-
달링산 산업 광동

냉각기 선택 시 고려해야 할 5가지 요소
산업용 냉각기 장치를 구매할 때 고려해야 할 5가지 핵심 요소
이 기사에서는 다음을 선택할 때 고려해야 할 필수 요소를 살펴봅니다. 냉각기 산업용 어플리케이션을 위한 올바른 선택 산업용 냉각기 귀하의 특정 요구 사항에 맞는 단위는 귀하의 운영의 효율성과 수명에 상당한 영향을 미칠 수 있습니다. 이 게시물을 읽으면 이러한 요소에 대한 포괄적인 이해를 얻을 수 있으며, 산업 프로세스를 최적화하고 궁극적으로 시간과 비용을 절약하는 정보에 입각한 결정을 내릴 수 있습니다. 선도적인 산업 냉각기 제조업체로서, 우리는 다양한 산업적 요구에 맞춰 고품질 솔루션을 제공하기 위해 최선을 다하고 있습니다.
목차
산업용 냉각기란 무엇이고 어떻게 작동하나요?
안 산업용 냉각기 이다 냉장 시스템 프로세스 또는 장비에서 열을 제거하는 것입니다. 순환하여 작동합니다. 냉각 유체일반적으로 물 또는 물/글리콜 혼합물을 통해 냉각기 시스템 ~의 핵심 구성 요소, 포함 압축기, 아 응축기, 하나 증발기, 그리고 팽창 밸브. 냉각기 의 원칙을 사용합니다 냉장 공정에서 열을 흡수하여 다른 곳으로 전달해 원하는 영역이나 장비를 효과적으로 냉각합니다. 냉각기 다양한 산업 공정에 대한 최적의 작동 온도를 유지하는 데 중요한 역할을 합니다. 공랭식 냉각기 그리고 수냉식 냉각기 열을 거부하는 방법입니다. 공랭식 냉각기 사용하다 앰비언트 냉매를 냉각하기 위한 공기, 수냉식 냉각기 물을 사용합니다 냉각 탑이나 다른 물의 공급원.
적절한 냉각기 크기를 선택하는 것이 왜 중요한가요?
올바른 선택 냉각기 크기 효율적이고 비용 효율적인 운영에 필수적입니다. 대형 냉각기 자주 켜지고 꺼지면서 마모가 증가합니다. 압축기 그리고 에너지 효율성이 감소했습니다. 반대로, 크기가 작은 냉각기 충족하기 위해 노력할 것입니다 냉각 요구 사항으로 인해 부적절한 결과가 발생합니다. 냉각 및 프로세스 장비의 잠재적 손상. 신뢰할 수 있는 냉각기 제조업체에서는 적절한 크기의 중요성을 강조합니다. 냉각기 특정 사항에 맞는 단위 냉각 용량 필수. 필수 사항 결정 냉각 용량 공정에서 생성된 열 부하, 원하는 것과 같은 요인에 따라 달라집니다. 냉각 유체 온도, 그리고 주변 온도.
작동 환경은 냉각기 성능에 어떤 영향을 미칩니까?
그리고 운영 환경 중요한 역할을 한다 냉각기 성능. 다음과 같은 요인 주변 온도, 습도 및 공기 질은 영향을 미칠 수 있습니다 냉각기 할 수 있는 능력 열을 발산하다 효과적으로. 예를 들어, 높은 주변 온도 줄일 수 있습니다 냉각기의 냉각 용량, 습도가 높으면 다음과 같은 문제가 발생할 수 있습니다. 부식 그리고 효율성이 감소합니다. 또한, 냉장 시스템 사용합니다 앰비언트 열을 제거하기 위한 공기 응축기따라서 적절한 유지 관리를 하는 것이 중요합니다. 주변 공기 비외부 정격 온도 냉각기. 우리는 만들었습니다 방폭 냉각기 화학 및 제약 산업의 요구를 충족시키기 위해서입니다.
시설의 특정 환경 조건을 고려하는 것이 필수적입니다. 냉각기 선택. 우리는 경험이 풍부한 냉각기 제조업체는 귀하가 제품을 선택하는 데 도움을 줄 수 있습니다. 냉각기 귀하의 특정한 과제를 견뎌내도록 설계되었습니다. 운영 환경예를 들어, 시설이 덥고 습한 기후에 위치하고 있는 경우 수냉식 냉각기 부식 방지 재질을 사용하는 것이 더 나은 선택일 수 있습니다.
냉각기의 압력과 유량 요구 사항은 무엇입니까?
프로세스의 압력 및 흐름 요구 사항을 이해하는 것은 매우 중요합니다. 냉각기 구매. 유량, 이는 유체의 양입니다. 냉각기 단위 시간당 순환할 수 있는지가 중요한 요소입니다. 압력 손실 시스템 전체에서 유체가 파이프, 피팅 및 장비를 통과할 때 발생하는 유체 압력 감소입니다. 동일한 냉각기, 다음을 보장하는 것이 중요합니다. 냉각기 펌프는 각 공정에 필요한 유량과 압력 요구 사항을 동시에 지원할 수 있습니다. 압력 게이지 각 기계에 적절한 유량을 공급하기 위해 펌프 압력을 파악하는 것이 필요합니다.
크기가 작은 펌프는 다음을 줄입니다. 펌프의 냉각 능력 또는 흐름이 발생하는 것을 방지할 수도 있습니다. 냉각기 제조업체로서 우리는 이러한 매개변수의 중요성을 이해합니다. 냉각기 특정 압력 및 흐름 요구 사항을 충족하도록 설계되어 최적의 성능과 열 전달을 보장합니다. 또한 맞춤형 옵션을 제공하여 냉각기 다양한 펌프 크기와 유량 구성을 포함해 귀하의 정확한 요구 사항에 맞춰 제공됩니다.
냉각기 시스템의 에너지 효율을 극대화하는 방법은 무엇인가요?
에너지 효율성 모든 산업 운영에 있어서 중요한 고려 사항이며, 냉각기 예외는 아닙니다. 최적화 냉각기 에너지 효율을 위한 시스템은 상당한 비용 절감과 환경 영향 감소로 이어질 수 있습니다. 개선을 위한 가장 효과적인 방법 중 하나 에너지 효율성 옳은 것을 선택하는 것이다 냉각기 귀하의 응용 프로그램에 맞는 크기입니다. 대형 냉각기 비효율적으로 작동할 것입니다. 냉각기 충족하기 위해 노력할 것입니다 냉각 요구 사항이 증가하여 에너지 소비가 증가합니다.
또 다른 중요한 요소는 냉각기 디자인과 기술. 현대 냉각기 가변 속도 드라이브와 같은 고급 기능을 통합하여 다음을 수행할 수 있습니다. 압축기 출력을 조정하려면 다음을 기반으로 합니다. 냉각 부하를 줄여 상당한 에너지 절감을 이룰 수 있습니다. 당사 제조 공장에서는 에너지 효율성을 우선시합니다. 냉각기 디자인. 우리의 냉각기 고효율 등 최신 기술과 부품을 활용 압축기 에너지 소비는 최소화하고 성능은 극대화하기 위한 고급 제어 시스템을 갖추고 있습니다.
공랭식과 수냉식 냉각기의 주요 차이점을 요약한 표는 다음과 같습니다.
기능 | 공냉식 냉각기 | 수냉식 냉각기 |
열 차단 | 주변 공기를 사용합니다 | 냉각탑이나 기타 공급원의 물을 사용합니다. |
능률 | 일반적으로 더운 기후에서는 효율성이 떨어집니다. | 특히 더운 기후에서는 더욱 효율적입니다. |
설치 | 설치가 간편하고 냉각탑이 필요 없음 | 더 복잡한 설치에는 냉각탑이나 수원이 필요합니다. |
유지 관리 | 유지 보수 비용 절감, 구성 요소 감소 | 냉각탑으로 인해 유지관리가 더 많이 필요함 |
발자국 | 더 작은 발자국 | 냉각탑으로 인해 더 큰 발자국 |
냉각 유체 온도는 냉각기 선택에 어떤 영향을 미칩니까?
그리고 냉각 유체 온도 또 다른 것이다 핵심 요소 선택할 때 고려해야 할 사항 냉각기. 다른 프로세스에는 다른 온도 범위가 필요하며 다음을 선택합니다. 냉각기 원하는 온도를 달성하고 유지할 수 있는 것이 필수적입니다. 예를 들어, 일부 응용 프로그램은 식품 및 음료 산업 거의 영하의 온도가 필요할 수 있고, 다른 사람들은 적당한 냉각만 필요할 수 있습니다. 제공된 배열에서 무작위 이미지가 있습니다.
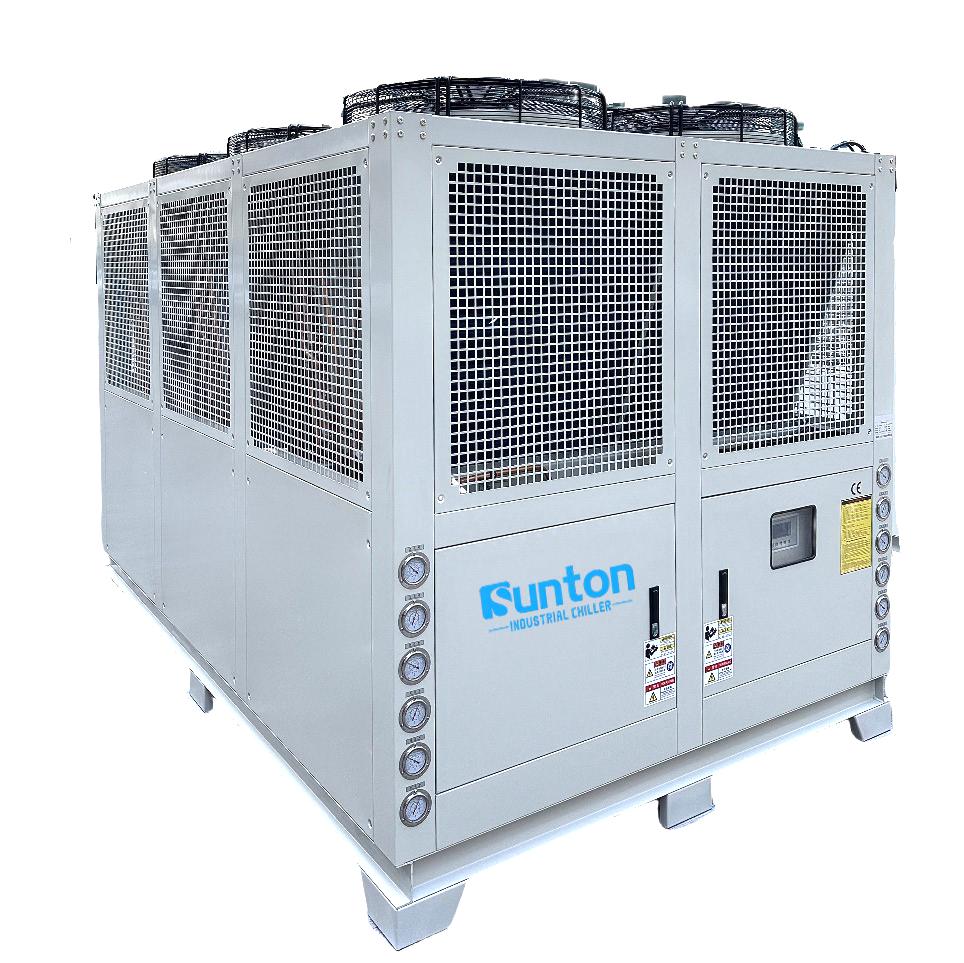
로서 냉각기 제조업체로서 우리는 광범위한 제품을 제공합니다 냉각기 특정 온도 범위 내에서 작동하도록 설계되었습니다. 냉각기 프로세스의 특정 온도 요구 사항을 충족하도록 사용자 정의하여 최적의 성능과 제품 품질을 보장할 수 있습니다. 글리콜 냉각기 특정 산업의 요구에 따라 매우 낮은 온도까지 도달할 수 있습니다.
증발기는 냉각기 성능에서 어떤 역할을 하나요?
그리고 증발기 의 중요한 구성 요소입니다 냉각기 공정 유체로부터 열을 흡수하는 것을 담당하는 시스템입니다. 증발기의 디자인과 효율성은 직접적으로 영향을 미칩니다 냉각기 전반적인 성과 및 냉각 용량.
다양한 유형이 있습니다 증발기, 쉘 앤 튜브, 브레이징 플레이트 및 마이크로채널 설계를 포함합니다. 각 유형은 열 전달 효율, 압력 강하 및 비용 측면에서 장단점이 있습니다. 냉각기 제조업체, 우리는 신중하게 선택합니다 증발기 최적화할 유형과 크기 냉각기 성능 각각의 특정 응용 프로그램을 위해. 우리의 냉각기 고품질을 활용하다 증발기 최대 열 전달 및 효율성을 위해 설계되어 안정적이고 일관된 성능을 보장합니다. 냉각.
냉각기 설치 시 고려해야 할 사항은 무엇입니까?
냉각기 설치 상당한 영향을 미칠 수 있는 중요한 측면입니다. 냉각기 성능과 수명을 보장합니다. 적절한 설치는 냉각기 고장 및 비용이 많이 드는 수리의 위험을 최소화하면서 효율적이고 안전하게 작동합니다. 선도적인 산업 냉각기 우리 회사는 고품질을 제공하고 싶습니다 농업용 산업용 냉각기.
여러 가지 요소를 고려해야 합니다. 냉각기 설치위치, 공간 요구 사항, 환기 및 전기 연결을 포함합니다. 냉각기 유지 관리 및 공기 흐름을 위한 충분한 여유 공간이 있는 통풍이 잘되는 곳에 설치해야 합니다. 적절한 전기 연결도 필수적입니다. 냉각기 올바른 전압과 전류를 수신합니다.
냉각기 수명을 늘리려면 정기적인 유지관리가 왜 중요한가요?
정기적인 유지관리는 장비의 수명과 최적의 성능을 보장하는 데 필수적입니다. 냉각기 시스템. 잘 유지 관리된 냉각기 더 효율적으로 작동하고, 에너지 소비가 적으며, 수명이 더 길어 궁극적으로 운영 비용과 잠재적 수리 비용을 절감할 수 있습니다.
정기적인 유지 관리 작업에는 청소가 포함됩니다. 응축기 코일, 냉매 수준 확인, 검사 증발기, 그리고 제어 시스템을 테스트합니다. 냉각기 제조업체로서 우리는 귀하의 제품을 유지하기 위해 포괄적인 유지 보수 서비스를 제공합니다. 냉각기 원활하고 효율적으로 실행됨.
사례 연구: 냉각기 선택의 실제 사례
사례 연구 1: 플라스틱 및 고무 산업
플라스틱 제조 회사는 사출 성형 기계의 과열로 인해 자주 가동이 중단되었습니다. 공정을 분석한 후 냉각 요구 사항에 따라 우리는 다음을 권장했습니다. 수냉식 냉각기 가변 속도 드라이브가 있는 압축기. 새로운 냉각기 정확한 온도 제어를 제공하고 개선되었습니다. 에너지 효율성, 에너지 비용이 30% 감소하고 생산 중단 시간이 크게 감소했습니다. 수냉식 스크류 중앙 냉각기 귀사의 산업적 요구에 완벽하게 부합합니다.
사례 연구 2: 식품 및 음료 산업
양조장은 일관된 발효 온도를 유지하는 데 어려움을 겪고 있었고, 이는 맥주 품질에 영향을 미쳤습니다. 우리는 그들에게 맞춤형 글리콜을 제공했습니다. 냉각기 필요한 저온을 달성하고 유지할 수 있는 시스템입니다. 새로운 냉각기 시스템을 도입한 후 제품 품질이 개선되었고 생산 용량이 25% 증가했습니다.
자주 묻는 질문
공랭식 냉각기와 수랭식 냉각기의 차이점은 무엇인가요?
안 공랭식 냉각기 사용하다 앰비언트 냉매를 냉각하기 위한 공기, 수냉식 냉각기 물을 사용합니다 냉각 탑이나 다른 물의 공급원. 수냉식 냉각기 일반적으로 더 효율적이며 특히 더운 기후에서 효과적이지만 더 복잡한 설치가 필요합니다.
내 적용 분야에 맞는 적절한 크기의 냉각기를 어떻게 결정합니까?
오른쪽을 결정하다 냉각기 크기 원하는 것을 고려하여 프로세스에서 생성된 열 부하를 계산하는 것을 포함합니다. 냉각 유체 온도, 그리고 다음을 고려하여 주변 온도. 상담하는 것이 가장 좋습니다. 냉각기 적절한 크기를 보장하려면 제조업체나 숙련된 HVAC 전문가에게 문의하세요.
산업용 냉각기의 일반적인 수명은 얼마입니까?
수명은 산업용 냉각기 사용, 유지 관리 및 운영 환경과 같은 요인에 따라 달라질 수 있습니다. 그러나 적절한 유지 관리를 통해 잘 구축된 냉각기 15~20년, 심지어 그 이상 지속될 수도 있습니다.
냉각기는 얼마나 자주 정비해야 합니까?
다음을 갖는 것이 좋습니다. 냉각기 자격을 갖춘 기술자가 연 1회 이상 서비스를 제공해야 합니다. 그러나 상황에 따라 더 자주 서비스를 제공해야 할 수도 있습니다. 냉각기 사용 및 작동 조건. 우리는 최고 수준의 섬유 산업을 위한 산업용 냉각기.
냉각기는 난방과 냉방을 모두 할 수 있나요?
네, 일부 냉각기 난방과 냉각. 이것을 히트펌프라고 합니다. 냉각기그리고 그들은 그것을 뒤집을 수 있습니다 냉장 필요할 때 난방을 제공하기 위해 순환합니다.
냉각기를 수리해야 한다는 일반적인 징후로는 무엇이 있나요?
귀하의 일반적인 징후 냉각기 수리가 필요할 수 있음 감소 포함 냉각 용량, 이상한 소음이나 진동, 누수, 잦은 켜짐과 꺼짐 반복.
주요 내용
- 올바른 선택 산업용 냉각기 효율적이고 비용 효율적인 운영을 위해 필수적입니다.
- 냉각기 크기, 작동 환경, 압력 및 흐름 요구 사항, 냉각 유체 온도, 증발기 유형, 설치 및 유지 관리 주요 요인 고려할 것.
- 에너지 효율성 올바른 것을 선택하면 극대화할 수 있습니다 냉각기 규모를 확대하고, 첨단 기술을 활용하고, 적절한 유지관리 관행을 구현합니다.
- 정기적인 유지관리는 장비의 수명과 최적의 성능을 보장하는 데 필수적입니다. 냉각기 체계.
- 신뢰할 수 있는 전문가와 상담하기 냉각기 저희와 같은 제조업체는 귀하가 최상의 제품을 선택하는 데 도움을 드릴 수 있습니다. 냉각기 고객님의 특정 요구 사항에 맞게 설치 및 유지관리가 올바르게 이루어지도록 하세요.
- 우리는 다양한 제품을 보유하고 있습니다 유제품 우유 냉각기 산업적으로 냉각기 귀하의 특별한 요구 사항에 맞게.
이러한 요소를 이해하고 저희와 같은 신뢰할 수 있는 파트너와 협력하면 산업 공정을 최적화하고 제품 품질을 개선하며 운영 비용을 절감할 수 있습니다. 오늘 저희에게 연락하여 저희의 냉각기 귀하의 사업에 도움이 되고 생산 목표를 달성하는 데 도움이 될 수 있습니다.
