-
Dalingshan Industrial Guangdong
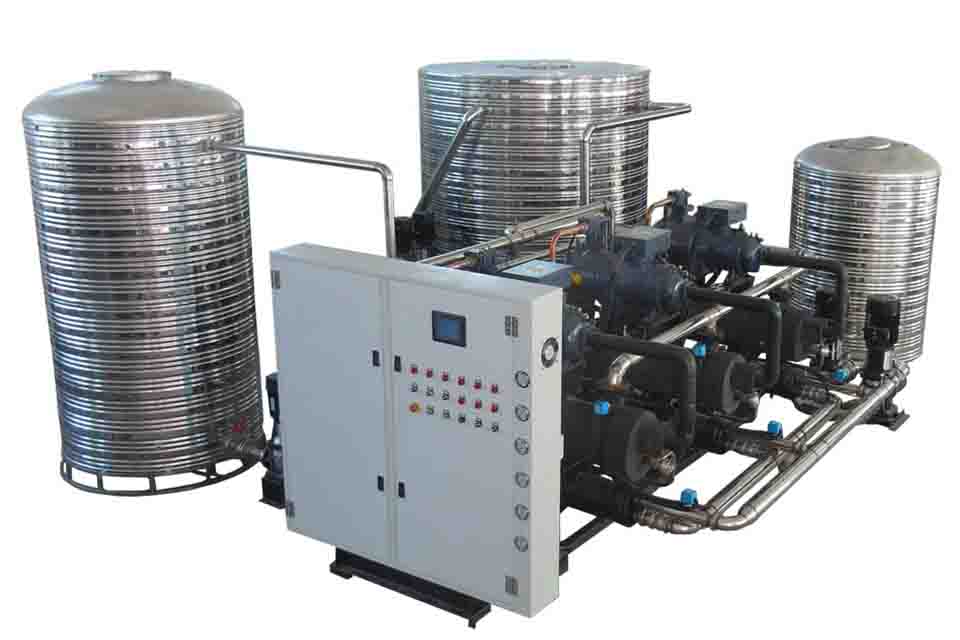
8 industrial chiller applications
8 Ton Air-Cooled Industrial Process Chiller System: The Ultimate Cooling Solution
This article will delve into the intricacies of industrial Kältemaschinen, specifically focusing on an 8 ton luftgekühlt industrial process chiller system. We’ll explore how these systems work, their applications across various industries, and why understanding them is crucial for businesses seeking efficient Kühlung solutions. Whether you’re in the plastics industry, food and beverage sector, or managing a data center, this article will provide valuable insights into selecting, maintaining, and optimizing your industrial chiller system, making it a worthwhile read for anyone looking to enhance their operational efficiency and product quality.
Inhaltsübersicht
What is an Industrial Chiller and How Does it Work?
As an industrial water chiller manufacturing plant, we specialize in creating high-performance Kühlung solutions tailored to a wide range of industries. An industrial chiller is essentially a refrigeration system that removes heat from a process or piece of equipment. Unlike standard air conditioners, Kältemaschinen are designed to handle the demanding Kühlung needs of industrial processes. Industrial chillers work by circulating a coolant, such as water or a water/glycol mixture, through the equipment to absorb heat.
Industrielle Kältemaschinen play a critical role in many processes by ensuring that machinery operates within optimal temperature ranges. This not only prevents overheating and potential damage but also improves the efficiency and longevity of the equipment. Chillers use a vapor-compression or absorption refrigeration cycle to cool the fluid, which is then circulated to remove heat from the process. The basic principle involves a refrigerant changing states – from a low-pressure gas to a high-pressure liquid and back again – to transfer heat away from the industrial process.
What are the Main Types of Industrial Chillers?
There are primarily two types of industrial chillers: luftgekühlt und wassergekühlt. The choice between these depends on the specific needs of the application. Air-cooled chillers use ambient air to dissipate heat from the refrigerant. They are typically used in smaller applications or where water availability is limited. These units are easier to install and maintain compared to wassergekühlt Kältemaschinen and are often more cost-effective in terms of initial investment.
Water-cooled chillers, on the other hand, use water from a cooling tower or other water source to remove heat. These are ideal for larger industrial processes that require greater Kühlung capacity and more stable temperatures. The types of chillers will influence how effectively heat is dissipated. The key difference is in the method used by the condenser to reject heat. Air-cooled chillers use fans to blow ambient air over the condenser coils, while wassergekühlte Kältemaschinen use water.
Why Choose an 8 Ton Air-Cooled Chiller?
An 8 ton air-cooled chiller represents a sweet spot for many industrial applications, offering a balance of Kühlung capacity and efficiency. This size is particularly suitable for medium-scale operations where precise temperature control is needed but a larger wassergekühlt system may be overkill. From my experience, an air-cooled chiller is preferred in environments where water conservation is a priority or where space is at a premium. An 8 ton air-cooled chiller also simplifies installation, as it does not require integration with a separate cooling tower or water source.
Choosing the right industrial chiller involves evaluating your Prozesskühlung needs, available space, and budget. An 8 ton unit is often selected for its versatility, capable of supporting a variety of industrial applications, from plastic injection molding to food processing. The main advantage of an luftgekühlt unit is its simplicity and lower maintenance requirements, making it an attractive option for many businesses. Our capabilities provide the ideal cooling solution for many industrial needs, contact us today to learn more.
What are the Key Components of a Chiller System?
Understanding the key components of a chiller system is crucial for anyone involved in its operation or maintenance. The primary components include the compressor, condenser, expansion valveund evaporator. The compressor is the heart of the system, responsible for compressing the refrigerant gas, which increases its temperature and pressure. As a manufacturer, we ensure that our compressors are robust and efficient, capable of withstanding the rigors of continuous industrial use.
Die condenser then cools the high-pressure refrigerant, causing it to condense into a liquid. In air-cooled chillers, this is achieved by blowing air over the condenser coils, while in wassergekühlt units, water is used. The expansion valve reduces the pressure of the liquid refrigerant, allowing it to expand and cool further. Finally, the evaporator absorbs heat from the process fluid, causing the refrigerant to vaporize and start the cycle anew.
How Do Industrial Chillers Use Refrigerant in the Cooling Process?
Kältemittel is the lifeblood of any industrial chiller, playing a pivotal role in the cooling process. The choice of refrigerant can significantly impact the efficiency and environmental footprint of the system. Chillers use refrigerant to absorb and transfer heat away from the process. The process begins when low-pressure gas enters the compressor. Inside the compressor, the gas is compressed, leading to an increase in both its pressure and temperature.
This high-pressure, high-temperature gas then moves to the condenser, where it releases heat and condenses into a high-pressure liquid. In luftgekühlt systems, this heat is dissipated into the ambient air, while in wassergekühlt systems, it is carried away by the condenser water. The high-pressure liquid then passes through the expansion valve, where its pressure drops, causing it to cool and partially evaporate. Finally, this cold, low-pressure refrigerant flows through the evaporator, absorbing heat from the process fluid and vaporizing completely, before returning to the compressor to repeat the cycle.
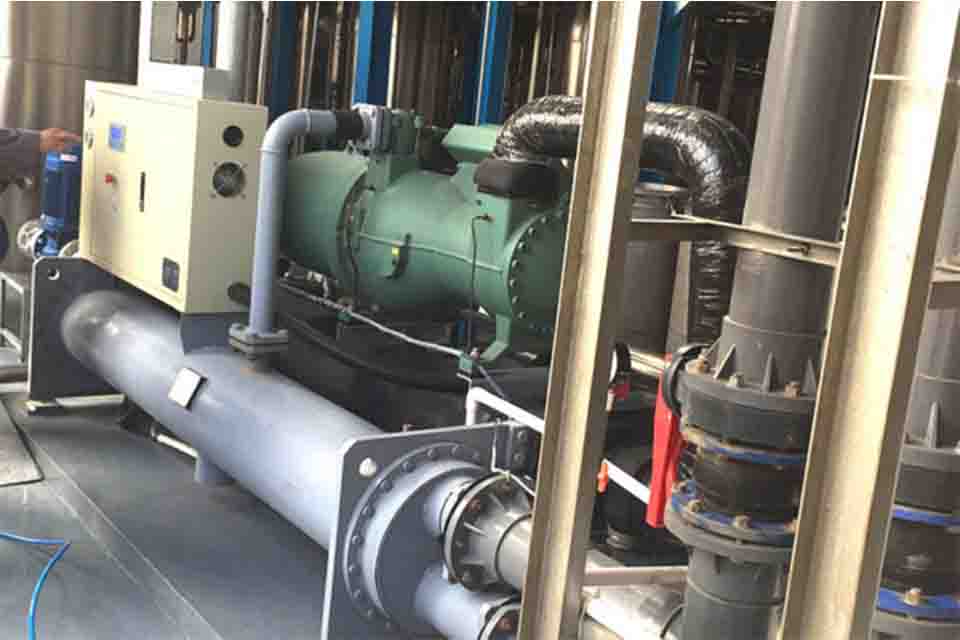
What Industries Benefit Most from Industrial Chiller Applications?
Industrial chiller applications are vast and varied, with many sectors relying on these systems to maintain product quality and operational efficiency. The plastics and rubber industry, for example, uses Kältemaschinen to cool molds and extruded products, ensuring dimensional stability and preventing defects. Similarly, the machining industry uses process chillers to cool cutting tools and workpieces, improving precision and extending tool life.
The food and beverage industry benefits significantly from Industriekälteanlagen, using them to cool ingredients, maintain fermentation temperatures, and preserve perishable goods. In the chemical and pharmaceutical sectors, Kältemaschinen are essential for controlling reaction temperatures and ensuring the safety and stability of processes. Other industries that rely heavily on Kältemaschinen include electronics manufacturing, laser cutting, printing, medical imaging, and data centers.
Here is a table summarizing some key industries and their specific uses for Industriekälteanlagen:
Industry | Use Case |
Plastics and Rubber | Cooling molds, extruded products |
Machining | Cooling cutting tools, workpieces |
Food and Beverage | Industrial Glycol Chillers For Brewery , Cooling ingredients, fermentation |
Chemical and Pharmaceutical | Controlling reaction temperatures |
Electronics | Cooling sensitive components, circuit boards |
Laser | Cooling laser heads, optics |
Printing | Maintaining ink viscosity, cooling rollers |
Medical | Cooling MRI machines, other imaging equipment |
Data Centers | Cooling servers, maintaining optimal operating conditions |
What Role Does a Cooling Tower Play in Industrial Cooling?
While air-cooled chillers rely on ambient air for heat dissipation, wassergekühlte Kältemaschinen often utilize a cooling tower as part of their Kühlung system. A cooling tower is a specialized heat exchanger that removes heat from water by evaporating a small portion of it. This evaporative cooling process allows the remaining water to be significantly cooled, which is then used to absorb heat in the chiller’s condenser.
Cooling towers are particularly effective in large industrial applications where a significant amount of heat needs to be dissipated. By using a cooling tower, wassergekühlte Kältemaschinen can achieve lower condensing temperatures, leading to improved energy efficiency and performance. However, they also require regular maintenance to prevent issues like scaling, corrosion, and biological growth, which can impact their effectiveness. Cooling Tower are crucial components, using a cooling tower can significantly enhance the performance of wassergekühlt systems.
How to Select the Best Industrial Chiller for Your Needs?
Choosing the best industrial chiller for your specific needs requires careful consideration of several factors. First, you need to determine the Kühlung capacity required, typically measured in tons or BTUs per hour. This will depend on the amount of heat your process generates and the desired temperature reduction. Next, you should evaluate the type of chiller that best suits your application, considering factors like water availability, space constraints, and energy efficiency.
It’s also essential to consider the operating environment and any specific requirements, such as the need for precise temperature control or resistance to corrosive substances. As a manufacturer, we offer a wide range of industrial Kältemaschinen designed to meet diverse needs, and our team can help you navigate these considerations to select the right industrial chiller for your application. Remember, investing in the right chiller can lead to significant long-term benefits, including improved product quality, reduced operating costs, and increased equipment lifespan. Selecting the right chiller is crucial for optimizing performance and achieving the desired results.
What are the Best Practices for Maintaining Industrial Chillers?
Maintaining industrial Kältemaschinen is crucial for ensuring their long-term performance and reliability. Regular maintenance can help prevent unexpected breakdowns, reduce energy consumption, and extend the lifespan of your equipment. As a manufacturer, we recommend following a comprehensive maintenance schedule that includes routine inspections, cleaning, and component checks.
One key aspect of chiller maintenance is ensuring proper water quality, particularly in wassergekühlt systems. This involves monitoring and controlling factors like pH, hardness, and dissolved solids to prevent scaling, corrosion, and biological growth. It’s also important to regularly inspect and clean components like the condenser und evaporator coils, as well as filters and strainers. Additionally, checking refrigerant levels and monitoring system pressures can help identify potential issues before they escalate.
Why is Energy Efficiency Important in Industrial Refrigeration?
Energy efficiency is a critical consideration in industrial refrigeration, impacting both operating costs and environmental sustainability. Efficient Kältemaschinen consume less energy to achieve the same level of Kühlung, resulting in lower utility bills and a reduced carbon footprint. As a manufacturer, we are committed to designing and producing energy-efficient Kältemaschinen that help our customers achieve their sustainability goals while minimizing operating expenses.
Several factors contribute to the energy efficiency of an industrial chiller, including the type of compressor used, the efficiency of the heat exchangers, and the sophistication of the control system. Modern Kältemaschinen often incorporate features like variable-speed drives, electronic expansion valves, and advanced control algorithms that optimize performance under varying loads. By investing in an energy-efficient chiller, businesses can achieve significant long-term savings and demonstrate their commitment to environmental responsibility.
Häufig gestellte Fragen
What is the difference between air-cooled and water-cooled chillers?
Air-cooled chillers use ambient air to cool the refrigerant, while wassergekühlte Kältemaschinen use water, often in conjunction with a cooling tower. Air-cooled units are typically easier to install and maintain, while wassergekühlt units are often more efficient, especially in large applications. There are two main types of industrial chillers: air-cooled and water-cooled.
How often should industrial chillers be serviced?
The frequency of service depends on factors like the type of chiller, operating conditions, and manufacturer recommendations. Generally, it’s advisable to have Industriekälteanlagen inspected and serviced at least once a year, with more frequent checks for critical components. Proper maintenance is essential for keeping your equipment cool and operating efficiently.
What is the typical lifespan of an industrial chiller?
With proper maintenance, Industriekälteanlagen can last for 15-20 years or even longer. However, the actual lifespan can vary depending on factors like usage patterns, operating environment, and the quality of the equipment. Regular maintenance and timely repairs can significantly extend the longevity of the equipment.
Can industrial chillers be used for both cooling and heating?
Some Industriekälteanlagen, known as heat pump Kältemaschinen, are capable of providing both Kühlung and heating. These systems can reverse the refrigeration cycle to transfer heat into the process fluid instead of removing it. Chillers also provide heating capabilities in some models.
What type of refrigerant is used in industrial chillers?
The type of refrigerant used in Industriekälteanlagen can vary depending on factors like the chiller’s design, Kühlung capacity, and environmental regulations. Common refrigerants include HFCs like R-134a and R-410A, as well as newer, more environmentally friendly options like HFOs.
How do I know what size chiller I need?
Determining the right size chiller involves calculating the heat load of your process and the desired temperature reduction. Factors to consider include the flow rate and specific heat of the process fluid, as well as the operating temperatures and environmental conditions. Consulting with a chiller manufacturer or a qualified HVAC professional can help ensure you select the appropriate size. Our Water Cooled Screw Water Chiller are designed to meet a wide range of industrial applications, ensuring you get the right industrial chiller for your needs.
Wichtigste Erkenntnisse
- Industrielle Kältemaschinen are essential for maintaining optimal operating temperatures in a wide range of industries, from plastics and machining to food processing and data centers.
- There are two main types of Industriekälteanlagen: luftgekühlt und wassergekühlt, each with its own advantages and ideal use cases.
- An 8 ton air-cooled chiller offers a balance of Kühlung capacity and efficiency, making it suitable for many medium-scale industrial applications.
- Key components of a chiller system include the compressor, condenser, expansion valveund evaporator, all working together to transfer heat away from the process.
- Choosing the best industrial chiller involves considering factors like Kühlung capacity, chiller type, operating environment, and energy efficiency.
- Regular maintenance, including inspections, cleaning, and component checks, is crucial for ensuring the long-term performance and reliability of Industriekälteanlagen.
- Energy efficiency is a critical consideration in industrial refrigeration, impacting both operating costs and environmental sustainability.
- As a manufacturer, we are committed to providing high-quality, energy-efficient Kältemaschinen tailored to the specific needs of our customers across various industries.
Remember, if you need help selecting or maintaining an industrial chiller, don’t hesitate to contact us. Our team of experts is ready to assist you in finding the perfect Kühlung solution for your needs. Anti-Explosion Chillers are just one example of our specialized product offerings designed to meet unique industrial challenges. We also offer Air Cooled Screw Central Chillers, providing efficient and reliable Kühlung for larger applications. For those in need of comprehensive Kühlung solutions, our HVAC Chillers are designed to deliver exceptional performance. We also understand the specific needs of industries such as agriculture, which is why we offer specialized Industrial Chillers For Agriculture to ensure optimal performance in these environments.
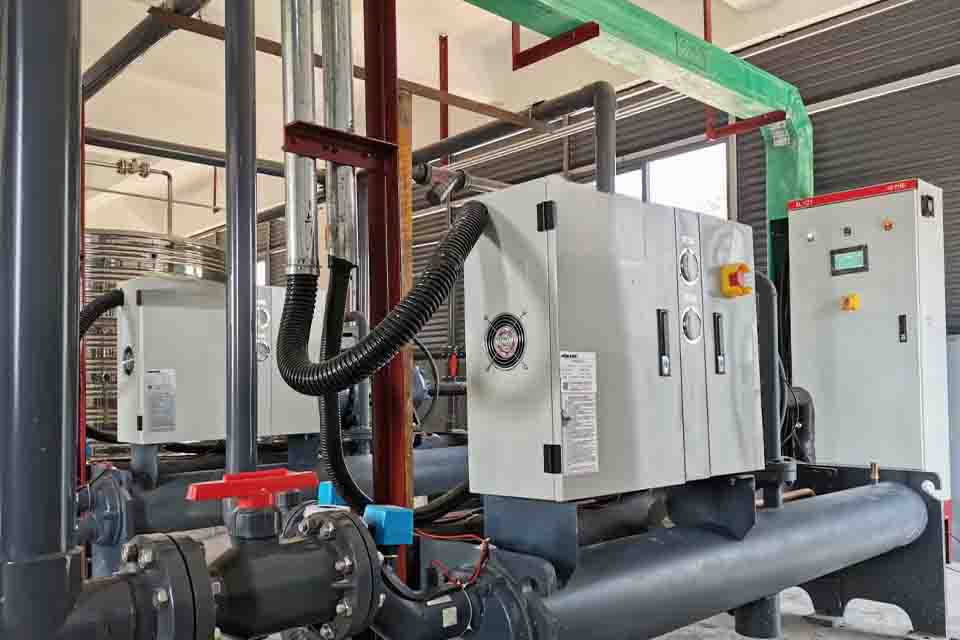