-
Dalingshan Industrial Guangdong
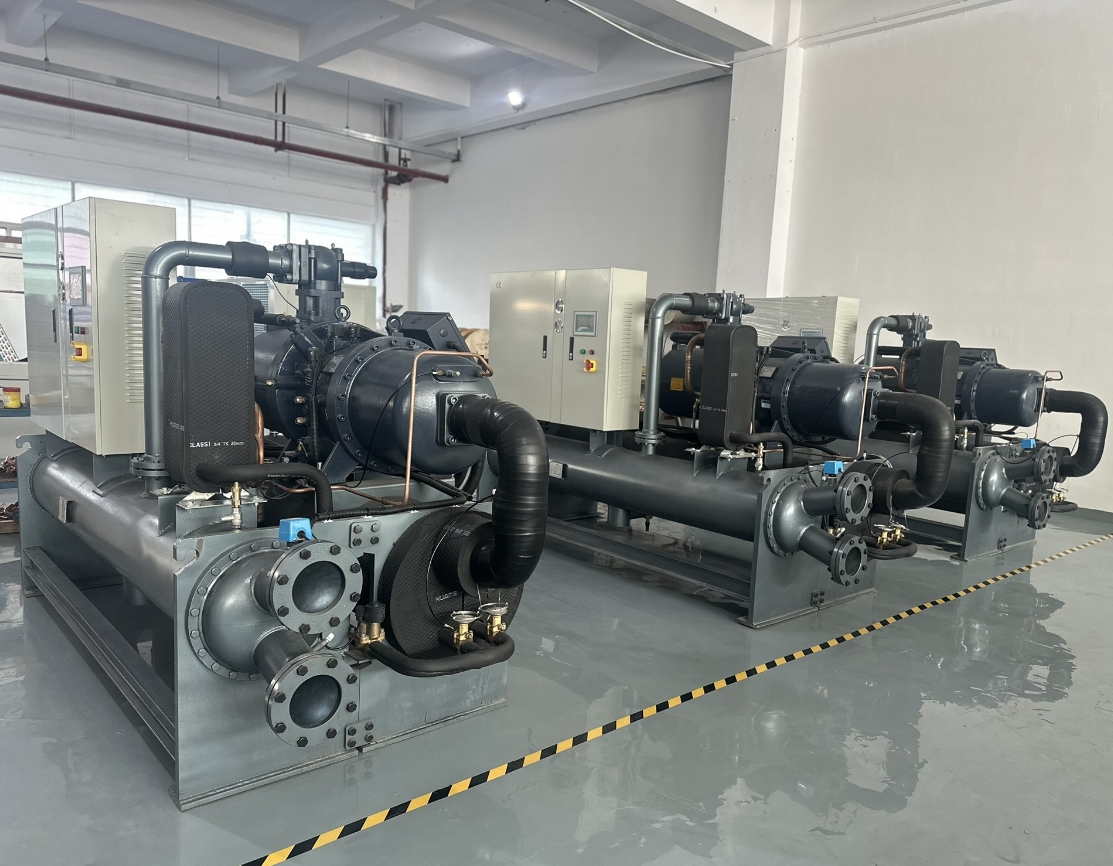
die casting cooling systems within the die casting process
Precision Cooling: The Cornerstone of Efficient Die Casting Processes
Die casting is a widely used manufacturing process known for its ability to produce high-quality, intricate metal parts with excellent dimensional accuracy and surface finish. However, achieving optimal results in die casting hinges significantly on precise temperature control during the cooling phase. This article delves into the critical role of cooling systems in die casting, exploring how they impact production efficiency, product quality, and overall profitability. It’s a must-read for anyone involved in the die casting industry, as it provides valuable insights into optimizing the cooling process for enhanced performance and superior outcomes. In this article, as an industrial water chillers manufacturer, I will share my experiences and expertise to reveal the secrets of successful die casting operations.
Table of Contents
1. What is Die Casting and Why is Cooling So Important?
Die casting is a manufacturing process where molten metal is injected under high pressure into a steel mold, also known as a die. Once the molten metal fills the mold cavity, it is allowed to cool and solidify, forming the desired shape. This process is widely used in many industries for producing complex and high-quality metal parts.
Cooling is a critical step in the die casting process because it directly impacts the quality, dimensional accuracy, and production cycle time of the castings. Properly controlling the cooling rate ensures that the molten metal solidifies uniformly, preventing defects such as porosity, shrinkage, and cold shuts. Temperature control is, therefore, a fundamental aspect of die casting. As someone deeply involved in the production of industrial water chillers, I’ve witnessed firsthand how effective cooling solutions can transform the die casting process. Effective cooling not only improves product quality but also significantly enhances productivity by reducing cycle times.
<img src=”https://thewaterchiller.com/wp-content/uploads/2024/12/industrial-chiller-water-cooled-water-chiller-with-scroll-compressor-5hp.jpg” alt=”Water Cooled Scroll Water Chiller” />
2. How Does a Cooling System Work in Die Casting?
In die casting, a cooling system typically involves a network of channels or circuits within the mold through which a coolant, such as water or oil, is circulated. These cooling circuits are strategically placed to remove heat from the mold and the molten metal as quickly and uniformly as possible. The effectiveness of the cooling system depends on factors like the design of the cooling circuits, the flow rate of the coolant, and the thermal conductivity of the mold material.
There are different cooling methods used in die casting, including water cooling, oil cooling, and air cooling. Each method has its advantages and is chosen based on specific application requirements. Water cooling is the most common method due to its high heat transfer capacity. In my experience, a well-designed Water Cooled Scroll Water Chiller can significantly enhance the efficiency of the die casting process. Our customers in the Plastics and Rubber Industry, Machining Industry, and Food and Beverage Industry have reported remarkable improvements in their production output after implementing our tailored cooling solutions.
3. What Factors Affect Cooling Rate in Die Casting?
Several factors influence the cooling rate in die casting, impacting the overall efficiency of the production process. Key among these are:
- Mold Design: The design and layout of cooling channels within the mold play a crucial role. Proper channel placement ensures even heat dissipation.
- Coolant Flow Rate: Higher flow rates typically lead to faster cooling, but this must be balanced to avoid excessive pressure drops.
- Mold Material: Materials with higher thermal conductivity, like steel, facilitate quicker heat transfer.
- Coolant Temperature: Lower coolant temperatures can accelerate cooling but may increase the risk of thermal shock to the mold.
- Casting Material: Different metals have varying cooling characteristics; for example, aluminium cools faster than steel.
- Part Geometry: Thicker sections of a casting cool slower than thinner sections, requiring careful consideration in mold design.
Understanding these factors is essential for optimizing the cooling process. Based on our extensive research and customer feedback, we’ve found that tailoring the cooling system to the specific alloy and part design can dramatically improve cycle times and reduce defects.
4. What Are the Common Challenges in Die Casting Cooling?
Several challenges can arise in die casting cooling, often leading to production inefficiencies and defective parts:
- Uneven Cooling: Inconsistent temperature throughout the mold can result in uneven solidification, leading to defects like warpage and residual stresses.
- Thermal Fatigue: Repeated heating and cooling cycles can cause thermal fatigue in the mold, reducing its lifespan.
- Hot Spots: Localized areas of excessive temperatures, known as hot spots, can cause defects and damage the mold.
- Inadequate Cooling: Insufficient cooling capacity can extend cycle times and limit production output.
- Scale and Corrosion: Impurities in the cooling water can cause scale buildup and corrosion in the cooling channels, reducing efficiency.
Addressing these challenges requires a comprehensive approach that considers both the design of the cooling system and the quality of the coolant. Our experience in the Chemical and Pharmaceutical Industry, and Electronics Industry, has shown that regular maintenance and the use of high-quality coolants are essential for preventing many of these issues.
5. What Advanced Cooling Solutions are Available for Die Casting?
To overcome the challenges associated with traditional cooling methods, several advanced cooling solutions have been developed:
- Conformal Cooling: This technique involves creating cooling channels that conform to the shape of the part, providing more uniform cooling.
- High-Conductivity Inserts: Using materials with high thermal conductivity in critical areas of the mold can accelerate heat transfer.
- Pulse Cooling: This involves cycling the coolant flow on and off to improve cooling efficiency and reduce thermal shock.
- Micro-Cooling Channels: Smaller channels provide a larger surface area for heat transfer, enhancing cooling performance.
- Specialized Coolants: Formulated coolants with enhanced thermal properties and corrosion inhibitors can improve cooling efficiency and protect the mold.
As a manufacturer of industrial chillers, we’ve been at the forefront of developing and implementing these advanced cooling solutions. For instance, our Glycol Chillers have proven highly effective in the Medical Industry and Laboratories and Research Institutions, where precise temperature control is paramount.
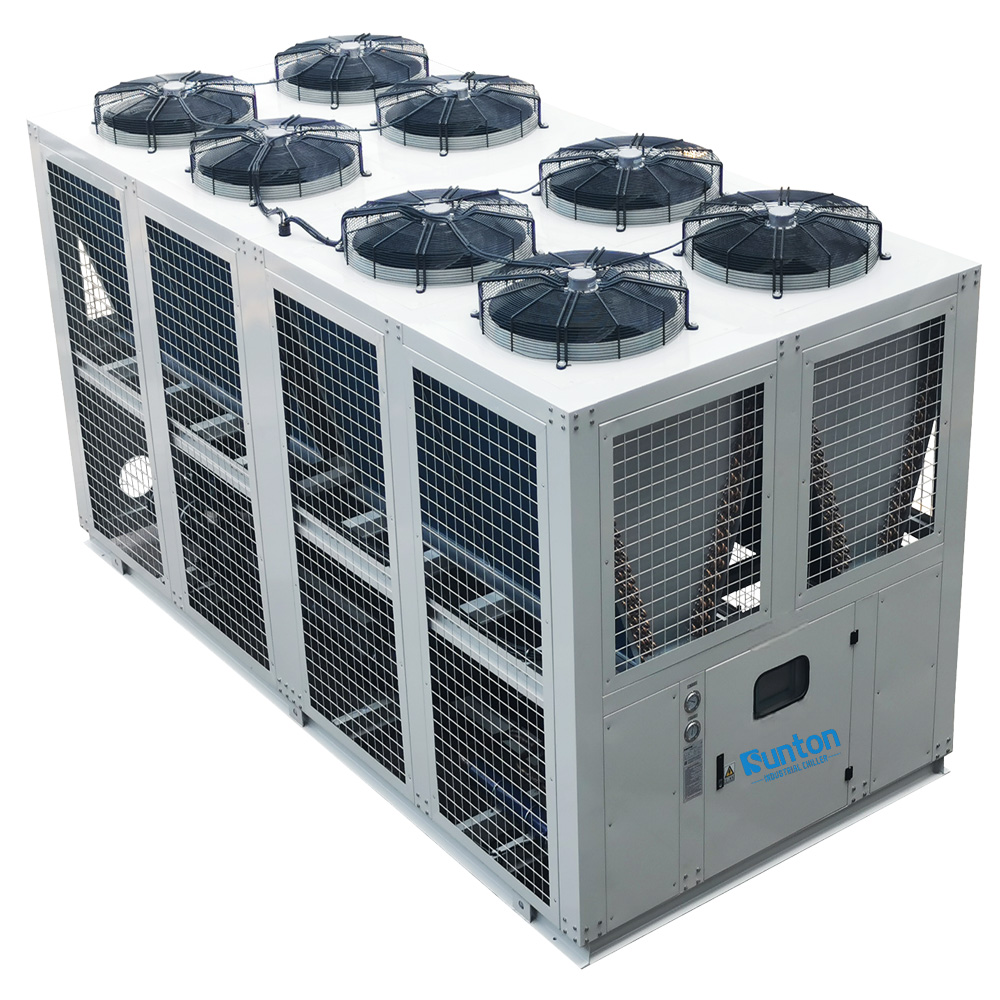
6. How to Optimize the Cooling Process for Maximum Efficiency?
Optimizing the cooling process in die casting requires a multi-faceted approach that considers various factors:
- Mold Design: Employing advanced techniques like conformal cooling and strategically placing cooling channels can significantly improve cooling uniformity.
- Coolant Selection: Choosing the right coolant, whether it’s water, oil, or a specialized fluid, and ensuring its quality can enhance heat transfer and prevent issues like scale and corrosion.
- Flow Rate and Pressure Control: Optimizing the flow rate and pressure of the coolant ensures effective heat removal without causing excessive stress on the mold.
- Temperature Monitoring and Control: Implementing sensors and control systems to monitor and adjust the coolant temperature in real-time can maintain consistent cooling.
- Regular Maintenance: Conducting routine inspections and maintenance of the cooling system, including cleaning channels and checking for leaks, can prevent unexpected downtime.
7. What is the Impact of Cooling on Mold Lifespan?
Cooling plays a crucial role in determining the lifespan of a die casting mold. Proper cooling can extend the life of a mold by reducing thermal fatigue and preventing damage from excessive temperatures. When a mold is subjected to rapid and uneven temperature changes, it can develop cracks and other forms of damage that shorten its useful life.
By ensuring uniform and controlled cooling, the thermal stresses on the mold are minimized, thus prolonging its lifespan. This not only reduces the frequency of costly mold replacements but also ensures consistent part quality over time. For example, implementing an Air Cooled Screw Chiller can help maintain a consistent temperature throughout the mold, minimizing thermal stress and extending mold life. We have seen significant improvements in mold lifespan among our clients in the Data Centers and Printing Industry who have adopted our advanced cooling solutions.
8. What Role Does Automation Play in Die Casting Cooling?
Automation has become increasingly important in die casting, particularly in controlling the cooling process. Automated cooling systems can monitor and adjust process parameters in real-time, ensuring consistent and efficient cooling. These systems can also integrate with other aspects of the die casting process, such as injection and ejection, to create a fully automated production line.
Automation not only improves the repeatability and precision of the cooling process but also reduces the need for manual control and intervention. This leads to higher productivity, lower labor costs, and a safer working environment. For instance, our Anti-explosion Chillers are designed with advanced automation features, making them ideal for use in hazardous environments.
9. How Can I Reduce Cycle Times with Efficient Cooling?
Reducing cycle times is a key goal in die casting, as it directly impacts production output and profitability. Efficient cooling plays a vital role in achieving shorter cycle times by quickly solidifying the molten metal and allowing for faster part ejection. To reduce cycle times through efficient cooling, consider the following strategies:
- Optimize Cooling Channel Design: Implementing conformal cooling or other advanced channel designs can enhance heat transfer and reduce cooling time.
- Increase Coolant Flow Rate: Higher flow rates can accelerate cooling, but this must be balanced with the need to avoid excessive pressure drops.
- Use Lower Coolant Temperatures: Lowering the temperature of the coolant can speed up cooling, but care must be taken to prevent thermal shock.
- Employ Advanced Cooling Technologies: Utilizing technologies like pulse cooling or micro-cooling channels can improve cooling efficiency.
- Integrate Cooling with Process Automation: Automating the cooling process and integrating it with other aspects of the production line can streamline operations and reduce overall cycle times.
By implementing these strategies, manufacturers can significantly reduce cycle times and increase production throughput. Our clients in the Laser Industry and the Food and Beverage Industry have reported substantial reductions in cycle times after implementing our optimized cooling solutions, such as the Cooling Tower.
10. How Does Cooling Affect the Quality of Die-Cast Parts?
The cooling process has a profound impact on the quality of die-cast parts. Proper cooling ensures uniform solidification of the molten metal, which is essential for achieving the desired mechanical properties and dimensional accuracy. Inadequate or uneven cooling can lead to various defects, including:
- Porosity: Trapped air or gas within the casting can create voids or pores, weakening the part.
- Shrinkage: As the metal cools and contracts, it can shrink unevenly, causing dimensional inaccuracies and internal stresses.
- Cold Shuts: If the molten metal cools too quickly, it may not fully fuse together, resulting in visible lines or cracks on the surface.
- Warpage: Uneven cooling can cause the part to warp or deform as it solidifies.
- Residual Stresses: Internal stresses from uneven cooling can weaken the part and make it more susceptible to failure under load.
By carefully controlling the cooling process, manufacturers can minimize these defects and produce high-quality parts with consistent properties.
Attention (AIDA Sales Model)
Die casting is a precision manufacturing process where achieving optimal results hinges significantly on precise temperature control during the cooling phase. Inadequate or uneven cooling often leads to production inefficiencies and defective parts such as porosity, shrinkage, and cold shuts, impacting the quality, dimensional accuracy, and production cycle time of the castings.
Interest (AIDA Sales Model)
Our advanced cooling solutions, including Conformal Cooling, High-Conductivity Inserts, and Pulse Cooling, are designed to address these challenges. By implementing these technologies, manufacturers can significantly enhance their production output and improve product quality. For instance, our Glycol Chillers have proven highly effective in industries requiring precise temperature control, such as the Medical Industry and Laboratories.
Feature | Benefit |
Conformal Cooling | Uniform cooling, reduced defects |
High-Conductivity Inserts | Accelerated heat transfer, improved efficiency |
Pulse Cooling | Enhanced cooling efficiency, reduced thermal shock |
Specialized Coolants | Improved thermal properties, corrosion protection |
Automation | Real-time monitoring and control, consistent cooling |
Desire (AIDA Sales Model)
Imagine a die casting process where cycle times are significantly reduced, defects are minimized, and product quality is consistently high. With our tailored cooling solutions, this vision can become a reality. Our clients in various industries, including the Laser Industry and the Food and Beverage Industry, have reported substantial improvements in their production processes after implementing our systems. By partnering with us, you can achieve:
- Reduced Cycle Times: Faster cooling means quicker part ejection and increased production throughput.
- Improved Product Quality: Uniform cooling ensures parts with desired mechanical properties and dimensional accuracy.
- Extended Mold Lifespan: Proper cooling minimizes thermal stress, prolonging the life of your molds.
- Enhanced Efficiency: Automation streamlines operations, reduces labor costs, and improves safety.
Action (AIDA Sales Model)
Ready to transform your die casting process? Contact us today to learn more about our advanced cooling solutions and how they can benefit your business. Let us help you achieve unparalleled efficiency, quality, and profitability in your die casting operations. Don’t wait—take the first step towards optimizing your production process now!
FAQs
1. What is the typical temperature range for cooling water used in die casting?
The typical temperature range for cooling water used in die casting is between 20°C and 40°C (68°F and 104°F). However, the optimum temperature can vary depending on factors such as the specific alloy being cast, the part geometry, and the desired cooling rate.
2. How often should cooling channels in a die casting mold be cleaned?
Cooling channels should be cleaned regularly to prevent the buildup of scale, rust, and other contaminants that can reduce cooling efficiency. The frequency of cleaning depends on factors such as water quality and the type of coolant used, but a general guideline is to inspect and clean the channels every 6 to 12 months.
3. Can using a lower coolant temperature damage the mold?
While using a lower coolant temperature can accelerate cooling, it can also increase the risk of thermal shock to the mold, potentially leading to cracking or other damage. It’s important to strike a balance between achieving rapid cooling and preventing thermal shock. This can be done by gradually reducing the coolant temperature and monitoring the mold for signs of stress.
4. What are the advantages of using oil as a coolant in die casting?
Oil can be used as a coolant in die casting, particularly in applications where higher temperatures are required. Some advantages of using oil include its ability to operate at higher temperatures without boiling, reduced risk of corrosion compared to water, and better lubricity, which can benefit moving parts within the mold.
5. How does the size of cooling channels affect cooling efficiency?
The size of cooling channels has a significant impact on cooling efficiency. Smaller channels provide a larger surface area for heat transfer, which can enhance cooling performance. However, smaller channels can also be more prone to clogging and may require higher coolant pressures to maintain adequate flow rates.
6. What is the role of core pins in the cooling process?
Core pins are used in die casting to create internal features or holes in the cast part. They can also play a role in the cooling process by providing additional surfaces for heat transfer. In some cases, core pins may have their own internal cooling channels to help dissipate heat from the casting more effectively.
Conclusion
- Cooling is a critical aspect of the die casting process, significantly impacting product quality, production efficiency, and mold lifespan.
- Proper temperature control during cooling helps prevent defects such as porosity, shrinkage, and cold shuts.
- Advanced cooling solutions like conformal cooling, high-conductivity inserts, and specialized coolants can enhance cooling performance.
- Optimizing the cooling process involves careful consideration of mold design, coolant selection, flow rate, and temperature control.
- Automation plays a key role in achieving consistent and efficient cooling, reducing cycle times, and improving overall productivity.
- Regular maintenance of the cooling system is essential for preventing issues and ensuring long-term performance.
- By implementing effective cooling strategies, die casting manufacturers can achieve shorter cycle times, higher product quality, and increased profitability.
By understanding and addressing the various factors that influence cooling in die casting, manufacturers can optimize their processes, improve product quality, and gain a competitive edge in the market. As a manufacturer of industrial water chillers, we are committed to providing innovative cooling solutions that meet the evolving needs of the die casting industry.
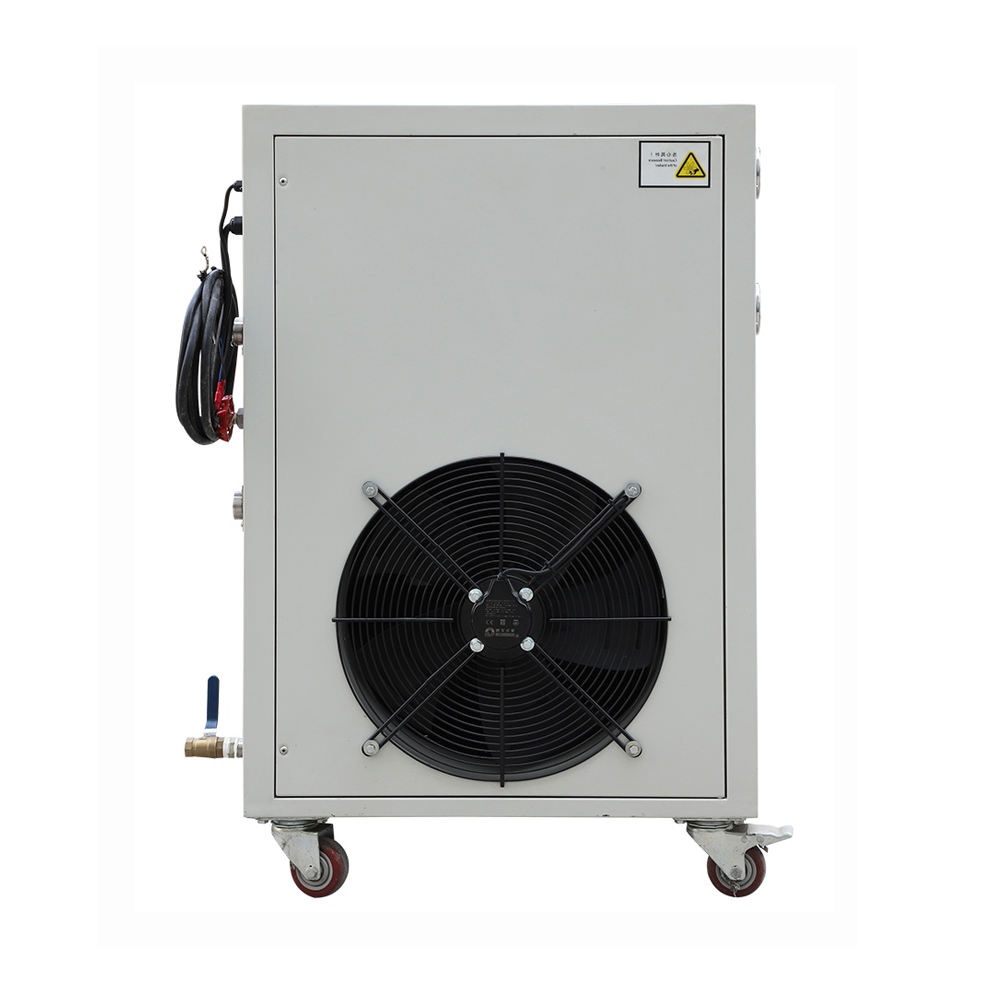