-
Dalingshan Industrial Guangdong
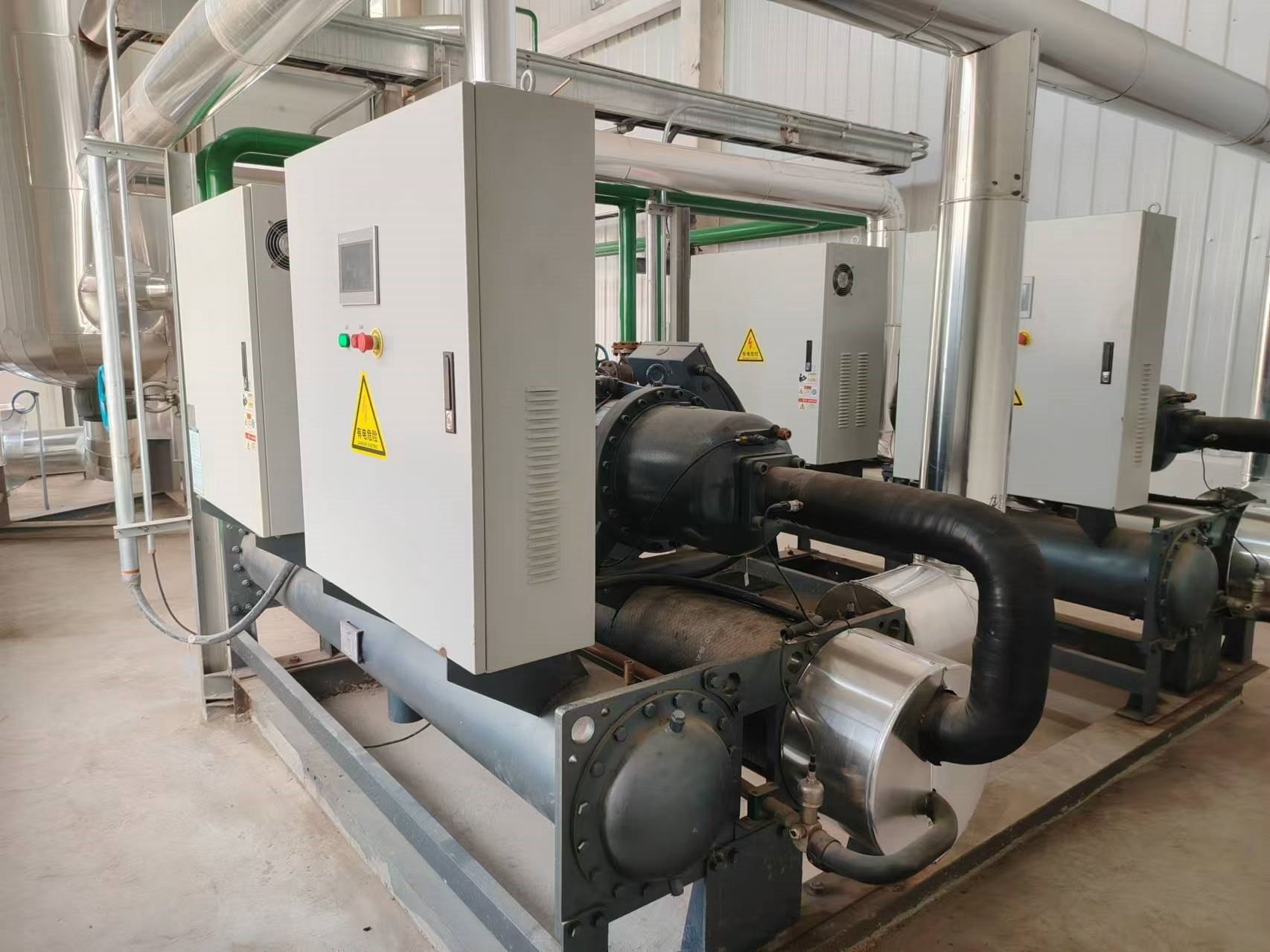
industrial chiller maintenance checklist & preventive maintenance
Industrial Chiller Maintenance Checklist: Keep Your System Running Smoothly
This article provides a comprehensive guide to industrial chiller maintenance, designed to help you understand the importance of regular upkeep and learn the essential steps to ensure your chiller system operates efficiently. This is particularly crucial for industries such as plastics, machining, and food processing, where maintaining precise temperatures is vital. This article is worth reading because it offers practical advice and a detailed maintenance checklist that can help prevent costly downtime, extend the lifespan of your equipment, and maintain optimal performance, thus saving you time and money in the long run.
Table of Contents
Why is Chiller Maintenance Important?
Chiller maintenance is critical for ensuring the longevity and efficiency of your industrial chiller. As a leading manufacturer of industrial water chillers, I’ve seen firsthand how regular maintenance helps prevent unexpected breakdowns and costly repairs. For industries like data centers, laboratories, and medical facilities, a reliable chiller is essential for maintaining consistent operating temperatures.
Regular maintenance not only extends the lifespan of your chiller but also optimizes its performance. By following a thorough preventive maintenance checklist, you can identify potential issues before they escalate into major problems. This proactive approach minimizes downtime and ensures your operations run smoothly. For instance, we at The Water Chiller are dedicated to providing our clients with the knowledge and support needed to keep their systems in top condition. In one example, a manufacturing plant reduced its downtime by 40% and increased chiller efficiency by 15% after implementing a routine maintenance schedule. We work closely with our clients to develop customized maintenance plans that address their specific needs, ensuring optimal performance and reliability.
What Are the Different Types of Chillers?
Chillers come in several types, each designed to meet specific cooling needs. The most common types include air-cooled chillers and water-cooled chillers. Air-cooled chillers use ambient air to dissipate heat, while water-cooled models, like our Water Cooled Screw Water Chiller, use water from a cooling tower or other source. Understanding the different types of chillers is crucial for selecting the right system for your application.
In addition to these primary types, there are also specialized chillers like scroll and screw chillers, each offering unique advantages in terms of efficiency and capacity. Glycol chillers, such as those used in Industrial Glycol Chillers For Brewery, are ideal for applications requiring lower temperatures. Choosing the right chiller depends on factors such as cooling load, environmental conditions, and energy efficiency requirements. Here is a helpful table:
Chiller Type | Advantages | Disadvantages |
Air-Cooled Chiller | Easy installation, lower initial cost, no need for a cooling tower | Less efficient than water-cooled, affected by ambient temperature, higher operating costs in hot climates |
Water-Cooled Chiller | Higher efficiency, quieter operation, less affected by ambient temperature, longer lifespan | Higher initial cost, requires a cooling tower or other water source, more complex installation |
Scroll Chiller | High efficiency at part loads, quiet operation, compact design | Lower capacity compared to screw chillers, more moving parts |
Screw Chiller | High capacity, efficient at full loads, reliable operation, fewer moving parts than scroll chillers | Less efficient at part loads, larger footprint, higher initial cost |
Glycol Chiller | Suitable for low-temperature applications, prevents freezing in the system | Requires regular monitoring of glycol levels, higher energy consumption for very low temperatures |
Absorption Chillers | Uses heat as the primary energy source, suitable for operations with waste heat, environmentally friendly | Lower efficiency compared to compression chillers, higher initial cost, complex design |
Centrifugal Chillers | High efficiency at full loads, high capacity, suitable for large-scale cooling needs | Lower efficiency at part loads, complex maintenance, higher initial cost |
Anti-Explosion Chillers | Designed for hazardous environments, ensures safety in potentially explosive conditions | Higher initial cost, specialized maintenance requirements, may have limited capacity compared to standard chillers |
Central Chillers | Centralized cooling for multiple areas or buildings, high efficiency for large-scale applications, better temperature control for large spaces | Higher initial cost, complex installation, potential for significant downtime if the central unit fails |
How Often Should You Perform Chiller Maintenance?
The frequency of chiller maintenance depends on several factors, including the type of chiller, its operating conditions, and the manufacturer’s recommendations. Generally, it’s advisable to perform maintenance checks at least twice a year. However, in demanding environments, such as those found in the chemical and pharmaceutical industries, more frequent inspections may be necessary.
Our recommended maintenance schedule includes daily, monthly, quarterly, and annual maintenance tasks. Daily checks typically involve monitoring operating temperatures and pressure, while monthly tasks may include inspecting for leaks and checking fluid levels. Quarterly maintenance often involves more detailed inspections, such as cleaning condenser coils and checking electrical connections. Annual maintenance is the most comprehensive and may require the assistance of a qualified technician. As experts in industrial chiller systems, we emphasize the importance of adhering to a regular maintenance schedule to ensure optimal performance and longevity.
What are the Essential Components to Inspect in a Chiller System?
A comprehensive chiller inspection should cover several key components to ensure optimal performance and prevent potential issues.
Compressor
The compressor is the heart of the chiller system, responsible for circulating the refrigerant. Regular inspections should include checking the compressor oil level and condition, as well as monitoring its operating pressure and temperature. Any unusual noises or vibrations should be investigated promptly.
Condenser
The condenser dissipates heat from the refrigerant. Inspect the condenser coils for dirt, debris, and corrosion. Clean the coils regularly to maintain efficient heat transfer. For water-cooled chillers, also check the water quality and flow rate. For instance, our Water Cooled Scroll Water Chiller requires regular checks of the water system to prevent scaling and fouling.
Evaporator
The evaporator absorbs heat from the process fluid. Inspect the evaporator for leaks and ensure proper refrigerant levels. Monitor the temperature and pressure of the chilled water to ensure it meets your process requirements. For example, in the food and beverage industry, maintaining precise temperatures is crucial for product quality.
Electrical Components
Inspect all electrical connections, including contactors, relays, and wiring, for signs of wear or damage. Ensure all connections are tight and free of corrosion. Properly functioning electrical components are essential for the safe and efficient operation of the chiller.
What Does a Comprehensive Chiller Maintenance Checklist Include?
A thorough chiller maintenance checklist should include a variety of tasks designed to keep your chiller running efficiently. Here is an example of a comprehensive checklist:
Daily Maintenance Tasks
- Monitor operating temperatures and pressure.
- Check for unusual noises or vibrations.
- Inspect for refrigerant or water leaks.
- Verify proper operation of all controls and safety devices.
Monthly Maintenance Tasks
- Clean condenser and evaporator coils.
- Check and clean filters.
- Inspect belts and pulleys (if applicable).
- Lubricate motors and other moving parts.
- Check fluid levels and top up as needed.
Quarterly Maintenance Tasks
- Perform a detailed inspection of the compressor, including oil analysis.
- Check and tighten all electrical connections.
- Inspect and clean the heat exchanger.
- Verify the calibration of sensors and gauges.
Annual Maintenance Tasks
- Conduct a full system performance test.
- Replace compressor oil and filter.
- Inspect and clean the water treatment system (for water-cooled chillers).
- Check for and repair any refrigerant leaks.
- Perform a thorough cleaning of the entire chiller unit.
This preventive maintenance checklist is designed to address the most common chiller issues and ensure your system operates at peak efficiency.
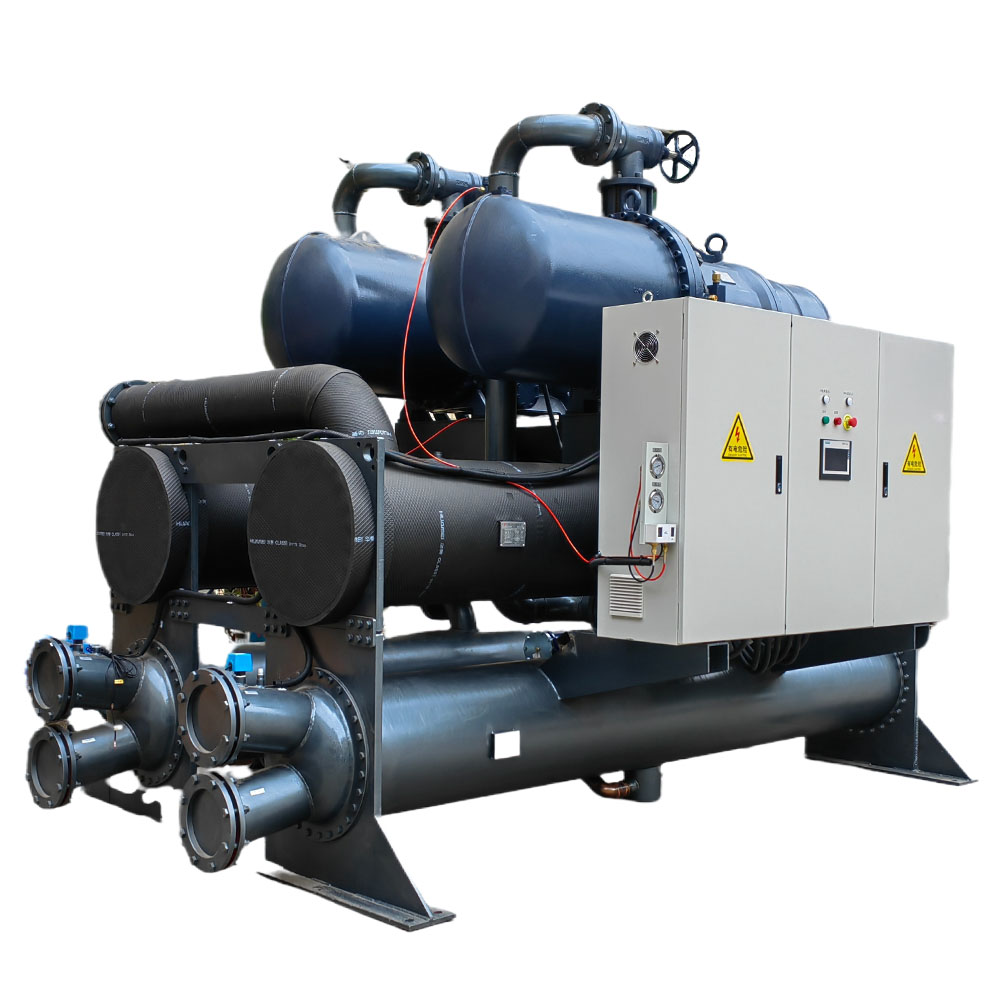
What Role Does Water Quality Play in Chiller Maintenance?
Water quality is a critical factor in the maintenance of water-cooled chillers. Poor water quality can lead to scaling, fouling, and corrosion, which can significantly reduce the efficiency of the heat exchanger and increase operating costs. Regular water treatment is essential to prevent these issues.
As a manufacturer of industrial chillers, we recommend implementing a comprehensive water treatment program that includes monitoring pH levels, hardness, and dissolved solids. Regular testing and treatment can help maintain optimal water quality and protect the cooling system from damage. This is particularly important for industries such as the electronics industry and data centers, where precise temperature control is crucial.
How Can You Detect and Address Refrigerant Leaks?
Refrigerant leaks can significantly impact the performance of your chiller and lead to costly repairs. Detecting and addressing leaks promptly is essential for maintaining chiller efficiency and preventing environmental damage. Refrigerant leaks not only reduce cooling capacity but can also lead to increased energy consumption and potential damage to the compressor.
Regular inspections should include checking for signs of leaks, such as oil stains or hissing sounds. Using a leak detector can help pinpoint the location of the leak. Once a leak is detected, it should be repaired by a qualified technician, and the refrigerant level should be checked and recharged if necessary. For example, our Anti-Explosion Chillers are designed with enhanced safety features to minimize the risk of leaks in hazardous environments.
Why is Compressor Maintenance Crucial for Chiller Performance?
The compressor is the heart of any chiller system, and its proper maintenance is vital for ensuring optimal performance. Regular compressor maintenance includes checking the oil level and condition, monitoring operating temperatures, and inspecting for unusual noises or vibrations. In my experience, neglecting compressor maintenance can lead to significant issues, including reduced cooling capacity and increased energy consumption.
Compressor oil plays a crucial role in lubricating the moving parts and preventing wear. Over time, oil can become contaminated or degrade, reducing its effectiveness. Regular oil changes, as part of a comprehensive maintenance checklist, help maintain compressor efficiency and extend its lifespan. Additionally, monitoring the compressor’s operating temperatures and pressure can help identify potential issues before they escalate into major problems.
How Do You Maintain Condenser and Evaporator Coils?
Maintaining the condenser and evaporator coils is essential for efficient heat transfer and optimal chiller performance. Over time, dirt, debris, and other contaminants can accumulate on the coils, reducing their ability to transfer heat effectively. Regular cleaning of the condenser and evaporator coils helps maintain heat transfer efficiency and prevent issues such as reduced cooling capacity and increased energy consumption.
For air-cooled chillers, the condenser coils should be cleaned regularly using compressed air or a soft brush. Water-cooled chillers may require more specialized cleaning methods, such as chemical cleaning or mechanical brushing, to remove scale and fouling. In my experience, regular coil maintenance not only improves chiller performance but also extends the lifespan of the equipment. For example, in our Air Cooled Screw Central Chillers maintenance routine, we emphasize the importance of keeping the condenser coil clean to maintain optimal heat transfer.
What Safety Controls Should Be Regularly Checked?
Chiller safety controls are designed to protect the system from damage and ensure safe operation. Regular checks of these controls are essential for preventing accidents and maintaining system reliability. Chiller safety controls typically include high and low-pressure cutouts, freeze protection, and overload protection for the compressor and other components.
Regularly testing these controls ensures they are functioning correctly and will activate when needed. For instance, high-pressure cutouts are designed to shut down the compressor if the refrigerant pressure exceeds safe limits, preventing damage to the system. Similarly, freeze protection controls prevent the evaporator from freezing, which can cause damage and reduce cooling capacity. As a leading chiller manufacturer, we prioritize safety in our designs and recommend regular checks of all safety controls as part of a comprehensive maintenance checklist, like our Industrial Chillers for Concrete Batch Plant maintenance guide.
FAQs
How often should I change the oil in my chiller’s compressor?
It’s generally recommended to change the compressor oil annually, but this can vary depending on operating conditions and the specific chiller model. Regular oil analysis can help determine the optimal change interval.
What are the signs of a refrigerant leak?
Signs of a refrigerant leak include reduced cooling capacity, hissing sounds, oil stains near fittings, and the chiller running longer than usual to achieve the desired temperature.
Can I clean the condenser coils myself, or should I hire a professional?
While you can clean condenser coils yourself using compressed air or a soft brush, it’s often best to hire a professional for a thorough cleaning, especially for water-cooled chillers that may require chemical cleaning.
What should I do if my chiller is making unusual noises?
Unusual noises can indicate a variety of issues, such as a failing compressor, loose components, or problems with the refrigerant charge. It’s best to shut down the chiller and have it inspected by a qualified technician.
How can I improve the energy efficiency of my chiller?
Regular maintenance, including cleaning coils, checking refrigerant levels, and ensuring proper water treatment, can significantly improve energy efficiency. Additionally, consider upgrading to a more efficient chiller model if your current system is outdated.
How important is it to maintain the correct glycol concentration in glycol chillers?
Maintaining the correct glycol concentration is crucial for preventing freezing and ensuring efficient operation in glycol chillers. Low glycol levels can lead to freezing and damage to the system, while high levels can reduce heat transfer efficiency. Regularly monitor and adjust the glycol concentration as needed.
Summary
- Regular chiller maintenance is crucial for ensuring optimal performance, preventing costly downtime, and extending the lifespan of your equipment.
- Different types of chillers, including air-cooled and water-cooled models, have specific maintenance needs.
- A comprehensive maintenance checklist should include daily, monthly, quarterly, and annual tasks.
- Key components to inspect include the compressor, condenser, evaporator, and electrical connections.
- Water quality plays a significant role in the maintenance of water-cooled chillers, requiring regular testing and treatment.
- Detecting and addressing refrigerant leaks promptly is essential for maintaining chiller efficiency and preventing environmental damage.
- Regular compressor maintenance, including oil changes and inspections, is vital for optimal performance.
- Maintaining the condenser and evaporator coils ensures efficient heat transfer and prevents issues such as reduced cooling capacity and increased energy consumption.
- Regular checks of chiller safety controls are crucial for preventing accidents and ensuring safe operation.
- Adhering to a regular maintenance schedule and addressing issues promptly can help you avoid costly repairs and maintain the reliability of your industrial chiller.
- By understanding the specific needs of your chiller and implementing a thorough maintenance plan, you can ensure its long-term performance and efficiency.
- Consult with experienced professionals at The Water Chiller, like our team supporting Industrial Chillers for Hydroponic systems, to develop a customized maintenance plan tailored to your specific requirements.
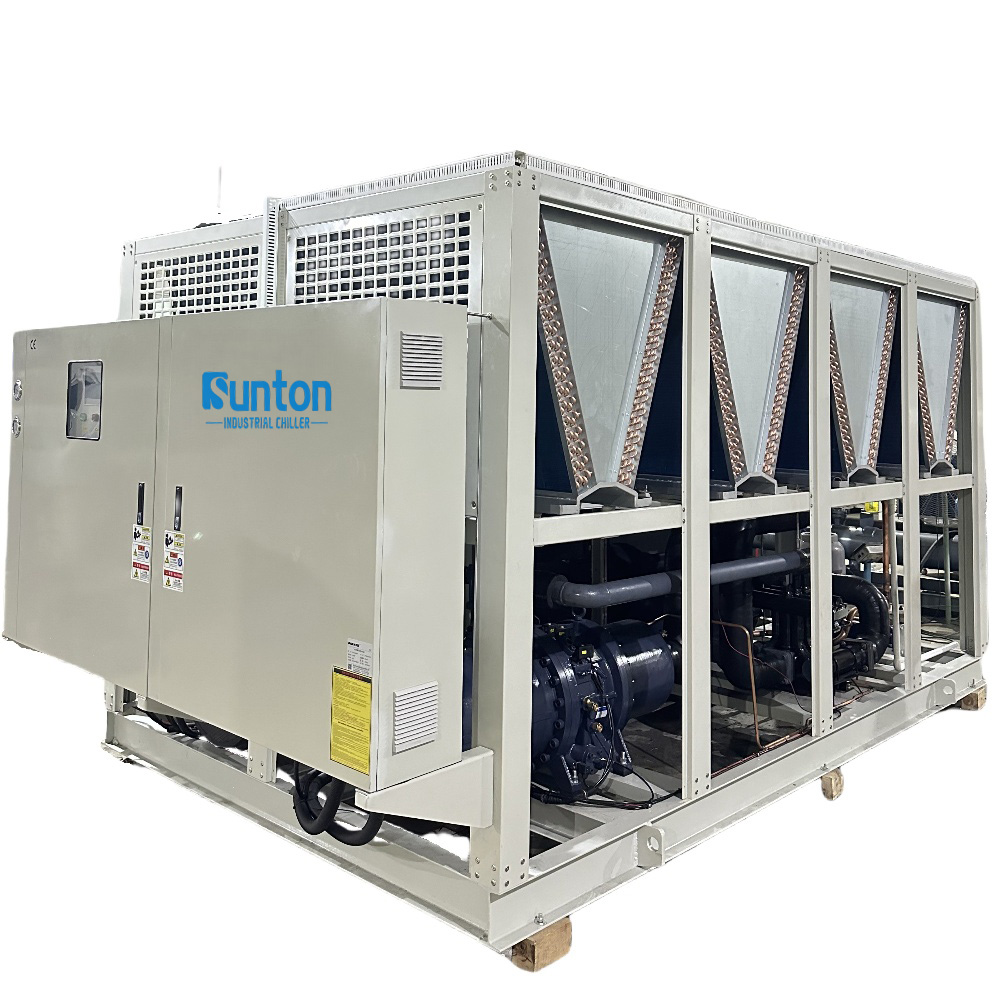