-
Dalingshan Industriel Guangdong
Refroidisseurs industriels pour plastique
Refroidisseurs en plastique haute performance pour l'industrie du plastique
Refroidisseurs en plastique, également connu sous le nom Les refroidisseurs pour plastique sont souvent refroidis à l'aide d'eau réfrigérée pour obtenir les propriétés souhaitées., sont essentiels pour maintenir un contrôle précis de la température dans divers procédés plastiquesCe guide explore le rôle essentiel de refroidisseurs dans le industrie du plastique, les différents types disponibles et comment choisir le système adapté à vos besoins spécifiques. Que vous soyez impliqué dans le moulage par injection ou l'extrusion de plastique, le contrôle de la température est essentiel. moulage, extrusion ou autre plastique applications, ces informations vous aideront à optimiser votre systèmes de refroidissement, améliorer la qualité du produit et améliorer l'efficacité globale. refroidisseur en plastique usines de fabrication, nous comprenons les exigences de refroidissement uniques de l'industrie des plastiques et proposons une gamme de solutions fiables et de haute qualité adaptées à vos besoins spécifiques.
Efficacité améliorée avec notre gamme de refroidisseurs industriels
Notre refroidisseurs en plastique offre précise contrôle de la température, l'efficacité énergétique et des performances fiables, essentielles pour optimiser votre procédés plastiquesNous fournissons des services personnalisés solutions de refroidissement pour répondre aux divers besoins de la industrie de transformation des matières plastiques. En collaborant avec nous, vous avez accès à des conseils d'experts, à des conceptions personnalisées, à des produits de haute qualité et à un service après-vente complet. Nous proposons une large gamme de refroidisseurs, notamment Refroidisseurs d'eau à spirale refroidis par eau, Refroidisseurs à vis refroidis par air, et Refroidisseurs d'eau à vis refroidis par eau, chacun conçu pour une efficacité et des performances maximales dans les applications industrielles exigeantes. Contactez-nous dès aujourd'hui pour discuter de vos besoins spécifiques et laissez-nous vous aider à choisir le modèle idéal refroidisseur pour votre opération.
<br>
Contrôle précis de la température pour des processus plastiques optimaux avec nos refroidisseurs de processus
Notre refroidisseurs de processus sont conçus pour fournir des résultats précis contrôle de la température, un facteur essentiel pour maintenir la qualité et la cohérence de votre produits en plastiqueNous proposons une gamme de capacité de refroidissement options pour répondre aux exigences spécifiques de vos processus. Le refroidisseur fournit un approvisionnement constant en eau réfrigérée pour un refroidissement efficace. refroidisseurs sont essentiels pour réguler la température dans des applications telles que moulage par injection, extrusion et soufflage moulageUn contrôle constant de la température conduit à une meilleure qualité du produit, à des temps de cycle plus rapides et à une réduction des déchets, améliorant ainsi votre efficacité globale. processus de fabrication du plastique. Précis contrôle de la température empêche le gauchissement, le rétrécissement et d'autres défauts pouvant survenir pendant le refroidissement, garantissant que vos produits répondent aux normes de qualité les plus élevées.
Circuits de réfrigération avancés pour un refroidissement fiable de vos processus plastiques
Notre refroidisseurs utiliser avancé réfrigération circuits conçus pour la fiabilité et l'efficacité. circuit de réfrigération comprend un compresseur, condenseur, et Les refroidisseurs centraux sont souvent utilisés dans les processus industriels pour maintenir des températures optimales., travaillant ensemble pour faire circuler réfrigérant et retirez la chaleur de votre procédés plastiques. Le le compresseur comprime le réfrigérant, augmentant sa température et sa pression. Le réfrigérant chaud et à haute pression s'écoule ensuite vers le condenseur, où il libère de la chaleur vers un fluide de refroidissement, tel que l'air ou l'eau. Le réfrigérant passe ensuite à travers un le détendeur du refroidisseur assure une régulation précise du débit de réfrigérant., en abaissant sa pression et sa température, avant d'entrer dans le évaporateurDans l'évaporateur, le réfrigérant froid absorbe chaleur du plastique, en le refroidissant efficacement. Ce système en boucle fermée assure un refroidissement constant et fiable, essentiel pour maintenir l'intégrité et la qualité de vos produits en plastique. Nous accordons la priorité à qualité et fiabilité de nos composants pour assurer des performances durables et minimiser les temps d'arrêt. Choisir un refroidisseur Il est essentiel de choisir le type de réfrigérant adapté à votre application spécifique pour optimiser ses performances. Nos refroidisseurs peuvent utiliser différents réfrigérants pour répondre au mieux à vos besoins.
Spécifications techniques
Spécification | Gamme/Options |
Capacité de refroidissement | 5 – 500 tonnes |
Réfrigérant | R-134a, R-410A, autres options écologiques |
Type de compresseur | Volute, vis, mouvement alternatif |
Type de condenseur | Refroidi par air, refroidi par eau |
Alimentation électrique | Personnalisable |
Contrôle de la température | Numérique, Programmable |
Les instructions d'utilisation de l'unité de commande sont essentielles pour un fonctionnement optimal. Consultez le manuel d’utilisation spécifique du refroidisseur pour obtenir des instructions détaillées sur le fonctionnement et l’entretien.
Impact environnemental : Nos refroidisseurs sont conçus dans un souci de respect de l'environnement. Nous proposons réfrigérant options à faible potentiel de réchauffement global (PRG) et optimiser les conceptions pour l'efficacité énergétique.
Avis des clients :
« Depuis l'installation de votre refroidisseur à eau« Nos temps de cycle de moulage par injection ont considérablement diminué et la qualité des produits s'est grandement améliorée. L'efficacité du refroidisseur a également réduit nos coûts énergétiques. » – Directeur d'usine, usine de fabrication de plastiques.
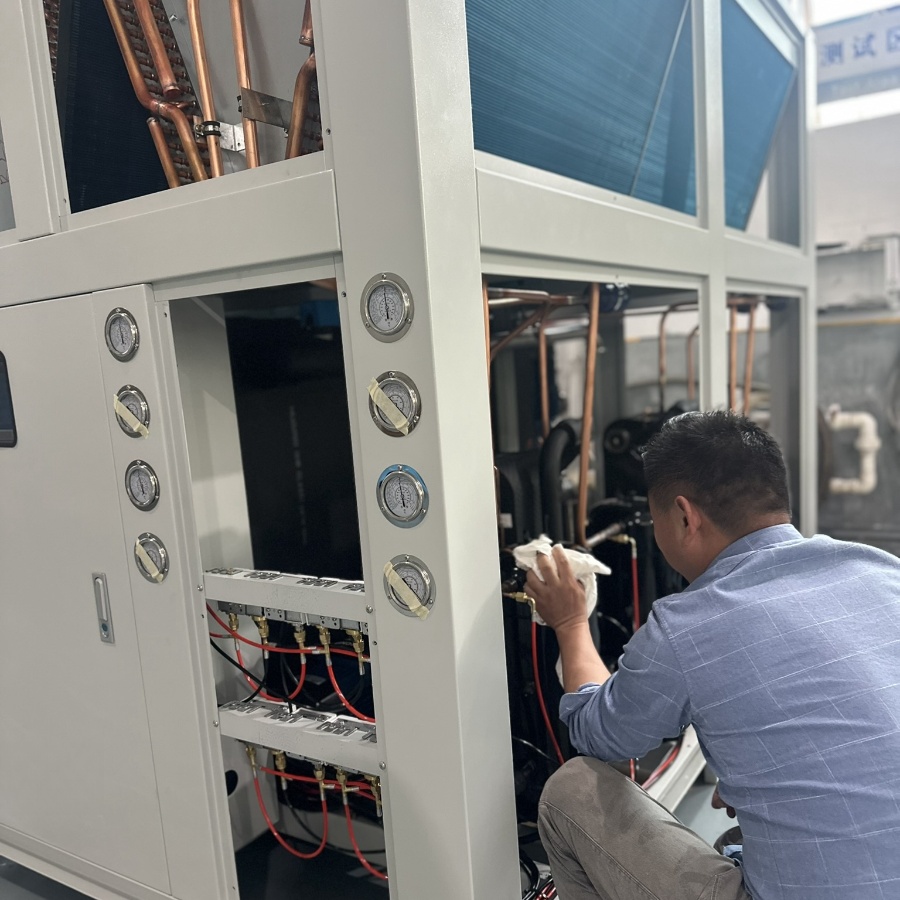
Résumé des avantages :
Boostez votre plastique Production avec nos refroidisseurs efficaces ! Un contrôle précis de la température garantit des produits de qualité supérieure tout en économisant de l'énergie. Contactez-nous pour une solution de refroidissement personnalisée
Refroidisseurs pour la transformation des matières plastiques : une plongée en profondeur dans le refroidissement des processus
Ce guide explore le rôle essentiel de refroidisseurs pour la transformation des matières plastiques, offrant un aperçu de leur fonctionnement, des différents types et des facteurs clés à prendre en compte lors du choix du bon système. Que vous soyez impliqué dans l'injection moulage, extrusion, ou autre procédés plastiques, la compréhension du refroidissement est essentielle pour produire des produits de haute qualité produits en plastique. Nous allons plonger dans les subtilités de refroidissement de processus, explorant les différents types de refroidisseurs systèmes, fonctionnalités clés et conseils de maintenance pour garantir votre systèmes de refroidissement fonctionnent bien.
Qu’est-ce qu’un refroidisseur et pourquoi le refroidissement est-il essentiel dans l’industrie du plastique ?
UN refroidisseur est un réfrigération machine qui élimine la chaleur d'un eau de procédé boucle et la transfère à un autre milieu, comme l'air ou eau industrielle. Le refroidissement est essentiel dans le industrie du plastique car cela a un impact direct sur la qualité du produit, les temps de cycle et les applications de refroidissement globales. efficacité opérationnelle. Dans des processus comme moulage par injection et extrusion, précis contrôle de la température est essentiel pour obtenir les propriétés matérielles souhaitées et prévenir les défauts.
Sans refroidissement suffisant, le plastique Le refroidissement peut ne pas se faire correctement, ce qui peut entraîner des déformations des pièces, des incohérences dimensionnelles et une diminution de la résistance mécanique. Un refroidissement rapide et contrôlé à l'eau réfrigérée, en revanche, permet d'obtenir des produits de meilleure qualité, des temps de cycle plus rapides et une productivité améliorée.
Différents types de refroidisseurs pour plastiques : choisir le bon
Divers types de refroidisseurs sont disponibles, chacun avec ses propres avantages et inconvénients. Comprendre ces différences est essentiel pour choisir le bon refroidisseur pour la transformation des matières plastiques.
- Refroidisseurs à air : Ceux-ci utilisent ambiant air à cool le réfrigérantIls sont généralement plus faciles à installer mais sont moins efficaces dans les climats plus chauds. Refroidisseurs d'eau à spirale refroidis par air sont parfaits pour les espaces restreints. Pour une efficacité optimale dans des climats variés, recherchez refroidisseurs à air conçus pour fonctionner correctement dans des conditions de température ambiante élevées et basses. refroidisseurs adapter leur fonctionnement pour maintenir des performances de refroidissement constantes quelle que soit la température de l’air ambiant.
- Refroidisseurs à eau : Ceux-ci utilisent un eau boucle vers cool le réfrigérant, offrant une plus grande efficacité énergétique, en particulier dans les environnements plus chauds. Ils nécessitent une tour de refroidissement ou une autre source d'eau. Refroidisseurs à eau sont plus efficaces grâce aux capacités supérieures de transfert de chaleur de l’eau.
- Refroidisseurs portables : Refroidisseurs portables offrent une flexibilité, vous permettant de les déplacer rapidement et de les connecter à différents équipements selon vos besoins. Ils conviennent aux petites opérations ou aux opérations temporaires refroidissement besoins. Considérez-les comme un compagnon de refroidissement pratique que vous pouvez facilement déplacer et déployer.
Pour des besoins industriels spécifiques, tels que les environnements dangereux, explorez les solutions spécialisées Refroidisseurs anti-explosionLe meilleur choix dépend de votre application spécifique, de votre budget et des conditions environnementales.
Comment fonctionne un refroidisseur ? Comprendre le circuit de réfrigération
Comprendre comment un travail de réfrigérations implique une compréhension de base de la circuit de réfrigération. UN refroidisseur utilise un fluide spécial appelé réfrigérant qui absorbe et libère la chaleur dans un cycle continu. circuit de réfrigération est le cœur de la refroidisseur, remplissant la fonction critique de refroidissement processus eau, qui est ensuite utilisé pour réguler la température de plastique équipements et matériaux de traitement. Voici une explication simplifiée :
- Compression: Le le compresseur comprime le réfrigérant, augmentant sa température et sa pression.
- Condensation: Le chaud, la haute pression réfrigérant s'écoule vers le condenseur, où il libère de la chaleur soit dans l'air (refroidi par air) ou eau (refroidie par eau)) et passe de l'état gazeux à l'état liquide.
- Expansion: Le réfrigérant liquide passe à travers un soupape d'expansion, abaissant sa pression et sa température.
- Évaporation: Le froid, basse pression réfrigérant s'écoule vers le évaporateur, où il absorbe chaleur du plastique processus eau. Le réfrigérant retourne à l'état gazeux, prêt à être à nouveau comprimé, répétant le cycle. La chaleur absorbée lors de l'évaporation est le mécanisme par lequel votre plastique les produits ou équipements sont refroidis.
Optimisation du moulage par injection avec des refroidisseurs : obtenir un contrôle précis de la température
Refroidisseurs sont essentiels dans le moulage par injection pour maintenir une cohérence température et pression dans le moule, ce qui permet d'obtenir des pièces de haute qualité produites avec de l'eau froide. Ils aident à gérer la chauffage et refroidissement cycles inhérents à la moulage par injection processus.
Contrôle précis de la température dans le moule est essentiel pour contrôler la vitesse de refroidissement du plastique fondu dans les applications de refroidissement. plastiqueCe refroidissement contrôlé permet aux fabricants d'obtenir les propriétés matérielles souhaitées et d'optimiser les temps de cycle. Sans un refroidissement approprié refroidissement, le plastique peut refroidir de manière inégale, ce qui entraîne des déformations, des rétrécissements ou d'autres défauts. refroidissement raccourcit également le cycle de refroidissement, permettant des taux de production plus rapides.
Amélioration des processus d'extrusion grâce aux refroidisseurs
Dans extrusion, refroidisseurs jouent un rôle essentiel dans le maintien de la température optimale du corps et de la matrice de l'extrudeuse. Ils assurent une refroidissement, contribuant à produire des uniformes produits en plastique.
Extrusion est un processus continu où plastique est fondu et forcé à travers une matrice pour créer des formes spécifiques. Une température constante est essentielle pour maintenir une viscosité et un débit uniformes du métal fondu. plastiqueSans refroidissement adéquat, les variations de température peuvent entraîner des incohérences dans le produit extrudé, affectant ainsi les dimensions et la résistance. Refroidisseurs assurer le bon déroulement du processus d'extrusion, produisant des produits uniformes et de haute qualité plastique produits.
Choisir le bon refroidisseur en plastique : facteurs à prendre en compte
Choisir le refroidisseur en plastique droit nécessite un examen attentif de plusieurs facteurs. Cela implique de prendre en compte le type de plastique étant utilisé, le spécifique processus plastique, requis contrôle de la température niveaux et l'ensemble capacité de refroidissement nécessaire. Voici quelques facteurs clés à prendre en compte :
- Capacité de refroidissement : Déterminez la capacité de refroidissement requise en tonnes ou en BTU en fonction de vos besoins spécifiques. besoins de refroidissementDes calculs inexacts pourraient conduire à un refroidissement inefficace ou à une puissance de refroidissement inadéquate pour vos besoins.
- Type de refroidisseur : Choisissez entre des refroidisseurs à air et à eau en fonction de vos ressources disponibles, des conditions environnementales et des considérations de coût à long terme. Les refroidisseurs à eau offrent souvent une meilleure efficacité mais nécessitent une installation et une maintenance plus complexes.
- Précision du contrôle de la température : Différents processus exigent différents niveaux de précision. Choisissez un refroidisseur qui offre la stabilité de température précise nécessaire à votre application.
- Efficacité énergétique : Recherchez des refroidisseurs avec des cotes d’efficacité énergétique élevées pour réduire les coûts d’exploitation.
- Exigences d'entretien : Tenez compte des besoins de maintenance du refroidisseur et choisissez-en un qui minimise les temps d’arrêt.
Refroidisseurs portables en plastique : des solutions de refroidissement flexibles pour les petites opérations
Glacières portables en plastique offrir un moyen flexible et efficace de cool divers procédés plastiquesCes unités compactes et mobiles sont parfaites pour les petites opérations, fournissant un refroidissement supplémentaire ou refroidissant des machines individuelles.
Ces polyvalents refroidisseurs sont idéales lorsque vous avez besoin de cool différents équipements ou lorsque vos besoins de refroidissement varient. Ils sont souvent utilisés en conjonction avec des machines de moulage plus petites, offrant une solution rentable lorsqu'un grand refroidisseur centralisé peut ne pas être nécessaire. Leur portabilité permet un déplacement facile, ce qui les rend adaptables aux besoins de production changeants.
Refroidisseurs de process plastique : garantir la qualité et la fiabilité de la production plastique
Refroidisseurs pour le traitement des matières plastiques sont indispensables pour maintenir des températures constantes dans divers processus de fabrication de plastique. Ces systèmes de refroidissement dédiés sont conçus spécifiquement pour les exigences de production de plastique, garantissant à la fois la qualité du produit et l'efficacité opérationnelle du refroidisseur. Ils maintiennent un contrôle précis de la température, ce qui conduit à une meilleure consistance du produit et à une minimisation des défauts.
En investissant dans des solutions robustes et fiables refroidisseurs de processus de plastiqueLes fabricants peuvent améliorer la qualité de leurs produits, raccourcir les temps de cycle et optimiser leur processus de fabrication global. Un refroidissement constant réduit le risque de défauts causés par les fluctuations de température, garantissant ainsi la production de produits de haute qualité. produits en plastique.
Comprendre vos besoins en équipements de traitement du plastique et en refroidissement
Différent procédés plastiques et les équipements ont des besoins de refroidissement uniques. moulage, extrusion, et moulage par soufflage, par exemple, chacun nécessite des approches différentes en matière de refroidissement. Il est essentiel de comprendre ces différences lors du choix d'un refroidisseur.
Moulage par injection nécessite une rapidité et une précision refroidissement de la moule pour maintenir les temps de cycle et éviter les déformations. Extrusion nécessite un contrôle constant de la température pour gérer le flux et la consistance de la fonte plastiqueLe moulage par soufflage nécessite un refroidissement pour conserver la forme de la pièce moulée. Pour évaluer vos besoins en refroidissement, tenez compte de facteurs tels que le type de plastique, le temps de cycle souhaité et les conditions environnementales.
Entretenir votre système d'eau pour une performance optimale du refroidisseur
Maintenir un environnement propre et efficace système d'eau est crucial pour une performance optimale du refroidisseur. Un refroidisseur bien entretenu système d'eau améliore l'efficacité du transfert de chaleur, réduit la consommation d'énergie et prolonge la durée de vie du refroidisseur. Si vous utilisez un refroidisseur à eau, un système d'eau correctement entretenu est essentiel pour l'efficacité globale. La mise en œuvre d'un programme de traitement de l'eau robuste peut réduire considérablement le risque de problèmes qui pourraient nuire à la capacité du refroidisseur à fonctionner correctement.
Le contrôle et le nettoyage réguliers de la tour de refroidissement, le cas échéant, permettent d'éviter l'accumulation de tartre, d'algues et d'autres contaminants qui peuvent réduire l'efficacité du refroidissement et endommager les composants du refroidisseur. Surveillance et entretien qualité de l'eau est essentiel pour une sécurité à long terme et fiable refroidissementCela comprend le nettoyage et l’inspection périodiques de la tour de refroidissement et la garantie que l’eau est traitée de manière appropriée pour éviter la corrosion et l’entartrage.
Principaux points à retenir : considérations essentielles pour les refroidisseurs en plastique
- Refroidisseurs sont indispensables pour maintenir des contrôle de la température dans procédés plastiques.
- Choisir le bon type de refroidisseur (refroidi par air, refroidi par eau, ou portable) est crucial.
- Il est essentiel de comprendre vos besoins en matière de capacité de refroidissement pour sélectionner la taille de refroidisseur appropriée.
- Un entretien régulier optimise refroidisseur performances et prolonge sa durée de vie.
- Différent procédés plastiques nécessitent des solutions de refroidissement spécialisées.