-
Dalingshan Industrial Guangdong
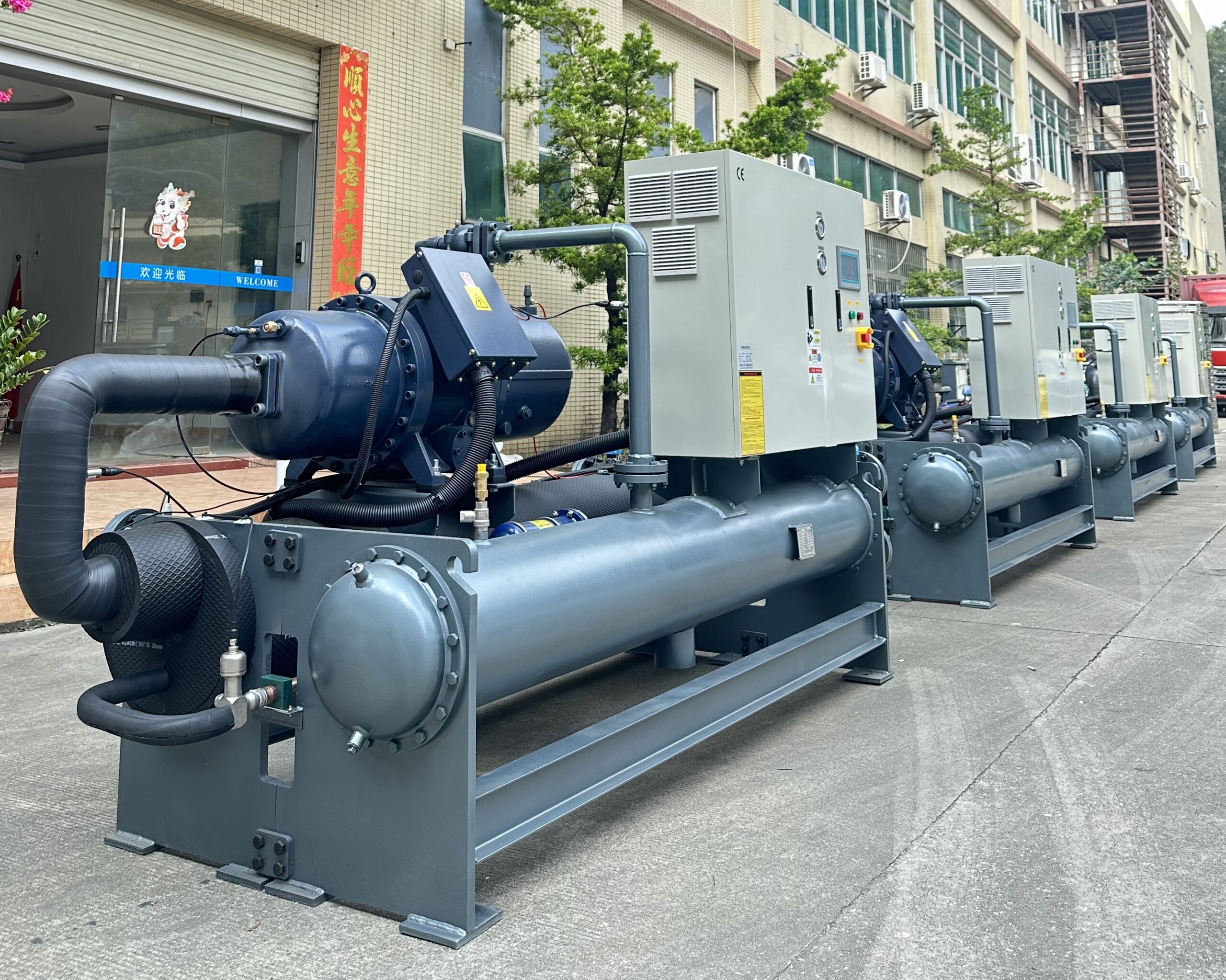
How To Decide A Industrial Chiller Solutions For Peak Performance
Industrial Chiller Solutions For Peak Performance
Looking for reliable industrial chiller solutions to boost your manufacturing efficiency? This guide explains how industrial chillers optimize processes like plastic molding, food production, and metalworking. The right system enhances productivity, quality, and cost savings.
Article Outline:
- What is an Industrial Chiller and Why is it Essential for Industrial Processes?
- Understanding Different Types of Chillers: Air-Cooled vs. Water-Cooled Industrial Chillers?
- How Does a Process Chiller Ensure Consistent Temperature Control in Manufacturing?
- What are the Key Industrial Applications That Rely on Industrial Cooling Systems?
- Why is a Reliable Cooling System Crucial for Maintaining Uptime in Production?
- What Factors Should You Consider When Choosing an Industrial Process Chiller for Your Specific Needs?
- Can an Efficient Chiller System Contribute to Energy Savings and Cost Reduction?
- What are the Benefits of Integrating Advanced Technologies into Industrial Chillers?
- How Can the Right Industrial Water Chiller Improve the Quality and Efficiency of Plastic Manufacturing Processes?
- Beyond Plastic: What Other Industrial Applications Benefit from Precise Process Cooling?
- Ensuring Longevity and Performance: What Maintenance is Required for an Industrial Chiller?
- Ready to Elevate Your Operations with a Superior Chiller?
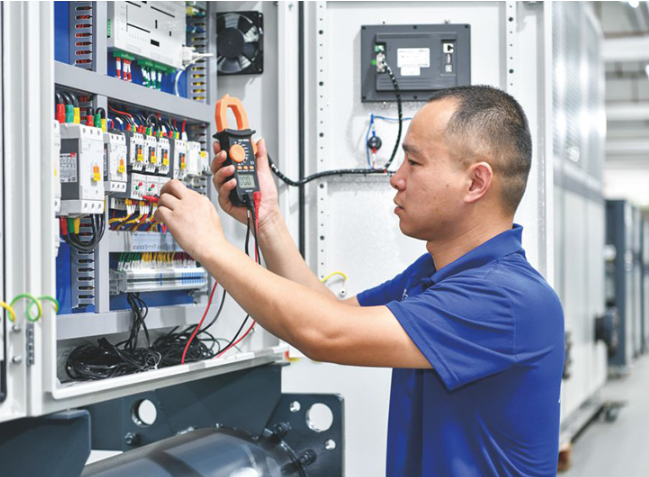
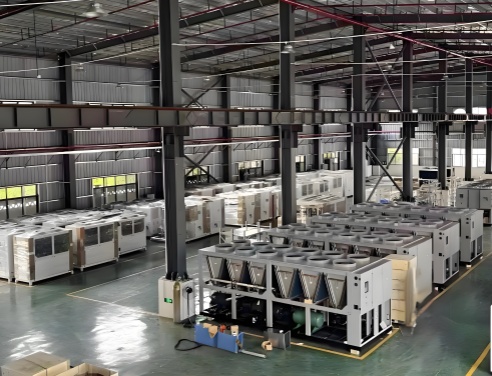
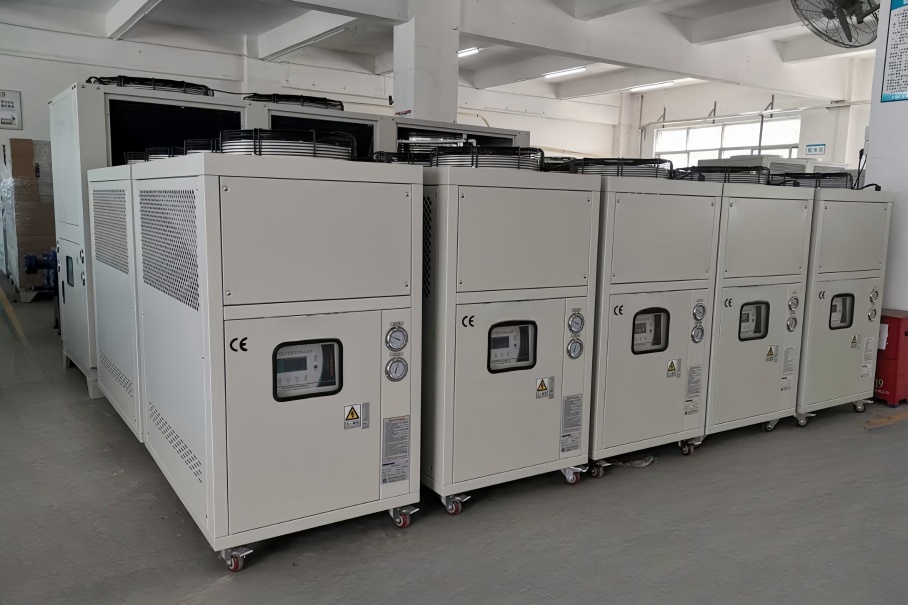
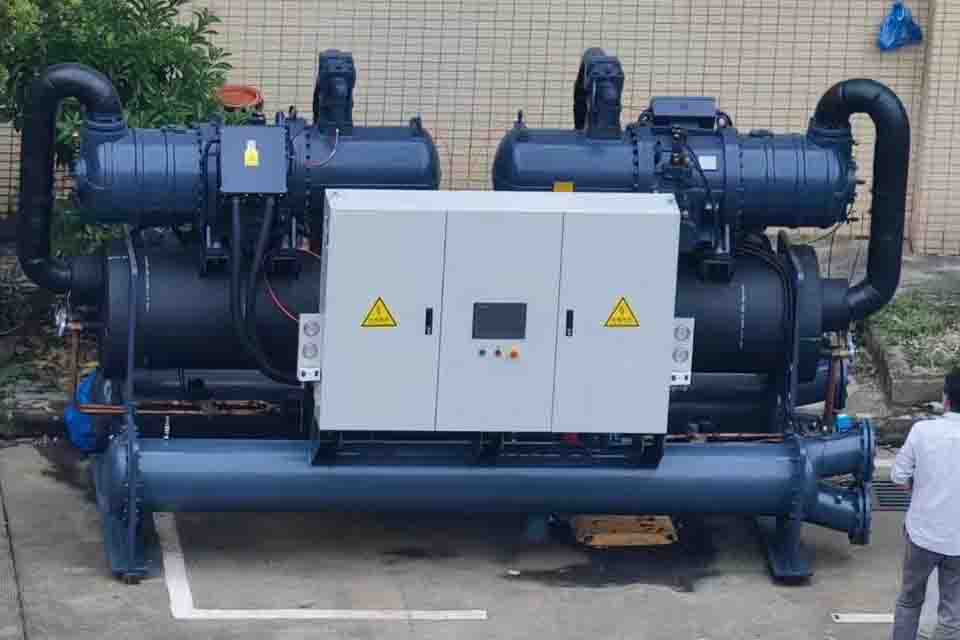
1. What is an Industrial Chiller and Why is it Essential for Industrial Processes?
Chillers remove heat from liquids (water/glycol) to cool equipment, preventing overheating and downtime. Essential for stable operations in plastics, food processing, and more.
As an experienced provider of industrial chiller solutions, we understand the pivotal role these systems play in a vast array of industrial processes.
In the realm of manufacturing, consistent and precise process cooling is often not just beneficial – it’s absolutely essential. Many industrial applications generate significant amounts of heat as a byproduct of their operation. Without an efficient cooling system, this excess heat can cause machinery to malfunction, reduce production rates, and even pose safety risks.
2. Understanding Different Types of Chillers: Air-Cooled vs. Water-Cooled Industrial Chillers?
When considering an industrial chiller, one of the first decisions you’ll face is choosing between an air-cooled and a water-cooled model. Both types of chillers achieve the same fundamental goal – providing process cooling – but they differ significantly in how they dissipate the heat they extract. As a provider of a comprehensive chiller range, we offer both technologies to cater to diverse cooling needs and facility requirements.
Air-Cooled: Uses ambient air; easier to install, ideal for water-scarce areas.
Air-cooled chillers, as the name suggests, use ambient air to cool the refrigerant in their condenser. They are generally easier to install and maintain as they don’t require a connection to a cooling water source like a cooling tower. This makes them a popular choice for applications where water availability or quality is a concern, or for smaller installations. On the other hand, water-cooled industrial chillers transfer heat from the refrigerant to a circulating cooling water loop, which then typically dissipates the heat through a cooling tower or a connection to city water. Water-cooled systems are often more energy-efficient, especially in larger capacities, and can offer more stable cooling temperatures. The choice between air-cooled industrial and water-cooled ultimately depends on factors like your facility’s infrastructure, energy efficiency goals, budget, and the specific demands of your industrial process cooling application. We can help you navigate these considerations to select the most suitable chiller system for your needs.
3. How Does a Process Chiller Ensure Consistent Temperature Control in Manufacturing?
Chillers maintain precise temps via a refrigeration cycle (compressor → condenser → evaporator), critical for product consistency and equipment longevity.
The chiller works by circulating a refrigerant through this closed loop. The compressor increases the pressure and temperature of the refrigerant vapor. This high-pressure, high-temperature vapor then flows to the condenser, where it releases heat and condenses into a high-pressure liquid. Next, the liquid refrigerant passes through an expansion valve, causing its pressure and temperature to drop significantly. This low-pressure, low-temperature refrigerant then enters the evaporator, where it absorbs heat from the process water or other fluid being cooled. The warmed refrigerant then turns back into a low-pressure vapor and returns to the compressor, restarting the cycle. Advanced chiller systems often incorporate sophisticated controls and sensors that continuously monitor fluid temperatures and adjust the refrigeration cycle to maintain the desired set point with remarkable accuracy. This precise temperature control provided by the process chiller is vital for achieving consistent product quality, optimizing cycle times, and preventing equipment damage in a wide range of industrial settings.
4. What are the Key Industrial Applications That Rely on Industrial Cooling Systems?
Our industrial chillers serve a diverse range of industrial applications, underscoring the widespread need for reliable industrial cooling. As specialists in industrial process cooling, we cater to numerous sectors where precise temperature control is critical.
One of the primary areas is plastics manufacturing, encompassing processes like plastic extrusion manufacturing, injection molding machine, blow molding, compression molding, rotational molding, transfer molding, thermoforming, and operation of bottle blowing machine and casting film machine.
Beyond plastics, our industrial chillers are also essential in industries such as:
- Food processing: Maintaining precise temperatures for food safety and quality during various stages of production.
- Metalworking: Cooling welding equipment (weld), machining tools, and heat-treating processes.
- Chemical and pharmaceutical: Controlling reaction temperatures and ensuring the stability of sensitive materials.
- Laser cutting and welding: Dissipating heat generated by high-power lasers.
- Printing: Maintaining optimal temperatures for printing presses and inks.
- HVAC: Providing chilled water for large-scale air conditioning systems. You can explore our range of HVAC Chillers.
- Agriculture: For controlled environment agriculture and hydroponic water chiller systems.
- Concrete production: Utilizing a water chiller for concrete batch plant to control the temperature of the concrete mix.
- Dairy: Our Dairy Milk Chillers ensure rapid and efficient cooling of milk.
- Brewing: Specialized Industrial Glycol Chillers For Brewery for precise fermentation temperature control.
This wide range of industrial use cases highlights the versatility and importance of industrial cooling provided by our chiller solutions.
5. Why is a Reliable Cooling System Crucial for Maintaining Uptime in Production?
Proper cooling reduces equipment wear, prevents failures, and extends production runs
In the fast-paced world of manufacturing, uptime is paramount. A reliable cooling system, particularly an industrial process chiller, is a cornerstone of operational continuity. As a trusted source for efficient and reliable industrial chillers for a wide range of applications, we understand that preventing overheating is key to maximizing uptime.
Without adequate process cooling, machinery operating under heavy loads can experience excessive heat buildup. By effectively removing heat, our chillers help maintain safe operating temperature ranges for your process equipment, extending their lifespan and reducing the likelihood of breakdowns. A well-maintained chiller system acts as a preventative measure against costly repairs and unexpected downtime, ensuring that your production lines keep running smoothly and efficiently.
6. What Factors Should You Consider When Choosing an Industrial Process Chiller for Your Specific Needs?
Selecting the right industrial process chiller is a critical decision that can significantly impact the efficiency and cost-effectiveness of your operations. As experts with decades of experience in the chiller industry, we advise considering several key factors to ensure you choose a system that perfectly aligns with your specific cooling needs.
First and foremost, understanding your cooling load is essential. This involves calculating the amount of heat that needs to be removed from your industrial process to maintain the desired operating temperature. Factors like the type of material being processed, the size and speed of your equipment, and the ambient temperature all contribute to the cooling load. Next, you need to determine the required temperature of the process water or coolant.
Other important considerations include:
- Chiller type: As discussed earlier, deciding between air-cooled and water-cooled industrial chillers based on your facility’s infrastructure and environmental conditions.
- Energy efficiency: Opting for an energy-efficient chiller can lead to significant cost savings over the long term. Look for features like high-efficiency compressor types and intelligent controls. Our ecodesign principles ensure energy saving in our units.
- Refrigerant type: Consider the environmental impact and regulatory requirements related to the refrigerant used in the chiller.
- Footprint and installation: Ensure that the chiller you choose fits within your available space and that your facility can accommodate the necessary electrical and plumbing connections. Our plug and play options offer ready for quick installation.
- Control system: A user-friendly and sophisticated control system can provide precise temperature control and allow for easy monitoring and integration with other equipment. Our smartlink technology offers advanced control capabilities.
- Maintenance requirements: Consider the ease of maintenance and the availability of service and support.
- Budget: Evaluate the initial investment cost as well as the long-term operating costs, including energy consumption and maintenance.
By carefully evaluating these factors, you can make an informed decision and select an industrial process chiller that will provide reliable and cost-effective cooling solutions for your specific industrial applications. We are here to guide you through this process and help you find the ideal chiller range for your unique requirements.
7. Can an Efficient Chiller System Contribute to Energy Savings and Cost Reduction?
As a provider of energy-efficient industrial chillers, we understand the importance of minimizing energy consumption while maximizing cooling performance.
Modern chiller technologies incorporate several features designed to enhance energy efficiency. These include:
- High-efficiency compressor types, such as scroll and screw compressors, which offer improved performance and lower energy consumption compared to older technologies. Our Water Cooled Scroll Water Chiller and Water Cooled Screw Water Chiller lines exemplify this efficiency.
- Optimized condenser and evaporator designs that maximize heat transfer efficiency.
- Intelligent control systems that precisely match cooling capacity to the actual load, preventing unnecessary energy usage.
- Variable speed drives (VSDs) that allow the compressor and fans to operate at variable speeds, further reducing energy consumption during partial load conditions.
- Free-cooling capabilities, which utilize ambient air to provide cooling when the outside temperature is low enough, reducing the reliance on the refrigeration cycle.
By choosing an energy-efficient industrial water chiller, you can significantly lower your electricity bills, reduce your carbon footprint, and potentially qualify for energy rebates or incentives. We are committed to providing cooling solutions that are not only reliable but also environmentally responsible and economically advantageous for our customers.
8. What are the Benefits of Integrating Advanced Technologies into Industrial Chillers?
The integration of advanced technologies into industrial chillers offers a multitude of benefits, enhancing their performance, reliability, and ease of use. As innovators in chiller systems, we continuously incorporate cutting-edge technologies into our products to provide our customers with the most advanced cooling solutions available.
One significant advancement is in control systems. Modern chillers often feature sophisticated microprocessors and programmable logic controllers (PLCs) that provide precise temperature control, real-time monitoring of operating parameters, and advanced diagnostic capabilities. Our smartlink system, for example, allows for remote monitoring and control, providing valuable insights into chiller performance and enabling proactive maintenance.
Advancements in heat exchanger design have led to more compact and efficient condenser and evaporator units. Technologies like microchannel heat exchangers enhance heat transfer while reducing the amount of refrigerant required.
The integration of these and other advanced technologies results in chillers that offer:
- Improved energy efficiency and lower operating costs.
- More precise and stable temperature control.
- Enhanced reliability and reduced downtime.
- Easier operation and maintenance through user-friendly interfaces and remote monitoring capabilities.
- Advanced diagnostics for proactive maintenance and troubleshooting.
- Smaller footprints and reduced space requirements.
By embracing these technological advancements, we ensure that our industrial chillers provide our customers with the most efficient and effective cooling solutions for their critical industrial processes.
9. How Can the Right Industrial Water Chiller Improve the Quality and Efficiency of Plastic Manufacturing Processes?
In the demanding world of plastic extrusion manufacturing, injection molding machine operation, and other plastic processing techniques, the role of an industrial water chiller is absolutely critical for both product quality and production efficiency. As a leading provider of chillers for a variety of plastic industry needs, we understand the specific demands of these processes.
Precise temperature control of the molds or dies is paramount in achieving high-quality plastic parts. Inconsistent or inadequate cooling can lead to a range of defects, including warping, sink marks, surface imperfections, and dimensional inaccuracies. The right industrial water chiller ensures that the mold temperature is maintained at the optimal level throughout the production cycle, resulting in consistent part quality and reduced scrap rates. Our chillers are specially designed for the unique cooling needs of plastic processing.
Furthermore, an efficient chiller system directly impacts cycle times. Faster and more effective cooling allows the plastic material to solidify more quickly, reducing the time the part needs to remain in the mold. This translates to increased production output and improved overall efficiency. A properly sized and well-maintained industrial water chiller can significantly reduce cycle times, leading to higher production volumes and lower per-part costs.
Whether you are involved in blow molding, thermoforming, or operating a bottle blowing machine or casting film machine, having a reliable industrial water chiller is essential for achieving consistent quality, optimizing cycle times, and maximizing the profitability of your plastic manufacturing operations. We offer a range of chillers for a wide range of plastic processing applications, ensuring that you have the perfect cooling solution for your specific needs.
10. Beyond Plastic: What Other Industrial Applications Benefit from Precise Process Cooling?
While the plastics industry heavily relies on industrial chillers, a wide range of industrial processes across various sectors benefit significantly from precise process cooling. Our chillers are designed to meet the diverse cooling needs of these industries.
In the food processing industry, chillers play a vital role in maintaining food safety and quality. They are used for cooling ingredients, controlling fermentation temperatures, and chilling finished products to prevent spoilage and ensure compliance with stringent regulations.
Metalworking industries utilize industrial cooling for various applications, including cooling welding equipment to prevent overheating and maintain weld quality, cooling machining tools to extend their lifespan and improve cutting accuracy, and controlling the temperature of quenching baths in heat-treating processes. Our Explosion-Proof Chillers can be crucial in certain metalworking environments.
The chemical and pharmaceutical industries rely on precise temperature control for chemical reactions, crystallization processes, and the storage of temperature-sensitive materials. Our Anti-Explosion Chillers are particularly relevant in these sectors where flammable substances may be present.
In the realm of advanced manufacturing, chillers are essential for cooling high-power lasers used in cutting, welding, and marking applications. The stable temperature provided by the chiller ensures consistent laser performance and prevents damage to the laser source.
Furthermore, industrial cooling is critical for data centers to dissipate the heat generated by servers and other electronic equipment, preventing overheating and ensuring reliable operation. Even seemingly unrelated applications like resistance welding benefit from efficient cooling to improve weld quality and electrode life.
This broad spectrum of applications underscores the fundamental role of industrial chillers in enabling efficient and reliable operations across a variety of industries. Our experience in the chiller industry allows us to provide tailored cooling solutions for even the most demanding industrial process cooling application needs.
11. Ensuring Longevity and Performance: What Maintenance is Required for an Industrial Chiller?
To ensure the longevity and optimal performance of your industrial chiller, regular and proactive maintenance is essential. As experienced providers of cooling equipment, we understand that a well-maintained chiller system will operate more efficiently, experience fewer breakdowns, and have a longer lifespan.
Key maintenance tasks for an industrial chiller include:
- Regularly inspecting and cleaning the condenser coils. Dust, dirt, and debris can accumulate on the coils, reducing their heat transfer efficiency and increasing energy consumption. For air-cooled chillers, this is a particularly important task.
- Monitoring and maintaining the proper refrigerant levels. Low refrigerant can significantly impact cooling capacity and efficiency.
- Checking for leaks in the refrigerant lines and other components.
- Regularly inspecting and cleaning or replacing air filters (in air-cooled units).
- Monitoring the temperature and pressure of the process water or coolant.
- Checking the pump and motor for proper operation and any signs of wear or leaks.
- Inspecting electrical connections for tightness and corrosion.
- Periodically analyzing the coolant to ensure proper pH levels and the absence of contaminants. For systems using glycol, maintaining the correct glycol concentration is crucial.
- Following the manufacturer’s recommended maintenance schedule for specific components like the compressor.
Implementing a preventative maintenance program, which includes these regular checks and servicing, can help identify potential issues early on, preventing costly breakdowns and ensuring that your industrial chiller continues to provide reliable and cost-effective cooling solutions for years to come. Proper maintenance is a small investment that yields significant returns in terms of uptime, efficiency, and the overall lifespan of your chiller system.
12. Ready to Elevate Your Operations with a Superior Chiller?
As you’ve learned, a reliable and efficient industrial chiller is not just a piece of equipment; it’s a critical component that underpins the success of a wide range of industrial processes, from plastic extrusion manufacturing to food processing. At [Your Company Name – implied by “we” throughout the text], we pride ourselves on being a trusted source for high-quality industrial water chiller and industrial process chiller solutions. With decades of experience in the chiller industry, we understand your unique cooling needs and are committed to providing efficient and reliable industrial chillers for a wide range of industrial applications.
Whether you need a robust air-cooled chiller, a high-capacity water-cooled system, or a specialized chiller for a specific application like hydroponic water chiller or brewery glycol chillers, we have the expertise and the product range to meet your requirements. Our chillers are specially designed to deliver precise temperature control, maximize energy efficiency, and ensure the uptime of your critical process equipment.
Don’t let inefficient cooling compromise your productivity or product quality. Contact us today to discuss your industrial cooling needs and discover how our chiller systems can elevate your operations to the next level. Let our experience in the chiller industry work for you. Get a quote today and experience the difference that a superior industrial chiller can make! Consider our Water Cooled Screw Central Chillers for larger applications or our Air Cooled Scroll Water Chiller for a versatile solution.
What is the difference between an air-cooled and a water-cooled industrial chiller?
connected to a cooling tower or other water source. Air-cooled units are generally easier to install, while water-cooled systems can be more energy-efficient for larger capacities.
What are the benefits of using a glycol chiller?
Glycol chillers use a mixture of water and glycol as the coolant, which allows for operation at temperatures below the freezing point of water. This is essential for applications like food processing and breweries where very low temperatures are required.
How often does an industrial chiller need maintenance?
The frequency of maintenance depends on the operating environment and the type of chiller. However, regular inspections and preventative maintenance tasks should be performed at least semi-annually, or recommendation from manufacturer.
Can an old or inefficient chiller increase my energy costs?
older or poorly maintained chillers can consume significantly more energy than modern, efficient models. Upgrading to a new, energy-efficient chiller can lead to substantial savings on your electricity bills.
What happens if my industrial chiller breaks down?
A chiller breakdown can lead to production shutdowns, equipment damage due to overheating, and potential financial losses. Having a reliable maintenance plan and a responsive service provider is crucial to minimize downtime.