-
Dalingshan Industriel Guangdong
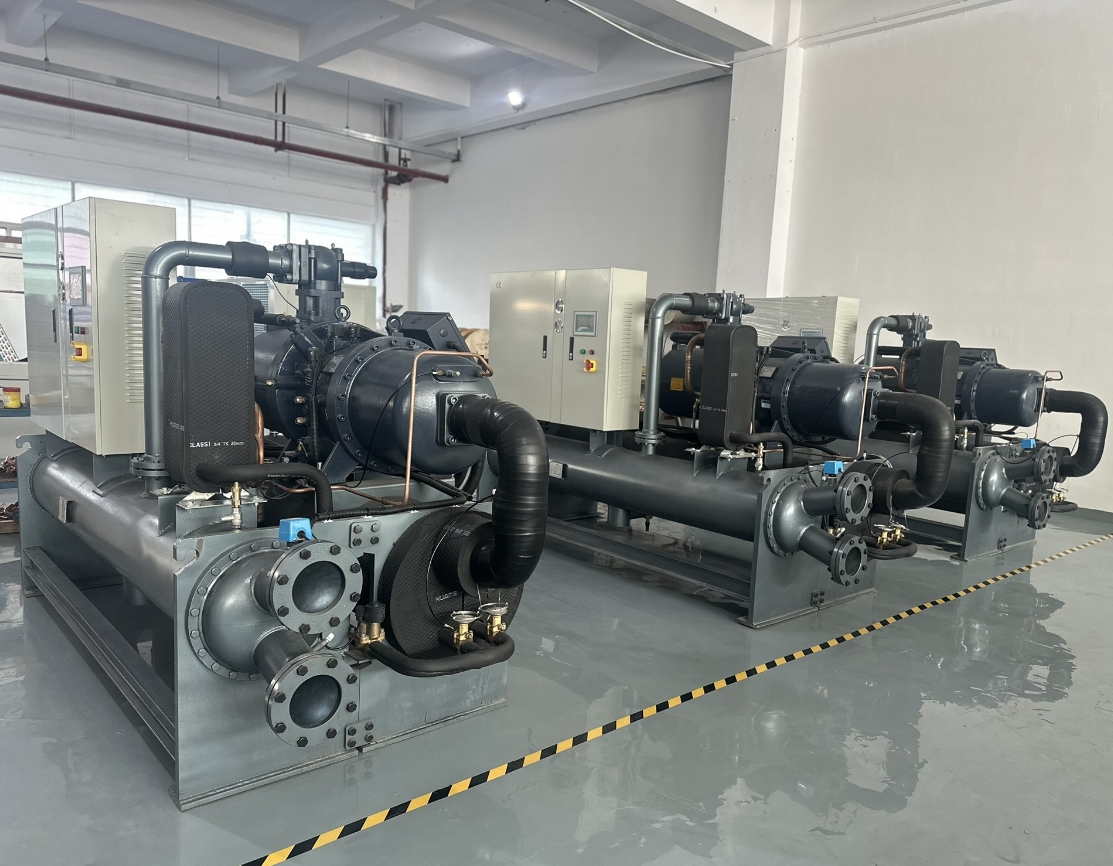
systèmes de refroidissement de moulage sous pression dans le processus de moulage sous pression
Refroidissement de précision : la pierre angulaire des processus de moulage sous pression efficaces
Le moulage sous pression est un procédé de fabrication largement utilisé, connu pour sa capacité à produire des pièces métalliques complexes de haute qualité avec une excellente précision dimensionnelle et une finition de surface. Cependant, l'obtention de résultats optimaux dans le moulage sous pression dépend en grande partie d'un contrôle précis de la température pendant la phase de refroidissement. Cet article se penche sur le rôle essentiel des systèmes de refroidissement dans le moulage sous pression, en explorant leur impact sur l'efficacité de la production, la qualité du produit et la rentabilité globale. C'est une lecture incontournable pour toute personne impliquée dans l'industrie du moulage sous pression, car il fournit des informations précieuses sur l'optimisation du processus de refroidissement pour des performances améliorées et des résultats supérieurs. Dans cet article, en tant que fabricant de refroidisseurs d'eau industriels, je partagerai mes expériences et mon expertise pour révéler les secrets des opérations de moulage sous pression réussies.
Table des matières
1. Qu’est-ce que le moulage sous pression et pourquoi le refroidissement est-il si important ?
Le moulage sous pression est un procédé de fabrication dans lequel du métal en fusion est injecté sous haute pression dans un moule en acier, également appelé matrice. Une fois que le métal en fusion remplit la cavité du moule, il peut refroidir et se solidifier, formant ainsi la forme souhaitée. Ce procédé est largement utilisé dans de nombreuses industries pour produire des pièces métalliques complexes et de haute qualité.
Le refroidissement est une étape cruciale du processus de moulage sous pression, car il a un impact direct sur la qualité, la précision dimensionnelle et la durée du cycle de production des pièces moulées. Un contrôle approprié de la vitesse de refroidissement garantit que le métal en fusion se solidifie uniformément, évitant ainsi les défauts tels que la porosité, le retrait et les fermetures à froid. Le contrôle de la température est donc un aspect fondamental du moulage sous pression. En tant que personne profondément impliquée dans la production de refroidisseurs d'eau industriels, j'ai pu constater de mes propres yeux à quel point des solutions de refroidissement efficaces peuvent transformer le processus de moulage sous pression. Un refroidissement efficace améliore non seulement la qualité du produit, mais améliore également considérablement la productivité en réduisant les temps de cycle.
<img src="”https://thewaterchiller.com/wp-content/uploads/2024/12/industrial-chiller-water-cooled-water-chiller-with-scroll-compressor-5hp.jpg”" alt=""Eau" cooled scroll water chiller” />
2. Comment fonctionne un système de refroidissement dans le moulage sous pression ?
Dans le moulage sous pression, un système de refroidissement comprend généralement un réseau de canaux ou de circuits à l'intérieur du moule à travers lesquels circule un liquide de refroidissement, tel que de l'eau ou de l'huile. Ces circuits de refroidissement sont placés de manière stratégique pour évacuer la chaleur du moule et du métal en fusion aussi rapidement et uniformément que possible. L'efficacité du système de refroidissement dépend de facteurs tels que la conception des circuits de refroidissement, le débit du liquide de refroidissement et la conductivité thermique du matériau du moule.
Il existe différentes méthodes de refroidissement utilisées dans la coulée sous pression, notamment le refroidissement par eau, le refroidissement par huile et le refroidissement par air. Chaque méthode a ses avantages et est choisie en fonction des exigences spécifiques de l'application. Le refroidissement par eau est la méthode la plus courante en raison de sa grande capacité de transfert de chaleur. D'après mon expérience, un refroidissement par eau bien conçu est la méthode la plus courante. Refroidisseur d'eau à spirale refroidi par eau peut améliorer considérablement l'efficacité du processus de moulage sous pression. Nos clients de l'industrie du plastique et du caoutchouc, de l'industrie de l'usinage et de l'industrie agroalimentaire ont signalé des améliorations remarquables de leur rendement de production après la mise en œuvre de nos solutions de refroidissement sur mesure.
3. Quels facteurs affectent la vitesse de refroidissement dans le moulage sous pression ?
Plusieurs facteurs influencent la vitesse de refroidissement dans le moulage sous pression, ce qui a un impact sur l'efficacité globale du processus de production. Parmi ceux-ci, on trouve notamment :
- Conception du moule : La conception et la disposition des canaux de refroidissement dans le moule jouent un rôle crucial. Un placement approprié des canaux assure une dissipation uniforme de la chaleur.
- Débit du liquide de refroidissement : Des débits plus élevés conduisent généralement à un refroidissement plus rapide, mais cela doit être équilibré pour éviter des chutes de pression excessives.
- Matériau du moule : Les matériaux à conductivité thermique plus élevée, comme l’acier, facilitent un transfert de chaleur plus rapide.
- Température du liquide de refroidissement : Des températures de liquide de refroidissement plus basses peuvent accélérer le refroidissement mais peuvent augmenter le risque de choc thermique pour le moule.
- Matériau de moulage : Différents métaux ont des caractéristiques de refroidissement différentes ; par exemple, l’aluminium refroidit plus rapidement que l’acier.
- Géométrie de la pièce : Les sections plus épaisses d'une pièce moulée refroidissent plus lentement que les sections plus minces, ce qui nécessite une réflexion approfondie lors de la conception du moule.
Il est essentiel de comprendre ces facteurs pour optimiser le processus de refroidissement. Sur la base de nos recherches approfondies et des commentaires de nos clients, nous avons constaté que l'adaptation du système de refroidissement à l'alliage et à la conception de la pièce peut considérablement améliorer les temps de cycle et réduire les défauts.
4. Quels sont les défis courants en matière de refroidissement du moulage sous pression ?
Plusieurs défis peuvent survenir lors du refroidissement du moulage sous pression, entraînant souvent des inefficacités de production et des pièces défectueuses :
- Refroidissement inégal : Une température incohérente dans tout le moule peut entraîner une solidification inégale, entraînant des défauts tels que des déformations et des contraintes résiduelles.
- Fatigue thermique : Les cycles de chauffage et de refroidissement répétés peuvent provoquer une fatigue thermique dans le moule, réduisant ainsi sa durée de vie.
- Points chauds : Des zones localisées de températures excessives, appelées points chauds, peuvent provoquer des défauts et endommager le moule.
- Refroidissement inadéquat : Une capacité de refroidissement insuffisante peut prolonger les temps de cycle et limiter la production.
- Tartre et corrosion : Les impuretés présentes dans l’eau de refroidissement peuvent provoquer une accumulation de tartre et une corrosion dans les canaux de refroidissement, réduisant ainsi l’efficacité.
Pour relever ces défis, il faut adopter une approche globale qui tienne compte à la fois de la conception du système de refroidissement et de la qualité du liquide de refroidissement. Notre expérience dans l'industrie chimique et pharmaceutique et dans l'industrie électronique a montré qu'un entretien régulier et l'utilisation de liquides de refroidissement de haute qualité sont essentiels pour prévenir bon nombre de ces problèmes.
5. Quelles solutions de refroidissement avancées sont disponibles pour le moulage sous pression ?
Pour surmonter les défis associés aux méthodes de refroidissement traditionnelles, plusieurs solutions de refroidissement avancées ont été développées :
- Refroidissement conforme : Cette technique consiste à créer des canaux de refroidissement qui épousent la forme de la pièce, offrant ainsi un refroidissement plus uniforme.
- Inserts à haute conductivité : L’utilisation de matériaux à haute conductivité thermique dans les zones critiques du moule peut accélérer le transfert de chaleur.
- Refroidissement par impulsions : Cela implique d'activer et de désactiver le flux de liquide de refroidissement pour améliorer l'efficacité du refroidissement et réduire les chocs thermiques.
- Canaux de micro-refroidissement : Les canaux plus petits offrent une plus grande surface de transfert de chaleur, améliorant ainsi les performances de refroidissement.
- Liquides de refroidissement spécialisés : Les liquides de refroidissement formulés avec des propriétés thermiques améliorées et des inhibiteurs de corrosion peuvent améliorer l'efficacité du refroidissement et protéger le moule.
En tant que fabricant de refroidisseurs industriels, nous sommes à l'avant-garde du développement et de la mise en œuvre de ces solutions de refroidissement avancées. Par exemple, notre Refroidisseurs au glycol se sont avérés très efficaces dans l’industrie médicale, les laboratoires et les instituts de recherche, où un contrôle précis de la température est primordial.
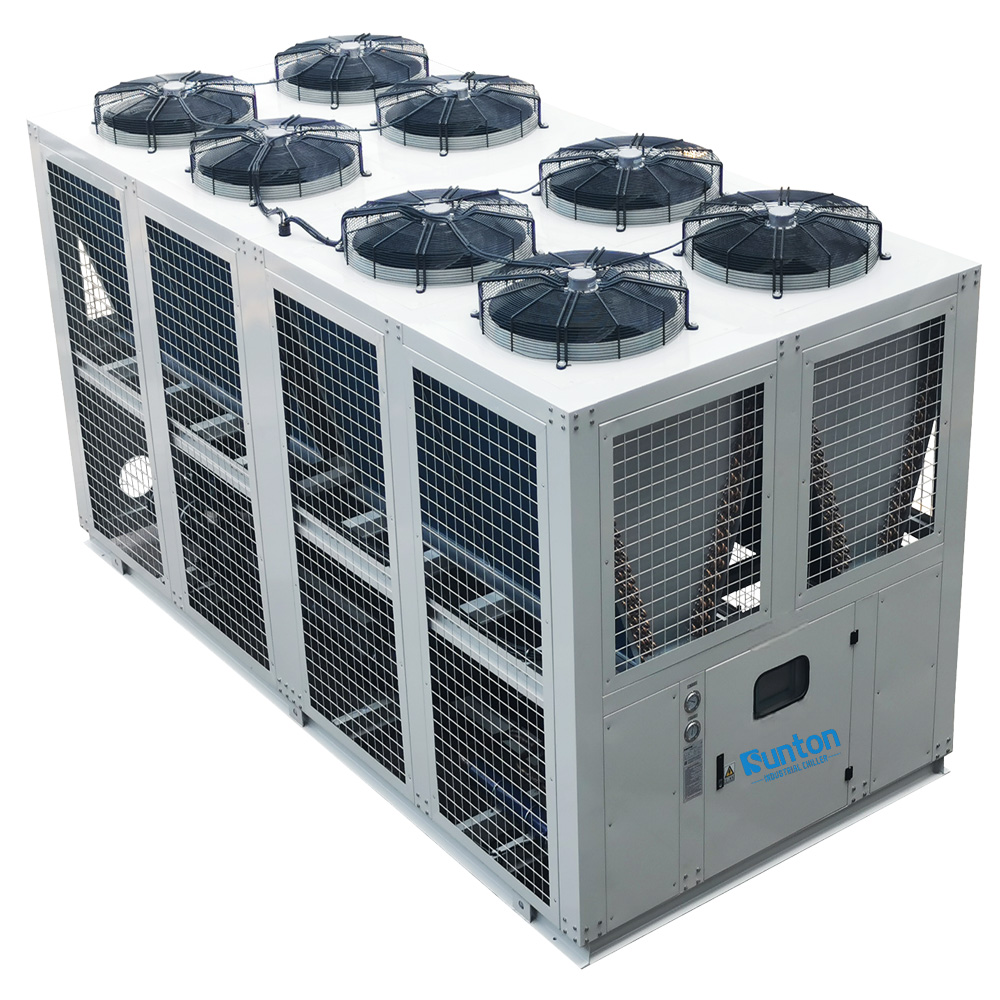
6. Comment optimiser le processus de refroidissement pour une efficacité maximale ?
L'optimisation du processus de refroidissement dans le moulage sous pression nécessite une approche à multiples facettes qui prend en compte divers facteurs :
- Conception du moule : L’utilisation de techniques avancées telles que le refroidissement conforme et le placement stratégique des canaux de refroidissement peuvent améliorer considérablement l’uniformité du refroidissement.
- Sélection du liquide de refroidissement : Choisir le bon liquide de refroidissement, qu'il s'agisse d'eau, d'huile ou d'un fluide spécialisé, et garantir sa qualité peut améliorer le transfert de chaleur et prévenir des problèmes tels que le tartre et la corrosion.
- Contrôle du débit et de la pression : L'optimisation du débit et de la pression du liquide de refroidissement assure une évacuation efficace de la chaleur sans provoquer de contraintes excessives sur le moule.
- Surveillance et contrôle de la température : La mise en œuvre de capteurs et de systèmes de contrôle pour surveiller et ajuster la température du liquide de refroidissement en temps réel peut maintenir un refroidissement constant.
- Entretien régulier : La réalisation d’inspections et d’entretiens de routine du système de refroidissement, y compris le nettoyage des canaux et la vérification des fuites, peut éviter les temps d’arrêt inattendus.
7. Quel est l’impact du refroidissement sur la durée de vie du moule ?
Le refroidissement joue un rôle crucial dans la détermination de la durée de vie d'un moule de moulage sous pression. Un refroidissement approprié peut prolonger la durée de vie d'un moule en réduisant la fatigue thermique et en évitant les dommages causés par des températures excessives. Lorsqu'un moule est soumis à des changements de température rapides et irréguliers, il peut développer des fissures et d'autres formes de dommages qui réduisent sa durée de vie utile.
En assurant un refroidissement uniforme et contrôlé, les contraintes thermiques sur le moule sont minimisées, ce qui prolonge sa durée de vie. Cela réduit non seulement la fréquence des remplacements coûteux du moule, mais garantit également une qualité constante des pièces au fil du temps. Par exemple, la mise en œuvre d'un Refroidisseur à vis refroidi par air peut aider à maintenir une température constante dans tout le moule, minimisant ainsi le stress thermique et prolongeant la durée de vie du moule. Nous avons constaté des améliorations significatives de la durée de vie des moules chez nos clients des centres de données et de l'industrie de l'impression qui ont adopté nos solutions de refroidissement avancées.
8. Quel rôle joue l’automatisation dans le refroidissement des pièces moulées sous pression ?
L'automatisation est devenue de plus en plus importante dans le domaine du moulage sous pression, notamment pour contrôler le processus de refroidissement. Les systèmes de refroidissement automatisés peuvent surveiller et ajuster les paramètres du processus en temps réel, garantissant ainsi un refroidissement constant et efficace. Ces systèmes peuvent également s'intégrer à d'autres aspects du processus de moulage sous pression, tels que l'injection et l'éjection, pour créer une ligne de production entièrement automatisée.
L'automatisation améliore non seulement la répétabilité et la précision du processus de refroidissement, mais réduit également le besoin de contrôle et d'intervention manuels. Cela conduit à une productivité accrue, à des coûts de main-d'œuvre réduits et à un environnement de travail plus sûr. Par exemple, notre Refroidisseurs anti-explosion sont conçus avec des fonctionnalités d'automatisation avancées, ce qui les rend idéaux pour une utilisation dans des environnements dangereux.
9. Comment puis-je réduire les temps de cycle grâce à un refroidissement efficace ?
La réduction des temps de cycle est un objectif clé dans le moulage sous pression, car elle a un impact direct sur le rendement et la rentabilité de la production. Un refroidissement efficace joue un rôle essentiel pour obtenir des temps de cycle plus courts en solidifiant rapidement le métal en fusion et en permettant une éjection plus rapide des pièces. Pour réduire les temps de cycle grâce à un refroidissement efficace, envisagez les stratégies suivantes :
- Optimiser la conception des canaux de refroidissement : La mise en œuvre d’un refroidissement conforme ou d’autres conceptions de canaux avancées peut améliorer le transfert de chaleur et réduire le temps de refroidissement.
- Augmenter le débit du liquide de refroidissement : Des débits plus élevés peuvent accélérer le refroidissement, mais cela doit être équilibré avec la nécessité d'éviter des chutes de pression excessives.
- Utiliser des températures de liquide de refroidissement plus basses : L'abaissement de la température du liquide de refroidissement peut accélérer le refroidissement, mais il faut veiller à éviter les chocs thermiques.
- Utiliser des technologies de refroidissement avancées : L’utilisation de technologies telles que le refroidissement par impulsions ou les micro-canaux de refroidissement peut améliorer l’efficacité du refroidissement.
- Intégrer le refroidissement à l’automatisation des processus : L’automatisation du processus de refroidissement et son intégration à d’autres aspects de la ligne de production peuvent rationaliser les opérations et réduire les temps de cycle globaux.
En mettant en œuvre ces stratégies, les fabricants peuvent réduire considérablement les temps de cycle et augmenter le rendement de production. Nos clients de l'industrie laser et de l'industrie agroalimentaire ont signalé des réductions substantielles des temps de cycle après la mise en œuvre de nos solutions de refroidissement optimisées, telles que Tour de refroidissement.
10. Comment le refroidissement affecte-t-il la qualité des pièces moulées sous pression ?
Le processus de refroidissement a un impact profond sur la qualité des pièces moulées sous pression. Un refroidissement adéquat assure une solidification uniforme du métal en fusion, ce qui est essentiel pour obtenir les propriétés mécaniques et la précision dimensionnelle souhaitées. Un refroidissement inadéquat ou irrégulier peut entraîner divers défauts, notamment :
- Porosité: L'air ou le gaz emprisonné dans la pièce moulée peut créer des vides ou des pores, fragilisant ainsi la pièce.
- Rétrécissement: À mesure que le métal refroidit et se contracte, il peut rétrécir de manière inégale, provoquant des inexactitudes dimensionnelles et des contraintes internes.
- Fermetures à froid : Si le métal en fusion refroidit trop rapidement, il risque de ne pas fusionner complètement, ce qui entraînera des lignes ou des fissures visibles à la surface.
- Déformation : Un refroidissement inégal peut entraîner une déformation de la pièce lors de sa solidification.
- Contraintes résiduelles : Les contraintes internes dues à un refroidissement inégal peuvent affaiblir la pièce et la rendre plus susceptible de tomber en panne sous charge.
En contrôlant soigneusement le processus de refroidissement, les fabricants peuvent minimiser ces défauts et produire des pièces de haute qualité avec des propriétés cohérentes.
Attention (Modèle de vente AIDA)
Le moulage sous pression est un procédé de fabrication de précision dans lequel l'obtention de résultats optimaux dépend en grande partie du contrôle précis de la température pendant la phase de refroidissement. Un refroidissement inadéquat ou irrégulier entraîne souvent des inefficacités de production et des pièces défectueuses telles que la porosité, le rétrécissement et les fermetures à froid, ce qui affecte la qualité, la précision dimensionnelle et le temps de cycle de production des pièces moulées.
Intérêt (Modèle de vente AIDA)
Nos solutions de refroidissement avancées, notamment le refroidissement conforme, les inserts à haute conductivité et le refroidissement par impulsions, sont conçues pour relever ces défis. En mettant en œuvre ces technologies, les fabricants peuvent considérablement améliorer leur rendement de production et la qualité de leurs produits. Par exemple, nos refroidisseurs au glycol se sont avérés très efficaces dans les industries nécessitant un contrôle précis de la température, telles que l'industrie médicale et les laboratoires.
Fonctionnalité | Avantage |
Refroidissement conforme | Refroidissement uniforme, défauts réduits |
Inserts à haute conductivité | Transfert de chaleur accéléré, efficacité améliorée |
Refroidissement par impulsions | Efficacité de refroidissement améliorée, choc thermique réduit |
Liquides de refroidissement spécialisés | Propriétés thermiques améliorées, protection contre la corrosion |
Automation | Surveillance et contrôle en temps réel, refroidissement constant |
Désir (Modèle de vente AIDA)
Imaginez un processus de moulage sous pression dans lequel les temps de cycle sont considérablement réduits, les défauts sont minimisés et la qualité du produit est constamment élevée. Grâce à nos solutions de refroidissement sur mesure, cette vision peut devenir réalité. Nos clients de divers secteurs, notamment l'industrie du laser et l'industrie agroalimentaire, ont signalé des améliorations substantielles de leurs processus de production après la mise en œuvre de nos systèmes. En collaborant avec nous, vous pouvez obtenir :
- Temps de cycle réduits : Un refroidissement plus rapide signifie une éjection plus rapide des pièces et un débit de production accru.
- Amélioration de la qualité du produit : Un refroidissement uniforme garantit des pièces possédant les propriétés mécaniques et la précision dimensionnelle souhaitées.
- Durée de vie prolongée du moule : Un refroidissement adéquat minimise le stress thermique, prolongeant ainsi la durée de vie de vos moules.
- Efficacité améliorée : L’automatisation rationalise les opérations, réduit les coûts de main-d’œuvre et améliore la sécurité.
Action (Modèle de vente AIDA)
Prêt à transformer votre processus de moulage sous pression ? Contactez-nous aujourd'hui pour en savoir plus sur nos solutions de refroidissement avancées et sur la manière dont elles peuvent bénéficier à votre entreprise. Laissez-nous vous aider à atteindre une efficacité, une qualité et une rentabilité inégalées dans vos opérations de moulage sous pression. N'attendez pas, faites le premier pas vers l'optimisation de votre processus de production dès maintenant !
FAQ
1. Quelle est la plage de température typique pour l’eau de refroidissement utilisée dans le moulage sous pression ?
La plage de température typique de l'eau de refroidissement utilisée dans la coulée sous pression est comprise entre 20 °C et 40 °C (68 °F et 104 °F). Cependant, la température optimale peut varier en fonction de facteurs tels que l'alliage spécifique coulé, la géométrie de la pièce et la vitesse de refroidissement souhaitée.
2. À quelle fréquence les canaux de refroidissement d'un moule de moulage sous pression doivent-ils être nettoyés ?
Les canaux de refroidissement doivent être nettoyés régulièrement pour éviter l'accumulation de tartre, de rouille et d'autres contaminants qui peuvent réduire l'efficacité du refroidissement. La fréquence de nettoyage dépend de facteurs tels que la qualité de l'eau et le type de liquide de refroidissement utilisé, mais il est généralement recommandé d'inspecter et de nettoyer les canaux tous les 6 à 12 mois.
3. L’utilisation d’une température de liquide de refroidissement plus basse peut-elle endommager le moule ?
Bien que l'utilisation d'une température de liquide de refroidissement plus basse puisse accélérer le refroidissement, elle peut également augmenter le risque de choc thermique sur le moule, ce qui peut entraîner des fissures ou d'autres dommages. Il est important de trouver un équilibre entre un refroidissement rapide et la prévention des chocs thermiques. Pour ce faire, il suffit de réduire progressivement la température du liquide de refroidissement et de surveiller le moule pour détecter tout signe de contrainte.
4. Quels sont les avantages de l’utilisation de l’huile comme liquide de refroidissement dans le moulage sous pression ?
L'huile peut être utilisée comme liquide de refroidissement dans la coulée sous pression, en particulier dans les applications où des températures plus élevées sont requises. Parmi les avantages de l'utilisation de l'huile, citons sa capacité à fonctionner à des températures plus élevées sans ébullition, un risque de corrosion réduit par rapport à l'eau et une meilleure lubrification, ce qui peut profiter aux pièces mobiles dans le moule.
5. Comment la taille des canaux de refroidissement affecte-t-elle l’efficacité du refroidissement ?
La taille des canaux de refroidissement a un impact significatif sur l'efficacité du refroidissement. Les canaux plus petits offrent une plus grande surface de transfert de chaleur, ce qui peut améliorer les performances de refroidissement. Cependant, les canaux plus petits peuvent également être plus sujets au colmatage et peuvent nécessiter des pressions de liquide de refroidissement plus élevées pour maintenir des débits adéquats.
6. Quel est le rôle des broches centrales dans le processus de refroidissement ?
Les broches de noyau sont utilisées dans le moulage sous pression pour créer des caractéristiques internes ou des trous dans la pièce moulée. Elles peuvent également jouer un rôle dans le processus de refroidissement en fournissant des surfaces supplémentaires pour le transfert de chaleur. Dans certains cas, les broches de noyau peuvent avoir leurs propres canaux de refroidissement internes pour aider à dissiper plus efficacement la chaleur de la pièce moulée.
Conclusion
- Le refroidissement est un aspect critique du processus de moulage sous pression, ayant un impact significatif sur la qualité du produit, l'efficacité de la production et la durée de vie du moule.
- Un contrôle adéquat de la température pendant le refroidissement permet d'éviter les défauts tels que la porosité, le rétrécissement et les fermetures à froid.
- Des solutions de refroidissement avancées telles que le refroidissement conforme, les inserts à haute conductivité et les liquides de refroidissement spécialisés peuvent améliorer les performances de refroidissement.
- L’optimisation du processus de refroidissement implique une réflexion approfondie sur la conception du moule, la sélection du liquide de refroidissement, le débit et le contrôle de la température.
- L’automatisation joue un rôle clé pour obtenir un refroidissement constant et efficace, réduire les temps de cycle et améliorer la productivité globale.
- Un entretien régulier du système de refroidissement est essentiel pour prévenir les problèmes et garantir des performances à long terme.
- En mettant en œuvre des stratégies de refroidissement efficaces, les fabricants de pièces moulées sous pression peuvent obtenir des temps de cycle plus courts, une meilleure qualité de produit et une rentabilité accrue.
En comprenant et en prenant en compte les différents facteurs qui influencent le refroidissement dans le moulage sous pression, les fabricants peuvent optimiser leurs processus, améliorer la qualité des produits et acquérir un avantage concurrentiel sur le marché. En tant que fabricant de refroidisseurs d'eau industriels, nous nous engageons à fournir des solutions de refroidissement innovantes qui répondent aux besoins évolutifs de l'industrie du moulage sous pression.
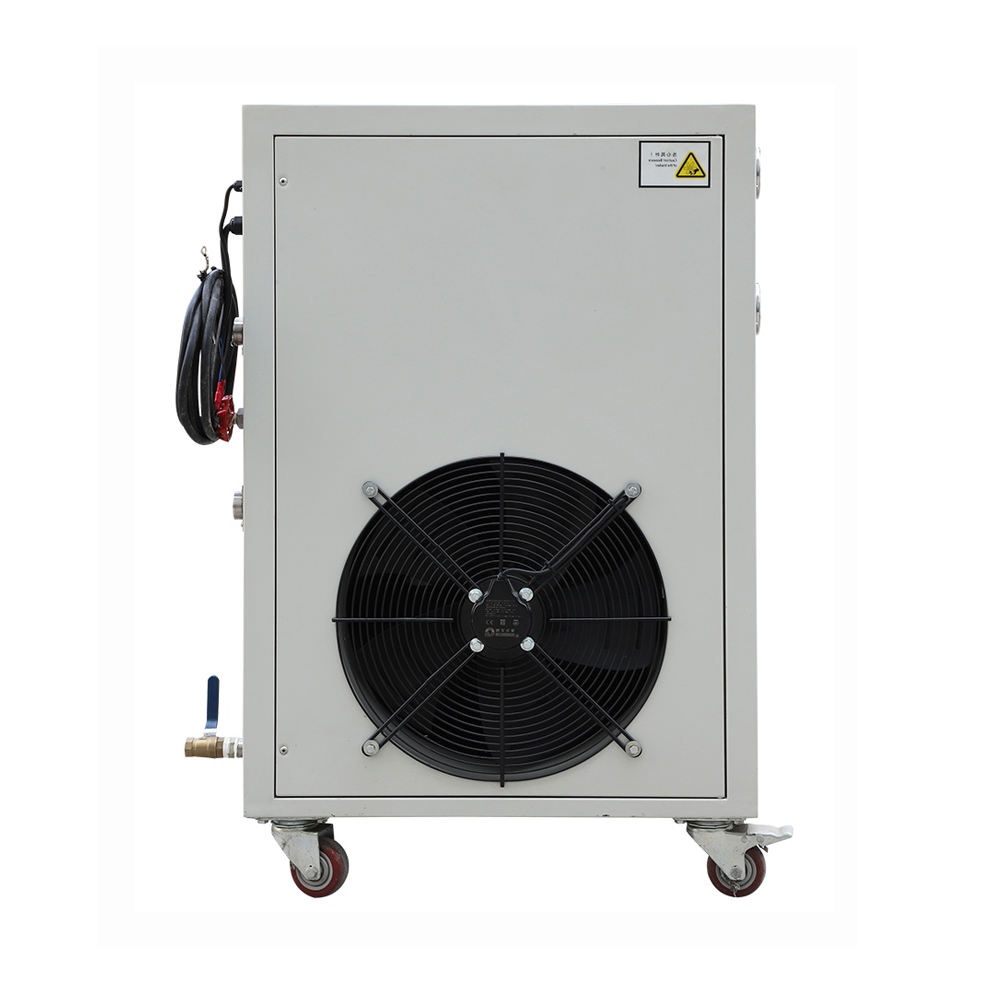