ്പെടുന്നു. ബാഷ്പീകരണ കോയിലുകളിൽ ഐസ് അടിഞ്ഞുകൂടുന്നതും നിങ്ങൾ കണ്ടേക്കാം. ചോർച്ചയുണ്ടെന്ന് നിങ്ങൾ സംശയിക്കുന്നുവെങ്കിൽ, ഉറവിടം സ്ഥിരീകരിക്കാനും കൃത്യമായി കണ്ടെത്താനും ഒരു ലീക്ക് ഡിറ്റക്ടർ ഉപയോഗിക്കുക. ചില്ലറിന്റെ കാര്യക്ഷമത നിലനിർത്തുന്നതിനും കൂടുതൽ നാശനഷ്ടങ്ങൾ തടയുന്നതിനും ചോർച്ചകൾ ഉടനടി പരിഹരിക്കേണ്ടത് നിർണായകമാണ്.
എന്റെ ചില്ലറിന്റെ പ്രശ്നം എനിക്ക് തന്നെ പരിഹരിക്കാൻ കഴിയുമോ, അതോ എപ്പോഴും ഒരു പ്രൊഫഷണലിനെ വിളിക്കണോ?
പവർ സപ്ലൈ പരിശോധിക്കൽ, കണ്ടൻസർ വൃത്തിയാക്കൽ, പിശക് കോഡുകൾ പരിശോധിക്കൽ തുടങ്ങിയ നിരവധി അടിസ്ഥാന ട്രബിൾഷൂട്ടിംഗ് ഘട്ടങ്ങൾ ഓപ്പറേറ്റർക്ക് തന്നെ നിർവഹിക്കാൻ കഴിയും. എന്നിരുന്നാലും, കംപ്രസർ പരാജയം, പ്രധാന റഫ്രിജറന്റ് ചോർച്ചകൾ അല്ലെങ്കിൽ നിയന്ത്രണ സിസ്റ്റം പ്രശ്നങ്ങൾ പോലുള്ള സങ്കീർണ്ണമായ പ്രശ്നങ്ങൾ ഒരു യോഗ്യതയുള്ള ടെക്നീഷ്യൻ കൈകാര്യം ചെയ്യണം. ശരിയായ പരിശീലനമില്ലാതെ ഈ പ്രശ്നങ്ങൾ പരിഹരിക്കാൻ ശ്രമിക്കുന്നത് കൂടുതൽ നാശത്തിലേക്ക് നയിച്ചേക്കാം.
ചില്ലർ അസാധാരണമായ ശബ്ദങ്ങൾ പുറപ്പെടുവിക്കാൻ കാരണമെന്താണ്?
ചില്ലറിൽ നിന്നുള്ള അസാധാരണമായ ശബ്ദങ്ങൾ വിവിധ പ്രശ്നങ്ങളെ സൂചിപ്പിക്കാം. ഉദാഹരണത്തിന്, പൊടിക്കുന്നതോ മുട്ടുന്നതോ ആയ ശബ്ദങ്ങൾ കംപ്രസ്സറിലെ മെക്കാനിക്കൽ തേയ്മാനം അല്ലെങ്കിൽ ആന്തരിക കേടുപാടുകൾ പോലുള്ള പ്രശ്നങ്ങളെ സൂചിപ്പിക്കാം. ഹിസ്സിംഗ് ശബ്ദങ്ങൾ റഫ്രിജറന്റ് ചോർച്ചയെ സൂചിപ്പിക്കാം. അസാധാരണമായ ശബ്ദങ്ങൾ കേട്ടാൽ, ചില്ലർ ഓഫ് ചെയ്ത് അയഞ്ഞ ഭാഗങ്ങൾ അല്ലെങ്കിൽ തടസ്സങ്ങൾ പോലുള്ള വ്യക്തമായ പ്രശ്നങ്ങൾ പരിശോധിക്കുക. കാരണം വ്യക്തമല്ലെങ്കിൽ, ഒരു പ്രൊഫഷണലിനെ സമീപിക്കുന്നതാണ് നല്ലത്.
എന്റെ ചില്ലറിന്റെ ഊർജ്ജ കാര്യക്ഷമത എങ്ങനെ മെച്ചപ്പെടുത്താം?
നിങ്ങളുടെ ചില്ലറിന്റെ ഊർജ്ജക്ഷമത മെച്ചപ്പെടുത്തുന്നതിന് നിരവധി രീതികൾ ആവശ്യമാണ്. ശരിയായ വായുപ്രവാഹം പ്രോത്സാഹിപ്പിക്കുന്നതിന് കണ്ടൻസർ വൃത്തിയുള്ളതും തടസ്സങ്ങളില്ലാത്തതുമാണെന്ന് ഉറപ്പാക്കുക. റഫ്രിജറന്റ് ലെവലുകൾ ശുപാർശ ചെയ്യുന്ന പരിധിക്കുള്ളിലാണെന്ന് ഉറപ്പാക്കാൻ പതിവായി പരിശോധിക്കുകയും നിലനിർത്തുകയും ചെയ്യുക. കൂടാതെ, എല്ലാ വാൽവുകളും ശരിയായി പ്രവർത്തിക്കുന്നുണ്ടെന്നും ആവശ്യാനുസരണം പൂർണ്ണമായും തുറന്നിട്ടുണ്ടോ അല്ലെങ്കിൽ അടച്ചിട്ടുണ്ടോ എന്നും പരിശോധിക്കുക. ഒരു പ്രതിരോധ അറ്റകുറ്റപ്പണി ഷെഡ്യൂൾ നടപ്പിലാക്കുന്നത് കാര്യക്ഷമത നിലനിർത്താനും ഊർജ്ജ ചെലവ് കുറയ്ക്കാനും സഹായിക്കും.
തീരുമാനം
സാധാരണ ചില്ലർ പ്രശ്നങ്ങൾ പരിഹരിക്കുന്നതിനുള്ള ഈ സമഗ്ര ഗൈഡിൽ നിന്നുള്ള ഏറ്റവും പ്രധാനപ്പെട്ട കാര്യങ്ങൾ ഇതാ:
- പതിവ് അറ്റകുറ്റപ്പണി പ്രധാനമാണ്: റഫ്രിജറന്റ് അളവ് പരിശോധിക്കൽ, കണ്ടൻസർ വൃത്തിയാക്കൽ, വാൽവുകൾ പരിശോധിക്കൽ എന്നിവയുൾപ്പെടെയുള്ള പ്രതിരോധ അറ്റകുറ്റപ്പണികൾ, സാധാരണ പ്രശ്നങ്ങൾ തടയുന്നതിനും നിങ്ങളുടെ ചില്ലറിന്റെ ആയുസ്സ് വർദ്ധിപ്പിക്കുന്നതിനും നിർണായകമാണ്.
- മൂലകാരണം തിരിച്ചറിയുക: ട്രബിൾഷൂട്ടിംഗ് നടത്തുമ്പോൾ, പവർ സപ്ലൈ, എറർ കോഡുകൾ തുടങ്ങിയ അടിസ്ഥാനകാര്യങ്ങളിൽ നിന്ന് ആരംഭിക്കുക, തുടർന്ന് കംപ്രസർ, വാൽവുകൾ പോലുള്ള കൂടുതൽ സങ്കീർണ്ണമായ ഘടകങ്ങളിലേക്ക് നീങ്ങുക.
- റഫ്രിജറന്റ് വസ്തുക്കൾ: റഫ്രിജറന്റ് ലെവലുകൾ ശരിയായി കൈകാര്യം ചെയ്യുന്നതും ചോർച്ചകൾ ഉടനടി പരിഹരിക്കുന്നതും ചില്ലറിന്റെ പ്രകടനത്തെയും കാര്യക്ഷമതയെയും സാരമായി ബാധിക്കും.
- ശുചിത്വ കണക്കുകൾ: കണ്ടൻസറും ബാഷ്പീകരണിയും വൃത്തിയായി സൂക്ഷിക്കുന്നത് ഒപ്റ്റിമൽ താപ കൈമാറ്റം ഉറപ്പാക്കുകയും തണുപ്പിക്കൽ ശേഷി കുറയുക, ഐസ് അടിഞ്ഞുകൂടൽ തുടങ്ങിയ പ്രശ്നങ്ങൾ തടയുകയും ചെയ്യുന്നു.
- സഹായം തേടേണ്ടത് എപ്പോഴാണെന്ന് അറിയുക: ഓപ്പറേറ്റർമാർക്ക് അടിസ്ഥാന പ്രശ്നപരിഹാരം നടത്താൻ കഴിയുമെങ്കിലും, കൂടുതൽ നാശനഷ്ടങ്ങൾ ഒഴിവാക്കാൻ സങ്കീർണ്ണമായ പ്രശ്നങ്ങൾ യോഗ്യതയുള്ള സാങ്കേതിക വിദഗ്ധർ കൈകാര്യം ചെയ്യണം.
- ഊർജ്ജ കാര്യക്ഷമത: പതിവായി വൃത്തിയാക്കൽ, ശരിയായ റഫ്രിജറന്റ് അളവ് നിലനിർത്തൽ, ശരിയായ വാൽവ് പ്രവർത്തനം ഉറപ്പാക്കൽ തുടങ്ങിയ രീതികൾ നടപ്പിലാക്കുന്നത് ഊർജ്ജ കാര്യക്ഷമത മെച്ചപ്പെടുത്തുകയും പ്രവർത്തന ചെലവ് കുറയ്ക്കുകയും ചെയ്യും.
- ആദ്യം സുരക്ഷ: നിങ്ങളുടെ ചില്ലറിൽ ട്രബിൾഷൂട്ട് ചെയ്യുമ്പോഴോ അറ്റകുറ്റപ്പണികൾ നടത്തുമ്പോഴോ എല്ലായ്പ്പോഴും സുരക്ഷയ്ക്ക് മുൻഗണന നൽകുക. ഏതെങ്കിലും ഘട്ടത്തെക്കുറിച്ച് ഉറപ്പില്ലെങ്കിൽ, ഒരു പ്രൊഫഷണലിനെ സമീപിക്കുക.
ഈ തത്വങ്ങൾ മനസ്സിലാക്കി പ്രയോഗിക്കുന്നതിലൂടെ, നിങ്ങളുടെ ചില്ലർ സിസ്റ്റം ഫലപ്രദമായി കൈകാര്യം ചെയ്യാനും, പ്രവർത്തനരഹിതമായ സമയം കുറയ്ക്കാനും, വിവിധ വ്യാവസായിക ആപ്ലിക്കേഷനുകളിൽ ഒപ്റ്റിമൽ പ്രകടനം ഉറപ്പാക്കാനും കഴിയും.
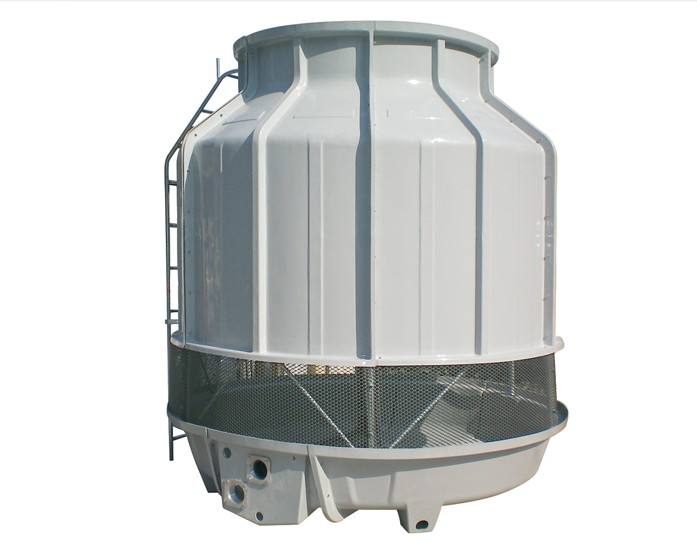