-
Dalingshan Industrial Guangdong

What’s Your Checklist When Your Industrial Chiller Compressor Burns Out?
Checklist When Your Industrial Chiller Compressor Burns Out?
Daftar Isi
Industrial chiller compressor burnout can halt production and lead to costly downtime. Use this step-by-step checklist to diagnose issues, prevent future failures, and ensure your system runs smoothly.

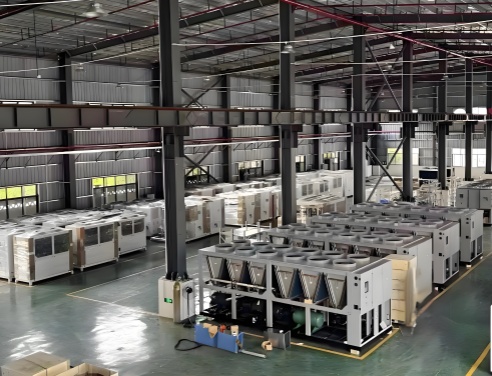
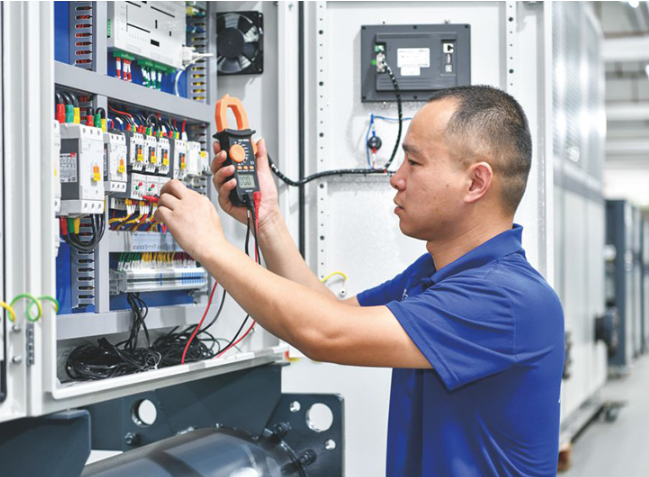
Critical Checks After Compressor Burnout
1. Electrical System Inspection
Bolded keyword: Start with a circuit inspection to rule out power-related causes:
- Turn off the power supply and inspect wires, plugs, and terminals for looseness or corrosion.
- Use a multimeter to check voltage stability. Fluctuations above ±10% require immediate correction.
- Replace blown fuses and investigate root causes (e.g., voltage spikes or short circuits).
Internal link: For voltage-sensitive systems, explore our Solusi Pendinginan Chiller Suhu Rendah designed for stable operation.
2. Overheating & Mechanical Damage
Bolded keyword: Look for overheating damage on the compressor:
- Check for discolored or burnt casing.
- Inspect internal temperatures using infrared thermometers. High temps (>200°F) indicate poor airflow or refrigerant issues.
- Clean dust-clogged condenser coils to restore heat exchange efficiency.
Internal link: Prevent overheating with our Pendingin Air Gulir Berpendingin Air, optimized for thermal management.
3. Refrigerant & Oil Contamination
Bolded keyword: Refrigerant contamination often follows compressor burnout:
- Test oil for acidity using litmus paper. Acidic oil (pH <5) requires a full system flush.
- Replace carbonized oil and install a charcoal core suction drier for 48 hours.
- Monitor pressure drops; aim for <2.5 PSI after cleanup.
Internal link: Contaminated systems benefit from Pendingin Sentral Sekrup Berpendingin Air with built-in filtration.
4. Flood Back & Short Cycling
Bolded keyword: Flood back damages compressors over time:
- Attach a temp sensor to the suction line to monitor refrigerant return.
- Track compressor cycles via the controller (e.g., E2 models). Short cycles (<5 minutes) signal improper load balancing.
- For racks, assess if a single compressor replacement suffices or a full rebuild is needed.
Internal link: Optimize cycle times with smart Pendingin HVAC featuring adaptive controllers.
5. Post-Repair Acid Test
Bolded keyword: Perform an acid test before restarting:
- Check oil levels and pump functionality.
- Run the new compressor at 50% load for 2 hours.
- Replace oil filters and liquid line filters if acid traces remain.
- Inspect valve plates and pistons for wear or carbon buildup.
Internal link: For harsh environments, use Pendingin Anti-Ledakan resistant to chemical corrosion.
Preventive Measures to Avoid Future Burnouts
Checklist Item | Action Required | Frekuensi |
Oil Quality Check | Test for acidity, moisture, and debris. | Bulanan |
Electrical Audit | Inspect wiring, fuses, and voltage stability | Triwulanan |
Pembersihan Kondensor | Remove dust/debris from coils. | Bi-Annually |
Flood Back Monitoring | Log suction line temps and cycle times. | Kontinu |
Internal link: Ensure long-term reliability with Pendingin Industri untuk Elektroplating, built for extreme conditions.
When to Call a Professional
If burnout recurs or system contamination persists:
- Stop operations immediately to avoid cascading failures.
- Contact certified technicians for refrigerant recovery dan system deep cleaning.
Pro tip: Pair your chiller with a Penukar Panas Selongsong dan Tabung to enhance cooling efficiency and reduce compressor strain.
By following this checklist, you’ll minimize downtime, extend compressor life, and maintain peak chiller performance. For complex issues, always rely on expert support and high-quality replacements.