-
Dalingshan Industrial Guangdong
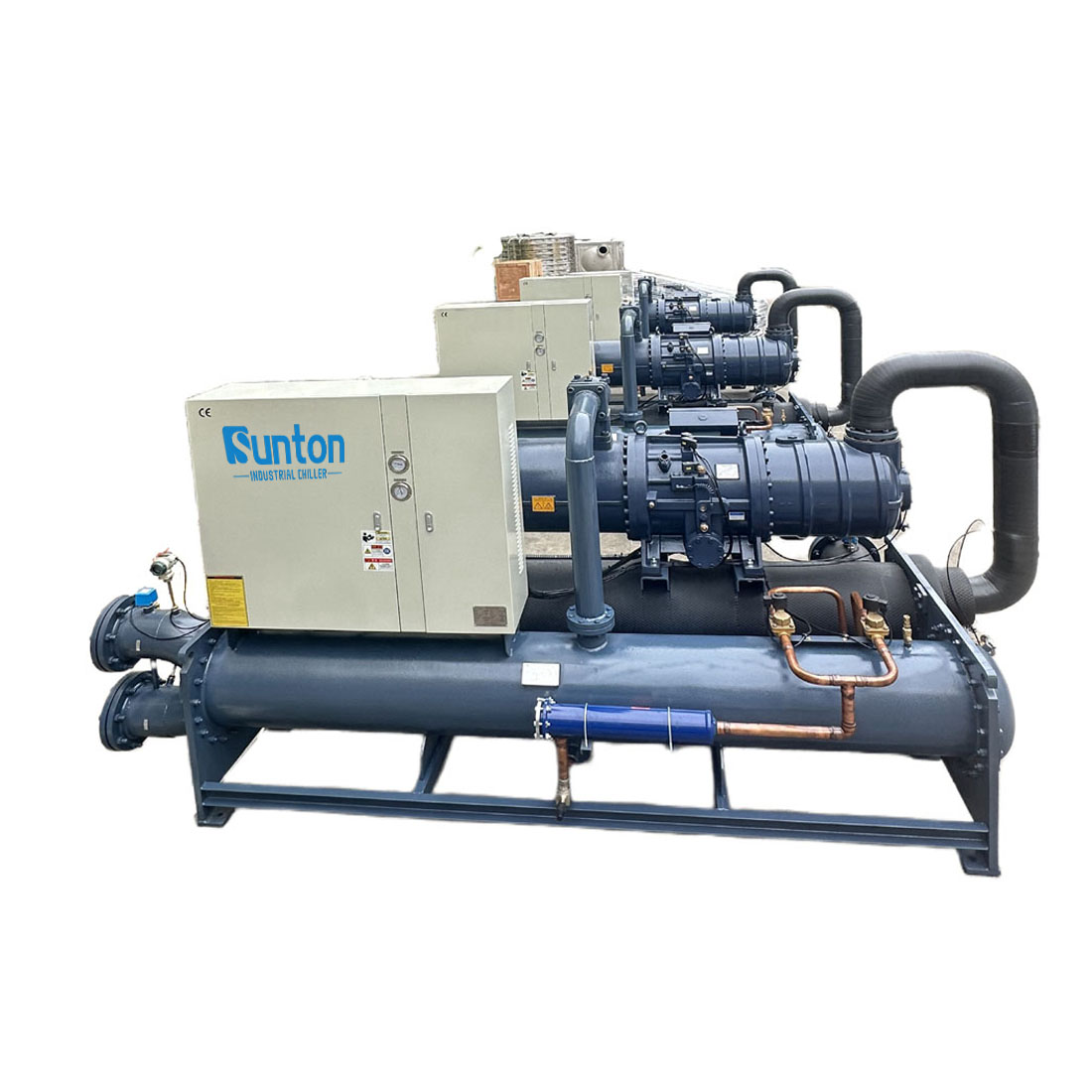
Pendingin untuk Pengolahan Plastik
Pendingin Berkinerja Tinggi untuk Pengolahan Plastik
Daftar Isi
Memastikan Kualitas dan memastikan bahwa pasokan air dingin mencukupi untuk proses Pendinginan yang tepat sangat penting untuk kinerja pendingin industri. mempertahankan suhu yang konsisten untuk hasil terbaik dalam pencetakan plastik. Efisiensi Panduan ini memberikan gambaran umum yang komprehensif tentang pendingin menggunakan air dingin untuk mendinginkan plastik secara efektif selama proses pencetakan.d di industri plastik, dengan fokus pada peran penting mereka dalam menjaga kontrol suhu yang tepat untuk berbagai proses manufaktur. Dari cetakan injeksi dan ekstrusi plastik untuk cetakan tiup dan pembentukan termal, kami mengeksplorasi bagaimana berbagai jenis pendingin berkontribusi pada kualitas produk, produksi yang efisien, dan keberhasilan operasional secara keseluruhan. Apakah Anda bengkel kecil atau fasilitas manufaktur berskala besar, memahami proses plastik kebutuhan pendinginan dapat dipenuhi dengan pendingin industri plastik portabel. sangat penting untuk mengoptimalkan proses produksi Anda. Sebagai perusahaan terkemuka pendingin plastik pabrik manufaktur, kami memahami pentingnya pendinginan yang andal dan efisien, dan kami menawarkan berbagai macam berkualitas tinggi pendingin disesuaikan untuk memenuhi kebutuhan spesifik Anda.
Pendingin air industri memainkan peran penting dalam menjaga suhu yang optimal. Peran Penting Pendingin dalam Industri Plastik
Pendingin merupakan komponen yang tidak terpisahkan dari industri plastik, menyediakan kontrol suhu yang tepat yang dibutuhkan untuk berbagai proses produksi. pendinginan sistem memastikan pendinginan yang konsisten cetakan, bahan, dan peralatan, yang sangat penting untuk menghasilkan produk berkualitas tinggi produk plastikKonsistensi yang ditawarkan oleh kami pendingin proses akan membantu mengoptimalkan semua aspek Anda proses pembuatan.
Tanpa pendingin, yang plastik mungkin tidak Dingin secara merata, sehingga dapat menyebabkan cacat seperti lengkungan, penyusutan, dan ketidakkonsistenan pada hasil akhir. produk plastik. Dapat diandalkan pendingin memungkinkan produsen untuk mempertahankan toleransi yang ketat, mengurangi limbah, dan mencapai waktu siklus yang lebih cepat. Baik itu cetakan injeksi plastik operasi atau ekstrusi plastik, pendinginan yang tepat sangat penting untuk memastikan hasil berkualitas tinggi.
Memahami Berbagai Jenis Pendingin Plastik
The industri plastik menggunakan berbagai jenis pendingin berdasarkan kebutuhan dan aplikasi spesifik mereka dalam produksi plastik. Memahami berbagai jenis ini sangat penting untuk memilih pendingin plastik kanan untuk fasilitas Anda.
- Pendingin Berpendingin Udara: Unit-unit ini menggunakan udara untuk menghilangkan panas dari refrigeran, menjadikannya solusi yang lebih sederhana dan lebih hemat biaya. Solusi ini sangat cocok untuk operasi yang lebih kecil dan di tempat yang akses airnya terbatas.
- Pendingin Berpendingin Air: Ini pendingin menggunakan air untuk menghapus panas, menawarkan lebih tinggi kapasitas pendinginan dan efisiensi energi, terutama di daerah beriklim hangat. Ini ideal untuk fasilitas yang lebih besar di mana air tersedia dengan mudah. Untuk operasi dengan persyaratan kontrol suhu yang sangat spesifik, pertimbangkan Pendingin Air Sekrup Berpendingin Air.
- Pendingin Portabel: Unit yang ringkas dan mudah dipindahkan ini menawarkan fleksibilitas, sehingga Anda dapat memindahkannya dengan mudah di antara berbagai mesin atau proses. Unit ini sangat cocok untuk operasi skala kecil hingga menengah yang membutuhkan Dingin peralatan yang bervariasi.
- Pendingin Sentral: Untuk skala besar plastik pabrik manufaktur, pendingin sentral menawarkan solusi terpadu untuk semua pendinginan kebutuhan dari satu sumber. Sistem ini lebih efisien untuk fasilitas dengan banyak mesin proses. Kita Pendingin Sentral Sekrup Berpendingin Udara menawarkan solusi pendinginan yang kuat dan andal untuk operasi berskala besar.
Memilih antara berpendingin udara dan berpendingin air Pilihan sering bergantung pada beberapa faktor, termasuk iklim fasilitas Anda, sumber daya yang tersedia, dan spesifikasinya. persyaratan pendinginan. Ketika pendingin berpendingin udara lebih nyaman dalam hal instalasi, pendingin berpendingin air sering kali memberikan kinerja yang unggul dan efisiensi yang lebih besar dalam kondisi pengoperasian tertentu.
Peran Penting Pendingin dalam Cetakan Injeksi
Dalam cetakan injeksi plastik, pendingin sangat penting untuk menjaga ketepatan cetakan suhu, memastikan bahwa plastik membeku dengan baik, dan mempertahankan kualitas produk yang tinggi. proses cetak injeksi membutuhkan manajemen panas yang cermat selama injeksi dan waktu pendinginan untuk mencapai sifat mekanik dan akurasi dimensi akhir yang dibutuhkan Bagian plastik.
A pendingin memainkan peran kunci dalam menghilangkan panas dari plastik ke dalam cetakan, memungkinkan waktu siklus yang lebih cepat, dan meminimalkan cacat pada bagian cetakan. Efektif pendinginan cetakan membantu mengurangi waktu siklus, meningkatkan output, dan menurunkan biaya produksi. pendingin cetak injeksi memungkinkan kontrol yang tepat suhu selama proses ini, hal ini dapat menimbulkan masalah pada produksi plastik, sehingga meningkatkan kualitas keseluruhan komponen yang diproduksi.
Pendingin dan Pentingnya dalam Ekstrusi Plastik
Ekstrusi adalah suatu proses yang berkesinambungan dimana plastik dicairkan dan dipaksa melalui cetakan untuk membuat bentuk seperti pipa, film, dan lembaran. proses pendinginan sangat penting di sini untuk menjaga sifat-sifat yang tepat dari produk akhir. Konsisten pendinginan sangat penting untuk menjaga keakuratan dimensi dan hasil akhir permukaan yang halus pada cetakan plastik akhir. produk plastik. Kita Pendingin Sekrup Berpendingin Udara merupakan pilihan yang efektif dan andal untuk jenis operasi ini.
A pendingin di dalam ekstrusi plastik digunakan untuk mendinginkan ekstruder laras, mati, dan diekstrusi plastik itu sendiri. Tepat pendinginan memastikan suhu seragam dipertahankan, yang mencegah lengkungan atau distorsi produk plastikIni digunakan untuk Dingin itu ekstruder plastik ke tempat yang tepat suhu operasi untuk optimal plastik pengolahan. Di area ini, sebuah pendingin adalah kunci untuk menghasilkan kualitas tinggi produk plastik.
Penggunaan Pendingin dalam Blow Molding
Cetakan tiup adalah plastik proses pembuatan dimana dipanaskan plastik ditiup menjadi cetakan untuk membuat bentuk berongga, seperti botol dan wadah. Di sini, pendingin memainkan peran penting dalam memastikan pembentukan dan pemadatan yang tepat dari produk plastik.
Selama cetakan tiup proses, plastik panas (biasanya dalam bentuk parison) dimasukkan ke dalam cetakanUntuk memungkinkan pembentukan bentuk yang diinginkan dengan tepat, cetakan perlu didinginkan. pendingin menyediakan pasokan yang konsisten Dingin air untuk mengendalikan cetakan suhu. Efektif pendinginan cetakan diperlukan untuk memastikan bahwa plastik mengeras dengan cepat dan merata, mencegah deformasi dan memastikan bahwa produk akhir memenuhi persyaratan dimensi dan kualitas. Dalam hal ini, pendingin memastikan Anda membuat bagian yang konsisten.
Memahami Pendingin Proses untuk Produksi Plastik
A pendingin proses, juga disebut sebagai pendingin proses plastik, adalah jenis pendinginan sistem yang dirancang khusus untuk menghilangkan panas dari proses industri tertentu, seperti plastik manufaktur. Dalam sebuah industri pengolahan plastik, A pendingin proses bekerja dengan menggunakan air industri untuk meningkatkan efisiensi. refrigeran untuk menyerap panas dari plastik dan memindahkannya ke tempat lain, menyediakan kontrol suhu yang konsisten untuk semua aspek produksi.
Pendingin proses sering digunakan untuk Dingin berbagai jenis peralatan di industri pengolahan plastik, dari ekstruder dan mesin cetak untuk kalender dan mesin terkait lainnya. Mereka menyediakan yang dibutuhkan kapasitas pendinginan untuk menangani sejumlah besar panas yang dihasilkan selama proses pembuatan plastik. Kita pendingin proses dirancang untuk menawarkan stabilitas suhu yang tepat dan konsisten pendinginan, sehingga meningkatkan kualitas secara keseluruhan produk plastik.
Komponen Utama Sistem Pendingin Plastik
A pendingin plastik Sistem ini biasanya terdiri dari beberapa komponen utama, yang masing-masing memainkan peran penting dalam keseluruhan proses pendinginan. Berikut ini adalah komponen utamanya:
- Kompresor: The kompresor bertanggung jawab untuk mengedarkan dan mengompresi refrigeran gas, meningkatkan suhu dan tekanannya. Ini adalah komponen kunci yang memberi daya pada seluruh pendinginan sistem. Kami kompresor gulir unit sangat dapat diandalkan dan sangat efisien.
- Kondensator: The kondensor digunakan untuk mendinginkan benda yang terkompresi refrigeran dengan melepaskan panasnya ke lingkungan sekitarnya, baik melalui udara atau airKomponen ini mentransisikan refrigeran dari wujud gas ke wujud cair.
- Penguap: The penguap adalah tempat cairan refrigeran menyerap panas dari proses plastik, menyebabkannya menguap menjadi gas. Komponen ini bertanggung jawab untuk pendinginan itu air proses.
- Katup Ekspansi: Katup ekspansi mengatur aliran refrigeran dan mengurangi tekanannya, mempersiapkannya untuk penguap.
- Unit Kontrol: Sebuah kecanggihan unit kontrol digunakan untuk memantau dan menyesuaikan pendingin kinerja, memastikan kontrol suhu yang tepat dan operasi yang efisien.
Memahami komponen-komponen kunci ini dapat membantu Anda lebih memahami bagaimana sebuah pendingin bekerja dan mengapa setiap bagian penting untuk pemeliharaan pendinginan yang andal.
Memilih Pendingin yang Tepat untuk Aplikasi Plastik Anda
Memilih pendingin plastik kanan tergantung pada beberapa faktor, termasuk jenis proses plastik, yang dibutuhkan kapasitas pendinginan, titik setel suhu yang diinginkan, dan anggaran keseluruhan. Memilih yang tepat jenis pendingin akan memungkinkan pabrik Anda beroperasi pada efisiensi puncak.
- Tentukan beban pendinginan: hitung kebutuhan untuk pendingin air industri. Hitung jumlah panas yang dihasilkan oleh spesifik Anda proses plastik untuk menentukan yang dibutuhkan kapasitas pendinginan unit Anda.
- Pilih jenis pendingin yang tepat: Pilih antara berpendingin udara, berpendingin air, atau pendingin portabel berdasarkan kebutuhan spesifik Anda, sumber daya, dan aplikasinya.
- Pertimbangkan efisiensi energi: Memilih pendingin dengan komponen efisiensi tinggi untuk mengurangi konsumsi energi dan biaya operasional.
- Mengevaluasi sistem kontrol: Pilih unit yang memberikan hasil yang tepat dan dapat diandalkan kontrol suhu, memungkinkan penyesuaian dan manajemen proses yang dioptimalkan.
Membuat pilihan yang tepat memerlukan pemahaman akan kebutuhan Anda, penilaian cermat terhadap pilihan Anda, dan kemitraan dengan pemasok yang berpengetahuan luas.
Memelihara Pendingin Plastik Anda agar Tahan Lama
Perawatan rutin sangat penting untuk memaksimalkan umur dan efisiensi mesin Anda. pendingin plastikPerawatan yang tepat memastikan bahwa sistem pendingin akan berfungsi dengan andal selama bertahun-tahun.
- Inspeksi Rutin: Jadwalkan pemeriksaan rutin untuk memeriksa adanya kebocoran, bagian yang rusak, atau keausan pada unit.
- Pembersihan: Bersihkan kumparan secara teratur kondensor dan penguap untuk memastikan ketepatan pertukaran panasPenumpukan debu, kotoran, dan kerak dapat secara signifikan mengurangi efisiensi pendingin.
- Manajemen Refrigeran: Pastikan tepat refrigeran tingkat dan segera mengatasi kebocoran.
- Pengolahan Air: Jika Anda menggunakan pendingin air, mengobati air dalam sistem Anda untuk mencegah terbentuknya kerak, korosi, dan penumpukan kontaminan, yang dapat menghambat kinerja unit.
- Layanan Profesional: Bermitra dengan yang terlatih layanan pendingin teknisi untuk menyediakan pemeliharaan preventif dan mengatasi masalah dengan cepat.
Perawatan rutin akan memungkinkan Anda pendingin agar dapat beroperasi sebagaimana mestinya selama bertahun-tahun mendatang, pastikan mesin cetak injeksi Anda memiliki pendinginan yang memadai.
FAQ Tentang Pendingin Plastik
Apa perbedaan antara pendingin berpendingin udara dan pendingin berpendingin air?
Pendingin berpendingin udara menggunakan udara untuk menghilangkan panas, ketika pendingin berpendingin air menggunakan air, menawarkan efisiensi yang lebih besar tetapi membutuhkan menara pendingin atau sumber air lainnya.
Bagaimana cara menghitung kapasitas pendinginan yang saya butuhkan?
Yang dibutuhkan kapasitas pendinginan tergantung pada ukuran dan jenis mesin Anda, jenis plastik sedang diproses, dan waktu siklus yang diinginkan. Konsultasikan dengan spesialis untuk menentukan kebutuhan spesifik Anda.
Dapatkah saya menggunakan pendingin portabel untuk proses ekstrusi plastik saya?
Unit portabel ideal untuk melengkapi pendinginan dan untuk operasi ekstrusi yang lebih kecil, tetapi operasi yang besar atau berkelanjutan mungkin memerlukan kapasitas pendinginan yang lebih tinggi.
Apa yang harus saya lakukan jika pendingin saya tidak bekerja dengan benar?
Jika pendingin air industri Anda tidak berfungsi dengan baik, pendingin tidak berfungsi, segera hubungi teknisi yang berkualifikasi. Terus menggunakan peralatan tanpa perbaikan yang tepat dapat menyebabkan kerusakan pada unit dan peralatan produksi Anda.
Poin Penting: Mengoptimalkan Pemrosesan Plastik dengan Pendingin yang Tepat
- Pendingin sangat penting untuk menjaga suhu yang tepat di berbagai proses plastik.
- Berbagai jenis pendingin tersedia, masing-masing memiliki keunggulan dan aplikasi spesifik.
- Perawatan yang tepat sangat penting untuk memastikan umur panjang dan efisiensi unit Anda.
- Memilih yang tepat pendingin tergantung pada pemahaman kebutuhan dan persyaratan spesifik Anda.
- Bermitra dengan perusahaan yang memiliki reputasi baik pembuatan pendingin plastik pabrik memastikan Anda memiliki akses ke produk dan dukungan berkualitas tinggi.
Dengan mengikuti wawasan dan saran dalam panduan ini, Anda dapat mengoptimalkan proses pendinginan secara efektif, meningkatkan kualitas produk, dan meningkatkan efisiensi manufaktur Anda. Silahkan hubungi kami untuk mendiskusikan spesifik Anda persyaratan pendinginan dan jelajahi rangkaian lengkap kami pendingin solusi. Penawaran kami mencakup berbagai solusi, mulai dari Solusi Pendinginan Chiller Suhu Rendah untuk Pendingin Anti-Ledakan sangat penting untuk keperluan pendinginan pada mesin cetak injeksi..