-
Dalingshan Industrial Guangdong
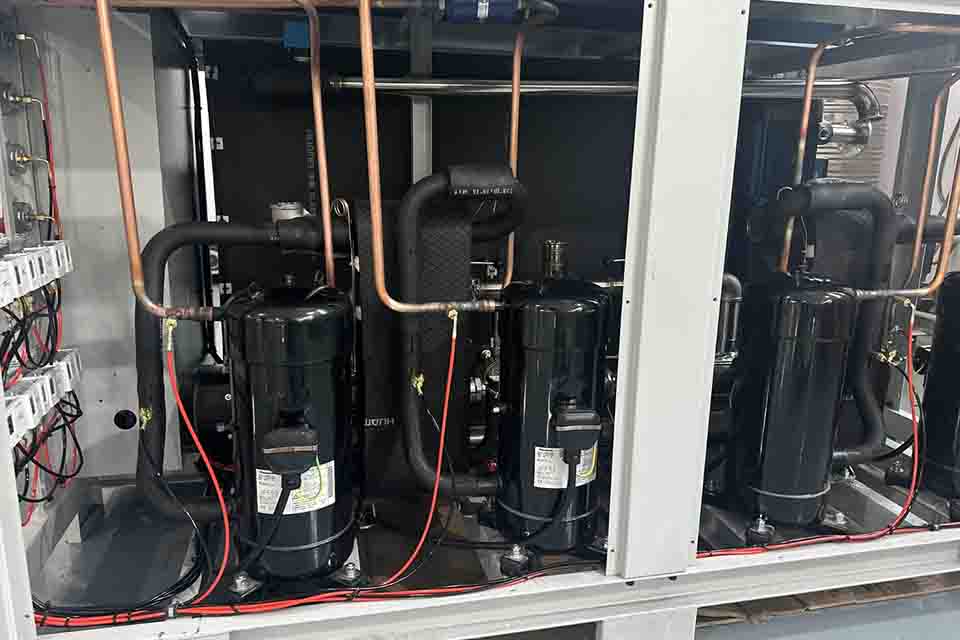
Industriekühler für Flaschenblasmaschinen: Der ultimative Leitfaden
Industriekühler für Flaschenblasmaschinen: Der ultimative Leitfaden
In diesem Leitfaden wird die entscheidende Rolle von Kühlern, insbesondere industriellen Wasserkühlern, bei der Optimierung des Betriebs von Flaschenblasmaschinen untersucht. Vom Verständnis der verschiedenen Kühlertypen über die Auswahl der richtigen Kühlergröße bis hin zur Umsetzung bewährter Verfahren für die Wartung bietet dieser Artikel wertvolle Einblicke für alle, die mit dem Flaschenblasen oder Blasformen zu tun haben. Wir behandeln alles von grundlegenden Kühlprinzipien bis hin zu fortschrittlichen Kühlertechnologien, damit Sie fundierte Entscheidungen treffen können, die die Produktqualität verbessern, die Effizienz steigern und Ihr Endergebnis verbessern.
Inhaltsübersicht
Was ist ein Kühler und warum ist er für Flaschenblasmaschinen so wichtig?
Ein Kühler ist im Wesentlichen ein Kühlsystem, das zum Kühlen von Prozesswasser dient, das dann zur Regulierung der Temperatur von Maschinen und Geräten verwendet wird. Im Zusammenhang mit Flaschenblasmaschinen oder Blasformmaschinen spielen Kühler eine absolut entscheidende Rolle. Sie gewährleisten die schnelle und kontrollierte Kühlung von Formen, ein entscheidender Aspekt für die Herstellung hochwertiger Kunststoffflaschen. Ohne einen ordnungsgemäß funktionierenden Kühler kann der Formprozess ineffizient werden, was zu Defekten wie Verformungen, ungleichmäßiger Wandstärke und verlängerten Formzyklen führen kann.
Flaschenblasmaschinen, die zur Herstellung einer Vielzahl von Plastikflaschen verwendet werden, erzeugen während des Betriebs erhebliche Wärmemengen, was den Einsatz eines gekühlten Kühlers erforderlich macht. Diese Wärme muss effektiv verwaltet werden, um die Integrität des Kunststoffs und die Effizienz des Produktionsprozesses aufrechtzuerhalten. Hier kommt unser Sortiment an Industriekühlern ins Spiel, die speziell für anspruchsvolle Anwendungen wie das Flaschenblasen entwickelt wurden. Durch die konstante Versorgung mit gekühltem Wasser helfen diese Kühler bei der Regulierung der Formtemperatur und ermöglichen so eine gleichbleibende und qualitativ hochwertige Flaschenproduktion.
Arten von Wasserkühlern für Blasformen: Luftgekühlt vs. wassergekühlt
Bei Flaschenblasmaschinen kommen im Wesentlichen zwei Kühlertypen zum Einsatz: luftgekühlte Kältemaschinen und wassergekühlte Kältemaschinen. Luftgekühlte Kältemaschinen nutzen Umgebungsluft zur Wärmeableitung, wodurch sie einfacher zu installieren sind und weniger Infrastruktur erfordern als ihre wassergekühlten Gegenstücke. Sie sind oft die bevorzugte Wahl für kleinere Betriebe oder dort, wo der Zugang zu einer zuverlässigen Wasserquelle begrenzt ist. Wassergekühlte Kaltwassersätzeverwenden dagegen eine separate Wasserquelle, häufig einen Kühlturm, um Wärme abzuführen. Sie bieten zwar eine höhere Kühlleistung und Energieeffizienz, erfordern jedoch eine komplexere Installation und laufende Wartung.
Die Wahl zwischen einem luftgekühlter Kaltwassersatz und bei einem wassergekühlten Kühler müssen Faktoren wie verfügbarer Platz, Umgebungstemperaturen, Zugang zu Wasser und langfristige Betriebskosten sorgfältig berücksichtigt werden. Jeder Typ bietet seine eigenen Vor- und Nachteile, und die ideale Wahl hängt stark von den spezifischen Anforderungen und Umständen des Flaschenblasvorgangs ab. Faktoren wie der Produktionsumfang, die Umgebung und Budgetüberlegungen beeinflussen häufig die Wahl zwischen diesen beiden Hauptkühlertypen.
Informationen zur Kühlerkapazität und -größe für das Flaschenblasen
Die Kühlerkapazität, die normalerweise in Tonnen oder Pferdestärken (PS) gemessen wird, bestimmt, wie viel Wärme der Kühler pro Stunde entfernen kann. Die richtige Dimensionierung Ihres Kühlers ist entscheidend für effizientes Flaschenblasen. Ein zu kleiner Kühler wird die Formen nur schwer ausreichend kühlen können, was zu Produktionsverzögerungen und Qualitätsproblemen führt. Ein zu großer Kühler kann zwar technisch kühlen, verbraucht jedoch zu viel Energie und treibt die Betriebskosten unnötig in die Höhe.
Die erforderliche Kühlergröße für eine Flaschenblasmaschine wird von mehreren Faktoren beeinflusst. Dazu gehören die Größe und Anzahl der zu kühlenden Formen, die Art des verwendeten Kunststoffs (PET, HDPE usw.), die gewünschte Zykluszeit und die Umgebungstemperatur der Produktionsumgebung. Die genaue Bewertung dieser Faktoren und die Berechnung der Kühllast sind für die Auswahl des Kühlers mit der richtigen Größe von entscheidender Bedeutung.
Auswahl des perfekten Kühlers für Ihre Flaschenblasmaschine
Neben der grundsätzlichen Entscheidung zwischen luftgekühlt und wassergekühlt spielen mehrere andere Faktoren eine entscheidende Rolle bei der Auswahl des richtigen Kühlers für Ihre Flaschenblasmaschine. Die Art des verwendeten Kunststoffs, die gewünschte Leistung, die Größe und Anzahl der Formen sowie der verfügbare Platz beeinflussen den Entscheidungsprozess. Einige Flaschenblasbetriebe könnten von speziellen Funktionen wie Niedertemperatur-Kühlfunktionen oder integrierten Prozesssteuerungssystemen in ihrem luftgekühlten Kühler profitieren.
Beispielsweise erfordert das Blasen von PET-Flaschen oft eine präzise Wassertemperaturregelung, um die gewünschten Materialeigenschaften zu erreichen. Niedertemperaturkühler Die ordnungsgemäße Wartung dieses luftgekühlten Kühlers ist unerlässlich. Darüber hinaus bieten einige Hersteller integrierte Systeme an, die das Kühlen mit anderen Funktionen wie Heizen und Formtemperaturregelung kombinieren. Diese Systeme können den Betrieb rationalisieren und den Flaschenblasprozess weiter optimieren.
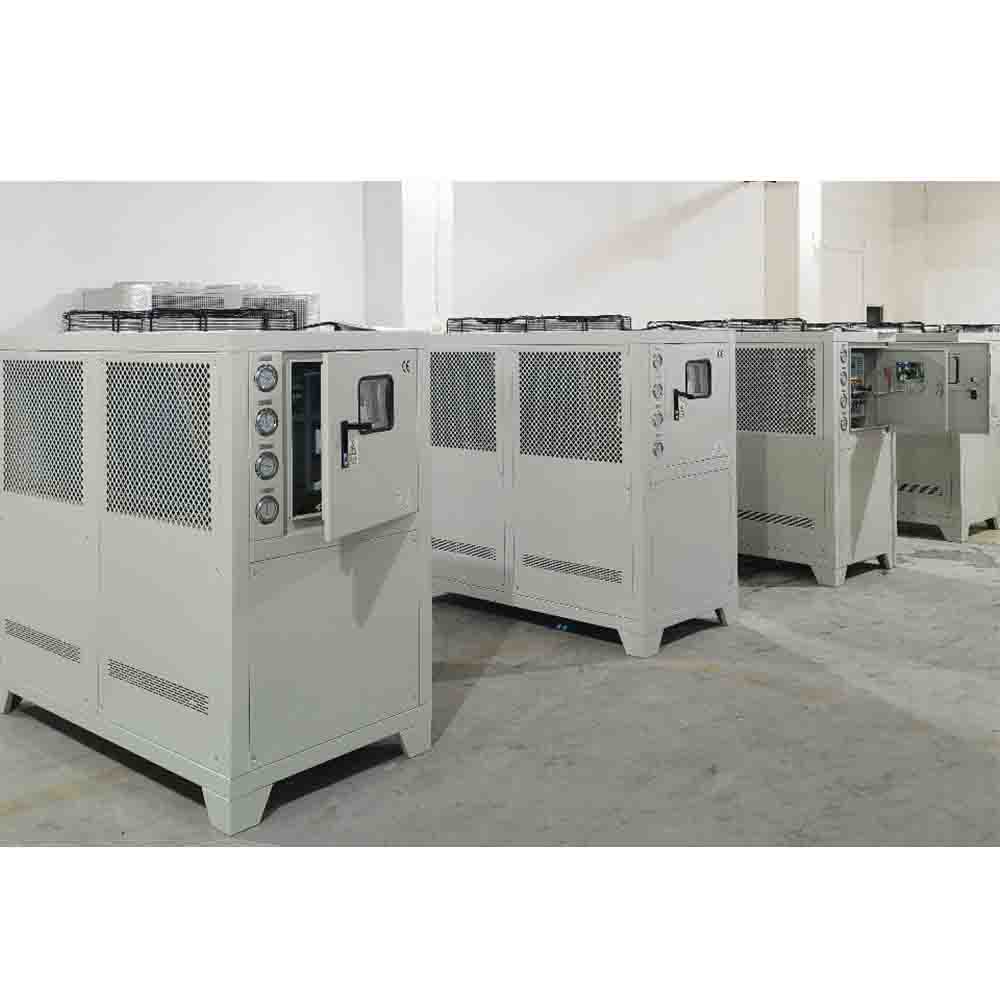
Der Flaschenblasprozess: Wie Kühler zur Effizienz beitragen
Der Flaschenblasprozess umfasst mehrere Schritte, vom Erhitzen der Vorform bis zum Abkühlen der Form. Kühler sorgen dafür, dass die Formen auf der richtigen Temperatur gehalten werden, sodass der geschmolzene Kunststoff schnell abkühlen und erstarren kann. Dies verkürzt die Zykluszeiten, erhöht die Produktionsleistung und verbessert die Gesamteffizienz der Flaschenblasmaschine. Richtig gekühlte Formen tragen auch zur Qualität der fertigen Flaschen bei, indem sie Defekte minimieren und eine gleichmäßige Wandstärke gewährleisten.
Beim Blasvorgang selbst wird ein erhitzter Vorformling in der Form mit Druckluft aufgeblasen. Präzise gesteuerte Niederdruckstufen sind entscheidend, um die gewünschte Flaschenform zu erreichen. Der Kühler als entscheidende Komponente des Kühlsystem, spielt eine direkte Rolle bei der Steuerung dieser Phasen und stellt sicher, dass der Kühlprozess den genauen Anforderungen jeder Phase der Flaschenherstellung entspricht.
Wartung Ihres Kältesystems für optimale Leistung
Regelmäßige Wartung ist der Schlüssel zur Gewährleistung der langfristigen Effizienz und Zuverlässigkeit Ihres Kühlsystems. Einfache Aufgaben wie das Reinigen der Kondensatorspulen, das Überprüfen des Kältemittelstands und das Überprüfen von Pumpen und anderen Komponenten können größere Probleme und kostspielige Ausfallzeiten verhindern. Ein vorbeugender Wartungsplan für die Kühlmaschine sollte regelmäßige Inspektionen, Reinigungen und Komponentenaustausch nach Bedarf umfassen.
Der effiziente Betrieb des Kühlers hängt in hohem Maße von der ordnungsgemäßen Wartung ab. Dazu gehört die Aufrechterhaltung der Wasserqualität für wassergekühlte Systeme, stellen Sie die richtige Kältemittelfüllung sicher und halten Sie den Kondensator frei von Schmutz. Regelmäßige Wartung verlängert nicht nur die Lebensdauer des Kühlers, sondern sorgt auch für optimale Kühlleistung, reduziert den Energieverbrauch und verbessert die Gesamteffizienz des Systems.
Fehlerbehebung bei häufigen Kühlerproblemen in Blasformanwendungen
Trotz regelmäßiger Wartung können gelegentlich Probleme mit dem Kühler auftreten. Wenn Sie die häufigsten Probleme und ihre möglichen Ursachen kennen, können Sie Probleme an Ihrem Kühler schnell diagnostizieren und beheben. Probleme wie unzureichende Kühlung, Lecks, ungewöhnliche Geräusche oder übermäßiger Energieverbrauch können häufig auf bestimmte Komponenten wie den Kompressor, den Kondensator oder das Kühlsystem zurückgeführt werden.
Wenn Sie sich mit der Funktionsweise von Kältemaschinen und den üblichen Schritten zur Fehlerbehebung auskennen, können Sie Ausfallzeiten minimieren und teure Reparaturen vermeiden. Eine Verringerung der Kühlleistung kann beispielsweise auf ein Problem mit dem Kühlmittel hinweisen, während ungewöhnliche Geräusche auf einen defekten Kompressor hinweisen können. Wenn Sie wissen, worauf Sie achten müssen, können Sie das Problem leichter identifizieren und feststellen, ob es sich einfach beheben lässt oder professioneller Service erforderlich ist.
Verwandte Produkte und integrierte Systeme für verbesserte Kühlung
Neben eigenständigen Kühlern können eine Reihe verwandter Produkte und integrierter Systeme die Kühleffizienz bei Flaschenblasanwendungen weiter verbessern. Dazu gehören Kühltürme für wassergekühlte Kühler, Temperaturregler zur präzisen Regelung der Formtemperatur und Pumpensysteme für eine optimale Wasserzirkulation. Die Integration dieser Komponenten in ein zusammenhängendes System kann den gesamten Flaschenblasprozess optimieren.
Bei größeren Flaschenblasbetrieben kann ein zentrales Kühlsystem effizienter sein als einzelne Kühler für jede Maschine. Diese Systeme umfassen häufig mehrere Kühler, Pumpen und ein Verteilungsnetz, um verschiedene Punkte im Produktionsprozess mit gekühltem Wasser zu versorgen. Dieser Ansatz ermöglicht eine bessere Kontrolle über die Kühlparameter, optimiert den Energieverbrauch und vereinfacht die Wartung.
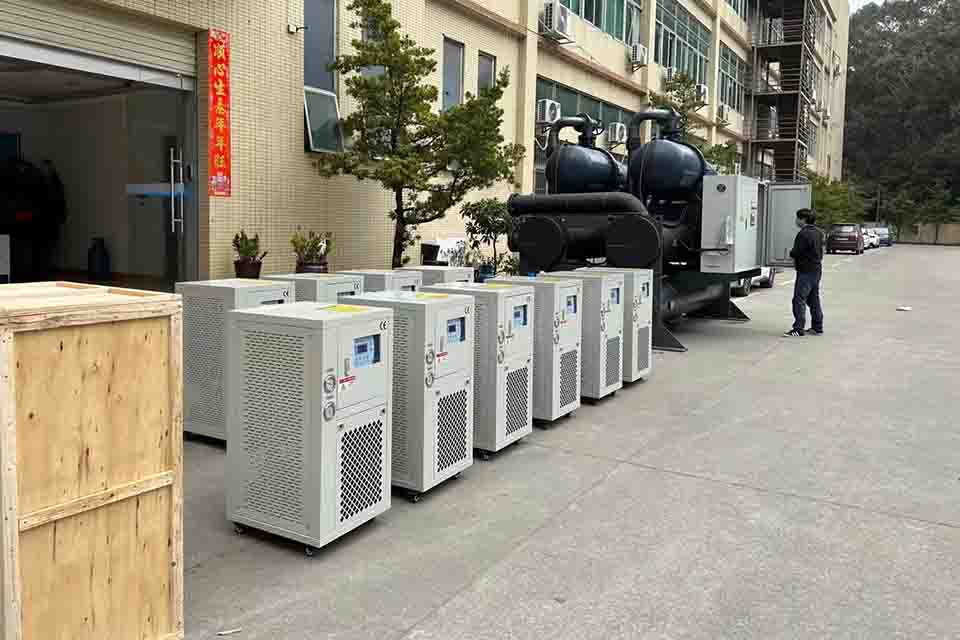
Erforschung moderner Kühltechnologien für das Flaschenblasen
Der Bereich der Kältetechnik entwickelt sich ständig weiter. Neue Innovationen zielen darauf ab, die Effizienz zu verbessern, die Umweltbelastung zu verringern und die Leistung zu steigern. Moderne Kältemaschinen können Kompressoren mit variabler Drehzahl, anspruchsvolle Steuerungssysteme und umweltfreundliche Kühlmittel enthalten. Diese Technologien bieten erhebliche Vorteile in Bezug auf Energieeinsparungen, präzise Temperaturregelung und reduzierte Betriebskosten.
Kompressoren mit variabler Drehzahl beispielsweise passen ihre Leistung an den Kühlbedarf an, optimieren so den Energieverbrauch und reduzieren den Kompressorverschleiß. Fortschrittliche Steuerungssysteme ermöglichen Echtzeitüberwachung und präzise Anpassungen, um optimale Kühlparameter im wassergekühlten Kühler aufrechtzuerhalten. Diese Technologien erweitern die Leistungsgrenzen von Kühlern und bieten erhebliche Vorteile für Flaschenblasvorgänge.
Kontaktieren Sie uns für fachkundige Beratung und individuelle Kühlerlösungen
Möchten Sie Ihren Flaschenblasvorgang mit einem Hochleistungskühler optimieren? Kontaktieren Sie uns noch heute! Wir bieten eine breite Palette an Kühlerlösungen, die auf die spezifischen Anforderungen von Flaschenblasmaschinen zugeschnitten sind. Unser Expertenteam kann Ihnen bei der Auswahl des richtigen Kühlerherstellers für Ihre Kunststoffverarbeitungsanforderungen helfen. Kühlergröße, Typ und Konfiguration für Ihre Anwendung, unabhängig davon, ob Sie ein kleines Unternehmen sind, das eine einzelne Flaschenblasmaschine betreibt, oder ein Großhersteller mit mehreren Produktionslinien.
Häufig gestellte Fragen:
Was ist der Unterschied zwischen einem wassergekühlten Kühler und einem luftgekühlten Kühler zum Flaschenblasen?
Wassergekühlte Kältemaschinen verwenden einen separaten Wasserkreislauf und Kühlturm zur Wärmeableitung. Sie bieten eine höhere Effizienz, erfordern jedoch eine komplexere Installation. Luftgekühlte Kältemaschinen verwenden Umgebungsluft zur Kühlung. Dies vereinfacht die Installation, weist in heißen Klimazonen jedoch möglicherweise eine geringere Effizienz auf.
Wie bestimme ich die richtige Kühlleistung für meine Flaschenblasmaschine?
Die Dimensionierung des Kühlers hängt von Faktoren wie Anzahl und Größe der Formen, Kunststoffart, gewünschten Zykluszeiten und Umgebungstemperatur ab. Für eine genaue Dimensionierung empfiehlt sich die Beratung durch einen Kühlerexperten.
Was sind die wichtigsten Wartungsschritte für einen Kühler, der mit einer Flaschenblasmaschine verwendet wird?
Zu den wesentlichen Wartungsaufgaben gehören die regelmäßige Reinigung der Kondensator-Spulen, die Kontrolle des Kältemittelstands, die Überprüfung von Pumpen und anderen Komponenten sowie die Sicherstellung einer ordnungsgemäßen Wasseraufbereitung für wassergekühlte Systeme.
Welche Probleme treten häufig bei Kühlern auf, die beim Flaschenblasen verwendet werden, und wie kann ich sie beheben?
Häufige Probleme sind unzureichende Kühlung, Leckagen, ungewöhnliche Geräusche und hoher Energieverbrauch. Die Fehlerbehebung umfasst häufig die Überprüfung des Kältemittelstands im luftgekühlten Kühler, die Inspektion des Kompressors und des Kondensators sowie die Überprüfung des ordnungsgemäßen Wasserflusses.
Welche Vorteile bietet die Verwendung eines Glykolkühlers mit einer Flaschenblasmaschine?
Glykol-Kühler ermöglichen niedrigere Kühltemperaturen, was für bestimmte Kunststoffarten oder spezielle Anwendungen zum Flaschenblasen von Vorteil sein kann.
Wie kann ich die Energieeffizienz meines Kühlsystems in einem Flaschenblasbetrieb verbessern?
Zur Verbesserung der Energieeffizienz gehören regelmäßige Wartung, die richtige Dimensionierung des Kühlers, die Verwendung energieeffizienter Komponenten und die Implementierung von Steuerungssystemen, die die Kühlleistung dem Bedarf des Wasserkühlers zum Flaschenblasen anpassen.
Wichtigste Erkenntnisse
- Kühler sind für die Aufrechterhaltung effizienter und qualitativ hochwertiger Flaschenblasvorgänge von entscheidender Bedeutung.
- Für eine optimale Leistung ist die Wahl des richtigen Kühlertyps und der richtigen Größe von entscheidender Bedeutung.
- Regelmäßige Wartung des wassergekühlten Kühlers verhindert kostspielige Ausfälle und verlängert die Lebensdauer der Geräte.
- Das Verständnis gängiger Kühlerprobleme ermöglicht eine schnelle Fehlerbehebung beim Wasserkühler zum Flaschenblasen.
- Durch moderne Kältetechnik lassen sich die Effizienz noch weiter steigern und die Betriebskosten senken.