-
Dalingshan Industrial Guangdong
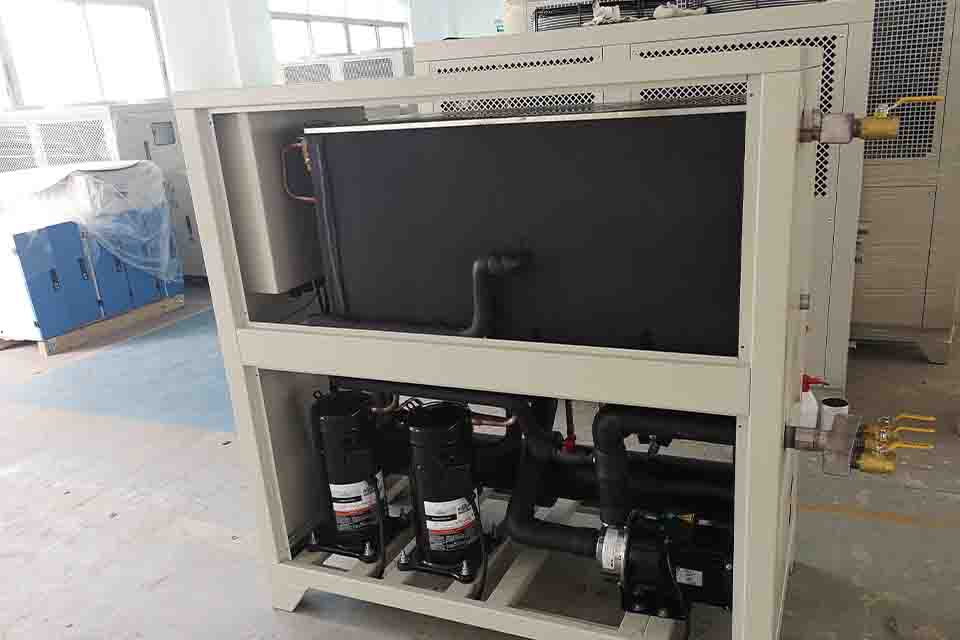
3 cara mikroprosesor mcs memberikan kontrol proses yang lebih ketat
Sistem Kontrol Mikroprosesor (MCS): Merevolusi Kontrol Proses Industri
Artikel ini membahas peran transformatif Sistem Kontrol Mikroprosesor (MCS) dalam lingkungan industri modern. Dari peningkatan presisi dalam produksi hingga memastikan kepatuhan terhadap standar lingkungan, teknologi MCS sangat diperlukan bagi bisnis yang ingin mengoptimalkan operasi dan meningkatkan efisiensi. Sebagai pabrik produksi pendingin air industri yang melayani berbagai sektor seperti Plastik dan Karet, Makanan dan Minuman, serta Pusat Data, memahami dan memanfaatkan MCS sangat penting untuk tetap kompetitif dan memenuhi kebutuhan pelanggan yang terus berkembang. Mari kita bahas mengapa MCS bukan sekadar pilihan, tetapi kebutuhan bagi industri saat ini.
Daftar Isi
Apa itu Sistem Kontrol Mikroprosesor (MCS)?
A sistem kontrol mikroprosesor (MCS) adalah sistem digital yang menggunakan satu atau lebih mikroprosesor untuk mengelola dan mengatur berbagai proses industri. Tidak seperti tradisional kontrol elektromekanis atau kontrol elektronik yang dibuat khususMCS menawarkan fleksibilitas, presisi, dan kemampuan beradaptasi yang lebih baik. mikroprosesor pada dasarnya adalah otak dari sistem, yang menjalankan instruksi yang tersimpan dalam memori untuk mengendalikan mesin, memantau kinerja, dan melakukan penyesuaian secara real-time. mikroprosesor pertama muncul pada awal tahun 1970-an. Dengan menggabungkan unit pemrosesan pusat pada satu sirkuit terpadu, mikroprosesor merevolusi komputasi dan otomatisasi.
Pada pendingin air industri kami, program kontrol mikroprosesor memastikan bahwa proses pendinginan dioptimalkan untuk aplikasi tertentu, baik itu mempertahankan suhu yang tepat dalam cetakan plastik atau memastikan pendinginan yang konsisten untuk server pusat data. Mikroprosesor telah mengikuti Hukum Moore. peningkatan kapasitas mikroprosesor telah mengikuti. Misalnya, mikroprosesor 8-bit yang terjangkau dengan pengalamatan 16-bit juga menjadi umum dalam banyak aplikasi industri. Mikroprosesor dan mikrokontroler dengan produk untuk keperluan industri.
Apa Perbedaan Mikrokontroler dengan Mikroprosesor dalam Aplikasi Industri?
Meskipun keduanya mikroprosesor dan mikrokontroler memainkan peran penting dalam otomatisasi, mereka melayani tujuan yang berbeda. mikroprosesor bertindak sebagai pusat unit kontrol di sebuah sistem komputer, menangani tugas-tugas kompleks dan membutuhkan komponen eksternal seperti memori dan perangkat input/output. Mikroprosesor digunakan untuk mengoperasikan memori eksternal. mikrokontroler, di sisi lain, adalah unit mandiri dengan CPU, memori, dan periferal bawaan, yang dirancang untuk tujuan tertentu kontrol tugas dalam suatu sistem tertanam.
Dalam konteks pendingin air industri, mikrokontroler sering digunakan untuk fungsi tertentu seperti memantau sensor suhu, mengendalikan pompa, dan mengelola alarm. Misalnya, mikrokontroler di kami Pendingin glikol mungkin bertanggung jawab untuk mengatur aliran glikol untuk mempertahankan suhu yang diinginkan, menunjukkan bagaimana mikrokontroler disesuaikan untuk tugas kontrol tertentu dalam sistem yang lebih besar. Mikroprosesor atau mikrokontroler memiliki ROM yang terus dikembangkan.
Mengapa Mikroprosesor Penting dalam Kontrol Proses Modern?
Mikroprosesor adalah tulang punggung modern pengendalian proses sistem karena kemampuannya untuk menangani algoritma yang kompleks, memproses data dalam jumlah besar, dan memberikan kontrol waktu nyata. Dalam pengaturan industri, mikroprosesor memungkinkan kontrol yang tepat atas berbagai parameter, sehingga menghasilkan peningkatan kualitas produk, pengurangan limbah, dan peningkatan keselamatan.
Misalnya, dalam Industri Permesinan, menjaga suhu yang konsisten sangat penting untuk mencegah pemuaian termal dan memastikan keakuratan komponen yang dikerjakan. Pendingin air industri kami, dilengkapi dengan teknologi canggih sistem kontrol mikroprosesor, dapat mempertahankan stabilitas suhu dalam toleransi yang ketat, menunjukkan peran penting mikroprosesor dalam mencapai presisi dan kualitas tinggi dalam proses manufaktur. kecepatan pemrosesan sistem penting dalam aplikasi ini.
Apa Komponen Utama MCS yang Efektif?
MCS yang efektif terdiri dari beberapa komponen utama yang bekerja secara harmonis:
- Mikroprosesor/Mikrokontroler: Unit pemrosesan inti yang menjalankan algoritma kontrol.
- Sensor: Perangkat yang mengukur parameter fisik seperti suhu, tekanan, dan laju aliran.
- Aktuator: Komponen yang melakukan tindakan kontrol, seperti menyetel katup atau menghidupkan motor.
- Antarmuka Pengguna: Sistem bagi operator untuk memantau dan berinteraksi dengan sistem kontrol.
- Catu Daya: Sumber daya yang stabil untuk memastikan pengoperasian yang andal.
Tabel: Komponen Utama MCS yang Efektif
Komponen | Fungsi | Contoh pada Pendingin Air |
Mikroprosesor | Menjalankan algoritma kontrol, memproses data | Mengontrol keseluruhan proses pendinginan |
Mikrokontroler | Mengelola tugas tertentu, antarmuka dengan sensor dan aktuator | Mengatur suhu, mengontrol pompa, mengelola alarm |
Sensor | Mengukur parameter fisik (suhu, tekanan, laju aliran) | Sensor suhu memantau suhu cairan pendingin |
Aktuator | Melaksanakan tindakan pengendalian (menyetel katup, menghidupkan motor) | Motor kompresor, motor pompa |
Antarmuka Pengguna | Memungkinkan operator untuk memantau dan berinteraksi dengan sistem | Layar sentuh untuk mengatur parameter dan melihat status |
Catu Daya | Memberikan daya yang stabil ke sistem | Memastikan pengoperasian semua komponen secara terus-menerus |
Komunikasi | Memungkinkan pertukaran data antara komponen dan sistem eksternal | Modbus, Ethernet/IP untuk integrasi dengan sistem kontrol pabrik |
Memori (RAM/ROM) | Menyimpan instruksi dan data program | Menyimpan algoritma kontrol, data sensor, dan pengaturan |
Masukan/Keluaran | Antarmuka dengan perangkat dan sinyal eksternal | Terhubung ke sensor, aktuator, dan peralatan lainnya |
Perangkat lunak | Program yang menentukan perilaku sistem dan mengontrol logika | Firmware, perangkat lunak aplikasi |
Fitur Keamanan | Melindungi sistem dan personel dari bahaya | Penghentian darurat, alarm, deteksi kesalahan |
Diagnostik | Memantau kesehatan sistem dan mengidentifikasi masalah | Rutinitas uji mandiri, pencatatan kesalahan |
Lampiran | Melindungi komponen dari faktor lingkungan | Kandang dengan peringkat IP untuk ketahanan terhadap debu dan air |
Sistem Pendingin | Mempertahankan suhu pengoperasian yang optimal untuk komponen elektronik | Kipas atau pendingin cairan untuk unit kontrol |
Di kami pendingin air gulir berpendingin air, komponen-komponen ini bekerja sama untuk mempertahankan kontrol suhu yang tepat. Sensor terus memantau suhu air, mikroprosesor memproses data ini, dan aktuator seperti kompresor dan kipas disesuaikan dengan tepat. Pendekatan terpadu ini memastikan kinerja dan efisiensi energi yang optimal.
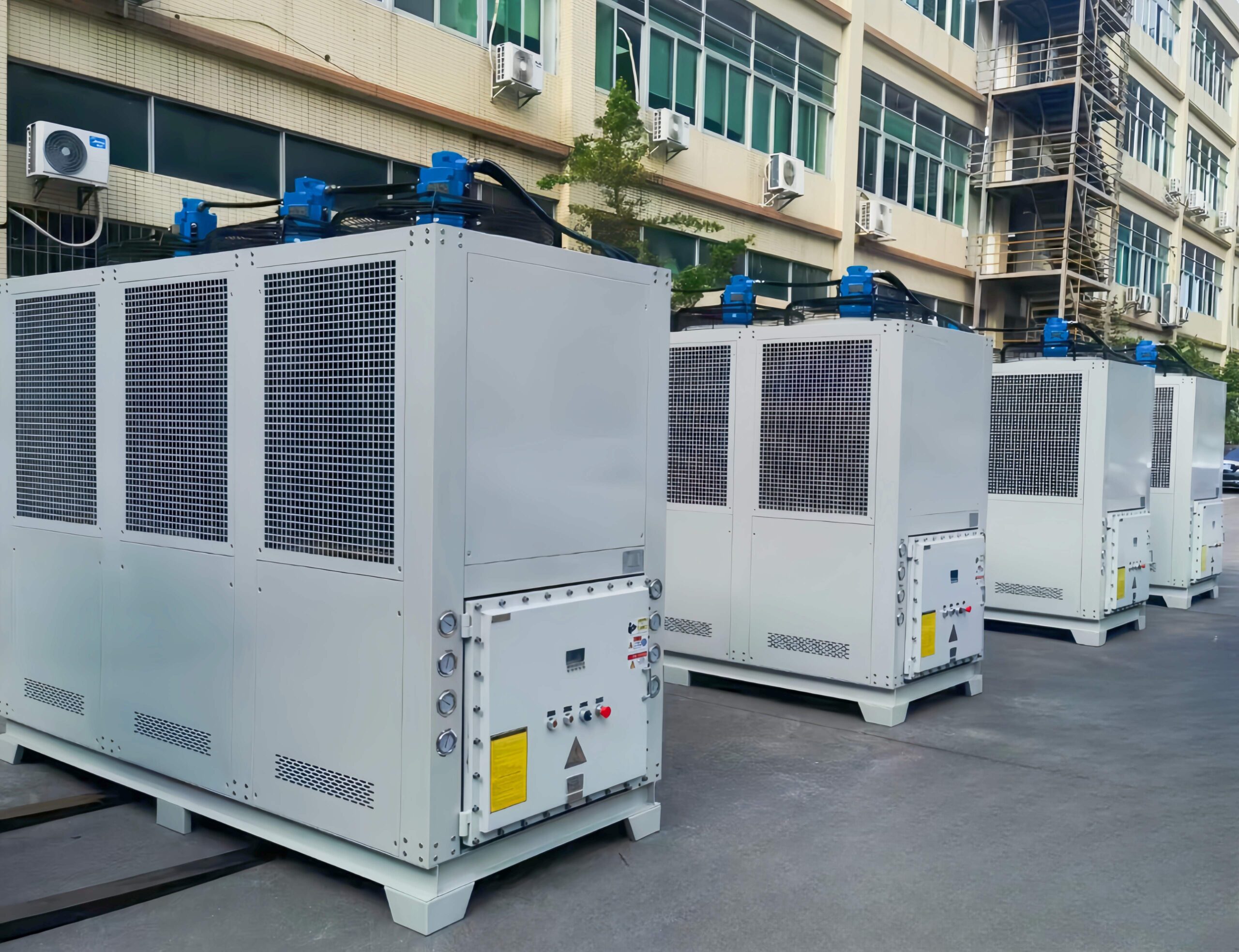
Bagaimana Sistem Tertanam Meningkatkan Fungsionalitas MCS?
Sistem tertanam, yang sering kali mencakup mikroprosesor, adalah sistem komputer khusus yang dirancang untuk melakukan tugas-tugas tertentu dalam sistem mekanik atau listrik yang lebih besar. Dalam konteks MCS, sistem tertanam meningkatkan fungsionalitas dengan menyediakan kontrol digital atas berbagai komponen, memungkinkan pemantauan waktu nyata, dan memfasilitasi komunikasi antara berbagai bagian sistem.
Misalnya, dalam pendingin air industri kami yang dirancang untuk Industri Medis, sistem tertanam memastikan bahwa parameter penting seperti suhu dan laju aliran dipertahankan dalam batasan yang ketat, penting untuk aplikasi seperti pendinginan mesin MRI. Banyak lagi mikroprosesor yang menjadi bagiannya dari sistem tertanam, menyediakan kontrol digital atas berbagai objek dari telepon seluler. Integrasi ini sistem tertanam ke MCS menunjukkan pentingnya mereka dalam meningkatkan keandalan dan kinerja.
Apa Peran Sistem Operasi dalam Kinerja MCS?
The sistem operasi (OS) dalam MCS sangat penting untuk mengelola sumber daya perangkat keras, menjadwalkan tugas, dan memastikan kelancaran eksekusi algoritma kontrol. OS yang dipilih dengan baik dapat berdampak signifikan pada kinerja, stabilitas, dan keandalan sistem secara real-time.
Dalam aplikasi industri yang kompleks, seperti di Industri Kimia dan Farmasi, OS yang kuat memastikan bahwa MCS dapat menangani beberapa tugas secara bersamaan tanpa mengorbankan kinerja. Pendingin air industri kami menggunakan teknologi canggih sistem operasi untuk mengelola berbagai fungsi, memastikan bahwa proses pendinginan penting tidak terganggu, dengan demikian menunjukkan pentingnya OS yang andal dalam menjaga efisiensi operasional.
Bagaimana MCS Dapat Meningkatkan Efisiensi dalam Industri Plastik dan Karet?
Industri Plastik dan Karet sangat bergantung pada kontrol suhu yang tepat selama berbagai tahap produksi, mulai dari pencetakan injeksi hingga ekstrusi. Penerapan MCS dapat meningkatkan efisiensi secara signifikan dengan:
- Mengoptimalkan Proses Pendinginan: Mikroprosesor dapat menyesuaikan parameter pendinginan secara dinamis berdasarkan umpan balik waktu nyata, memastikan laju pendinginan yang optimal dan mengurangi waktu siklus.
- Mengurangi Konsumsi EnergiDengan mengendalikan pengoperasian peralatan pendingin secara tepat, MCS meminimalkan pemborosan energi dan menurunkan biaya operasional.
- Meningkatkan Kualitas Produk: Kontrol suhu yang konsisten menghasilkan kualitas produk yang seragam, mengurangi cacat dan tingkat pemborosan.
Misalnya saja, kami pendingin industri untuk industri tekstil dirancang untuk memenuhi kebutuhan pendinginan khusus dari berbagai proses produksi tekstil. Dengan menggunakan MCS yang canggih, kami memastikan bahwa pendingin kami memberikan pendinginan yang tepat dan andal, sehingga meningkatkan produktivitas dan kualitas produk dalam industri tekstil. Gunakan mikroprosesor mesin sistem manajemen untuk mencapai tujuan ini.
Apa Manfaat Penerapan MCS dalam Industri Makanan dan Minuman?
Industri Makanan dan Minuman memerlukan kontrol suhu yang ketat untuk menjaga keamanan, kualitas, dan masa simpan produk. Penerapan MCS menawarkan beberapa manfaat:
- Peningkatan Keamanan Pangan: Kontrol suhu yang tepat mencegah pertumbuhan bakteri dan memastikan kepatuhan terhadap peraturan keamanan pangan.
- Peningkatan Konsistensi Produk:Pendinginan yang konsisten memastikan keseragaman dalam tekstur, rasa, dan penampilan produk.
- Peningkatan EfisiensiSistem kontrol otomatis mengurangi intervensi manual, menyederhanakan operasi, dan meminimalkan kesalahan manusia.
Kami pendingin glikol industri untuk pabrik bir adalah contoh utama bagaimana MCS dapat bermanfaat bagi Industri Makanan dan Minuman. Dengan mempertahankan suhu glikol yang tepat, pendingin kami memastikan kondisi fermentasi dan penyimpanan yang optimal, yang penting untuk menghasilkan bir berkualitas tinggi. Hal ini menunjukkan dampak signifikan MCS dalam menjaga kualitas produk dan efisiensi operasional.
Bagaimana MCS Mendukung Kepatuhan terhadap Standar Pengendalian Polusi yang Semakin Ketat?
Dengan standar pengendalian polusi yang semakin ketat, industri berada di bawah tekanan untuk meminimalkan dampak lingkungan mereka. MCS memainkan peran penting dalam mencapai kepatuhan dengan mengoptimalkan proses untuk mengurangi emisi dan limbah. sistem dapat memberikan strategi pengendalian itu akan menjadi tidak praktis untuk diterapkan menggunakan elektromekanis kontrol.
Misalnya, dalam Industri Kimia, kontrol yang tepat atas suhu reaksi dapat meminimalkan pembentukan produk sampingan yang berbahaya. Pendingin air industri kami, yang dilengkapi dengan MCS canggih, memungkinkan produsen kimia untuk mempertahankan kondisi reaksi yang optimal, mengurangi emisi, dan memastikan kepatuhan terhadap peraturan lingkungan. Hal ini menunjukkan bagaimana teknologi MCS mendukung praktik industri yang berkelanjutan dan bertanggung jawab terhadap lingkungan. Standar pengendalian polusi yang ketat secara efektif memerlukan sistem pengendalian emisi mobil untuk menggunakan mikroprosesor.
Mengapa Memilih Pendingin Air Industri Kami dengan Teknologi MCS Canggih?
Sebagai produsen terkemuka pendingin air industri, kami memahami peran penting kontrol suhu yang tepat dalam berbagai industri. Pendingin kami dilengkapi dengan teknologi canggih sistem kontrol mikroprosesor dirancang untuk memberikan kinerja, keandalan, dan efisiensi yang tak tertandingi.
Inilah alasan mengapa Anda harus memilih produk kami:
- KustomisasiKami menawarkan solusi khusus untuk memenuhi kebutuhan spesifik berbagai industri, dari Plastik dan Karet hingga Pusat Data.
- Teknologi Canggih:Pendingin kami menggabungkan kemajuan terbaru dalam mikroprosesor dan mikrokontroler teknologi, memastikan kinerja optimal dan efisiensi energi.
- Keandalan:Dengan kuat desain sistem dan pengujian yang ketat, pendingin kami dibuat untuk menahan tuntutan lingkungan industri.
- Dukungan Ahli:Tim ahli kami menyediakan dukungan komprehensif, dari desain sistem hingga pemasangan dan pemeliharaan, memastikan integrasi dan pengoperasian yang lancar.
Dengan memilih pendingin air industri kami, Anda berinvestasi dalam teknologi MCS mutakhir yang akan meningkatkan efisiensi operasional Anda, meningkatkan kualitas produk, dan mendukung tujuan keberlanjutan Anda.
Pertanyaan Umum
Industri apa yang dapat memperoleh manfaat dari pendingin air industri Anda?
Pendingin air industri kami dirancang untuk memenuhi kebutuhan berbagai industri, termasuk Plastik dan Karet, Permesinan, Makanan dan Minuman, Kimia dan Farmasi, Elektronik, Laser, Percetakan, Medis, Laboratorium dan Lembaga Penelitian, dan Pusat Data.
Bagaimana sistem kontrol mikroprosesor pada pendingin Anda meningkatkan efisiensi energi?
The sistem kontrol mikroprosesor pada pendingin kami mengoptimalkan pengoperasian komponen pendingin berdasarkan data waktu nyata, meminimalkan konsumsi energi sekaligus mempertahankan kontrol suhu yang tepat. Hal ini menghasilkan penghematan energi yang signifikan dan mengurangi biaya operasional.
Dapatkah pendingin Anda diintegrasikan dengan sistem kontrol pabrik yang ada?
Ya, pendingin kami dirancang agar dapat diintegrasikan dengan sistem kontrol pabrik yang ada. Pendingin kami mendukung berbagai protokol komunikasi, sehingga memungkinkan pemantauan dan kontrol terpusat.
Dukungan seperti apa yang Anda tawarkan untuk produk Anda?
Kami menawarkan dukungan menyeluruh, termasuk desain sistem, pemasangan, pelatihan, dan pemeliharaan. Tim ahli kami siap membantu Anda di seluruh proses, memastikan kinerja dan keandalan yang optimal.
Bagaimana pendingin Anda membantu mematuhi peraturan lingkungan?
Chiller kami, dilengkapi dengan MCS canggih, memungkinkan kontrol yang tepat atas proses industri, mengurangi emisi, meminimalkan limbah, dan membantu industri mematuhi standar pengendalian polusi yang semakin ketat.
Apa yang membuat teknologi MCS Anda lebih unggul dari sistem kontrol tradisional?
Teknologi MCS kami menawarkan fleksibilitas, presisi, dan kemampuan beradaptasi yang lebih baik dibandingkan dengan teknologi tradisional kontrol elektromekanis atau kontrol elektronik yang dibuat khususHal ini memungkinkan penyesuaian waktu nyata, pemantauan jarak jauh, dan integrasi yang lancar dengan sistem lain, sehingga meningkatkan efisiensi operasional secara keseluruhan.
Kesimpulan
- Sistem Kontrol Mikroprosesor (MCS) merevolusi kontrol proses industri dengan menawarkan presisi, fleksibilitas, dan efisiensi yang tak tertandingi.
- Mikroprosesor dan mikrokontroler memainkan peran yang berbeda namun saling melengkapi dalam sistem otomasi modern.
- Sistem tertanam meningkatkan fungsionalitas MCS dengan menyediakan kontrol waktu nyata dan integrasi yang mulus.
- Sebuah yang kuat sistem operasi sangat penting untuk kinerja MCS yang andal di lingkungan industri yang menuntut.
- Penerapan MCS dapat secara signifikan meningkatkan efisiensi, kualitas produk, dan kepatuhan terhadap standar lingkungan di berbagai industri.
- Pendingin air industri kami, dilengkapi dengan teknologi MCS yang canggih, menawarkan solusi yang disesuaikan, teknologi mutakhir, keandalan, dan dukungan ahli untuk memenuhi kebutuhan pelanggan kami yang terus berkembang.
Dengan menggunakan teknologi MCS, industri dapat mencapai tingkat kinerja, efisiensi, dan keberlanjutan yang baru. Sebagai mitra tepercaya, kami berkomitmen untuk menyediakan solusi inovatif yang memberdayakan pelanggan kami untuk berkembang dalam lanskap persaingan saat ini. Hubungi kami hari ini untuk mempelajari lebih lanjut tentang bagaimana pendingin air industri kami dengan teknologi MCS yang canggih dapat mengubah operasi Anda.
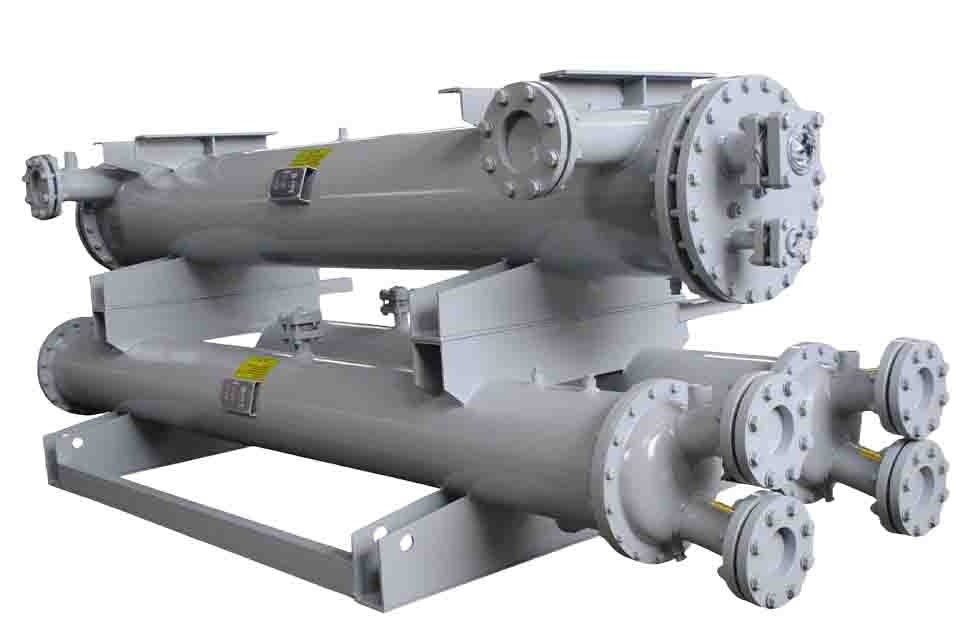