-
ডালিংশান ইন্ডাস্ট্রিয়াল গুয়াংডং
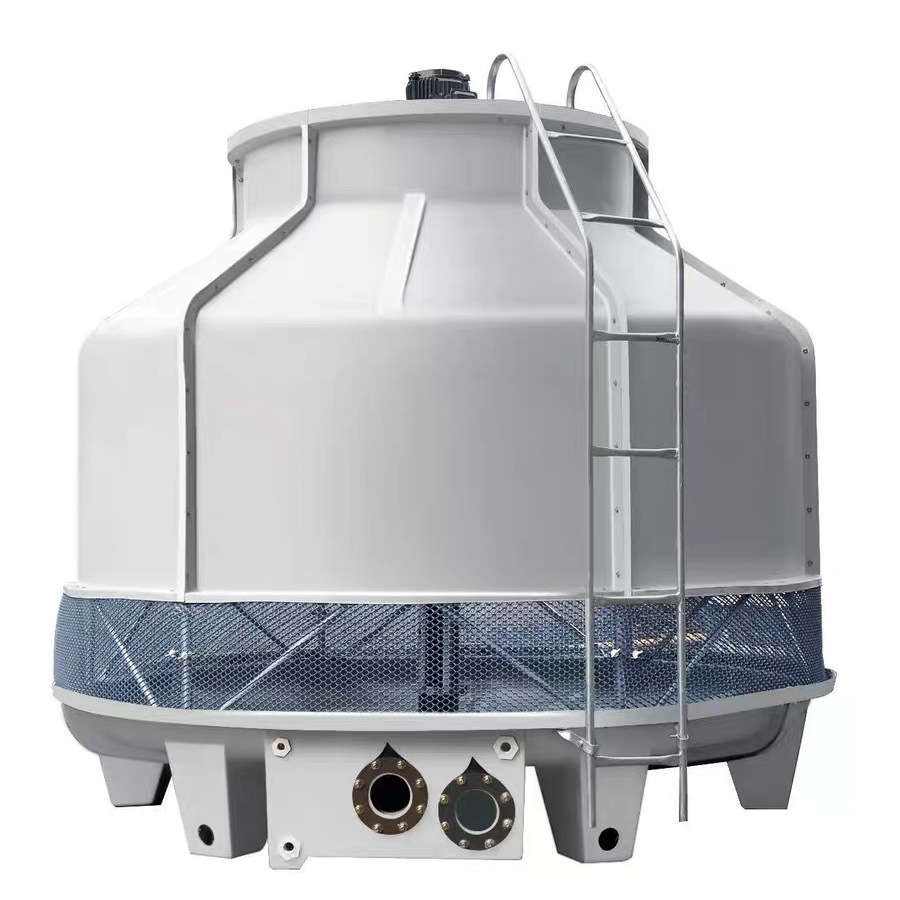
গ্রীষ্মকালে কুলিং টাওয়ারের দক্ষতা উন্নত করার টিপস
দক্ষ কুলিং টাওয়ার সলিউশনের মাধ্যমে আপনার কার্যক্রম সর্বাধিক করুন
তুমি কি খুঁজছো? দক্ষতা উন্নত করা আপনার শিল্প প্রক্রিয়া এবং শক্তি খরচ কমানো? ক কুলিং টাওয়ারপ্রায়শই উপেক্ষা করা হয়, এটি আপনার সিস্টেমের একটি গুরুত্বপূর্ণ অংশ। এটি আপনার ক্রিয়াকলাপের ফলে উৎপন্ন অতিরিক্ত তাপ অপসারণে গুরুত্বপূর্ণ ভূমিকা পালন করে। এই প্রবন্ধে, আমরা দেখব কিভাবে সঠিকভাবে রক্ষণাবেক্ষণ করা কুলিং টাওয়ার আপনার সুবিধার কর্মক্ষমতাকে উল্লেখযোগ্যভাবে প্রভাবিত করতে পারে, বিশেষ করে গ্রীষ্মের শীর্ষ সময়ে। প্লাস্টিক, খাদ্য ও পানীয় এবং ডেটা সেন্টারের মতো শিল্পের যে কোনও ব্যক্তির জন্য এই নির্দেশিকাটি অপরিহার্য, যারা নির্ভরযোগ্য কুলিং সমাধানের উপর নির্ভর করে।
সুচিপত্র
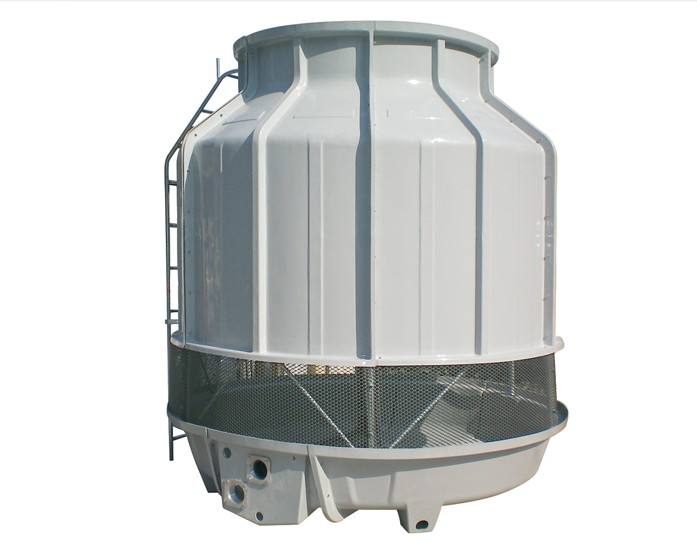
কুলিং টাওয়ার কী এবং কেন এটি গুরুত্বপূর্ণ?
ক কুলিং টাওয়ার একটি বিশেষায়িত তাপ বিনিময়কারী বর্জ্য তাপ অপসারণের জন্য ডিজাইন করা হয়েছে জল ব্যবস্থা শিল্প ও বাণিজ্যিক প্রক্রিয়ায় ব্যবহৃত হয়। কুলিং টাওয়ারগুলি সাধারণত যখন সরঞ্জাম থেকে তাপ বের হয়, যেমন a শীতলকারী, বায়ুমণ্ডলে বিচ্ছুরিত করতে হবে। এই প্রক্রিয়াটিকে বলা হয় বাষ্পীভবন, কার্যকরভাবে জলকে ঠান্ডা করে, যা পরে পুনঃসঞ্চালিত হয়। এটিকে আপনার শিল্প কারখানার জন্য একটি বিশাল রেডিয়েটর হিসাবে ভাবুন, যা আপনাকে সর্বোত্তম অপারেটিং তাপমাত্রা বজায় রাখতে দেয়। সঠিকভাবে কার্যকরী কুলিং টাওয়ার ছাড়া, আপনার উৎপাদন উচ্চ তাপমাত্রার দ্বারা প্রভাবিত হতে পারে, যা আপনার সরঞ্জাম এবং পণ্যগুলিকে প্রভাবিত করতে পারে। কুলিং টাওয়ার হল একটি তাপ প্রত্যাখ্যান ডিভাইস যা ব্যবহার করে বাতাস এবং জল উষ্ণ জল ঠান্ডা করার জন্য। তাপ প্রত্যাখ্যান সর্বাধিক করে, আমরা নিম্নতর তাপমাত্রা বজায় রাখতে সক্ষম জলের তাপমাত্রা.
কেন এটা গুরুত্বপূর্ণ? অনেক শিল্পে, সামঞ্জস্যপূর্ণ তাপমাত্রা অপরিহার্য। আপনি প্লাস্টিক প্রক্রিয়াকরণ করছেন, ধাতু মেশিন করছেন, খাদ্য ও পানীয় উৎপাদন করছেন, অথবা একটি ডেটা সেন্টার চালু রাখছেন, নির্ভুল তাপমাত্রা নিয়ন্ত্রণ অত্যন্ত গুরুত্বপূর্ণ। উদাহরণস্বরূপ, ইলেকট্রনিক্স শিল্প সংবেদনশীল উপাদানগুলির কর্মক্ষমতা বজায় রাখার জন্য স্থিতিশীল অপারেটিং তাপমাত্রা প্রয়োজন। একটি নির্ভরযোগ্য কুলিং টাওয়ার এই গুরুত্বপূর্ণ প্রক্রিয়াগুলির পিছনে প্রায়শই অপ্রকাশিত নায়ক। শীতলকরণ প্রক্রিয়া নিশ্চিত করে যে আপনার শীতলকরণ সরঞ্জাম কার্যকরভাবে তার কাজ করতে পারে।
একটি কুলিং টাওয়ার কীভাবে সামগ্রিক কুলিং সিস্টেমের দক্ষতাকে প্রভাবিত করে?
ক কুলিং টাওয়ারের প্রাথমিক কাজ হল সামগ্রিকভাবে সমর্থন করা শীতলকরণ ব্যবস্থাএর দক্ষতা সরাসরি অন্যান্য গুরুত্বপূর্ণ উপাদানগুলির কর্মক্ষমতার উপর প্রভাব ফেলে, যেমন আপনার শীতলকারী. যত ভালো, কুলিং টাওয়ার যত কম কাজ করবে, শীতলকারী করতে হবে। উদাহরণস্বরূপ, যদি একটি কুলিং টাওয়ার স্কেলিং বা ফাউলিংয়ের সাথে লড়াই করছে, তাহলে এর ফলে তাপমাত্রা বেশি হবে ঠান্ডা জল টাওয়ার থেকে ফিরে আসছি। এই উষ্ণ জল যা ফিরে আসে শীতলকারী এর কার্যকারিতা সরাসরি প্রভাবিত করবে, বৃদ্ধি করবে শক্তি খরচ এবং শক্তি খরচ কারণ এই উষ্ণ জলকে কাঙ্ক্ষিত প্রক্রিয়া তাপমাত্রায় ঠান্ডা করার জন্য চিলারকে আরও কঠোর পরিশ্রম করতে হবে।
সঠিকভাবে রক্ষণাবেক্ষণ করা কুলিং টাওয়ার কেবল নিশ্চিত করে না যে শীতলকারী দক্ষতার সাথে কাজ করতে পারে, কিন্তু কমাতেও সাহায্য করে পানি এবং শক্তি খরচ। শীতলকরণের দক্ষতা এমন একটি বিষয় যা আমরা শিল্প জল চিলার উৎপাদন নকশা পর্যায় থেকে বিবেচনা করুন। আমরা আমাদের ক্লায়েন্টদের একটি তৈরি করতে সাহায্য করতে পারি পানি ব্যবস্থাপনা পরিকল্পনা তাদের জন্য শীতল জল ব্যবস্থা। দ্য কুলিং টাওয়ার সিস্টেমের দক্ষতা আপনার সরঞ্জামের সামগ্রিক জীবনকেও প্রভাবিত করে। অন্যান্য উপাদানগুলির সাথে একসাথে কাজ করে শীতলকরণ ব্যবস্থা, কুলিং টাওয়ার আপনার যন্ত্রপাতির কার্যক্ষম জীবনকাল বাড়াতে সাহায্য করে। যখন শীতলকরণ ব্যবস্থার দক্ষতা অপ্টিমাইজ করা না হলে, এটি অন্যান্য উপাদানগুলিকে তাদের প্রয়োজনের চেয়ে বেশি কাজ করতে বাধ্য করতে পারে, যার ফলে অকাল ক্ষয় এবং ছিঁড়ে যেতে পারে।
কুলিং টাওয়ারের দক্ষতা প্রভাবিত করার মূল কারণগুলি কী কী?
বেশ কিছু কারণ প্রভাবিত করতে পারে কুলিং টাওয়ারের দক্ষতাসবচেয়ে বড় অপরাধীদের মধ্যে একজন হল ক্ষয়, যা স্কেলের দিকে পরিচালিত করে জমাট বাঁধা এবং হ্রাস করে তাপ স্থানান্তর টাওয়ারের ভরাট ক্ষমতা। দুর্বল পানির গুণমান এছাড়াও একটি গুরুত্বপূর্ণ ভূমিকা পালন করে, স্কেলিং এবং ফাউলিং ঘটায়, যার ফলে বাধাগ্রস্ত হয় কুলিং টাওয়ারের জল কার্যকরভাবে ঠান্ডা করার ক্ষমতা। অন্যান্য কারণগুলির মধ্যে রয়েছে জলের ধরণ, জলের তাপমাত্রা, এবং কাজের সময়, যার সবকটিই সামগ্রিক কর্মক্ষমতাকে প্রভাবিত করে। উদাহরণস্বরূপ, শক্ত জল স্কেলিংয়ে অবদান রাখতে পারে যা দক্ষতা হ্রাস করে, যদিও উচ্চতর জলের তাপমাত্রা সিস্টেমের উপর চাপ বাড়াতে পারে।
দ্য চক্রের সংখ্যা কুলিং টাওয়ারটি যেখান দিয়ে যায় তা আরেকটি গুরুত্বপূর্ণ বিবেচ্য বিষয়। জল বাষ্পীভূত হওয়ার সাথে সাথে এর ঘনত্ব দ্রবীভূত কঠিন পদার্থ বৃদ্ধি পায়। এটাকেই আমরা বলি ঘনত্বের চক্রদ্রবীভূত কঠিন পদার্থের ঘনত্ব যখন খুব বেশি হয়ে যায়, তখন এটি কুলিং টাওয়ারের পৃষ্ঠে স্কেল তৈরির দিকে পরিচালিত করে। এই স্কেল একটি অন্তরক হিসেবে কাজ করে, যা হ্রাস করে তাপ স্থানান্তর দক্ষতা, এবং জোর করে সিস্টেমের দক্ষতা হ্রাস করা। এটি নিয়ন্ত্রণ করতে, বিস্ফোরণ কিছু ঘনীভূত দূষক অপসারণের জন্য জল ফেলে দেওয়া হয়। কার্যকরভাবে নিয়ন্ত্রণ করা চক্রের সংখ্যা সর্বোত্তম শীতলতা বজায় রাখার জন্য গুরুত্বপূর্ণ এবং জল দক্ষতা.
নিয়মিত কুলিং টাওয়ার রক্ষণাবেক্ষণ কেন প্রয়োজনীয়?
নিয়মিত কুলিং টাওয়ার রক্ষণাবেক্ষণ সর্বোত্তম কর্মক্ষমতা নিশ্চিত করা এবং ব্যয়বহুল প্রতিরোধের জন্য অত্যন্ত গুরুত্বপূর্ণ ডাউনটাইমনিয়মিত রক্ষণাবেক্ষণ ছাড়া, একটি কুলিং টাওয়ার সময়ের সাথে সাথে কম দক্ষ হয়ে উঠবে কারণ জমাট বাঁধা, ক্ষয়, এবং জৈবিক বৃদ্ধি। রক্ষণাবেক্ষণের এই অভাব সরাসরি সংযুক্ত যন্ত্রপাতির কর্মক্ষমতাকে প্রভাবিত করে, যার ফলে আপনার সরঞ্জামের আরও ক্ষয়ক্ষতি হতে পারে। কল্পনা করুন আপনার শিল্প শীতলকারী খারাপভাবে রক্ষণাবেক্ষণ করা কুলিং টাওয়ারের কারণে সঠিক তাপমাত্রা বজায় রাখতে সমস্যা হচ্ছে। আমরা দেখেছি এর ফলে অপরিকল্পিত বিদ্যুৎ বিভ্রাট এবং উৎপাদন দক্ষতা হ্রাস পেয়েছে।
জল চিকিত্সা এর একটি গুরুত্বপূর্ণ অংশ কুলিং টাওয়ার রক্ষণাবেক্ষণ। এটি কর্মক্ষমতা হ্রাসের কারণগুলিকে নিয়ন্ত্রণ করতে সাহায্য করে। যথাযথ ব্যবস্থা ছাড়াই জল চিকিত্সা, এর কর্মক্ষমতা কুলিং টাওয়ার ঝুঁকির সাথে ভুগছে, লিজিওনেলা বৃদ্ধি এবং বর্ধিত ক্ষয় সমস্যা। নিয়মিত রক্ষণাবেক্ষণ বজায় রাখতে সাহায্য করে পানির গুণমান, সরিয়ে দেয় কঠিন পদার্থ এবং আঁশ গঠন রোধ করে। নিয়মিত রক্ষণাবেক্ষণ, যেমন পরিদর্শন করাপরিষ্কার করা এবং টাওয়ার ফিল সর্বাধিক করার জন্য অত্যন্ত গুরুত্বপূর্ণ শীতলকরণ ক্ষমতা কুলিং টাওয়ারের এবং আপনার দীর্ঘ জীবন নিশ্চিত করার জন্য শীতলকরণ সরঞ্জাম. ধারাবাহিক রক্ষণাবেক্ষণ মানে আপনার শীতলকরণ ব্যবস্থা কার্যকরভাবে কাজ করে এবং হ্রাস করে শক্তি ব্যবহার.
চিলারের সাথে মিলিত হলে কুলিং টাওয়ার সিস্টেম কীভাবে কাজ করে?
ক কুলিং টাওয়ার সিস্টেম এবং একটি শীতলকারী সর্বোত্তম শীতলতা অর্জনের জন্য একটি সিম্বিওটিক সম্পর্কের মধ্যে কাজ করুন। শীতলকারী প্রক্রিয়াজাত জলকে ঠান্ডা করে, যখন কুলিং টাওয়ার চিলার যে তাপ উৎপন্ন করে তা সরিয়ে দেয়। শীতলকারী তাপ সঞ্চার করে কনডেন্সার জল, যা পরে কুলিং টাওয়ারে প্রবাহিত হয়। এখানে, উষ্ণ জল ঠান্ডা করা হয় বাষ্পীভবন এবং তারপর ফিরে এলেন শীতলকারী চক্রটি পুনরাবৃত্তি করতে। এইভাবে তারা একে অপরের সাথে একত্রে কাজ করে কাঙ্ক্ষিত প্রক্রিয়া তাপমাত্রা বজায় রাখার জন্য।
একটির মধ্যে সমন্বয় শীতলকারী এবং একটি কুলিং টাওয়ার আপনার সম্পূর্ণ শীতলকরণ প্রক্রিয়ার দক্ষতা এবং নির্ভরযোগ্যতা নির্ধারণ করে। যদি কুলিং টাওয়ার দক্ষতার সাথে কাজ করছে না, এটি প্রভাবিত করবে চিলার তাপ অপসারণের ক্ষমতা। এটি কেবল সামগ্রিকভাবে আপস করে না সিস্টেমের দক্ষতা, কিন্তু উচ্চতর দিকেও নিয়ে যায় শক্তি খরচসঠিকভাবে রক্ষণাবেক্ষণ করা কুলিং টাওয়ার নিশ্চিত করে যে শীতলকারী সর্বোত্তম অবস্থার অধীনে কাজ করে, এবং প্রদান করে শীতলকরণের চাহিদা বিভিন্ন শিল্প অ্যাপ্লিকেশনের জন্য। যখন শীতলকারী এবং কুলিং টাওয়ার পুরো শীতলতা জুড়ে একসাথে তাদের সেরাটা দিয়ে কাজ করছে সিস্টেমের কর্মক্ষমতা সর্বাধিক করা হয়।
কুলিং টাওয়ারের কর্মক্ষমতা হ্রাসে ক্ষয় কী ভূমিকা পালন করে?
ক্ষয় একটি গুরুত্বপূর্ণ সমস্যা যা হ্রাস করে শীতলকরণের দক্ষতা টাওয়ার। টাওয়ারের কাঠামোর ধাতুগুলি ক্রমাগত সংস্পর্শে আসার কারণে ক্ষয়প্রাপ্ত হতে পারে জল এবং বাতাস, হ্রাস করা শীতলকরণ ক্ষমতা. ক্ষয় মরিচা এবং আঁশ তৈরির দিকে পরিচালিত করে জমাট বাঁধা, যা অন্তরক হিসেবে কাজ করে, বাধা দেয় তাপ স্থানান্তর প্রক্রিয়া। এর অর্থ হল সিস্টেমের একই কাঙ্ক্ষিত লক্ষ্যে পৌঁছাতে আরও শক্তির প্রয়োজন হবে ঠান্ডা জল তাপমাত্রা।
তাছাড়া, ক্ষয় লিক এবং কাঠামোগত ক্ষতি হতে পারে। এর ফলে অপরিকল্পিত ডাউনটাইম এবং ব্যয়বহুল মেরামত। খারাপ পানির গুণমান তৈরি করতে পারি ক্ষয় আরও খারাপ, একটি শক্তিশালী থাকা অপরিহার্য করে তোলে পানি পরিশোধন কর্মসূচি। সম্বোধন ক্ষয় কেবল সরঞ্জাম রক্ষণাবেক্ষণের বিষয় নয়, এটি হ্রাস করার বিষয়েও শক্তি খরচ, এবং বৃদ্ধি আপনার সরঞ্জামের জীবনকালউপেক্ষা করা ক্ষয় ভিতরে কুলিং টাওয়ার বড় ধরনের অপারেশনাল অদক্ষতার দিকে নিয়ে যেতে পারে এবং সম্ভাব্যভাবে পুরো প্রক্রিয়াটিকেই বিপন্ন করে তুলতে পারে। আমাদের অভিজ্ঞতা দেখিয়েছে যে ধারাবাহিক চিকিৎসা এবং রক্ষণাবেক্ষণ বেশিরভাগ ক্ষেত্রেই প্রতিরোধ করতে পারে ক্ষয় সমস্যা।
গ্রীষ্মকাল আমার কুলিং টাওয়ারের কার্যক্রমকে কীভাবে প্রভাবিত করে?
দ্য গ্রীষ্মকাল, বিশেষ করে যখন গ্রীষ্মের মাস, এর উপর উল্লেখযোগ্য চাপ সৃষ্টি করে কুলিং টাওয়ার পরিবেশের তাপমাত্রা বৃদ্ধি এবং উচ্চতর কারণে শীতলকরণের চাহিদা। দ্য গ্রীষ্মের তাপ আগত জলের তাপমাত্রা বাড়ায়, যা জলের জন্য আরও কঠিন করে তোলে কুলিং টাওয়ার দক্ষতার সাথে ঠান্ডা করার জন্য। এর ফলে হ্রাস পেতে পারে শীতলকরণ ক্ষমতা এবং উচ্চতর পরিচালন ব্যয়ও। একটি সু-রক্ষণাবেক্ষণ ব্যবস্থা পরিচালনা করতে সহায়তা করে গ্রীষ্মের তাপ কার্যকরভাবে।
সময় গ্রীষ্মের সর্বোচ্চ সময়, উচ্চতর কারণে সৃষ্ট নির্দিষ্ট চ্যালেঞ্জগুলিকে সক্রিয়ভাবে মোকাবেলা করা গুরুত্বপূর্ণ জলের তাপমাত্রা এবং বর্ধিত ব্যবহার। এই চ্যালেঞ্জগুলি উপেক্ষা করলে আপনার উৎপাদন প্রভাবিত হতে পারে, সিস্টেম ব্যর্থতার সম্ভাবনা বৃদ্ধি পেতে পারে এবং আপনার শক্তি ব্যবহারএকটি ব্যাপক গ্রীষ্মকালীন রক্ষণাবেক্ষণ পরিকল্পনা তাই আপনার কর্মক্ষমতা বজায় রাখার জন্য অত্যন্ত গুরুত্বপূর্ণ কুলিং টাওয়ার পুরো মরসুম জুড়ে। এটি নিশ্চিত করতে সাহায্য করে যে সিস্টেমটি তার গতিতে চলছে সর্বোচ্চ দক্ষতা এবং কার্যকরভাবে উন্নত শীতলকরণের চাহিদা। এ শিল্প জল চিলার উৎপাদন, আমরা এই চ্যালেঞ্জগুলি বুঝতে পারি, এবং আপনার সাথে সহায়তা করার জন্য এখানে আছি কুলিং টাওয়ার প্রয়োজনীয়তা, বিশেষ করে সময়কালে গ্রীষ্মকাল.
আমার কুলিং টাওয়ার সর্বোচ্চ দক্ষতায় কাজ করছে কিনা তা আমি কীভাবে নিশ্চিত করতে পারি?
আপনার নিশ্চিত করতে কুলিং টাওয়ার কাজ করে সর্বোচ্চ দক্ষতা, বেশ কয়েকটি মূল দিকের উপর মনোযোগ দিন। ধারাবাহিক জল চিকিত্সা স্কেলিং, ফাউলিং নিয়ন্ত্রণের জন্য অত্যন্ত গুরুত্বপূর্ণ, এবং ক্ষয়নিয়মিতভাবে পরিদর্শন করা ক্ষতির কোনও লক্ষণের জন্য টাওয়ারটি বা জমাট বাঁধা স্কেল নিশ্চিত করুন যে ভালভ এবং অন্যান্য সমস্ত যন্ত্রাংশ সঠিকভাবে কাজ করছে। পর্যবেক্ষণ করুন জলস্তর এবং প্রয়োজনীয় সমন্বয় করুন।
নিয়মিত পরিষ্কার-পরিচ্ছন্নতা টাওয়ার ফিল এটিও অপরিহার্য, কারণ এটি ধ্বংসাবশেষ দিয়ে দূষিত হতে পারে এবং কঠিন পদার্থ সময়ের সাথে সাথে, যা ব্যাপকভাবে দক্ষতা হ্রাস করে. সামঞ্জস্য করা বিস্ফোরণ হার সর্বোত্তম বজায় রাখতেও সাহায্য করতে পারে ঘনত্বের চক্র এবং প্রতিরোধ করুন জমাট বাঁধা ক্ষতিকর দ্রবীভূত কঠিন পদার্থসাবধানে পর্যবেক্ষণ এবং অপ্টিমাইজ করার মাধ্যমে কুলিং টাওয়ারের কার্যক্রম, আমরা আপনাকে সাহায্য করতে পারি দক্ষতা উন্নত করুন এবং কমাও শক্তি খরচ এবং এছাড়াও কমাতে সাহায্য করুন সামগ্রিক পরিচালন খরচ। নিয়মিত চেক, একটি দৃঢ় সহ পানি ব্যবস্থাপনা পরিকল্পনা, কুলিং টাওয়ারের দীর্ঘমেয়াদী কর্মক্ষমতায় বিশাল পরিবর্তন আনতে পারে। শিল্প জল চিলার উৎপাদন, আমরা বিশ্বাস করি যে সঠিক রক্ষণাবেক্ষণ হল সর্বোত্তম কর্মক্ষমতার চাবিকাঠি।
কুলিং টাওয়ারের জন্য আমার গ্রীষ্মকালীন রক্ষণাবেক্ষণ পরিকল্পনায় কী কী অন্তর্ভুক্ত করা উচিত?
একটি ব্যাপক গ্রীষ্মকালীন রক্ষণাবেক্ষণ পরিকল্পনা জন্য কুলিং টাওয়ার বেশ কিছু গুরুত্বপূর্ণ পদক্ষেপ অন্তর্ভুক্ত করা উচিত। প্রথমত, একটি পুঙ্খানুপুঙ্খ টাওয়ার পরিষ্কার ঋতু শুরুর আগে পরিষ্কার করা অপরিহার্য, এর মধ্যে রয়েছে টাওয়ার ফিল যেকোনো অপসারণ করতে জমাট বাঁধানিয়মিতভাবে বেসিন পরীক্ষা এবং পরিষ্কার করা, এবং নিশ্চিত করা যে নজলগুলি পরিষ্কার। জলস্তর ঘন ঘন পরীক্ষা করা উচিত। নিয়মিত পানির গুণমান পরীক্ষা এবং একটি পানি পরিশোধন কর্মসূচি স্কেল প্রতিরোধ করা গুরুত্বপূর্ণ, ক্ষয় এবং জৈবিক বৃদ্ধি। এর মধ্যে উপযুক্ত ব্যবহার জড়িত পানি এবং রাসায়নিক এবং পর্যবেক্ষণ জল রসায়ন.
রক্ষণাবেক্ষণের জন্য একটি সক্রিয় দৃষ্টিভঙ্গি অত্যন্ত গুরুত্বপূর্ণ গ্রীষ্মের মাস. এছাড়াও, নিশ্চিত করুন যে আপনার জল পরিশোধন ব্যবস্থা সঠিকভাবে ক্যালিব্রেটেড এবং ভালোভাবে কাজ করছে। এর ফ্যান এবং মোটর পরীক্ষা করুন কুলিং টাওয়ারগুলি ডিজাইন করা হয়েছে গ্রীষ্মের ভারী বোঝা সামলাতে। একটি সুনির্দিষ্ট অনুসরণ করে গ্রীষ্মকালীন রক্ষণাবেক্ষণ পরিকল্পনা, তুমি বজায় রাখতে পারো সর্বোচ্চ দক্ষতা সময়কালে গ্রীষ্মের সর্বোচ্চ সময়। আমাদের দক্ষতা শিল্প জল চিলার উৎপাদন আপনাকে সর্বোত্তম বিকাশে সাহায্য করতে পারে ব্যবস্থাপনা পরিকল্পনা তোমার জন্য কুলিং টাওয়ার.
আমার কুলিং টাওয়ারের প্রয়োজনীয়তার জন্য আমি কোথায় বিশেষজ্ঞের পরামর্শ এবং সহায়তা পেতে পারি?
আপনার সম্পর্কে বিশেষজ্ঞ পরামর্শ এবং সহায়তার জন্য কুলিং টাওয়ার, এটি উপকারী যোগাযোগ করুন পরামর্শের জন্য। আমরা, এ শিল্প জল চিলার উৎপাদন, ডিজাইন, উৎপাদন এবং রক্ষণাবেক্ষণে বছরের অভিজ্ঞতা আছে শিল্প কুলিং টাওয়ারআমাদের দল জল চিকিত্সা বিশেষজ্ঞ আপনার অপ্টিমাইজ করতে সাহায্য করতে প্রস্তুত পানি ব্যবস্থাপনা পরিকল্পনা। সঠিকটি বেছে নেওয়ার জন্য আপনার কি নির্দেশনার প্রয়োজন? কুলিং টাওয়ার অথবা সাহায্যের প্রয়োজন কুলিং টাওয়ারের জল চিকিত্সা, আমরা আপনাকে সাহায্য করার জন্য এখানে আছি।
একটি নির্ভরযোগ্য ব্যক্তির সাথে কাজ করা জল পরিশোধন কোম্পানি আপনার সিস্টেমটি সর্বোত্তমভাবে কাজ করে তা নিশ্চিত করে। আমাদের সাথে সহযোগিতা করে, আপনি পেশাদারদের একটি দলের সাথে যোগাযোগ করতে পারবেন যাদের বিভিন্ন শিল্পে কাজ করার অভিজ্ঞতা রয়েছে, থেকে শুরু করে চিকিৎসা শিল্প প্রতি খাদ্য ও পানীয় শিল্পআমরা তৈরি করতে পারি জল পরিশোধন কর্মসূচি আপনার নির্দিষ্ট চাহিদা পূরণের জন্য। আমরা এখানে আছি আপনার নিশ্চিত করার জন্য কুলিং টাওয়ার দক্ষতার সাথে, নির্ভরযোগ্যভাবে এবং আপনার বাজেটের মধ্যে কাজ করে। আপনার সর্বাধিক সুবিধা অর্জনের জন্য আমরা আপনাকে প্রয়োজনীয় দক্ষতা এবং সহায়তা প্রদান করতে পারি শীতলকরণ ব্যবস্থা.
বৈশিষ্ট্য | গুরুত্ব |
---|---|
নিয়মিত পরিদর্শন | ছোটখাটো সমস্যাগুলিকে বড় সমস্যায় পরিণত হতে বাধা দেয়। |
পানি শোধন | ক্ষয়, স্কেল তৈরি এবং জৈবিক বৃদ্ধি নিয়ন্ত্রণ করে। |
অপ্টিমাইজড ব্লোডাউন | ঘনত্বের আদর্শ চক্র বজায় রাখে। |
পরিষ্কার করা | সর্বোচ্চ তাপ স্থানান্তর দক্ষতা নিশ্চিত করে। |
সক্রিয় পদ্ধতি | ডাউনটাইম কমায় এবং সরঞ্জামের আয়ুষ্কাল বাড়ায়। |
- মনে রাখার জন্য গুরুত্বপূর্ণ বিষয়:
- সঠিকভাবে রক্ষণাবেক্ষণ করা কুলিং টাওয়ার সামগ্রিকভাবে অপরিহার্য শীতলকরণ ব্যবস্থা দক্ষতা।
- জল চিকিত্সা প্রতিরোধের জন্য অত্যন্ত গুরুত্বপূর্ণ ক্ষয়, স্কেলিং, এবং জৈবিক বৃদ্ধি।
- নিয়মিত রক্ষণাবেক্ষণ উন্নত হয় কুলিং টাওয়ারের দক্ষতা এবং পরিচালন খরচ কমায়।
- একটি ব্যাপক গ্রীষ্মকালীন রক্ষণাবেক্ষণ পরিকল্পনা বজায় রাখতে সাহায্য করে সর্বোচ্চ দক্ষতা উষ্ণতম মাসগুলিতে।
- আমরা এমন একটি কোম্পানি যার বিশেষজ্ঞদের একটি দল আপনার সমস্ত বিষয়ে সহায়তা করার জন্য প্রস্তুত কুলিং টাওয়ার চাহিদা, যোগাযোগ করুন আজ।
প্রায়শই জিজ্ঞাসিত প্রশ্নাবলী
আমার কুলিং টাওয়ার কতবার পরিদর্শন করা উচিত?
আমরা অন্তত একটি পুঙ্খানুপুঙ্খ পরিদর্শনের পরামর্শ দিচ্ছি বছরে দুবার, এবং আরও ঘন ঘন গ্রীষ্মের মাস যখন সিস্টেমটি ভারী বোঝার মধ্যে থাকে।
আমার কুলিং টাওয়ারের রক্ষণাবেক্ষণের প্রয়োজন কিনা তার লক্ষণগুলি কী কী?
লক্ষণগুলির মধ্যে রয়েছে হ্রাস শীতলকরণ ক্ষমতা, উচ্চতর শক্তি খরচ, অস্বাভাবিক শব্দ, এবং স্কেলের দৃশ্যমান লক্ষণ জমাট বাঁধা অথবা ক্ষয়.
কুলিং টাওয়ার সিস্টেমে ব্লোডাউন কেন গুরুত্বপূর্ণ?
ব্লোডাউন ঘনীভূত অপসারণ করে দ্রবীভূত কঠিন পদার্থ জল থেকে, স্কেল গঠন রোধ করে এবং সর্বোত্তম বজায় রাখে ঘনত্বের চক্র। এটি বজায় রাখতে সাহায্য করে শীতলকরণের দক্ষতা.
আমি কি নিজে নিজে কুলিং টাওয়ার রক্ষণাবেক্ষণ করতে পারব?
যদিও মৌলিক পরীক্ষাগুলি ঘরে বসেই করা যেতে পারে, পেশাদার জল চিকিত্সা এবং রক্ষণাবেক্ষণ অত্যন্ত বাঞ্ছনীয়, কারণ এটি সামগ্রিক দীর্ঘমেয়াদী খরচ কমায়। জল চিকিত্সা বিশেষজ্ঞ আপনার একটি গভীর বিশ্লেষণ প্রদান করতে পারে জল রসায়ন, এবং সেই অনুযায়ী একটি চিকিৎসা পরিকল্পনা তৈরি করুন।
কিভাবে একটি কুলিং টাওয়ার শক্তি খরচ কমায়?
দক্ষ নিশ্চিত করে তাপ স্থানান্তর, সঠিকভাবে রক্ষণাবেক্ষণ করা কুলিং টাওয়ার তোমার অনুমতি দেয় শীতলকারী আরও দক্ষতার সাথে পরিচালনা করতে, এর পরিমাণ কমাতে শক্তি খরচযখন কুলিং টাওয়ার সঠিকভাবে রক্ষণাবেক্ষণ করা হয়, এটি দক্ষতা হ্রাস করে সমগ্রের সিস্টেম.
লিজিওনেলা কী এবং আমার কুলিং টাওয়ারে এটি কীভাবে প্রতিরোধ করব?
লেজিওনেলা এটি একটি ক্ষতিকারক ব্যাকটেরিয়া যা বৃদ্ধি পেতে পারে কুলিং টাওয়ার দরিদ্রদের সাথে পানির গুণমাননিয়মিত জল চিকিত্সা এবং সঠিক রক্ষণাবেক্ষণ এর বৃদ্ধি রোধ করতে সাহায্য করে, এবং কঠোরভাবে প্রয়োগের মাধ্যমে এটি নিয়ন্ত্রণ করা যেতে পারে পানি ব্যবস্থাপনা পরিকল্পনা.
আসুন আমরা আপনার শিল্প প্রক্রিয়াগুলিকে দক্ষ এবং নির্ভরযোগ্যভাবে উন্নত করতে সাহায্য করি কুলিং টাওয়ার সমাধান। আপনার উৎপাদনে পৌঁছাতে আমরা কীভাবে সাহায্য করতে পারি সে সম্পর্কে আরও জানতে আজই আমাদের সাথে যোগাযোগ করুন এবং সর্বোচ্চ দক্ষতা লক্ষ্য।
সম্পর্কিত প্রবন্ধ: