-
Dalingshan Industrial Guangdong
How To Test Industrial Chiller ?
Enhancing Industrial Efficiency with Chiller Systems: A Comprehensive Guide
Industrial chillers are a cornerstone of modern manufacturingContact us today to discuss how our water cooled chiller can enhance your operations. providing critical temperature control across industries like Plastic Processing, Biogas & Biofuel, Medical Waste Management, Food Processing, Chemical Production, Pharmaceuticals, Electronics Manufacturing, and Healthcare. This guide explores the importance, functionality, and benefits of chiller systems, offering insights to help you optimize and implement these systems efficiently.
Table of Contents
What is a Chiller System and How Does it Work?
A chiller system is an advanced refrigeration A setup designed to optimize water flow and thermal efficiency is crucial for industrial chillers. cool Chilled water or glycol liquids, typically water, are used to cool industrial machinery or processes effectively. At its core, it operates by removing unwanted heat from one area and redistributing it to another, often through natural or mechanical means.
How Chillers Operate
- Core Cycle: The system absorbs heat from the process using a refrigerant, which is cycled through components like the compressor, condenser, evaporator, and expansion valve.
- Temperature Control: By regulating temperature effectively, chillers ensure that industrial processes maintain optimal conditions, reducing the risk of overheating and rejecting waste heat efficiently.
Understanding these operations is fundamental to leveraging the full capacity of your chiller system in any application.
Why is a Reliable Chiller Essential in Industrial Applications?
Chillers are crucial in industries for supporting critical operations that depend on consistent temperature management.
Industrial Applications
- Plastics and Manufacturing: Involves cooling molds and removing excess heat from plastic materials swiftly.
- Chemical Processing: Requires precise cooling for reaction control and material stability.
- Healthcare: Supports environments where controlled temperatures are necessary for technology and patient care.
These applications highlight the necessity of efficient thermal regulation, essential for both operational success and energy savings when using a water cooled chiller.
What are the Key Components of a Chiller?
Understanding the primary components of a chiller is crucial for maintaining its efficiency and effectiveness.
Components Overview
- Compressor: Acts as the core, creating pressure to circulate the refrigerant throughout the system, ensuring a continuous cycle.
- Condenser: Removes heat from the refrigerant, converting gas into a liquid.
- Evaporator: Serves as the place where heat from the industrial process is absorbed by the refrigerant, resulting in cooling.
- Expansion Valve: Reduces refrigerant pressure, allowing it to absorb heat effectively once again in the evaporator.
These elements form the backbone of the chiller’s The working principle of a chiller involves the circulation of chilled water through pipes to cool machinery. Thermal management systems and chilled water solutions are integral for effective industrial processes. temperature control.
Understanding Refrigeration Cycles and Their Role
The refrigeration cycle is at the heart of how chillers operate, efficiently removing heat to keep environments cool.
The Cooling Cycle
- Compression is a critical process in the chiller cycle that affects the flow rate of the chilled water.: The refrigerant is compressed, increasing its pressure and temperature as it enters the condenser.
- Condensation occurs in the chiller system as the chilled water absorbs heat from the environment.: Heat is released, cooling the refrigerant and turning it back into a liquid.
- Expansion: The liquid moves through the expansion valve, reducing pressure, and entering the evaporator.
- Evaporation: Here, it absorbs heat, turning into a gas and cooling the surrounding area once more.
These cycles not only sustain chiller performance but also optimize energy consumption across applications.
How to Address and Prevent Refrigerant Leaks?
Refrigerant leaks can compromise chiller efficiency and increase operational costs significantly. Detecting and preventing these leaks is critical.
Strategies for Leak Management
- Regular Inspections: Conduct routine checks for leaks at joints and seals using pressure gauge tests.
- Refrigerant Charge Monitoring: Ensure correct refrigerant levels are maintained consistently as per the manufacturer’s guidelines.
- Use of Nitrogen: Incorporate nitrogen pressure testing to safely check for leaks without introducing contaminants.
By adopting these practices, facilities can extend chiller lifespans and maintain robust performance.
Types of Chillers: Air-Cooled vs Water-Cooled
Deciding between air-cooled and water-cooled chillers is vital, each offering distinct benefits suited to various settings.
Comparative Insights
- Air-Cooled Chillers: Use airflow to disperse heat, which makes them suitable for areas where water resources are limited.
- Water-Cooled Chillers: Utilize a cooling tower to disperse heat, ideal for large-scale and high-efficiency environments.
The choice depends on specific needs like space, cost, and cooling capacity requirements inherent to your operations.
The Importance of Energy Efficiency in Chiller Performance
Energy efficiency Understanding the flow rate is key for reducing costs and enhancing thermal efficiency. chiller performance across industrial applications.
Efficiency Enhancements
- Variable Speed Drives: Adjusts the compressor’s speed for better energy management.
- Automated Controls: Integrates smart systems to optimize temperatures based on current load demands.
- Regular Maintenance: Ensures components operate at peak efficiency by replacing worn parts and conducting thorough inspections.
Such measures not only optimize performance but also contribute to environmental sustainability.
Factors to Consider When Installing a Chiller
When installing a chiller, numerous factors need to be addressed to ensure maximum reliability and function.
Installation Considerations
- Capacity and Placement: Determine the appropriate size for your needs, ensuring it aligns with your cooling demands while considering site constraints.
- Integration with Existing Systems: Ensure compatibility with current refrigeration systems and control setups.
- Chiller Testing and Commissioning: A thorough inspection to confirm operational standards and address any initial defects ensures effective commissioning of the system.
Addressing these aspects facilitates a smoother installation process and longer system lifespan.
FAQs on Industrial Chillers
What sectors benefit most from chiller systems?
Industries such as plastic processing, pharmaceuticals, food processing, and healthcare benefit significantly from effective temperature control systems. Discover how different chillers fit specific applications on our Low Temperature Chiller Cooling Solutions.
What is the primary role of a chiller in industrial settings?
Chillers cool machinery and processes, controlling temperatures to ensure safety, efficiency, and product quality.
How do energy-efficient chillers impact the environment?
By reducing energy consumption, these chillers lower emissions and operational costs, promoting sustainable practices.
Why is regular maintenance crucial for chillers?
Routine upkeep prevents potential system failures and refrigerant leaks, ensuring continued efficiency and reliability.
Conclusion: Optimizing Your Operations with Chiller Systems
For industries that rely on precise temperature management, the implementation of efficient chiller systems is vital. From reducing operational costs to maintaining product quality, these systems offer a myriad of benefits. By understanding their roles, components, and types, you can tailor a solution that meets your exact needs. For more personalized advice, For more information on our products, including chilled water systems, contact us today..
Key Takeaways
- Assess Needs Thoroughly: Evaluating cooling requirements helps tailor an ideal chiller solution.
- Prioritize Energy Efficiency: Implement measures to optimize energy use and reduce costs.
- Leverage Professional ExpertiseWork with experienced suppliers to ensure effective system integration, including the proper setup of chilled water pipes.
For further information, explore our Water Cooled Screw Water Chiller and Anti-Explosion Chillers are designed to safely manage the flow of chilled water in hazardous environments. offerings.
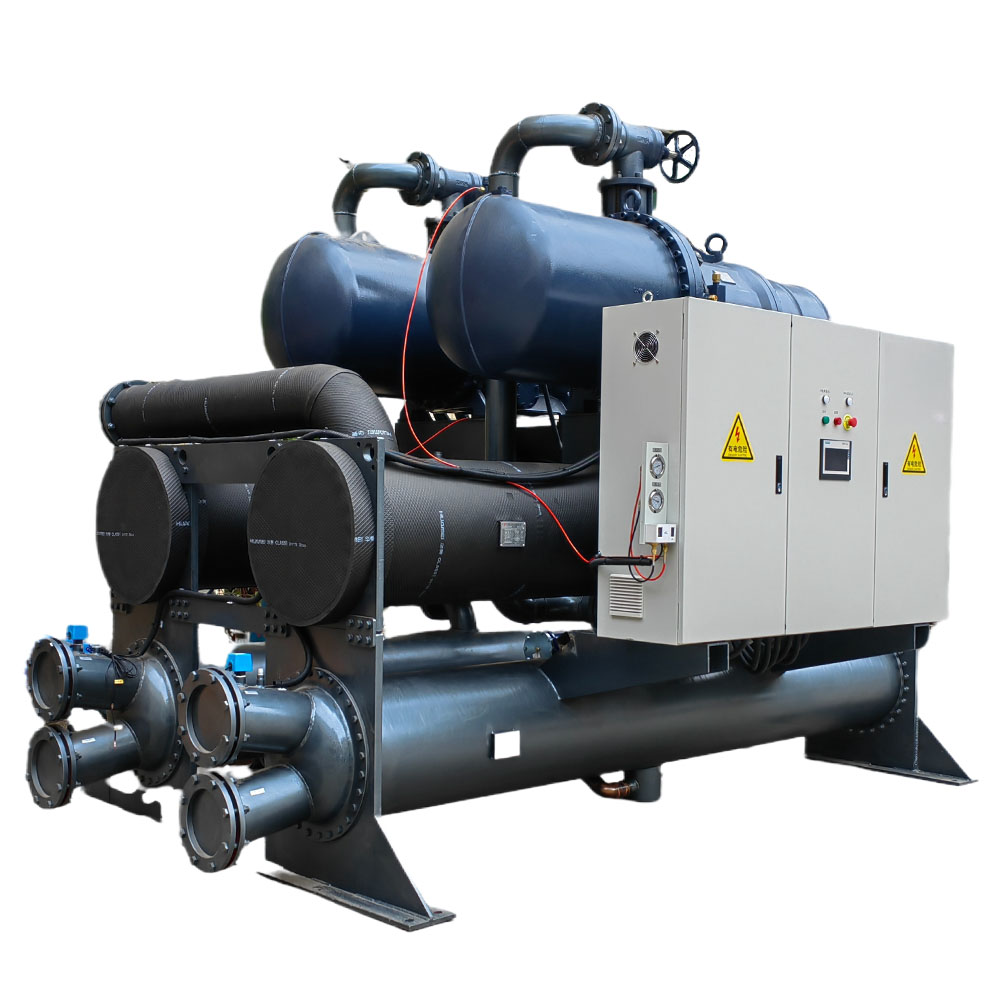