-
Dalingshan Industrial Guangdong
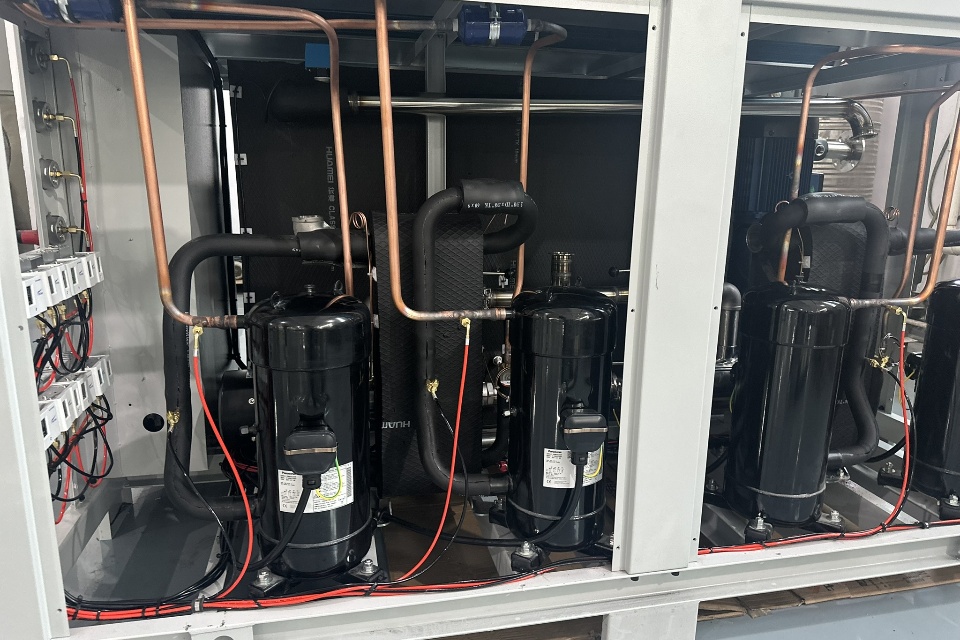
Understanding Explosion Proof Chillers
Explosion Proof Chillers: The Ultimate Solution for Hazardous Chemical Processing
In industries that handle hazardous chemicals, safety is not just a priority; it’s an absolute necessity. Processes involving flammable, explosive, or reactive substances require specialized equipment designed to mitigate risks and ensure the utmost protection for personnel and facilities. This is where explosion-proof Explosion-proof chillers are designed to operate safely in hazardous environments. come into play. This article delves into the critical role of explosion-proof chillers in explosion and hazardous chemical processing, highlighting their unique features, benefits, and why choosing the right chiller is paramount for maintaining a safe and efficient operation. If your operations involve hazardous materials, this is a must-read to understand how these specialized chillers can safeguard your business.
Explosion Proof chiller Article Outline
목차
What Makes a Chiller Explosion-Proof?
Explosion-proof chillers are specifically engineered to operate safely in environments where flammable gases, vapors, liquids, or combustible dust may be present. Unlike standard industrial chillers, every component is designed to prevent ignition of the surrounding atmosphere. Here are the defining characteristics:
- Explosion-Proof Enclosures: All electrical components, including motors, controls, and wiring, are housed within specially designed enclosures. These enclosures are built to contain an internal explosion, preventing the propagation of flames or sparks to the external environment.
- Intrinsically Safe Wiring: Wiring methods and materials are chosen to limit electrical and thermal energy to levels below what is required to ignite a specific hazardous atmospheric mixture. This prevents any sparks from occurring.
- Sealed Components: Components like the compressor and switches are hermetically sealed to prevent contact between potentially flammable substances and ignition sources.
- Compliance with Standards: Explosion-proof chillers adhere to rigorous international and regional standards, such as ATEX, IECEx, NEC (in North America), and others. These standards dictate the design, construction, testing, and certification requirements for equipment used in hazardous locations.
Why are Explosion-Proof Chillers Essential in Hazardous Environments?
In industries such as chemical processing, oil and gas, pharmaceuticals, and any environment where volatile substances are handled, the risk of explosion is a constant concern. Many processes in these industries generate significant heat, and precise explosion proof chiller technology is essential. temperature control is often crucial for product quality, process efficiency, and, most importantly, safety.
Here’s why explosion-proof chillers are indispensable:
- Preventing Ignition: They eliminate potential ignition sources, drastically reducing the risk of explosions triggered by electrical sparks or hot surfaces.
- Maintaining Safe Operating Temperatures: They provide reliable cooling to keep processes within safe temperature limits, preventing runaway reactions or auto-ignition of volatile substances.
- Protecting Personnel and Assets: By preventing explosions, they safeguard personnel from injury and protect valuable equipment and facilities from damage.
- Ensuring Regulatory Compliance: Using appropriate explosion-proof equipment is often a legal requirement in hazardous environments, ensuring compliance with safety regulations and standards.
- Business Continuity: By preventing accidents and downtime, explosion-proof chillers contribute to uninterrupted operations and business continuity.
Key Features of Explosion-Proof Chillers
Beyond their specialized safety features, explosion-proof chillers offer capabilities tailored to demanding industrial applications:
- Robust Construction: Built to withstand harsh environments, with durable materials and components resistant to corrosion and wear. This is especially important when dealing with corrosive chemicals.
- Precise Temperature Control is vital in environments classified as division 1 or division 2. Advanced control systems maintain tight temperature tolerances, essential for many chemical processes. This ensures consistent product quality and process efficiency in hazardous processes.
- High Cooling Capacity: Available in a wide range of cooling capacities to handle the heat loads of various industrial processes. This allows for effective cooling even in demanding applications.
- Redundancy Options: Many models offer redundant components, such as dual compressors or pumps, to ensure continuous operation even if one component fails.
- Remote Monitoring and Control: Advanced control systems allow for remote monitoring and adjustment of chiller operation, providing real-time data and alerts.
Types of Explosion-Proof Chillers
Explosion-proof chillers are available in several configurations, each offering advantages for specific applications:
- Air-Cooled Chillers: These chillers use ambient air to dissipate heat from the refrigerant. They are generally easier to install and maintain than water-cooled chillers. Explore our Air Cooled Screw Chiller options for a reliable air-cooled solution.
- Water-Cooled Chillers: These chillers use water from a cooling tower or other source to dissipate heat. They are often more energy-efficient than air-cooled models, especially in hot climates. Our Water Cooled Screw Water Chiller is a powerful and efficient option.
- Split System Chillers: These systems separate the condensing unit (containing the compressor and condenser) from the evaporator unit, which can be located closer to the process being cooled. This design offers flexibility in installation, particularly in space-constrained areas. We offer a wide selection of chillers to meet your needs, such as our versatile Air Cooled Scroll Water Chiller.
- Packaged Chillers: These are self-contained units that include all the necessary components, such as the compressor, condenser, evaporator, and controls, in a single package. They are typically easier to install and require less space than split systems.
Choosing the Right Cooling Capacity
Selecting the appropriate cooling capacity is crucial for optimal performance and safety. The required capacity depends on several factors:
- Heat Load: The amount of heat generated by the process that needs to be removed. This can be calculated based on the process parameters, such as the type and quantity of chemicals involved, reaction temperatures, and processing time.
- Ambient Temperature: The temperature of the surrounding environment. Higher ambient temperatures reduce the efficiency of air-cooled chillers and may necessitate a higher cooling capacity.
- Safety Margin: It’s essential to include a safety margin in the cooling capacity calculation to account for potential variations in heat load, future process expansions, and unexpected temperature spikes.
- Redundancy Requirements: If continuous operation is critical, consider incorporating redundant cooling capacity to ensure that cooling is maintained even if one chiller unit fails.
Understanding the Role of Refrigerants in Hazardous Environments
The choice of refrigerant is a critical consideration for explosion-proof chillers. Several factors influence this decision:
- Flammability: Traditional refrigerants like R-22 are being phased out due to environmental concerns. Modern alternatives, such as HFOs (hydrofluoroolefins), offer lower global warming potential but may have some degree of flammability. The selection must consider the specific hazardous environment classification.
- Toxicity: Some refrigerants can be toxic if inhaled in high concentrations. Proper ventilation and leak detection systems are crucial.
- Environmental Impact: Regulations increasingly favor refrigerants with low global warming potential (GWP) and zero ozone depletion potential (ODP).
- Performance: Different refrigerants have varying thermodynamic properties, affecting the performance of the cooling system in hazardous locations. chiller’s efficiency and cooling capacity.
- Compatibility: The refrigerant must be compatible with the materials used in the chiller’s construction to prevent corrosion or leaks.
Installation and Maintenance: Ensuring Continued Safety
Proper installation and maintenance are paramount for the safe and reliable operation of explosion-proof chillers:
- Professional Installation: Installation should only be carried out by qualified technicians experienced in working with explosion-proof equipment and hazardous environments. They must adhere to all relevant codes and standards. Consider our Anti-Explosion Chillers for specialized installations.
- Regular Inspections: Routine inspections are essential to identify and address potential issues, such as leaks, loose wiring, or component wear, before they escalate into safety hazards.
- Preventive Maintenance of explosion-proof chillers is essential to ensure their reliability in hazardous processes. A comprehensive preventive maintenance program should be implemented, including tasks like cleaning condenser coils, checking refrigerant levels, and testing safety interlocks.
- Record Keeping: Detailed records of all inspections, maintenance activities, and repairs should be maintained to track the chiller’s history and ensure compliance with safety regulations.
Applications of Explosion-Proof Chillers in Chemical Processing
Explosion-proof chillers are vital in various chemical processing applications, including:
- Reaction Temperature Control: Many chemical reactions are exothermic, generating significant heat. These chillers maintain optimal reaction temperatures, ensuring product quality, maximizing yield, and preventing runaway reactions.
- Solvent Recovery: Processes involving the recovery of volatile solvents often require cooling to condense the vapors. Explosion-proof chillers provide safe and efficient cooling for these operations.
- Storage of Flammable Materials: Storage facilities for flammable liquids or gases often require explosion-proof cooling systems to maintain safe temperatures and prevent pressure buildup.
- Pharmaceutical Manufacturing: Many pharmaceutical processes involve volatile substances and require precise temperature control in hazardous environments.
- Petrochemical Processing: Refineries and other petrochemical plants utilize explosion-proof chillers for various cooling applications in areas where flammable hydrocarbons are present.
Customization Options: Tailoring Chillers to Specific Needs
We understand that each application has unique requirements. We offer a range of customization options to ensure our explosion-proof chillers meet your specific needs.
- Cooling Capacity: From small laboratory-scale chillers to large industrial systems, we can provide the cooling capacity you need.
- Temperature Range: Our chillers can be configured to operate across a wide range of temperatures, from cryogenic to above-ambient.
- Control Systems: Choose from basic manual controls to sophisticated PLC-based systems with remote monitoring and data logging.
- Materials of Construction: We offer a variety of materials, including stainless steel and other corrosion-resistant alloys, to ensure compatibility with your specific chemicals and operating environment.
- Redundancy: We can incorporate redundant components, such as dual compressors and pumps, for added reliability.
- Special Features: We can add features like specialized alarms, leak detection systems, and custom enclosures to meet your specific safety and operational requirements. Consider a Cooling Tower for enhanced cooling efficiency.
The Future of Explosion-Proof Chiller Technology
The field of explosion-proof chiller technology is continually evolving. Here are some key trends:
- Advanced Refrigerants: The development of new refrigerants with lower flammability and reduced environmental impact is ongoing.
- Smart Controls: Integration with Industry 4.0 technologies, enabling real-time monitoring, predictive maintenance, and remote diagnostics.
- Improved Energy Efficiency: Continued focus on reducing energy consumption through advanced compressor designs, optimized heat transfer, and intelligent control algorithms.
- Enhanced Safety Features: Development of more sophisticated safety interlocks, leak detection systems, and other features to further enhance safety in hazardous environments.
FAQs
What is the difference between explosion-proof and flame-proof?
While often used interchangeably, there can be subtle differences depending on the specific standards being followed. Generally, both terms refer to equipment designed to prevent ignition of an external explosive atmosphere. Explosion-proof typically implies the ability to contain an internal explosion, while flame-proof may focus on preventing flames from escaping an enclosure.
Can explosion-proof chillers be used for comfort cooling in hazardous areas?
Yes, explosion-proof chillers can be used for comfort cooling in occupied spaces within hazardous areas, provided they are appropriately sized and installed according to relevant codes and standards.
What certifications should I look for in an explosion-proof chiller?
Common certifications for explosion-proof equipment include ATEX (for Europe), IECEx (international), and UL/FM (for North America). The specific certification required may vary depending on your location and the specific hazardous environment classification.
Are there any special considerations for installing explosion-proof chillers?
Yes, installation must be carried out by qualified personnel familiar with the requirements for hazardous locations. This includes proper grounding, bonding, wiring methods, and sealing of conduits.
How do I determine the right cooling capacity for my application?
A thorough assessment of the heat load generated by your process is essential. This involves considering factors like the type and quantity of chemicals involved, reaction temperatures, processing times, and ambient temperatures. It’s recommended to consult with a chiller expert to ensure accurate sizing.
Conclusion
- Safety First: Explosion-proof chillers are essential for maintaining safe operations in industries dealing with hazardous chemicals.
- Reliable Cooling: They provide precise cooling system solutions. temperature control, ensuring product quality and process efficiency.
- Customization is Key: Choose a chiller tailored to your specific needs, considering factors like cooling capacity, temperature range, and control options.
- Compliance is Crucial: Ensure your chiller meets all relevant safety standards and certifications for hazardous locations.
- Maintenance Matters: Regular inspections and preventive maintenance are vital for continued safe and reliable operation.
- Partner with Experts: Select a reputable chiller manufacturer with experience in explosion-proof equipment and a commitment to safety.
By investing in the right explosion-proof chiller and implementing proper safety practices, you can protect your personnel, facilities, and the environment while maintaining efficient and productive operations.