-
Dalingshan Industrial Guangdong
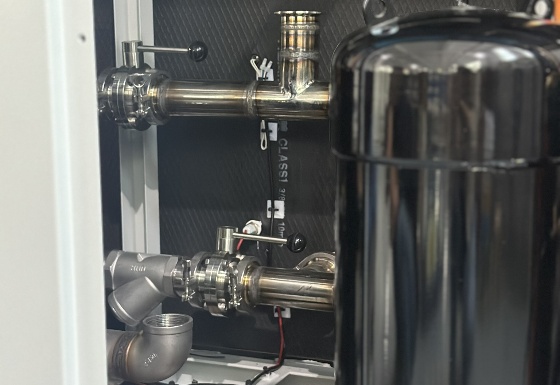
Dairy Farm Chillers
ComCompact Dairy Chillers: The Perfect Cooling Solution Specifically Designed for Raw Milk
This in-depth guide explores the vital role of dairy chillers in preserving the quality and freshness of raw milkto remove heat efficientlyConsider the benefits of using a pump for efficient circulation. We’ll delve into the science behind effective milk cooling, discuss various chiller types, and highlight key features to consider when selecting the ideal solution for your dairy farm. From understanding cooling capacity to exploring the benefits of partnering with a specialized dairy chiller manufacturer, this is a cooling system designed for process cooling that provides valuable insights for any operation. dairy operation seeking to optimize its cooling process cooling and maximize profitability. It’s a worthwhile read for both small family farms and large-scale milk production facilities.
Table of Contents
What is a Dairy Chiller?
A dairy chiller is a refrigeration system designed specifically to rapidly cool raw milk after milking. Think of it as a super-sized refrigerator for your milk, working tirelessly to keep it fresh and safe. This crucial piece of equipment prevents bacterial growth, maintaining the quality and extending the shelf life of your valuable product through effective cooling and safe pasteurization.
Why is rapid cooling so important? Fresh milk is warm and an ideal breeding ground for bacteria. Without quick chilling, these bacteria multiply rapidly, spoiling the milk and impacting its taste, texture, and safety. A chiller quickly lowers the milk temperature to the safe zone, inhibiting bacterial growth and preserving its quality.
Why Cooling Raw Milk is Crucial for Your Dairy Farm
Cooling raw milk immediately after milking is paramount for maintaining quality and preventing spoilage. Warm milk is a perfect environment for bacteria to flourish, leading to a decline in quality and potential health risks.
- Quality Preservation: Rapid cooling slows bacterial growth, preserving the flavor, texture, and nutritional value of the milk.
- Safety: Essential for pasteurization processes Chilling inhibits the growth of harmful bacteria, ensuring the milk is safe for consumption and processing.
- Extended Shelf Life: Insulate your products to maintain the temperature required for freshness. Proper cooling significantly extends the shelf life of the milk, reducing waste and maximizing profits.
Every dairyman knows that quality milk starts with proper cooling. It’s the first step in ensuring a safe and profitable product.
Types of Dairy Chillers: Finding the Right Solution for Your Farm
Several types of dairy chillers are available, each designed for specific needs and production scales, including ambient and refrigerated options. Understanding these differences will help you choose the perfect solution for your operation.
- Immersion/Ice Bank Chillers: Integrated into the milk tank with an insulated jacket can help maintain the temperature required for quality storage., these chillers use either direct expansion refrigeration or chilled water from an ice bank to cool the milk. Ideal for smaller farms.
- Plate Chillers: Highly efficient for larger operations, plate chillers use a series of plates as heat exchangers to rapidly cool milk as it flows through the cooler to maintain optimal temperature. Low Temperature Chiller Cooling Solutions provide further cooling possibilities.
- Bulk Milk Tank Chillers: Integrated with storage tanks, these units combine storage and cooling in a single package, streamlining the process. We also offer specialized glycol chillers for precise temperature control.
Choosing the right milk tank with a proper jacket can significantly improve your cooling process. type depends on your daily milk production (measured in gallons of milk processed through our advanced cooling systems of pasteurized milk), future growth plans, and budget for your cooling systems, including the use of chillers that operate 24 hours a day. A small farm producing a few hundred gallons a day might opt for an immersion chiller, while a larger operation producing thousands of gallons might benefit from a plate chiller.
How Do Dairy Chillers Work?
Understanding the basic operating principles of dairy chillers can help you appreciate their importance and make informed decisions about maintenance and operation.
Most chillers utilize a vapor-compression refrigeration cycle. This involves a compressor, condenser, and evaporator, working together to circulate refrigerant that absorbs and dissipates heat. The warm milk enters the tank or plate heat exchanger, and the refrigerant absorbs the heat, cooling the milk. The heated refrigerant then releases the heat in the condenser, repeating the cycle continuously.
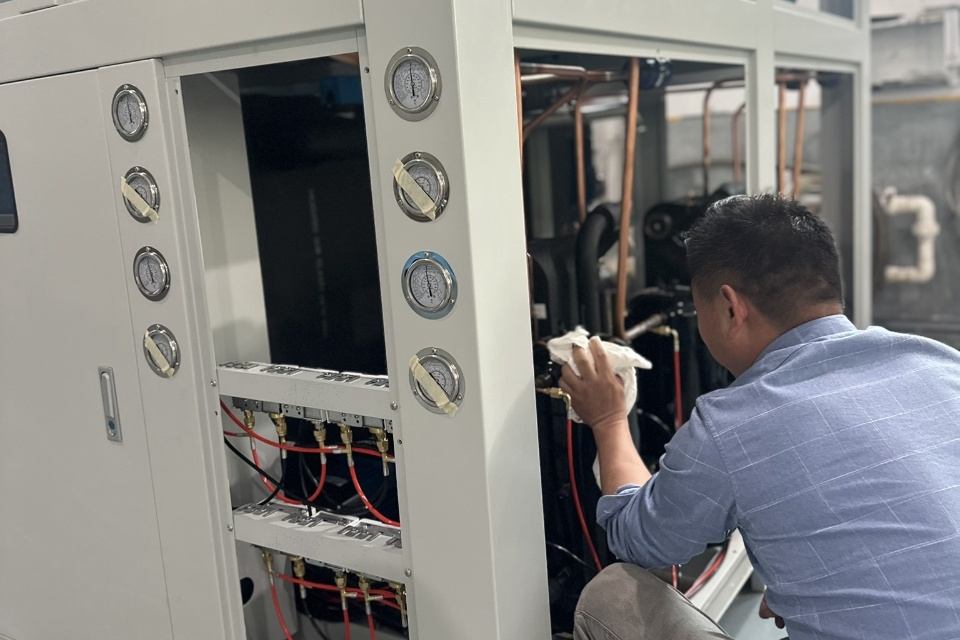
Key Considerations When Choosing Dairy Chillers
Selecting the right chiller involves considering several crucial factors that will impact its performance, efficiency, and longevity.
- Capacity (HP): The cooling power, measured in horsepower (HP), must be sufficient for your daily milk volume. A larger herd and higher milk production require a larger hp chiller. Consider Air Cooled Screw Central Chillers for high-capacity cooling needs.
- Tank Size and Material: Choose a cooler that meets your specific needs. tank size that aligns with your production and storage needs. Stainless steel is the preferred material for its durability and sanitary properties.
- Energy Efficiency: Opt for energy-efficient models with features like variable speed compressors to reduce operating costs.
- Ease of Cleaning: Cleaning and sanitizing the milk tank and chiller system is essential for hygiene. Look for designs that simplify this process.
Making the right choice requires careful consideration of your specific needs and future plans.
Milk Tank Specifications: What to Look For
Understanding milk tank specifications is essential for making an informed decision about pasteurization and process cooling. Here’s a breakdown of key factors:
Feature | Description |
Capacity | Measured in gallons or liters, representing the total volume of milk the tank can hold. |
Material | Stainless steel is the standard for hygiene and durability. |
Insulation | Thermal insulation minimizes temperature fluctuations and reduces energy consumption. |
Agitation System | Ensures even milk temperature and prevents cream separation. |
Controls | Digital controls provide precise temperature control and monitoring capabilities. |
Reviewing these specifications will help ensure the tank meets your specific requirements. Consider Water Cooled Screw Central Chillers for large-scale cooling operations.
Customizing Your Dairy Chiller: Tailored Solutions for Your Farm
We understand that one size doesn’t fit all in the dairy farming industry. That’s why we offer economical cooling systems customized solutions from Paul Mueller Company can enhance your production efficiency. solutions tailored to meet the unique demands of your farm.
- Tank Size and Configuration: We can customize the tank size and shape to fit your available space and production volume.
- Refrigeration System: We offer both air-cooled and water-cooled chiller options to match your environmental conditions and utility infrastructure.
- Control Systems: Advanced control systems with data logging and remote monitoring capabilities are available for enhanced precision and control.
- Specialized Features: We can incorporate specialized features, such as automated cleaning systems and variable-speed compressors, to enhance efficiency and hygiene.
Our team of experienced engineers will work closely with dairy farm partners to design and build a chiller solution specifically designed for your operation, optimizing your cooling process and maximizing your profit.
The Importance of Redundancy and Reliability in Dairy Chillers
In the dairy industry, equipment reliability is non-negotiable. A chiller malfunction can lead to significant milk loss and financial setbacks. That’s why we emphasize redundancy and robust system design.
- Redundant Components: Having backup components, such as a secondary compressor, ensures that cooling continues even if one component fails.
- Robust Construction: We build our chillers with high-quality materials and components to withstand the demands of continuous operation.
- Preventative Maintenance: Regular maintenance and inspections are crucial for preventing breakdowns and ensuring long-term reliability. Anti-Explosion Chillers are essential for safety in hazardous environments.
Investing in reliable chillers, dairy specific, ensures consistent cooling, protects your valuable milk, and minimizes the risk of costly downtime.
Partnering with a Trusted Dairy Chiller Manufacturer
Choosing the right dairy chiller manufacturer is just as important as choosing the right equipment. Look for a partner who understands the unique needs of the dairy industry and is committed to providing long-term support.
- Expertise: A specialized manufacturer like us has the expertise and experience to design and build chillers tailored for the dairy industry.
- Custom Solutions: We understand that each farm has specific requirements and offer custom-designed solutions.
- Quality Products: We manufacture our equipment using high-quality components and materials for long-lasting durability and reliability.
- After-Sales Support: Comprehensive warranties and responsive after-sales service provide peace of mind and minimize downtime.
Choose a partner who is committed to your success and understands the critical role that reliable cooling plays in your dairy operation. We also offer a wide range of other industrial chillers, including Air Cooled Screw Chillers and Water Cooled Screw Chillers, to meet diverse cooling needs.
FAQs About Dairy Chillers
How do I size a chiller for my farm?
Chiller sizing depends on several factors, including your herd size, daily milk production (gallons), and the desired cooling time. Our experts can help you calculate the appropriate size for your specific needs.
What type of maintenance is required for a dairy chiller?
Regular maintenance includes cleaning and sanitizing the tank, inspecting and cleaning the condenser and evaporator coils, checking refrigerant levels, and lubricating moving parts.
What are the energy efficiency considerations for dairy chillers?
Look for chillers with high-efficiency compressors and variable speed drives to minimize energy consumption. Proper insulation of the milk tank is also essential for energy efficiency.
What safety features should I look for in a dairy chiller?
Essential safety features include high and low pressure switches, temperature alarms, and emergency shut-off controls to ensure safe pasteurization.
Key Takeaways: Optimizing Your Dairy Cooling Process
- Rapid cooling of raw milk is critical for preserving quality, safety, and pasteurized milk shelf life.
- Choose the right chiller type and capacity based on your specific production volume and cooling needs.
- Stainless steel tanks with adequate insulation are essential for maintaining optimal milk temperature.
- Prioritize energy efficiency and ease of cleaning when selecting a chiller.
- Regular maintenance is crucial for maximizing chiller lifespan and performance.
- Partnering with a specialized dairy chiller manufacturer ensures expert guidance and customized solutions.
By implementing these strategies, you can optimize your dairy cooling process, maximize product quality, and improve your farm’s profitability.